New Pump Technology May Improve Small Package Plant
Treatment
NSFC Staff Writer Natalie Eddy
Editor’s Note: A major part of the
National Small Flows Clearinghouse’s mission is to report on new
technologies as we become aware of them. It is in that spirit that we
present this article. Mention of a product or service in a Small Flows
Quarterly article is not an endorsement by the NSFC. All manufacturers and
consultants who have not registered themselves in the NSFC’s database are
invited to do so by calling our technical services
department.
Small flow wastewater treatment package plants (plants treating
fewer than one million gallons per day) have a history of poor settling in
the final clarifier, but a new wastewater treatment package plant pump,
called the Geyser Pump, may be the long-awaited answer for
operators. “Being an operator for a wastewater treatment package plant
can be a nightmare,” said Warren Peace, who has installed Geyser Pumps in
seven plants in West Virginia, Virginia, Kentucky, Tennessee, and
Maryland. According to Peace, all of the system operators have experienced
improvements. “These small package plants are 10 times more difficult to
operate than full-size systems because of the difficulty in
maintaining a solids inventory. “The discovery of this pump was
very liberating. I wanted to get the word out to these plant operators
that there is a solution. Finally, a pump that can handle a 2-inch solid,
has no moving parts, and has the capability to accurately deliver very low
rates of flow, typically less than 2 gallons per minute.” Peace, an
environmental engineer who owns Advanced Engineering Services of Botetourt
County, Virginia, said the device gives wastewater treatment plant
operators with plants processing fewer than 40,000 gallons per day (gpd)
the same measure of control as operators of plants processing 10 million
gpd. Masao Kondo, who holds a doctorate in mechanical engineering and
owns NCA2 of Dunn, North Carolina, developed the pump. Peace contacted
Kondo after learning about the pump from a friend who had attended a
presentation about it at a conference in North Carolina. The two worked
out an agreement to distribute the pump, and Kondo received a patent for
the device in December 2000.
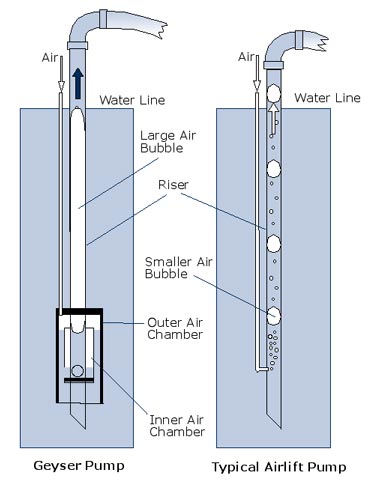 The Theory “The difficulty in controlling
solids in the clarifier is due primarily to the method of sludge return,”
said Peace. “If the population of biological solids (mixed liquor
suspended solids—MLSS) gets very high, greater than 3,500 milligrams per
liter, or if the plant experiences an upset, solids will exit the
clarifier.” “In many small systems, the rate of flow reduces residence
time in the final clarifier to less than one hour.” He explained that
in a typical airlift pump, air rises and pushes the effluent along when
the air’s buoyancy is greater than the weight of the liquid. However, the
trouble arises because there is no way to control the amount of air
delivered. “Airlift pumps are nice, but they are either on or off,”
said Peace. “If you try to slow them down, they just stop. With the Geyser
Pump, the air bubble is made in a separate chamber. You can control the
formation of that bubble by how fast you put air into the line. “If you
want to pump 2 gallons per minute and have a gallon of fluid in the riser
of a 2-inch line, you would want the pump to pulse twice a minute. You
would have to fill the chamber at a rate that produces a bubble twice a
minute and then you would have 2 gallons per minute. It’s that
simple.” Peace said with the Geyser Pump, return rates can be reduced
to 100 percent of influent flow or lower, if necessary. The old airlift
method is very reliable, according to Peace, provided the operator
maintains an adequate supply of air to the system. Conversely, if the air
supply is not adequate, the pump will stop operating. Pump It Up The idea that the Geyser Pump is based on
is not a new concept. In fact, the idea of using air to move liquid
originated in the 1780s, according to Peace. For years, an airlift
pump consisted of a vertical tube with 60 percent of its length submerged,
and an air supply line entering the vertical tube greater than four pipe
diameters from its end. If the air flow is sufficient, the buoyant force
of the bubble will grow greater than the weight of the column of liquid
above it pushing the liquid out of the end of the tube. “The greatest
advantages of airlift pumps are their lack of moving parts and their
ability to move large or heavy solids,” said Peace. “One of the greatest
disadvantages to using an airlift pump is its limited useful range of
flow. If airflow to a typical airlift pump is reduced by a relatively
small amount, it will cease to operate. “The Geyser Pump significantly
improves the characteristic advantages of the airlift pump, while allowing
it to operate over a much larger range of flow rates.” Peace explained
further that the bubble is produced in a chamber outside of the pump
riser. Air is supplied to an airtight dome that has the pump riser
extending through the center. Inside the dome is a second, smaller,
inverted air dome with the pump riser also extending through its
center. “Imagine the old diving bell that looked like a bucket on the
divers’ heads,” said Peace. “We’ve taken a dome or diving bell and placed
a pump riser through it with an additional cylinder that puts air inside
until the air pressure rises.” An entrance is provided to the riser
pipe, capable of allowing a bubble greater than the diameter of the pipe
to enter. As air is applied to the larger dome, the pressure inside
increases until it is greater than the pressure of the column of water in
the pump riser. “When this condition is met, a bubble is released from
the air dome into the pump riser. Then, just as in a typical airlift pump,
the bubble rises and carries the column of liquid in the riser out the end
of the pipe,” Peace added. “This sounds very simple, but it is
revolutionary in two ways. First, it requires the use of significantly
less air to operate relatively large airlift pumps. Second, it allows an
airlift pump to provide a very predictable and controllable rate of
flow.”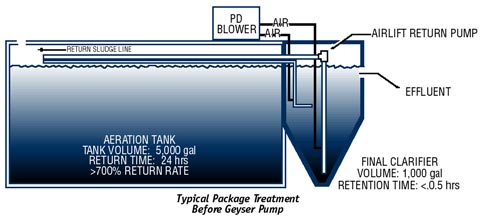 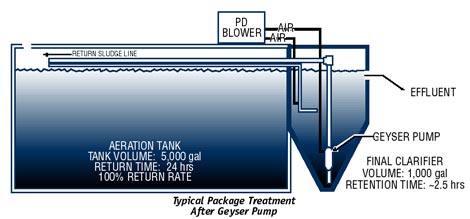 Getting
Pumped Installing the Geyser Pump is relatively simple and
inexpensive. The installed cost of the device can be less than $500,
depending upon the job specifications. “All you have to do is just unscrew
the old one and put the new one in,” Peace said. The pump is available
in a range of sizes and various construction materials, which can be
tailor-made to the application and the customer’s preference. Peace
said the pump also might be used in flow equalization, sludge mixing,
sludge transfer, chemical dosing, and many other applications outside the
wastewater treatment field. “This is the only thing out there that will
work on these small flow situations. I know the frustration of these
operators. They are sometimes blamed for their inability to control
something that up to now could not be controlled,” said Peace. First
Application Peace said the first application occurred near his
hometown, Eagle Rock, Virginia, on a 20,000 gpd package plant. The plant
had received a new permit that required a stringent nitrogen limit.
“They were trying to increase the sludge age,” Peace said. “As they
tried to raise the concentration, they had difficulty in maintaining a
solids inventory. I have seen that problem with every package plant I have
operated. “A few months before, I had come across material on this new
pump at a conference a friend had attended in North Carolina. The part
that intrigued me was the air pump that was fully controllable and could
be set to whatever rate you needed to feed the plant and return the
sludge.” Peace said that after they installed the Geyser Pump at the
Eagle Rock plant, the response was immediate. “It was like throwing a
switch. The effluent was considerably lower in solids. A few months later,
the ammonia level was less than 1 mg/L for total suspended solids, and
biochemical oxygen demand was in the single digits,” said Peace. “Today,
the plant is still perking along, doing better than ever. In the meantime,
we have installed pumps in six other package plants.” Hello Operator Paul Peery, utility supervisor
for Botetourt County Public Works Department package plant, believes the
Geyser Pump will make a long-lasting impact in the package plant industry.
“I think the pump has made a big improvement in the package plant
treatment process,” said Peery, who oversees the Eagle Rock facility and
has been an operator for 12 years. “Our plant was the first wastewater
treatment plant where the Geyser Pump was used. Basically it was installed
on a trial-and-error basis to see how it was going to handle. I wasn’t
sold on it in the beginning. I was concerned that it would stop up, but it
does an excellent job. I don’t think you can stop them up.” Ammonia
levels have gone down at Eagle Rock, a 10-year-old, 20,000 gpd package
plant, since the pump’s installation six months ago. The plant’s levels
went from 7 milligrams per liter to less than 0.2 after installing the
pump, allowing the plant to more than meet their set limit. “What we
ran into is pretty much what every package plant runs into. There was no
accurate way of controlling the sludge rate without stopping up the
system,” said Peery. “The thing about the Geyser Pump is it gives you
the ability to better control the return sludge rate versus package plants
with the air lift return design. You can set it to pulse at a wide variety
of second or minute intervals. The control of air pressure sets the length
of time it takes for the sludge to fill the vault of the pump, increasing
the retention time in the clarifier. The longer retention time in the
clarifier helps reduce the ammonia levels.” Peery said the pump can be
interchanged into the design of different systems “easily and affordably.”
He added that he would recommend the pump to other package plant
operators. Arville Anderson, who operates a wastewater treatment
package plant in Middlesborough, Kentucky, agrees that the pump is a
success. “It appears to be working really well for us,” said
Anderson. “We’re a small package plant with a flow of 5,000 gpd. We had
been having problems regulating the return sludge flow. Since we installed
the new pump, we are able to reduce the flow without stopping the line. We
couldn’t regulate our return flow before. We just had a constant flow. If
we would try to shut down the lines, they would clog. It has given us a
more consistent return and better looking effluent.” Anderson said the
pump has been in place for three months at the 15-year-old facility,
located in Southeastern Kentucky. Anderson could not recall the exact
price of the pump installation but said it was not very expensive. “We’ve
not only saved money, but it has allowed us to meet our effluent limits a
lot easier for our permit. “I think it’s really made a big impact on
operations of the plant,” said Anderson, who has worked at the residential
wastewater facility for the past 10 years. “I recommend it for any
small treatment plant.”
www.nesc.wvu.edu/nsfc/Articles/SFQ/SFQw02_web/SFQw02_NewPump.html
|