|
|
Донецкий национальный технический университет
Механический факультет
кафедра: "Технология машиностроения"
Автореферат
выпускной работы по теме:
Влияние физико-механических свойств полимерной связки абразивного инструмента на качество обрабатываемой
поверхности
магистранта Павлюка С.В.
e-mail: pavlsv_ne@ukrtop.com
руководитель: доц., к.т.н.
Ищенко А.Л.
Influence of physic-mechanical properties of polymeric copula of abrasive instrument on quality of processed surface
Pavlyuk S.V., master's degree
leader: ph.d. Ishchenco A.L.
Considerable part of polishing energy will be transformed in thermal energy. High temperatures in the
area of cutting cause defects in the superficial layer of detail. Therefore thermal descriptions of copula of abrasive
instrument take on special significance. In-process resulted to dependence to determination of the temperature fields,
thermal streams temperatures, in the area of polishing, and also other thermophysical descriptions of processes of abrasive
treatment and thermal properties of copulas.
Содержание |
1. Общая характеристика работы
2. Актуальность темы
3. Цель и задачи исследования
4. Методы исследования
5. Научная новизна
6. Практическое значение и реализация полученных результатов
7. Содержание работы
8. Заключение и перспективы исследования
|
1 Общая характеристика работы |
Приведенный материал носит описательный, поверхностный характер, поскольку на момент создания страницы магистерская работа
была далека от заверения. В автореферате представлены лишь некоторые наброски, указывающие
направление работы в целом, круг решаемых проблем и задач – наработки, описывающие существующие положения и исследования,
оговаривающие область пересечения с другими сферами знаний.
|
2 Актуальность темы |
Повышение надежности и долговечности деталей машин является основной проблемой машиностроения. Постоянный рост требований
к качеству и точности рабочих поверхностей заставляет тщательнее исследовать и использовать технологические возможности
методов окончательной обработки, из которых наиболее распространенным является шлифование, превратившееся за вторую
половину прошлого века, из способа понижения шероховатости в наиболее производительный способ формообразования.
Шлифование обеспечивает допуск при обработке поверхностей до сотых долей миллиметра, высокую чистоту обработки и высокую
степень ровности, к тому же при обработке закаленных и специальных легированных сталей и сплавов это наиболее
промышленно-приемлемый метод, а широко внедряемые современные материалы: керамика, армированные металлы и полимеры,
многослойные металлы с неметаллическим ламинированием зачастую могут быть обработаны только при помощи шлифования.
В отличие от других методов обработки со снятием стружки, при шлифовании невозможно наблюдать непосредственно процесс
резания, поэтому крайне необходимо знать факторы, влияющие на качество и точность шлифования. Одним из таких факторов является связка.
От качества связки зависит коэффициент использования потенциальных возможностей инструмента, область его применения,
работоспособность, производительность и экономическая эффективность. Кроме того, состав связки определяет технологичность
и сложность производства инструмента.
Связка должна обеспечивать высокую режущую способность инструмента, наиболее полное использование абразивных зерен,
малое тепловыделение, низкий коэффициент трения, способствовать снижению параметров шероховатости обработанной поверхности,
исключать схватывание с обрабатываемым материалом. От связки зависит не только износостойкость инструмента, но и механизм
резания, и характер взаимодействия с обрабатываемым материалом, сила и температура резания, структурное и напряженное
состояние поверхностного слоя обработанного изделия, коэффициент трения, адгезионные и диффузионные явления в зоне резания.
На основании вышеизложенного можно с уверенностью утверждать, что тема данной работы является достаточно актуальной и перспективной.
|
3 Цель и задачи исследования |
Целью данной работы является исследование влияния физико-механических свойств полимерных связок абразивного инструмента
на качество обрабатываемой поверхности. Для этого необходимо решить следующие задачи:
- Проанализировать и обобщить известные физико-механические свойства связок.
- Рассмотреть существующие силовые и тепловые зависимости процесса шлифования.
- Разработать параметрические модели фрагментов шлифовальных кругов с различными видами связки в среде ANSYS.
- Исследовать напряженно-деформированное и температурное состояние фрагментов при различный условиях обработки, оценить удерживающую способность связок.
- Исследовать динамику поведения единичного зерна при изменяющихся параметрах полимерной связки.
- Проанализировать полученные результаты и дать рекомендации по использованию той или иной связки для конкретных условий работы.
|
4 Методы исследования |
Для решения поставленных задач применяются следующие методы:
- Системный анализ. Предполагает комплексный подход к исследованию проблемы: обработку и обобщение существующих
зависимостей, анализ взаимосвязи и степени влияния факторов, создание математической модели.
- Компьютерный эксперимент - компьютерное моделирование. Необходимо для проверки работоспособности математической модели
и уменьшения объема стендовых экспериментов.
- Экспериментальные исследования. Создание испытательного стенда, изготовление абразивных кругов на органической связке
с различными свойствами, проведение опытов, обработка результатов (выявление ошибок и сравнение полученных результатов с ожидаемыми).
|
5 Научная новизна |
Предлагаемая компьютерная модель будет являться новой формой расчета режимов обработки, позволит определить температуру и деформации в зоне
резания, поможет учесть изменение параметров системы во времени, наглядно продемонстрирует распределение тепловых потоков
и напряжений в материале, существенно упростит оптимизацию процессов резания.
|
6 Практическое значение и реализация полученных результатов |
Любая связка – это многоэлементная композиция, причем каждый ингредиент
композиции может существенно менять ее свойства. Аналитически оценивать значительное количество влияющих факторов весьма
трудоемкое занятие, также не возможно каждый раз проводить эксперименты по определению температур и деформаций связки и
обрабатываемого материала. Поэтому создаваемая компьютерная модель будет весьма полезной: позволит учесть изменение
физических величин (предела прочности, вязкости, коэффициента трения, теплопроводности, коэффициента линейного теплового
расширения) от температуры и времени, оценить граничные условия процесса, позволит быстро и легко подобрать режимы обработки,
дать рекомендации по эффективному использованию того или иного вида связки.
Материалы магистерской работы были обсуждены и одобрены на дне науки кафедры "Технология машиностроения" ДонНТУ 5 мая 2005 года.
|
7 Содержание работы |
На практике наиболее широкое применение находят круги на органических связках (55% от общего количества). Это объясняется
тем, что такой инструмент прост в изготовлении и универсален в работе; обладает самозатачиваемостью и высокой режущей
способностью; работает с охлаждением и без него; используется как для доводочных чистовых операций шлифования, так и для
заточки твердосплавной части инструмента, а также твердого сплава со сталью (круги на связке Б156); позволяет получать
низкие параметры шероховатости и бездефектные поверхностные слои.
Все органические связки (Б1, Б2, БЗ, Б4, Б8, БР, Б156, БП2, БП3, ТО2, 01) представляют собой композиции на основе
порошкообразного органического связующего материала – пульвербакелита (ПБ) – измельченной смеси новолачной феноло-формальдегидной
смолы с уротропином. Предел прочности на растяжение ПБ не менее 13 МПа, а после действия 2%-ного раствора соды на образец – не
менее 65 МПа [1]. ПБ имеет много достоинств – высокую износостойкость, влагостойкость, простоту совмещения с другими
порошковыми компонентами, низкие параметры переработки – давление и температуру. Тепло- и термостойкость ПБ значительно
ниже температур, возникающих в процессе работы инструмента (теплостойкость фенолоформальдегидных полимеров не превышает 250°С) [1].
В настоящее время в качестве связующего материала активно применяются жидкие органические смолы. Они обеспечивают лучшее
смачивание и более полное обволакивание абразивных частиц связкой по сравнению с прессованным ПБ, в результате чего
повышается стойкость инструмента. Используя составы на жидких смолах, можно изготовить инструмент без применения давления,
что предотвращает дробление зерен при прессовании, к тому же прессформы для жидких составов отличаются простотой конструкции.
Для того чтобы абразивный инструмент имел высокую производительность и стойкость, его связка должна быть достаточно прочной,
чтобы надежно удерживать абразивное зерно до его полного износа и в то же время изнашиваться с такой же интенсивностью.
Прочность удержания зерен является одним из важнейших условий работоспособности, основным критерием выбора связки шлифовального
инструмента. Прочность удержания зерен можно оценивать по их длительности нахождения в связке или по размеру площадки
затупления при установившемся режиме резания одного и того же материала [5]. При этом чем больше площадка износа, тем выше
прочность удержания зерен.
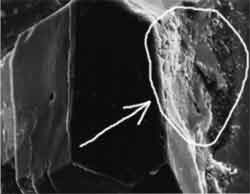
Рисунок 1 – Микроснимок площадок износа зерна
Прочность закрепления зерна в связке главным образом зависит от типа и состава (компонентов) связки, от глубины заделки,
формы, величины и развитости поверхности абразивного зерна. Зерно удерживается в матрице, во-первых, за счет механического
охвата материалом связки и, во-вторых, вследствие химического взаимодействия компонентов связки с поверхностью абразивного
зерна. Последнее является наиболее эффективным средством повышения прочности удержания, достигается введением в связку
химически взаимодействующих с абразивом компонентов. Сила удержания зависит от адгезионной активности компонентов связки
к поверхности абразивного зерна и растет с увеличением работы адгезии.
В зависимости от применяемой схемы, вида и метода шлифования, инструмент, работающий в условиях динамической ударной
циклически повторяющейся нагрузки, воспринимает напряжения сжатия, среза и изгиба. Поэтому прочностные характеристики
связок, модуль упругости Е, прочность на сжатие sсж, прочность на изгиб
sизг, ударная вязкость ан и твердость HRB оказывают существенное влияние
на экономичность процесса шлифования. Повышение прочности связки инструмента в целом дает возможность увеличить скорость
резания. Модуль упругости и твердость определяют размерную стойкость и качество поверхностного слоя обрабатываемого изделия.
Помимо прочности удержания зерна и износостойкости, большое значение имеет коэффициент трения, а также характер
взаимодействия связки с обрабатываемым материалом. Связка должна обладать антифрикционными свойствами, причем
чем они выше, тем ниже температура трения при шлифовании и в меньшей степени проявляются диффузионные и адгезионные процессы.
Антифрикционные свойства связок зависят прежде всего от их типа и состава: основы связок, наполнителей и вводимых твердых
смазок, адгезионных и диффузионных свойств. В качестве твердых смазок применяют графит, фториды кальция, кадмия и цинка,
нитриды циркония и бора, бориды титана, хрома, молибдена, сульфиды цинка и железа.
Значительная часть энергии шлифования преобразуется в тепловую энергию. Высокие температуры шлифования могут вызвать
дефекты в поверхностном слое детали (прижоги, трещины и др.), снижающие качество изделия, в связи с чем теплопроводность
связки приобретает значение одного из основных факторов процесса шлифования. Для определения тепловых свойств связок,
расчета температурных полей, тепловых потоков, температур в зоне шлифования, а также других теплофизических характеристик
процессов абразивной обработки важно знать свойства как самих абразивных зерен, так и их композиций с другими материалами,
применяющимися при изготовлении связок. Органические связки абразивного инструмента на основе фенолоформальдегидных смол
имеют низкую теплопроводность, что является причиной их высокой чувствительности к тепловым воздействиям в контактной
зоне. Нагрев связки выше температуры стеклования приводит к ее размягчению и, следовательно, к преждевременному вырыванию
работоспособных алмазных зерен, поэтому качество шлифованных поверхностей и износостойкость абразивного инструмента во
многом определяются возникающей в зоне резания температурой и распределением тепла в системе: изделие – круг – стружка – охлаждающая среда.
Зная распределение тепловых потоков, величины и характер температурных полей в круге, изделии и стружке, можно:
- правильно формулировать основы теории износа абразивного инструмента;
- оценивать характер взаимодействия зерна с обрабатываемым материалом;
- предвидеть характер разрушения абразивных зерен и абразивного инструмента в целом;
- наиболее целесообразно выбирать абразивный материал для работы в тех или иных условиях;
- оценивать влияние СОТС на процесс шлифования и отыскивать пути его эффективного использования;
- регулировать процесс шлифования для получения минимального теплового воздействия на поверхностные слои изделия и режущего инструмента.
Таков неполный перечень задач, необходимость выяснения которых заставляет искать пути
изучения и регулирования температуры, возникающей при шлифовании деталей.
Большинство работ по расчету температуры при шлифовании, основаны на применении теории мгновенных источников тепла
(точечного, линейного, плоского и т. д.). В основе приведенного расчета в качестве исходного используется решение
уравнения теплопроводности для плоского мгновенного источника тепла [2]:
(1)
В формуле (1) а = l1/(c·g) – коэффициент температуропроводности,
м2/с; l1 – коэффициент теплопроводности, вт/(м·град); t1 – момент времени,
для которого проводится расчет температуры, с; с – удельная теплоемкость, дж/(кг·град); g – плотность
материала, кг/м3; Q1 – тепловой поток, дж/м2; q1 – температура
на поверхности шлифуемой пластины,°С.
Температурное поле при действии источника тепла не мгновенно, а в течение времени t2
определится интегрированием выражения (1):
(2)
где D – доля тепла, идущая в изделие; qср – средняя по поверхности контакта интенсивность
теплового потока, дж/м2·с; t2 = 0,06·bк/Sпр – время
действия источника тепла, с; bк – ширина круга, мм; Sпр – продольная подача, м/мин; t3 – переменная
интегрирования времени, с.
На поверхности пластины у = 0 в момент наибольшего нагрева, т. е. когда t1 =
t2 температура определится преобразованием уравнения (2) к виду:
(3)
По формуле (3) можно рассчитать температуру поверхностного слоя обрабатываемой детали при однопроходном шлифовании.
С увеличением числа проходов нагрев поверхности возрастает, так как тепло от каждого последующего прохода суммируется
с теплом, накопленным в предыдущих проходах. Учитывая это, температуру поверхностного слоя при многопроходном шлифовании
можно определить по зависимости:
(4)
В формуле (4) n – число проходов; t4 – время, сек; u – темп
охлаждения шлифуемой поверхности после выхода рассматриваемой точки из-под круга, вычисляемый по формуле:
(5)
где q6 и q5 – температура точки поверхности
пластины соответственно моментам времени t5 и t6, °С.
Согласно [2] для диапазона температур 450 – 800°С (723 – 1073 °К) среднее значение темпа охлаждении u
для сплавов ВК15М, ТТ7К12, ТТ10К8Б, Т15К6, ТТ16К6 соответственно равно 0,92; 0,72; 0,65; 0,41; 0,39 град/с.
Интенсивность теплового потока qср складывается из интенсивности теплообразования от пластической деформации
q1 обрабатываемого материала, трения зерен и связки о поверхность изделия, обозначаемых соответственно q2 и q3:
qср = q1 + q2 + q3 (6)
Зависимости, по которым определяются слагаемые формулы (6) подробно рассмотрены в [2]. В данной работе представлены лишь результаты исследований:
так для шлифования плоскостей:
для сталей средней твердости (например сталь 45):
q = 120,7·Vи-0,38·Sп·t0.88·kт·kз·kм (7)
для жаропрочных сплавов на основе никеля (например сплав ХН77ТЮ):
q = 81,5·Vи-0,35·Sп·t0.8·kт·kз·kм (8)
для титановых сплавов (например сплав ВТ5):
q = 91·Vи-0,36·Sп·t0.86·kт·kз·kм (9)
В формулах (7 – 8) Vи – скорость детали; Sп – поперечная подача; t – глубина резания;
kт, kз, kм – поправочные коэффициенты, учитывающие зависимость мощности от твердости,
зернистости и материала зерна [2].
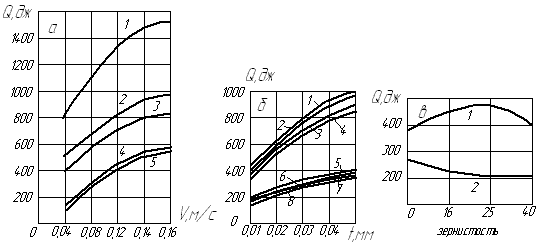
Рисунок 3 – Зависимость Qд от: а – режимов шлифования при обработке сплава ЖС6К:
(1 – Vu = 0,015 м/с; 2 – 0,05; 3 – 0,1; 4 – 0,15; 5 – Vu = 0,2 м/с);
б – глубины резания при различной зернистости абразива:
(1 и 5 – зернистость 6; 2 и 6 – 16; 3 и 7 – 40; 4 и 8 – 25),
обрабатываемый материал – сталь 45 (кривые 1, 2, 3, 4)
и титановый сплав ВТ-3 (кривые 5, 6, 7, 8);
в – зернистости абразивного круга при различной скорости детали:
(1 – 0,015; 2 – 0,1 м/с), материал образца – титановый сплав ВТЗ [3].
Кроме рассмотренных, мощность теплового источника может быть определена другими методами. Так, например, для круглого
шлифования можно использовать формулу:
(10)
где Q – общее количество тепла, выделяемое при шлифовании; В – ширина шлифовального круга; lк – длина
дуги контакта шлифовального круга с деталью [4]; kp – коэффициент, представляющий отношение общего количества
тепла к теплу, отводимому в деталь. Учитывая, что примерно 80% энергии деформации переходит в тепло, а остальная часть – в
поглощенную скрытую работу изменения кристаллической решетки и упругую деформацию, можно написать:
Q = 0,8·Pz·Vкр/427 (11)
где Vкр – окружная скорость шлифовального круга; Рz – составляющая усилия резания,
действующая в плоскости, касательной к шлифовальному кругу.
По Е.Н. Маслову, для круглого шлифования:
Pz = 20,6·t0,6·Sпр0,7·Vд0,7 (12)
где t – глубина шлифования; Sпр – продольная подача; Vд – скорость вращения детали.
Влияние окружной скорости круга Vкр, на силы шлифования и температуру поверхностного слоя твердого сплава ТТ10К8Б
приведено на рис. 2а. С уменьшением Vкр радиальная Рy и тангенциальная Pz составляющие силы шлифования возрастают.
Сила же Рx изменяется незначительно. Заметим, что характер изменения сил для интервала скоростей 14 – 20 м/с
более резкий, чем для интервала 20 – 40 м/с.
Рисунок 2 – Влияние: а) окружной скорости круга Vкр, м/с
(режимы шлифования: Sпр = 1 м/мин, t = 0,02 мм/дв.ход, Fкр = 70 мм2);
б) продольной подачи Sпр, м/мин (Vкр = 28 м/с, t = 0,02 мм/дв.ход, Fкр = 70 мм2);
в) глубины шлифования t, мм (Vкр = 28 м/с, Sпр = 1 м/мин, Fкр = 70 мм2);
на силы резания (Pz, Py, Px) и температуру поверхностного слоя q,°K.
Увеличение продольной подачи вызывает почти линейное увеличение усилий шлифования Pz, Py и Px (рис. 2б).
Большое возрастание нормальной составляющей силы шлифования, чем тангенциальной, показывает уменьшение режущей способности
круга при повышенной производительности.
Влияние глубины шлифования на температурные и силовые режимы можно проанализировать по рис. 2в. Можно заметить, что
тангенс угла наклона кривых Рy, Pz и Рx в зависимости от глубины шлифования больше, чем
в зависимости от продольной подачи. На температуру поверхностного слоя глубина шлифования оказывает несколько меньшее
влияние, чем продольная подача. Так, например, при изменении продольной подачи от 1 до 3 м/мин (рис. 2б) температура
поверхностного слоя увеличивается на 270 град, а при изменении глубины шлифования также в 3 раза – от 0,01 до 0,03 мм/ход – только на 200 град.
На рис. 3 представлены зависимости сил шлифования и температуры поверхностного слоя от площади обработки (а) и типа связки (б).
Рисунок 3 – зависимости сил шлифования и температуры поверхностного слоя от:
a) площади обработки Fкр мм2, (режимы шлифования: Vкр = 28 м/с, Sпр = 1 м/мин, t = 0,02 мм/дв.ход);
б) типа связки (Vкр = 28 м/с, Sпр = 1 м/мин, t = 0,02 мм/дв.ход).
Преобразовывая формулы Л.П. Исаева и С.С. Силина, характеризующие распределение тепла между деталью Qд,
шлифовальным кругом Qкр и стружкой Qстр находим:
(13)
где Lд – длина детали; b1 – величина перебега круга; ад – коэффициент
температуропроводности обрабатываемой детали. Следовательно, можно определить значение интенсивности источника тепла,
если известны режимы шлифования и теплофизические параметры (l, с, g, а)
обрабатываемой детали и шлифовального круга.
Анализ вышеизложенного позволяет сделать следующие выводы: повышение скорости шлифования приводит к уменьшению количества
тепла, уходящего в деталь. Это может быть объяснено увеличением скорости деформации, способствующей большей концентрации
тепла в стружке, а также ростом охлаждающего действия абразивного круга, подающего в зону источника большее количество
холодных абразивных зерен. Степень влияния режимов на количество тепла Q с увеличением скорости шлифования увеличивается.
Интенсивность теплового потока зависит от общего количества тепла, попавшего в деталь, площади шлифования, глубины
шлифования и продольной подачи. Таким образом правильно подобранные для конкретных условий обработки режимы резания
и связка существенно увеличивают период стойкости инструмента и качество обрабатываемой поверхности, исключая прижоги и термические трещины.
|
8 Заключение и перспективы исследования |
Ранее были описаны шесть основных задач выполняемой работы, первые две – успешно завершены, а именно:
- проанализированы и обобщены известные физико-механические свойства связок, произведена оценка факторов влияющих на
качество поверхностного слоя материала и работоспособность абразивного инструмента;
- рассмотрены существующие силовые и тепловые зависимости процесса шлифования.
Остальные части работы будут завершены предположительно в сентябре-октябре сего года, после чего последует серия экспериментов,
подтверждающих работоспособность компьютерной модели, а уж после будут сделаны основные выводы и рекомендации.
|
Cписок литературы |
- Захаренко И.П. Алмазные инструменты и процессы обработки. – К.: Техніка, 1980. – 215 с.
- Ящерицын П.И., Зайцев А.Г. Повышение качества шлифованных поверхностей и режущих свойств абразивно-алмазного инструмента. – Минск, "Наука и техника", 1972. – 480 с.
- Ящерицын П.И., Цокур А.Н., Еременко М.Л. Тепловые явления при шлифовании и свойства обрабатываемых поверхностей. – Минск, "Наука и техника", 1973. – 184 с.
- Маслов Е.Н. Основы теории шлифования металлов. – М.: "Машгиз", 1951. – 179 с.
- http://www.uran.donetsk.ua/~masters/2000/mehf/strelkov
- http://www.techno.edu.ru
|
|
|
|