Geomechanics 96, Rakowski (ed.), Balkema, Rotterdam. - 1997. - p.319-321. ISBN 90 5410 921 1
Increase of destroying ability of pulsing jets by application of hydrodynamically-active substances
A.B.Stupin, A.P.Simonenko
Donetsk State University, Ukraine
B.S.Lubarskiy, A.F.Pertsev
State Paramilitary Mine Rescue Service, The Ministry of Coal Industry, Ukraine
V.S.Kolomiets
Donetsk State Technical University, Ukraine
ABSTRACT: In the report the opportunity of the increase of the work productivity of a pulsing jet generator, without the change of its design, is shown by using of water solutions of hydrodynamically-active polymers as operating fluid instead of water. The preparation of such operating fluids is provided through erosion specially developed hard water soluble polymer compositions in flowing cassette. The results of the tests on the destruction of plaster and coal-cement blocks of various durability have demonstrated, that the jet of a water solution of polymer composition has an increased destroying action in comparison with clean water at the expense of the increase of the depth of punched aperture about 1.5 — 3.5 times.
Numerous researches (Timoshenko G.M. & Bugrik V.A. 1989, Bugrik V.A., & Ovcjannikov V.P. 1981) have proved the opportunity of the use of pulsing jets for the destruction of various hard materials. For the expansion of the area of the application of hydropulsing engineering it is necessary to improve the geometrical and dynamic parameters of the jet. Traditional ways of improvement of these parameters such as the increase of the nozzle diameter forming the jet and increase of pressure; choice of a rational flowing part of the executive body are connected with the necessity of introducing significant changes in the design of the main units and increase of the capacity being consumed by the generator.
In the case of the industrial use of hydro-pulsing machines it needs to decrease hydraulic losses in the supplying pipelines so as, in some cases they can reach 25%. The most important problem in the use of hydropulsing engineering is the increase of the destroying action of a jet in blind apertures with the depth 0.2 - 0.3 m and more, since in this case its interaction with the bulk of the material being destroyed acquires the character of a “discharging” jet, which sharply reduces the productivity of the hydropulsing machine.
One of the methods of the increase of the efficiency of the of an impulsing jet generator (IJG), without the change of its design can be the use of water solutions of hydrodynamically-active sub-stances such as operating fluid (for example, high-molecular polymers — polyethylenoxide, polyacrylamide and others). In the papers (Povh I.L. et al. 1981, Stupin A.B., Aslanov P.V. 1981) the possibility of the significant reduction of hydrodynamic resistance and of the impact on turbulence is shown by introducing the additions in a flow of Newtonian fluids. The efficiency of the application of hydrodynamically-active polymers depends on a number of factors. The main one of which is the process of solutions preparation. In recent years the works on the designing of various quickly dissoluble polymer compositions and special equipment to introduction in the flow of fluid are being carried out.
In the given work a hydrodynamically-active polymer polyethylenoxide (PEO) hard water soluble polymer compositions (HWSPC) have been worked out, which, having the increased mass output, make it possible to produce the briquettes of the required geometrical form with the given surface of the mass output of PEO. Later on such briquettes have been installed in flowing cassettes and the used for the continuous express - preparation of hydrodynamically-active operating fluids of hydropulsing machines during the research of the destroying action of water jets and jets of the HWSPC solutions.
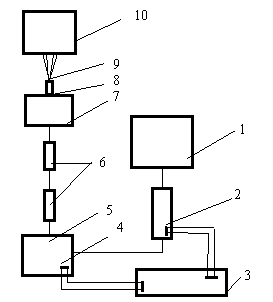
Figure 1
The basic scheme of placing the equipment for the period of comparative tests is shown in Figure 1, we used the following designations: 1 - capacity for water or HWSPC water solution; 2 - supplying pump; 3 - control panel; 4 - pumping plant; 5 - head pipeline; 6 - flowing cassettes with HWSPC briquettes; 7 -pulsing jet generator; 8 - working nozzle; 9 - pulsing jet; 10 - 1x1x1 m3 coal-cement (or plaster) block being tested.
The tests have been carried out in three conducted stages. At the first stage, investigations have been focused on the comparative valuation of the destroying action of a jet, the previously prepared homogenous solution and another one as the solution, obtained by erosion of the HWSPC briquettes in the cassettes during the supply of the operating fluid to IJG. At the same stage from the point of view of preservation the quality of the solution installation place of the cassettes has been chosen optimumly.
At the second and third stages the efficiency of the use of jets with addition and without them has been checked up by the destruction of blocks of plaster and coal-cement mixture. The results of these investigations are shown in Figure 2 - 3 and in Table 1.
In Figure 2 the dependences of the depth of a punched aperture in the plaster block on the time of the interaction of a jet are represented. Curve 1 is obtained for the water jet; curves 2 and 3 — done for previously prepared homogenous HWSPC solutions containing PEO, correspondingly, 0.002 and 0.004 % in weight; curves 4 and 5 correspond to the HWSPC solutions jets, prepared in the cassettes, when 25 minutes and 4 hours have passed after the contact of the HWSPC material with water. The initial distance from the nozzle outlet to the plaster block surface during tests was constant and equal to 0.14 m.
As it follows from Figure 2 the pulsing jets, of previously prepared similar homogenous HWSPC solution have higher destroying ability. But the depth of the punched aperture in comparison with a water
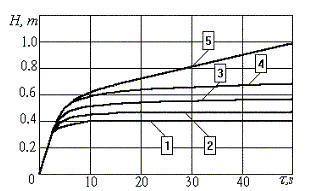
Figure 2
jets has increased moderately. This is connected with the mechanical destruction of PEO macromolecules in the supplying pump and in the pumping plant of high pressure. Hence, the use of the previously prepared HWSPC solution is inexpedient, and the cassettes with briquettes, aimed at preserving the quality of the solution, should be installed at the place of high pressure between the pumping plant and IJG. The increase of the time of contact of the HWSPC material with water increases the efficiency of the destruction of the plaster block (compare curve 4 and 5 Figure 2). This is connected with the increased of the PEO mass output from the briquette, which result in increasing the contents of hydrodynamically-active substance in the solution.
In Figure 3 the dependences of the depth of the punched aperture in the coal-cement block (coefficient of durability on the scale of Protodjakonov is equal to 1,6) on the of the jet interaction time are represented. Curve 1 corresponds to the destruction of the block by a water jet; curves 2 and 3 — by the jets of HWSPC solutions, prepared in two cassettes. For curves 3 and 2 the center of a punched aperture was at the distance of 0,35 m and 0,5 m from the lateral and top edges of the boiler, correspondingly. From the data given above it is evident, that if we use the HWSPC water solutions as a operating fluid, the depth of a punched aperture is 1,5 – 3,5 times (depending on the duration of the work of IJG) more than the depth of an aperture, punched by a water jet.
The results of the experiment on the destruction of a coal-cement block, the coefficient of durability of which is 2,5, are of a special interest. The experiment checked up the efficiency of the work of pulsing jets in the conditions of modeling a coal layer of the increased durability. It has been found out that pulsing jets from water and HWSPC water solutions punched in the block during 60 seconds of work apertures with depth 0,22 and 0,71 m, correspondingly.
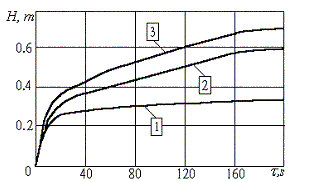
Figure 3
Table 1
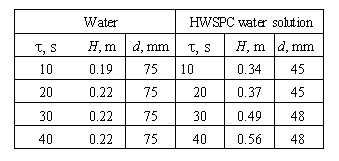
The further tests have been conducted on the determination of the depth H and diameter d of punched apertures as a function of the operation time IJG t. The results of tests are depicted in Table 1, from which it is evident, that the pulsing jet of water by 20 second punches in the block the aperture with depth 0,22 m and the further effect of a jet does not increase the depth of this aperture. At the same time during the time destruction of the block by a pulsing jet of the HWSPC solution the depth of a punched aperture increases and by 40 second becomes equal to 0,56 m.
The results of an additional experiment, modeling the process of hydroextractions of coal (the destruction of a coal-cement block by pulsing jets and by moving with the given speed along the border), have confirmed the increased efficiency of jets from the HWSPC solutions. Thus, for example, the depth of the crack, formed in the block after the momentary passage of a water jet, is 0,19 m, and after the passage of a jet of the HWSPC solution — 0,34 m.
The experiments carried out showed, that when using as operating fluid of the HWSPC solutions the diameter of a punched aperture decreases. Thus the water jet forms in the plaster block an aperture with the average diameter 77 mm, and the from jet the HWSPC solution — 52 mm. The similar results for a coal-cement block with the coefficient of durability 2,5 are 75 and 48 mm, correspondingly. It is connected with the fact, that hydrodynamically-active polyethylenoxide increases not only the effective range of jets, but their compactness, as well.
Thus, the use of water solutions of hydrodynamically-active polyethylenoxide as operating fluid, prepared from HWSPC in the flowing cassettes, improves the efficiency of the work of IJG without the change of its design. The increase of the efficiency is reached at the expense of the increase of the depth of a punched aperture and distance from the nozzle cut up to processed block, as well as the reduction of hydraulic losses in the flowing part of the main units of the generator and supplying pipelines.
REFERENCES
Bugrik V.A. & V.P. Ovcjannikov 1981. The introduction of cutting work at the mines with the common technology during the use of pulsing water jets. The elaboration of the deposits of natural resources, 87: 91 - 96.
Povh I.L., Stupin A.B. & A.P. Simonenko 1981. The use of SAS for decrease of a turbulent friction of liquids in technological devices. Aerodynamics in technological processes: 230 -240. Moscow: Nauka.
Stupin A.B. & P.V. Aslanov 1981. Turbulent structure of flow with additives reducing friction. Eng-neering-physics J. 41(5): 809 - 814.
Timoshenko G.M. & V.A. Bugrik 1989. Hydropulsing hacking — a promising way of the excavation of coal of the mines with the common technologies. The coal of Ukraine, 6: 13 - 14.