english
Главная страница ДонНТУ
Страница магистров ДонНТУ
Поисковая система ДонНТУ
E-mail: evgeni483@mail.ru
Главная страница
Электронная библиотека"
Перечень ссылок
Индивидуальное задание
Автореферат магистерской работы
на тему: "Совершенствование технологического обеспечения абразивной обработки тонкостенных цилиндрических
изделий"
Выполнил: Лепетуха Денис Евгеньевич
Научный руководитель: Михайлов Александр Николаевич
Тема магистерской работы: "Совершенствование технологического обеспечения абразивной обработки тонкостенных цилиндрических
изделий ".
1 Введение
Постоянное развитие техники на современном этапе требует использование деталей, представляющих собой тонкостенные оболочки. В настоящее время их количество значительно увеличивается в общей массе деталей, подвергаемых механической обработке. Оболочковые изделия, обеспечивая высокую прочность и плотность компоновки, находят широкое применение в самых разных отраслях промышленности и, что особенно важно, в наиболее важных областях: самолето- и ракетостроении, криогенной технике и холодильных установках, космических и военно-промышленных разработках.
Наряду с увеличением доли тонкостенных изделий в общей массе обрабатываемых деталей, повышаются и технические требования к точности размеров оболочковых поверхностей, формы и их взаимного расположения, требования к качеству поверхностного слоя. В особо точном (прецизионном) машиностроении эти требования достигают порядка микрометров и долей микрометра. Из-за основной особенности тонкостенных изделий – их малой жесткости, выполнение этих требований является довольно сложной задачей.
Наибольшие трудности при обработке оболочковых деталей возникают при решении вопроса их закрепления на станке.
В качестве окончательной обработки цилиндрических тонкостенных деталей применяют главным образом абразивную обработку. На этой стадии технологического процесса окончательно формируются параметры поверхностного слоя и размеры готовой детали.
Но не стоит упускать из вида и предыдущие стадии обработки, так как для таких деталей особенно остро стоит вопрос о технологической наследственности. Вопросам наследственности посвящены работы таких ученых, как А.М. Дальский, А.Г. Колесников, А.М. Дмитриев, А.С. Васильев, Б.М. Базров, Ю.А. Шачнев, А.И. Кондаков, П.И. Ящерицин, Э.В. Рыжов, А.Г. Суслов и другие.
Наследственные связи как повышают, так и понижают показатели качества, поэтому важно на каждом этапе изготовления прецизионных цилиндрических тонкостенных изделий учитывать их влияние на характеристики детали. Явление технологической наследственности позволяет формировать оптимальные технологические среды и изменять свойства предмета обработки в желаемом направлении, в том числе, на жизненный цикл. Одним из важнейших факторов, который влияет на качество деталей, является сила закрепления заготовки в технологическом приспособлении. Значимость этого фактора для качества деталей отмечалась еще в работах основоположников машиностроения В.М. Кована, В.С. Корсакова, А.П. Соколовского, А.Б. Яхина.
Наложение сил закрепления на обрабатываемую заготовку приводит к возникновению деформаций и, как следствие, возникновению погрешности. Для тонкостенных изделий, характеризующихся малой жесткостью, погрешности, связанные с наложением сил закрепления могут принимать весьма значительных величин, поэтому этот фактор является определяющим при конструировании приспособления и подборе оптимальных режимов обработки. Особое внимание на это следует обращать внимание при шлифовании прецизионных тонкостенных цилиндров, так как в этом случае погрешности от сил закрепления могут превысить допуск на их изготовление и вывести их из разряда прецизионных.
Так же при шлифовании тонкостенных цилиндров возникают высокие температуры в зоне резания, в результате чего могут возникнуть проблемы, связанные с прижогами, изменениями структуры металла и возникновением внутренних напряжений.
Отсюда вытекает еще одна проблема – подбор СОТС и определение наиболее приемлемой схемы охлаждения.
Цели и задачи работы
Как уже известно, наибольшее влияние на качество обработанных шлифованием тонкостенных цилиндров оказывает зажимное приспособление, поэтому решение проблемы закрепления таких заготовок сводится к исследованиям в области технологической оснастки. Для шлифования таких заготовок наиболее рационально применять приспособления с распределенными силами закрепления. Такие приспособления ориентированы на равномерное распределение усилий закрепления или стремящиеся к нему (множественность точек приложения). Считается, что равномерно распределенные силы приводят к равномерной деформации тонкостенной поверхности оболочковой заготовки. Однако на практике при шлифовании тонкостенных цилиндров прецизионных деталей обнаружились погрешности формы. Это связано с так называемым краевым эффектом.
Наиболее заметно влияние краевого эффекта при шлифовании деталей с жесткими требованиями отклонения формы оболочковой поверхности. Эти отклонения сравнимы с величиной погрешности формы. В таком случае необходимо прибегать к преднамеренному искажению поверхности цилиндра. Суть преднамеренных искажений состоит в создании сил закрепления, распределенных по определенному закону. В настоящее время ведутся работы в области технологии машиностроения, связанные с заданным неравномерным распределением сил закрепления. Но оснастка, обеспечивающая любой заданный закон распределения еще не получила распространения на производстве. Явления, связанные с преднамеренными искажениями, рассматривались в работах Ш.М. Билика, А.М. Дальского, М.П. Новикова и других ученых.
Отсюда вытекает цель работы: исследовать методы закрепления прецизионных тонкостенных цилиндров, разработать способ, существенно уменьшающий возникающие погрешности формы и найти оптимальное соотношение между величиной усилий закрепления и глубиной резания.
Основные задачи: в зависимости от показателей качества определить область применения технологической оснастки; разработать методы определения погрешности формы при закреплении тонкостенных цилиндрических изделий; предложить конструктивные подходы и методы расчета оснастки для создания любого заданного закона распределения силы закрепления с целью уменьшить погрешности формы особо точных тонкостенных цилиндров.
Предполагаемая научная новизна: планируется разработать методы определения погрешности формы при закреплении тонкостенных цилиндров; разработка принципов, на основе которых возможно конструирование технологической оснастки с распределением сил закрепления по требуемому закону.
Обзор существующих исследований и разработок
Проблема шлифования тонкостенных цилиндрических изделий является малоизученной, о чем можно говорить исходя из некоторого дефицита информации по этому вопросу. Это прежде всего связано с областью применения самих тонкостенных изделий, которые только начинают широко использоваться. Так же изучение напряженно деформированного состояния требует применение мощного математического аппарата, который в свою очередь требует мощной вычислительной техники, которая появилась сравнительно недавно.
В настоящее время ведутся работы, посвященные вообще обработке тонкостенных изделий, особое внимание при этом уделяется вопросу закрепления нежесткой заготовки.
Так, например, в работе Д. Д. Евсеева, А. С. Тарапанова, к. т. н., профессора
Орловского государственного технического университета О ДОПУСТИМЫХ УСИЛИЯХ РЕЗАНИЯ ПРИ ТОКАРНОЙ ОБРАБОТКЕ ТОНКОСТЕННЫХ ЦИЛИНДРИЧЕСКИХ ОБОЛОЧЕК рассматривают процесс токарной обработки как наиболее приемлемый. Это связано с тем, что высокая склонность к упругим температурным деформациям тонкостенных элементов при их окончательной обработке шлифованием вызывает погрешности формы элементов деталей и их поверхностей. Использование тонкого точения взамен шлифования позволяет исключить шаржирование абразивом, трещины и прижоги.
Решающее значение на эксплуатационные свойства нежестких тонкостенных деталей оказывает точность формы и размеров. В процессе токарной обработки возникает трудность в обеспечении точности, обусловленная деформацией обрабатываемой детали резцом.
В свете вышесказанного возникает необходимость расчета допустимых сил резания, с целью назначения оптимальных режимов резания.
Расчетная схема представляет собой цилиндрическую оболочку, защемленную с одного торца и нагруженную с другого торца усилиями резания в виде трех сосредоточенных сил. Для описания напряженно-деформированного состояния оболочечного элемента используем полубезмоментную теорию расчета цилиндрических оболочек В. З. Власова, что позволяет рассмотреть неосесимметричное нагружение оболочечного элемента. В этой теории, кроме общих гипотез теории оболочек Кирхгофа-Лява: гипотезе о неизменности нормалей, позволяющей свести исследование деформации оболочки к исследованию деформации ее срединной поверхности, и гипотезе о ненадавливании одного слоя оболочки на другой, что позволяет рассматривать напряженное состояние в оболочке как плоское, введены дополнительные допущения.
Оболочками в теории упругости принято называть тела, ограниченные двумя криволинейными поверхностями, расстояние между которыми мало по сравнению с прочими размерами тела.
Геометрическое место точек, равно удалённых от обеих поверхностей, является срединной поверхностью оболочки.
Срединная поверхность, толщина и граничный контур в совокупности полностью определяют оболочку с геометрической стороны.
Задачею теории оболочек как отдела теории упругости, является изучение их деформации под действием заданной нагрузки. При этом будем считать материал оболочки изотропным и следующим закону Гука, а перемещения её точек – малыми сравнительно с толщиною.
Различаются оболочки тонкие и толстые. Тонкою будем называть такую оболочку, для которой максимальным значением отношения толщины к радиусу кривизны срединной поверхности можно пренебречь по сравнению с единицей. Соответственно толстою назовем такую оболочку, для которой подобное пренебрежение недопустимо. Допуская обычную для технического расчёта относительную погрешность 5%, будем считать тонкими такие оболочки, у которых
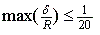
а оболочки, у которых это неравенство не соблюдается, будем считать толстыми.
Заметим, что оболочки обладают весьма выгодными упругими свойствами и при рациональном проектировании могут выдерживать значительную нагрузку при минимальной толщине. Данное свойство оболочек позволяет создавать из них конструкции весьма легкие при достаточной прочности и способствует широкому применению подобных конструкций в самолётостроении, кораблестроении, строительстве железобетонных сооружений – везде, где малый вес является жизненно необходимым свойством конструкции. При этом подавляющее большинство встречающихся на практике оболочек имеет толщину, лежащую в диапазоне
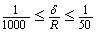
т.е. принадлежащих к числу тонких оболочек, вследствие чего именно теория тонких оболочек представляет наибольший практический интерес.
При рассмотрении деформации оболочки считаем выполненными такие допущения (гипотеза Кирхгофа-Лява), согласно с которыми:
1) прямолинейный нормальный к срединной поверхности элемент оболочки остается прямолинейным и нормальным к деформированной срединной поверхности, сохраняя при этом свою длину;
2) нормальными напряжениями на площадках, которые параллельны срединной поверхности, можно пренебречь в сравнении с аналогичными напряжениями на площадках, которые перпендикулярны срединной поверхности.
Суть этой гипотезы состоит в том, что упругое относительное удлинение в нормальном к срединной поверхности направлении и поперечное смещение принимаются приблизительно такими, которые равняются нулю, и считается, что нормальное напряжение на площадке, параллельной срединной поверхности, не влияют существенно на величины относительных удлинений в тангенциальной плоскости.
Что касается напряженно-деформированного состояния, возникающего при шлифовании тонкостенных цилиндрических изделий, то для того, чтобы определить универсальную характеристику, отражающую цель технологического воздействия и вид базовой технологической поверхности проводится классификация видов распределенной нагрузки. Эту характеристику в дальнейшем можно использовать как основу для описания любого вида распределенной нагрузки. Проведенная классификация показала, что таким общим свойством можно считать интенсивность, изменяющуюся по любому закону. Тогда любой закон распределения сил закрепления, в том числе и равномерно распределенный, является частным случаем.
Для исследования возникающей вблизи краев погрешности формы для определения вида этой погрешности необходимо пользоваться положениями теории упругости для тонкостенных оболочек. Уравнение равновесия для цилиндрической оболочки вдоль оси запишется:
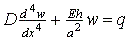
где w – компонент смещения элемента оболочки в направлении радиуса заготовки от наружной поверхности к центру; a - средний радиус оболочки; q- интенсивность нагрузки; Е – модуль упругости материала заготовки; h – толщина оболочки; D – жесткость оболочки при изгибе:
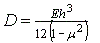
где мю - коэффициент Пуассона материала заготовки.
Для упрощения записи и восприятия уравнения равновесия в теории оболочек введено обозначение:
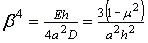
Тогда уравнения равновесия для цилиндрической оболочки заготовки можно записать:
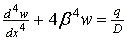
Из оболочки двумя меридиональными сечениями выделяется элемент – элементарная полоска, которая рассматривается как бесконечно длинная полоска, расположенная на упругом основании. Теоретическая зависимость погрешности формы от распределения сил закрепления рассматривается для наиболее распространенного случая распределения сил – равномерно распределенного. Кроме того, рассуждения и математические выводы для этого случая используются в качестве основы для других видов распределения и других видов оболочковых заготовок не только в теории оболочек, но и в инженерных расчетах.
В ходе исследований было определено, что равномерно распределенные силы закрепления вызывают неравномерную деформацию вблизи краев, фланцев, вырезов, отверстий и других конструктивных элементов, изменяющих жесткость заготовки. Вблизи краев увеличение w радиуса составляет (1):

где Q- сила закрепления; l – длина заготовки (зоны приложения силы закрепления); Е - модуль упругости материала заготовки; бэтта - коэффициент, который рассчитывается по формуле:
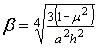
где мю - коэффициент Пуассона материала заготовки. А в средней части:

Используя аналогичные рассуждения можно получить выражение для прогиба оболочковой поверхности вблизи других конструктивных элементов. Например, вблизи фланца прогибы рассчитываются:

где х – расстояние от фланца. На рис. 1 изображены графики прогибов образующей оболочковой заготовки от действия равномерно распределенных сил закрепления вблизи края зубчатого колеса (рис. 1, а) и у фланца гладкой оболочковой поверхности (рис. 1, б).
Рисунок 1а – Прогибы образующих оболочковых поверхностей
Полученные зависимости для увеличения радиуса заготовки позволяют оценить величину погрешности формы оболочковой детали и определить случаи, когда величина этих погрешностей будет оказывать существенное влияние на наследственную составляющую погрешности формы, или когда погрешность от закрепления превышает допуск или составляет от него значительную часть. Тогда при разработке технологического процесса следует принять меры к уменьшению этой составляющей суммарной погрешности. Данные исследования показали, что при равномерно распределенной силе закрепления обрабатываемая оболочковая поверхность деформируется неравномерно. Поэтому для уменьшения этой погрешности необходимо создать неравномерную нагрузку.
Неравномерно распределенные силы закрепления могут быть созданы, например, тепловым способом. Здесь важно найти взаимосвязи температуры нагрева обрабатываемой поверхности и погрешности формы оболочковой поверхности заготовки.
Рисунок 1б – Прогибы образующих оболочковых поверхностей
Известно, что 80% внешней работы, затрачиваемой на шлифование, преобразуется в теплоту и только 20% - в потенциальную энергию деформации кристаллической решетки. При шлифовании нагревается все изделие, но в зоне контакта поверхности абразивного круга и шлифуемого изделия температура может быть очень высокой.
Рентгенографический анализ поверхностных слоев шлифуемой закаленной стали показывает наличие увеличенного содержания остаточного аустенита. Это указывает на процесс вторичной закалки, протекающий при шлифовании закаленных сталей, для чего необходима температура выше температуры аустенитового превращения (800’C). При работе отдельных невыгодно ориентированных зерен может возникнуть температура до 1600’С.
Однако время воздействия этой температуры весьма незначительно. На это указывает то обстоятельство, что при шлифовании незакаленных сталей структура поверхностных слоев обычно не изменяется, так как для структурных изменений незакаленных сталей требуется большая выдержка при высокой температуре, чем закаленной.
При соблюдении заданных режимов шлифования поверхность изделия из закаленной стали имеет тонкий слой измененной структуры, возникший в результате вторичной закалки и высокого отпуска.
В тех случаях, когда шлифование производилось с повышенными скоростями, режимами или с применением затупленных кругов, образуются местные глубокие изменения микроструктуры стали – ожоги. Они возникают в результате высокой концентрации теплоты в малых объемах металла. Во всех случаях, наличие ожога на поверхности металла служит причиной для окончательной забракованию изделия, так как ожоги часто приводят к внезапному разрушению изделий под нагрузкой.
Поскольку наибольшее количество тепла выделяется за счет трения круга о шлифуемую поверхность, то основные мероприятия, направленные на снижение температуры шлифования, заключаются в снижении коэффициента трения между кругом и деталью.Прежде всего необходимо обеспечить достаточно обильную подачу охлаждающей жидкости в зону резания и улучшение ее качества, так как смазочно-охлаждающая жидкость уменьшает коэффициент трения между кругом и деталью.
При увеличении скорости вращения шлифовального круга количество выделяемого тепла возрастает. С увеличением скорости вращения заготовки также возрастает выделение тепла, но одновременно сокращается продолжительность воздействия источника тепла, что снижает температуру шлифования.
Увеличение поперечной подачи во всех случаях ведет к росту температуры шлифования и продолжительности ее воздействия. Поэтому при шлифовании особенно важно применение малых чистовых подач и выхаживания в конце цикла, что позволяет получить поверхность без ожогов.
Температура шлифования возрастает при шлифовании слишком твердыми кругами, так как в этом случае затупившиеся зерня несвоевременно удаляются с поверхности круга и повышают коэффициент трения. Круги из белого электрокорунда выделяют меньше тепла в зоне шлифования, чем круги из нормального электрокорунда. Наиболее целесообразно для уменьшения возможного появления ожогов применять круги на бакелитовой связке и наименее – на вулканитовой.
Снижении температуры шлифования может быть достигнуто шлифованием пористыми и высокопористыми кругами. С увеличением пористости, т.е. с повышением номера структуры, уменьшается возможность появления ожогов, так как трение при этом меньше, лучше размещается снимаемая стружка, зерна круга легко обновляются. Температура шлифования зависит так же от скорости отвода тепла от места его образования, т.е. от теплопроводности шлифуемого материала. Чем выше теплопроводность, тем меньше вероятность возникновения ожогов. Поэтому для металлов с малой теплопроводностью необходимо ограничивать режимы шлифования.
Создание неравномерно распределенной силы закрепления возможно тепловым способом. Расчетная схема представляет собой сборку двух оболочковых деталей (рис. 2).
Рисунок 2 – Цилиндрическая оболочковая заготовка на оправке
Заготовка толщиной стенки hз и средним радиусом аз устанавливается на оправку с толщиной стенки hо и средним радиусом ао с гарантированным диаметральным сборочным зазором . Выражение для определения температуры нагрева системы оправка-заготовка учитывает диаметральный сборочный зазор, натяг d, связанный с силой закрепления заготовки и коэффициенты линейного температурного расширения материалов оправки и заготовки (aз, aо):
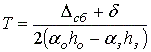
Закрепление оболочковых заготовок в термооснастке основано на увеличении линейных размеров сопрягаемых деталей. Чем больше толщина стенки детали, тем больше будет расширение при нагревании на одну и ту же температуру. Поэтому толщина стенки у оправки должна быть больше, чем у заготовки.
Связь температуры нагрева t1 заготовки для создания необходимой силы закрепления с увеличением радиуса (2):

где a - коэффициент линейного температурного расширения материала заготовки. Соответствие выражений (1) и (2) доказывает принципиальную возможность создания распределённых сил закрепления с помощью температурного поля. То есть, при равномерном температурном поле возникают такие же деформации оболочковой поверхности, как и при других способах создания равномерно распределенной нагрузки.
Принцип создания неравномерно распределенной силы закрепления состоит в получении неравномерно распределенного температурного поля.
Рисунок 3 – Погрешность формы от равномерно распределенных сил закрепления и распределения нагрузки для уменьшения этой погрешности
Уменьшение температуры нагрева в зонах, где прогибы от равномерно распределенных сил больше (вблизи отверстий, вырезов, фланцев, краев) позволит получить меньшие деформации обрабатываемой поверхности (рис. 3). Здесь w – прогиб оболочковой поверхности от равномерно распределенной нагрузки, q – эпюра равномерно распределенной нагрузки для уменьшения погрешности формы.
Реализация неравномерного температурного поля состоит в меньшей температуре нагрева края заготовки относительно средней части. Тогда сложное температурное состояние раскладывается на три элементарных (рис. 4) и температура для каждого из трёх состояний суммируется в соответствующих сечениях. Состояние А – это равномерный прогрев заготовки, прогиб рассчитывается по выражению (2). Состояние Б и В соответствуют прогибу заготовки:

где х – расстояние от сечения, где температура заготовки изменяется (т. О1 и О2).
Рисунок 4 – Схема распределения температуры в оболочковой заготовке вдоль оси
Расчеты по приведенным формулам показывают, что при разнице температур средней части и края порядка нескольких градусов погрешность формы оболочковой поверхности уменьшается.
Для того, определить температуру в любой точке поверхности заготовки в любой момент времени, используется дифференциальное уравнение теплопроводности:
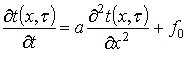
где t=t(x,t) – температура в точке с координатой x в момент времени t, (координата x отсчитывается от источника тепла); с – теплоемкость единицы массы материала заготовки ( удельная теплоемкость): r - плотность материала; l - коэффициент теплопроводности; f0 – плотность теплового потока:

где wТ– производительность источника тепла (количество выделяемого тепла в единицу времени в единице объема тела заготовки, Дж/м3*с); cr - теплоемкость единицы длины.
Дифференциальное уравнение теплопроводности дополняется начальными и граничными условиями. Начальные условия характеризуют распределение температуры t в заготовке в начальный момент времени t=0. примем, что температура заготовки перед началом технологического воздействия равномерна и равна температуре окружающей среды: t(x,0)=t0.
Граничные условия определяют взаимодействие заготовки с окружающей средой. В поставленной технологической задаче поверхность заготовки не имеет теплоизоляции, поэтому часть тепла через наружную и внутреннюю цилиндрические поверхности предаётся окружающей среде. Потерянное технологической системой тепло вычисляется по закону Ньютона: количество тепла qn, передаваемое в единицу времени с единицы поверхности в окружающую среду, прямо пропорционально разности температур поверхности тела t и окружающей среды t0:

где aТ – коэффициент теплоотдачи.
Решение дифференциального уравнения теплопроводности позволяет получить значения температуры заготовки в любой точке на расстоянии x от источника тепла в любой момент времени и представляется в виде матрицы. Решение, представленное в таком виде, удобно при определении разности температур Dt края и средней части, длины l более холодной зоны и для определения времени Dt, в течении можно производить технологическое воздействие на заготовку. Фактически, время Dt связано с основным технологическим временем и влияет на выбор режимов резания (скорости резания и подачи). Кроме этого важно и время, которое проходит до наступления интервала Dt. Оно определяет вспомогательное время на закрепление заготовки. Принцип работы оснастки позволяет совмещать основное и вспомогательное технологические времена.
Ряд параметров и положений не могут быть определены теоретически. Например, величина коэффициента теплоотдачи aТ может быть найдена только экспериментально и зависит от условий окружающей среды. Кроме того, на этом этапе исследования не известна скорость распространения тепла на обрабатываемой оболочковой поверхности и характер температурного поля (стационарный или нестационарный). Поэтому для определения этих положений и параметров, а так же для подтверждения теоретически полученных результатов были проведены экспериментальные исследования.
Планируемый практический результат. Планируемые собственные результаты
В ходе выполнения магистерской работы планируется исследовать напряженно деформированное состояние тонкостенной цилиндрической заготовки в результате наложения на поверхность оболочки равномерно распределенной нагрузки. На основании этого планируется разработка принципов, которые лягут в основу проектирования и построения приспособлений для закрепления заготовки при шлифовании.
Планируется определение зависимости изменения сил резания в зависимости от изменения глубины резания, а это в свою очередь окажет влияние на величину усилия закрепления, что может привести к излишней деформации тонкостенной нежесткой заготовки. Поэтому, следует определить оптимальную величину снимаемого слоя, чтобы иметь высокую производительность и требуемое качество готовой детали.
Планируется изучить влияние температур, возникающих при шлифовании, на жесткость оболочковой поверхности и качество поверхностного слоя, а также предложить методы борьбы с высокими температурами.
В магистерской работе предполагается привести классификацию тонкостенных изделий, изучение теории оболочек для описания напряженного состояния тонкостенных цилиндрических изделий, разработка конструкции зажимного приспособления, построение модели абразивной обработки оболочковой детали.
Заключение
Технологическое обеспечение шлифования тонкостенных цилиндрических изделий – тема, на первый взгляд, не сложная. Но в результате ее анализа всплывает большое количество проблем и задач, требующих решения.
Вся проблема заключается в том, что детали такого типа обладают малой жесткостью и приложение даже сравнительно небольших нагрузок может привести к возникновению погрешностей, соизмеримых с допуском. Малая жесткость тонкостенных цилиндров исключает любое точечное воздействие на оболочковую поверхность, поэтому единственным способом их закреплением является приложение распределенной нагрузки.
Но наложение равномерно распределенной нагрузки так же не является лучшим вариантом, т.к. в результате проявления краевого эффекта вблизи отверстий, вырезов, фланцев, краев заготовки наблюдаются погрешности формы, соизмеримые для прецизионных оболочковых заготовок с допустимым отклонением формы.
Все это приводит к необходимости разработать зажимные приспособления, в которых бы нагрузка распределялась не равномерно, а по требуемому закону, создавая в требуемых местах дополнительную излишнюю деформацию, а в некоторых наоборот – воздействуя с меньшим усилием. Исходя из этого, важным в этой теме является поиск принципов, позволяющих, как можно с меньшими затратами построить зажимное приспособление с возможностью создания распределенной нагрузки по любому требуемому закону для заготовок с различными конструктивными особенностями.
Для этого так же важно разработать методику определения требуемого закона распределенной нагрузки исходя из уравнений деформации тонкостенных цилиндров теории оболочек.
На основании экспериментов или моделирования процесса необходимо вывести зависимости сил резания на деформацию оболочки, из чего можно сделать вывод об оптимальной глубине резания, и вообще о влиянии этого параметра на изучаемый процесс.
Анимированная схема - основные направления исследования
СПИСОК ИСПОЛЬЗУЕМОЙ ЛИТЕРАТУРЫ:
1. Ящерицин П.И. Шлифование металлов. – М.: Машиностроение, 1970. – 360 с.
2. Маслов Е.Н. Теория шлифования материалов. – М.: Машиностроение, 1974. – 325 с.
3.Шевченко В.П., Цванг В.А. Граничные интегральные уравнения в теории оболочек.– Киев: Наукова думка,1986 – 224 с.
4.О ДОПУСТИМЫХ УСИЛИЯХ РЕЗАНИЯ ПРИ ТОКАРНОЙ ОБРАБОТКЕ ТОНКОСТЕННЫХ ЦИЛИНДРИЧЕСКИХ ОБОЛОЧЕК Д. Д. Евсеев, А. С. Тарапанов, к. т. н., профессор
Орловский государственный технический университет
Орел, Россия
5. Автореферат диссертации д.т.н. Дальского А.М. на тему: "Обеспечение качества прецизионных оболочковых деталей путем уменьшения погрешности формы от сил закрепления.
М.: МГТУ им. Н.Э. Баумана.
Главная страничка
Электронная библиотека"
Перечень ссылок
Главная страница ДонНТУ
Страница магистров ДонНТУ
Поисковая система ДонНТУ