УДК 622.232.5: 532.517.6: 532.232.72
Способы и средства создания безопасных и здоровых условий труда в угольных шахтахим - Сборник научных трудов. - Макеевка-Донбасс. - 2005. - с.81-88.
Гидроимпульсная струя на крутопадающих пластах
Н.С. Сургай, докт. техн. наук (УкрНИИпроект), В.С. Коломиец, канд. техн. наук, А.Л. Зуйков, инж. (ДонНТУ)
Рассмотрены варианты применения гидроимпульсной струи для ведения очистных, подготовительных и проходческих работ на тонких крутопадающих, в том числе и выбросоопасных пластах. Описан принцип действия генератора импульсных струй положенного в основу гидроимпульсных установок
Высокоэффективное функционирование экономики любой страны невозможно без широкого использования собственных топливно-энергетических ресурсов. На уровне с природным газом и нефтью, запасы которых недостаточны для удовлетворения собственных нужд, важную роль в топливно-энергетическом балансе Украины играет уголь, роль которого в ближайшем будущем будет повышаться [1].
Учитывая это, не вызывает сомнений актуальность проблемы поиска новых путей существенного повышения эффективности угледобычи. Решение ее, по мнению многих исследований [2], неразрывно связано с созданием и освоением технологий и оборудования более высокого уровня для всех звеньев технологической цепочки подземной угледобычи, обеспечивающих как высокие технико-экономические показатели, так и получение качественного топлива, и улучшение условий труда горняков.
Особенно актуальным является создания эффективных технологий и средств выемки тонких (в особенности крутопадающих) пластов обуславливается также высокой актуальностью включения в разработку размещенных в них запасов. По данным [2, 3, 4] крутопадающие пласты в Украине, Российской Федерации, Германии, Франции, Испании и др. странах содержат большие вскрытые запасы угля ценных марок. Так, в Донбассе на тонкие и весьма тонкие пласты приходится около 45-50% всех запасов. Только ЦРД во вскрытых пластах мощностью 0,3 – 0,6 м содержит более 900 млн. т. коксующегося угля. Тем не менее, удельный вес добычи из них не превышает 18% [7], и в последние десятилетия этот показатель непрерывно сокращается, как в Украине, так и за рубежом.
Одна из причин этого кроется в том, что из-за неблагоприятных условий развитие средств механизации выемки этих пластов значительно отстает от развития выемочных средств для пластов пологого и наклонного падения. Отработка тонких крутопадающих пластов, в основном, ведется отбойными молотками, реже комбайнами с индивидуальной крепью, чаще всего с присечкой боковых пород, что приводит к ухудшению качества угля и снижению нагрузки на забой при высокой трудоемкости процесса угледобычи.
Из-за низкого уровня механизации угледобычи технико-экономические показатели и безопасность работ на шахтах с крутопадающими пластами низкие. Так, на шахтах Центрального района производительность труда подземного рабочего на выход составляет 3,5 – 4,8 т, затраты пневмоэнергии на 1 т добытого угля 100 –120 кВт•ч, расход леса около 65 м3 на 1000 т. Эти показатели находятся в прямой зависимости от горногеологических условий.
Необходимо также отметить, что механическое воздействие на пласт провоцирует внезапные выбросы на пластах опасных по выбросам угля и газа в незащищенных зонах [5].
Разработка способов выемки крутопадающих пластов, которые обеспечивали бы эффективную и безопасную их отработку, в том числе и опасных по внезапным выбросам и с включающими породами средней и ниже средней крепости, является актуальным инженерно-техническим заданием.
Анализ состояния отечественных и зарубежных работ по созданию средств выемки крутопадающих пластов показывает, что решить эту проблему только с помощью механического разрушения исполнительными органами режущего действия не удается.
Большие резервы успешного решения поставленных задач кроются в расширении подземной гидравлической отбойки угля, технико-экономические показатели которой выше, чем при традиционной технологии [2, 4]. При гидравлическом способе отбойки полезного ископаемого, особенно в случае применения высоконапорных импульсных струй, затраты энергии на 1 т отбитого угля можно довести до уровня лучших показателей при механическом разрушении (0,5 – 1,0 кВт•ч/т), а производительность труда рабочего по добыче увеличить в 1,5 раза и более в сравнении с показателями механизированных забоев. Гидравлические технологии и средства их реализации успешно применяются как в странах СНГ, так и за рубежом (в Японии, КНР, Австрии, Канаде, Германии) [7]. Добившись значительных успехов при разработке средних и мощных пластов, гидромеханизация имеет более скромные достижения при отработке тонких пластов.
Мировой научный опыт свидетельствует, что важнейшими положительными качествами, в случае применения их при выемке тонких и весьма тонких пластов, будут обладать выемочные машины с гидроимпульсными исполнительными органами [2, 6, 8]. Они, при малых габаритных размерах и массе, производя разрушение угольного массива импульсной струей воды, обеспечат гарантированную взрывобезопасность, почти полное пылеподавление и хорошую приспосабливаемость к изменяющейся гипсометрии пласта. Однако, в настоящее время в мировой практике машин, осуществляющих выемку тонких крутопадающих пластов угля импульсными струями воды в условиях шахт с традиционной технологией, нет.
Результатом многолетней работы сотрудников Донецкого национального технического университета в области разработки гидроимпульсных устройств, обеспечивающих принятую для шахт обычной технологии влажность отбитого угля, стало создание генератора импульсных струй (ГИС), обеспечивающего преобразование малорасходного (до 0,0015 м3/с) стационарного потока рабочей жидкости высокого давления (до 32,0МПа) в импульсный повышенных мгновенных расходов (до 0,025 м3/с) того же давления.
В схему ГИС входят струеформирующий ствол с рабочим насадком, балластный гидропневмоаккумулятор, распределитель (главный клапан), поршневой накопитель, рабочий гидропневмоаккумулятор и управляющий клапан.
Работа ГИС заключается в том, что распределитель периодически подключает к рабочему аккумулятору через накопитель либо насосную установку с балластным аккумулятором (фаза накопления), либо струеформирующий ствол с рабочим насадком (фаза выстрела). В начале осуществляется накопление в поршневом накопителе некоторого объема воды (около 300 – 350 мл), направляемой от высоконапорного питающего насоса малорасходным потоком. В фазу выстрела через насадок диаметром 10-12 мм истекает большерасходный импульсный поток (частота следования 2 – 7 Гц) почти того же давления, который и разрушает горный массив. Мощность потока в период выстрела воды составляет около 500 – 700 кВт. Именно большая мощность потока обеспечивает значительную разрушающую способность струи.
Генератор импульсных струй был положен в основу ряда гидроимпульсных установок предназначенных для выполнения различных технологических процессов в условиях шахт отрабатывающих как крутые, так и пологие пласты.
Гидроимпульсная выемочная установка ГИУВм-1 (рис 1) предназначена для выемки угля на весьма тонких крутопадающих пластах без постоянного присутствия рабочих в очистном пространстве. Технологией работ с применением комплекса оборудования ГИУВм-1 предусматривается выемка угля импульсной высоконапорной струей воды по традиционной схеме с применением комбайна [2].
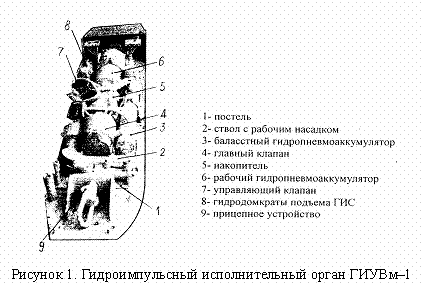
Комплекс оборудования ГИУВм-1 состоит из гидроимпульсного исполнительного органа с габаритами 0,29 x 0,4 x 2,0 м (рис. 2), лебедки подачи исполнительного органа, высоконапорной насосной установки, приборов контроля положения исполнительного органа в лаве.
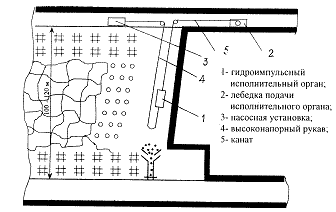
Рисунок 2. Отработанная технологическая схема выемки крутопадающего пласта гидроимпульсной установкой ГИУВм–1
Подвод рабочей жидкости к исполнительному органу от высоконапорной насосной установки, питаемой от противопожарно-оросительной сети, осуществляется по гибким рукавам с внутренним диаметром 12 – 20 мм. В качестве питающей установки при работе ГИУВм-1 использовали серийно выпускаемый ОАО «Новгородский машзавод» трехплунжерный насос СНТ.01.010, приводимый в движение пневмомотором К-75. Перемещение исполнительного органа ГИУВм-1 вдоль забоя с рабочей скоростью 6 … 10 м/мин осуществлялось серийной шахтной лебедкой 1ЛГКНм с пневмоприводом, обеспечивающей тяговое усилие не менее 50 кН. Возможен вариант применения электропривода на высоконапорном насосе и лебедке подачи при условии их расположения на откаточном штреке.
Управление всем комплексом оборудования, входящего в состав ГИУВм-1, осуществлялось дистанционно с пульта, смонтированного на вентиляционном штреке.
При выемке угля ГИУВм-1, перемещаемой вдоль забоя по челноковой схеме, обслуживали четыре человека: машинист и помощник машиниста, управляющие работой насосной установки и лебедкой подачи исполнительного органа, и двое рабочих, которые выгружали уголь в вагоны на откачном штреке.
Технологический цикл выемки гидроимпульсной установкой ГИУВм-1 состоял из следующих основных процессов: отбойка угля исполнительным органом путем образования импульсной струей врубовой щели вдоль всего забоя по линии контракта почва-пласт; доставка леса; зачистка забоя; крепление лавы; подготовка оборудования ГИУВм-1 к очередной выемке угля.
В результате приемочных испытаний опытного образца ГИУВм - 1 получены следующие показатели:
- за период испытаний из опытных лав добыто около 26,0 тыс. тонн угля. Максимальная техническая производительность при диаметре насадка 10 мм, величине подводимого к ГИС давления воды 27,0 МПа и расходе 5,4 м3/ч составила 1,4 т/мин (пл. «Толстый», мощность 0,7 м) и 3,0 т/мин (пл. «Мазурка», мощность 1,3 м). Эксплуатационная производительность составила в среднем 55 – 100 т/сутки и 170 – 200 т/сутки, соответственно. Эти показатели зависели, в основном, от квалификации рабочих, согласованности операций выемочного цикла и обеспеченности крепежным материалом;
- влажность отбитой горной массы не превышала 10%;
- пробы воздуха на исходящей струе, отобранные в период выполнения основной операции цикла, показали их качественное улучшение по сравнению с пробами из молотковой и щитовой лавы;
- установлено, что эффективность приведенной технологической схемы выемки тонких крутопадающих выбросоопасных угольных пластов гидроимпульсной установкой ГИУВм-1 без постоянного присутствия людей в очистном забое достаточно высока.
Машина буровая гидроимпульсная МБГИ-1 (рис. 3), в комплекте с дополнительным оборудованием (высоконапорной насосной установкой, подводящим высоконапорным ставом, средствами подачи на забой) предназначена для прохождения с помощью высоконапорных импульсных струй воды восстающих скважин по углю на крутопадающих пластах мощностью свыше 0,4 м.
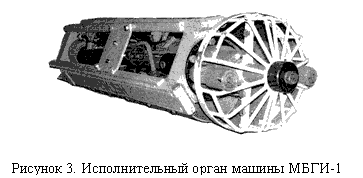
Питание МБГИ-1 рабочей жидкостью и комплектующего оборудования энергией, осуществляется аналогично установке ГИУВм-1.
Схема расположения оборудования в забое приведена на рис. 4.
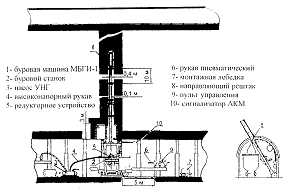
Рисунок 4. Технологическая схема бурения скважин МБГИ–1
Порядок выполнения нарезных работ следующий: после того, как МБГИ-1 подготовлена к выполнению очередного рабочего цикла (наращен став подачи, исполнительный орган находится вблизи забоя), открывается вентиль подвода воды к высоконапорному насосу и вентиль подвода воздуха к пульту управления пневмомоторами станка подачи и высоконапорного насоса. При запуске высоконапорного насоса автоматически происходит ввод ГИС в автоколебательный режим работы. После достижения его устойчивого режима работы (в течение 10 – 15 с. после запуска насоса) включается мотор на медленную подачу става вверх. После выдвижения става на длину секции производилось отключение подачи воздуха и воды на высоконапорный насос или переключение воды на сброс. Затем, с помощью захвата и манипуляций системой подачи станка, осуществлялась фиксация става подачи в захвате, отсоединение последней секции става от задней обоймы, спуск каретки станка подачи в нижнее положение, установка и фиксация следующей секции става подачи на задней обойме, соединение ее с зафиксированной в захвате секцией, снятие захвата и отключение воздуха, питающего моторы станка подачи.
На этом завершилась подготовка МБГИ-1 к выполнению следующего цикла.
При выполнении работ по прохождению скважины после того, как были произведены операции по соединению секций става и снятие захвата, без отключения воздуха от пневмомоторов станка подачи возобновлялся подвод высоконапорной воды к задней обойме и выполнение выше описанных операций.
Вытекающая из скважины пульпа попадала на штрек в специально изготовленной деревянный короб, из которого вода вытекала в канаву штрека, а уголь в конце смены убирался в вагонетку.
В результате приемочных испытаний опытного образца ГИУВм - 1 получены следующие показатели:
- за период испытаний в условиях пластов «Кулага» и «Соленый» пройдено 9 скважин диаметром 400 мм максимальной длины 106 м и общей около 500 м.
- отклонение скважины от заданного направления за счет отсутствия непосредственного контакта исполнительного органа с забоем составило не более 1 м.
- при эквивалентном диаметре рабочих насадков 12 мм, и давлением на выходе высоконапорного насоса 24,0 – 28,0 МПа техническая производительность МБГИ-1 составила 25 – 40 м/час, эксплуатационная – 4 – 6 м/час.
По результатам проведенных испытаний гидроимпульсных установок на ОАО «Днепропетровский агрегатный завод» изготовлена установочная серия ГИУВм-1 в количестве 4 штук и образец МБГИ-1, которые предназначены для отработки технологии комплексного использования в различных горногеологических условиях и решения вопроса серийного производства.
Кроме того, в настоящее время ведутся работы по созданию устройств использующих импульсные струи для образования разгрузочных пазов с последующей выемкой оставшейся пачки угля при проведении подготовительных выработок по выбросоопасным пластам.
Список использованных источников:
Сургай Н. С. Разработка и реализация перспективных программ развития угольной промышленности Украины: Автореф. дис. … канд. техн. наук. – Донецк, 1992. – 21 с.
Основы проектирования технологии безлюдной выемки угля: Учеб. пособие. К. Ф. Сапицкий, В. Д. Мороз. – К.: УМК ВО, 1991. – 132 с.
Новые направления технологии разработки крутых пластов Донбасса / Липкович С. М., Братишко А. С., Кучер А. Т., Цяпа Н. А. в кн.: Безлюдная выемка угля. – Сб. научн. тр. – Киев: Наук. думка, 1980. – с. 119 – 123.
Нетрадиционные технологические процессы добычи угля / В. Н. Потураев, С. А. Полуянский и др. – Киев: Техника, 1986. – 214 с.
Жуков В. В., Малюга М. Ф., Лунев С. Г. Концепция формирования нового направления выемки крутых пластов //Уголь Украины, 1993. – №11. – с. 3 – 5.
Коломиец В. С. Создания гидроимпульсного органа разрушения выемочной машины для шахт обычной технологии: Автореф. дис. … канд. техн. наук. – Донецк, 1984. – 23 с.
Мучник В. С., Маркус М. Н., Голланд Э. Б. Подземная гидравлическая добыча угля. – М.: Недра, 1986. – 223 с.
Тимошенко Г. М, Гулин В. В. Способ и средства гидроимпульсной отбойки угля для шахт “сухой” технологии /Донецк. политех. ин–т. – Донецк, 1994. – Деп. в ГНТБ Украины, №1276. – Ук. 94.