|
English |
ДонНТУ|
Портал магистров ДонНТУ|
Прохорова Елена Вячеславовна
alena_stud
ukr.net
Механический факультет
Специальность:
Металлорежущие станки и системы
Группа:МС-01б
Тема магистерской работы:"Совершенствование способа исследования параметров рабочей поверхности алмазных кругов методом профилографирования".
Руководитель:
Матюха П.Г.
Автореферат магистерской работы:
Общая характеристика работы
Актуальность проблемы. Выпуск конкурентоспособной машиностроительной продукции неразрывно связан с
резким подъемом технического уровня выпускаемых машин, увеличением надежности и долговечности в эксплуатации,
повышением их точности и увеличением производительности труда. Решение этих задач возможно за счет применения
материалов повышенной прочности и износостойкости, создания нетрадиционных способов обработки.[11]
В настоящее время одним из высокопроизводительных технологических процессов, обеспечивающих высокое качество
обработки, является алмазное шлифование кругами на металлических связках с электроэрозионным воздействием на
рабочую поверхность круга (РПК), которое можно осуществлять введением технологического тока в зону резания или
в автономную зону.
Анимация 1. - Модель процесса шлифования
Вместе с тем, нет научных основ, по поводу автоматической стабилизации выходных технологических показателей
процесса с поддержанием режущих способностей круга при обработке труднообрабатываемых материалов.
Таким образом, проблема повышения продуктивности электроэрозионной правки алмазных кругов и шлифования
труднообрабатываемых материалов за счет поддержания режущих способностей круга в процессе шлифования –
актуальная научная проблема.
Исследования проводились на кафедре «Металлорежущие станки и инструменты» Донецкого национального
технического университета.
Цель работы. Целью работы является повышение продуктивности и качества обработки труднообрабатываемых
материалов алмазным шлифованием за счет повышения режущих способности рабочей поверхности круга и сокращения
вспомогательного времени, а также повышение эффективности и расширение технологических возможностей алмазного
шлифования.
Методика исследования. В методике использованы экспериментальные методы исследования с использованием
однофакторного и многофакторного экспериментов. Использовалась специальные устройства, приспособления и ЭВМ.
Научная новизна. Данная установка позволяет автоматизировать процесс регистрации данных и их обработки
и в дальнейшем будет использована для исследования рельефа алмазных кругов, заправленных электроэрозионным
способом. Такой метод исследования рельефа алмазных кругов позволит в несколько раз сократить затраты времени.
Обзор существующих способов определения параметров рабочей поверхности
шлифовальных кругов
Для изучения расположения абразивных и алмазных зерен, лежащих на поверхности круга, и их разновидности
предложено много методов. Рассмотрим кратко предложенные различными исследователями методы определения расстояния
между абразивными зернами, лежащими на поверхности круга, относительно оси круга.
Изучение расположения абразивных и алмазных зерен перекатыванием по многослойной фольге. По данным
А.Н. Резникова [1], наиболее близкий результат к количеству активных зерен дает метод прокатки по фольге,
толщина которой должна быть равна глубине резания. На рис. 1 приводится схема предложенного метода определения
числа абразивных зерен на рабочей поверхности абразивного инструмента[2].
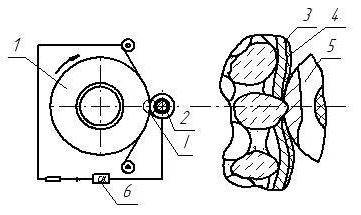
Рисунок 1. - Схема экспресс - метода определения числа зерен на рабочей поверхности
абразивного инструмента
Сущность способа заключается в автоматическом подсчете числа электрических импульсов, возникающих при прокатывании
фольги 3 с изолирующим покрытием 4 между рабочей поверхностью инструмента 1 и специальным роликом
2. Фольга и пластина 5 ролика подключается к источнику тока. В момент прохождения вершиной зерна
зоны контакта ролика с кругом, оно, вдавливаясь в материал фольги, разрывает изолирующую пленку и замыкает
электрическую цепь, в момент выхода вершины зерна из зоны контакта электрическая цепь разрывается. Новый
электрический импульс возникает при прохождении зоны контакта следующим абразивным зерном. Электрические
импульсы регистрируются счетчиком импульсов. Число абразивных зерен на единицу поверхности подсчитывается
как отношение числа зафиксированных импульсов mим за время τ к площади участка
сканирования:
,
где Hp – толщина регистрирующей пластины ролика.
Точность определения числа абразивных зерен по предложенному способу зависит от возможности наложения отдельных
электрических импульсов и обеспечивается за счет выбора конструктивны параметров регистрирующей пластины ролика.
Метод шлифования лысок. Изучение наложений проекций зерен непосредственно на шлифовальном круге методически
неудобно и поэтому неровности заправленного круга исследованы не непосредственно на круге, а отраженными на
шлифуемой поверхности.
Для этой цели разработан метод совмещения проекций зерен, названный «методом шлифования лысок» [3],
который имеет некоторое сходство с известным методом «косых срезов» и заключается в том, что на зеркально
доведенном цилиндрическом образце, установленном неподвижно в центрах круглошлифовального станка, врезанием
заправленного круга сошлифованная лыска.
Образующаяся при этом поверхность лыски представляет совокупность следов всех выступающих зерен вращающегося
круга, а в сечении этой поверхности цилиндрической поверхностью образца совмещены следы граней выступающих
зерен. Линия пересечения поверхностей лыски и образца очерчивает неровности круга, которые и изучаются в
отраженном и увеличенном виде на лыске.
Масштаб увеличения определяется диаметрами образца и шлифовального круга и глубиной врезания круга в образец,
или шириной сошлифованной лыски.
На лысках могут быть отражены только неровности круга, получающиеся в результате его перекрестной правки.
Винтовые неровности от односторонней правки не могут быть перенесены на лыску при неподвижном образце, так
как наиболее выступающие зерна располагаются по винтовой линии непосредственно друг за другом и срезают все
неровности на лыске. Осуществить же на станке мгновенный отвод образца от шлифованного круга практически не
представляется возможным.
Лыски, полученные шлифованием, перекрестно заправленным кругом, изучаются и фотографируются на микроскопе с
увеличением x60, в затемненном поле. На фотографии лыски, приведенной на рис. 2, видны отраженные на ней
неровности шлифовального круга, заправленного с шагом правки Т=0,2мм/об.
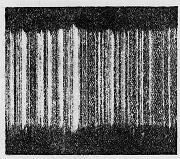
Рисунок 2. - Фотография лыски на образце
Исследование формы неровностей круга, образованных правкой, может быть произведено следующим образом: на
поверхности вращающегося круга врезание алмаза прорезаются кольцевые канавки, затем заправленным таким
образом кругом производиться врезное шлифование образца. На поверхности образца от канавок круга образуются
кольцевые выступы, профиль которых отражает профиль канавок круга.Профиль выступов на образце изучается с
помощью проектора и двойного микроскопа Линника.
Этот способ исследования может применяться при изучении форм неровностей, наносимых алмазом на
шлифовальном круге.
Изучение формы, количества и характера распределения вершин зерен с использованием метода царапания
исследуемым кругом поверхности клина с малым углом подъема. Измерения производят в следующем порядке.
Исследуемый круг (ролик) устанавливают на шпиндель продольношлифовального станка, приводят во вращение и
врезают плоский клин (рис.3). Зерна ролика, расположенные в рабочем поверхностном слое (РПС), придут в
соприкосновение с клином в разных точках в соответствии с разновысотностью взаимного расположения. При отношении
сторон клина, например 1:250, 1 мм продольного смещения соответствует разновысотности зерен в 4 мкм. Измеряя
смещение царапин на кли-не с точностью 0,2 мм, удается разделить зерна с разновысотностью 0,8-1 мкм. Точность
повысится, если обработку царапин производить по фотоснимку с увеличением в 4-5 раз.
В качестве начала отсчета принимается царапина наиболее выступающего зерна. Ширина каждой царапины и их
число по мере роста глубины врезания увеличиваются и на некоторой глубине царапины сливаются (перекрываются).
Глубина перекрытия hn характеризует момент, с которого начинается снятие материала со всей поверхности клина.
В последующем профиль царапин остается уже неизменным, ибо только зерна, лежащие до глубины hn, оставляют
следы на обработанной поверхности.
Метод царапания исследуемым кругом поверхности клина с малым углом подъема учитывает такие обстоятельства,
что режущие зерна не могут быть распределены с помощью статической модели круга не только из-за кинематического
перекрытия их друг другом, но и из-за того, что число утраченных в динамике процесса зерен заранее не известно.[4]
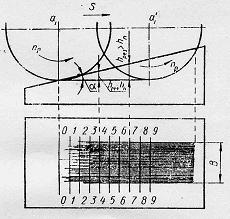
Рисунок 3. - Схема царапания клина роликом
Фотографирование одного и того же места шлифовального круга через бинокулярный микроскоп с последующей
обработкой с помощью стереометров и стереокомпараторов. Микростереофотограмметрическое исследование заключается
в следующем[3, 7, 8]. После правки поверхность шлифовального круга фотографируется через бинокулярный микроскоп
со специальной фотонасадкой. Фотографирование производится непосредственно на шлифовальном станке, для чего
микроскоп устанавливается на станке (рис. 4).
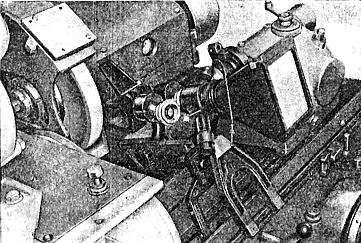
Рисунок 4.- Установка микроскопа на шлифовальном станке
Увеличение в микроскопе при зернистости шлифовального круга №46 следует принимать x30-x40. Меньшие увеличения
создают большие трудности измерения на стереограмметрических приборах. При больших увеличениях не удается
получить хорошую резкость по глубине, что также затрудняет измерения профиля зерна.
Настройка на резкость при фотографировании производится через матовое стекло фотокамеры. Для лучшей
настройки на резкость применяется 6-8-кратная лупа. Лупа предварительно устанавливается на любой поверхности,
регулируется на наилучшую резкость и затем переносится на матовое стекло фотокамеры. Применение лупы для
настройки на резкость значительно улучшает качество фотоснимков.
Для определения масштаба фотоснимков, т.е. общего увеличения, с учетом увеличения в объективе, окуляре и в
фотокамере, при этих же условиях производилось фотографирование специальной масштабной линейки.
Фотографирование каждого участка производится через правый и левый тубус микроскопа.
С целью выявления рельефа поверхности круга на отпечатках полученных снимков наносятся с помощью стереоскопа
или стереометра горизонтали, т.е. линии, соединяющие точки, находящиеся на одной высоте. Горизонтали наносятся
по поперечному сечению наиболее выступающего зерна. Вся поверхность шлифовального круга при этом как бы
рассекается горизонтальной плоскостью, над которой выступают различные участки – большие или меньшие, в
зависимости от их расположения по высоте. Правильность нанесения горизонталей контролируется на прецизионном
стереометре, на котором производится дальнейшая обработка снимков.
Фотографирование одного и того же места шлифовального круга через бинокулярный микроскоп с последующим
рассмотрением фотографий через стереоскоп. Сложная картина износа отдельных абразивных зерен на рабочей
поверхности шлифовального круга изучалась и фотографировалась при помощи бинокулярного микроскопа. Величина
износа измерялась непосредственно индикатором, монтированным на кожухе круга.
Для установления картины износа шлифовального круга наблюдали (при помощи бинокулярного микроскопа) за
износом абразивных зерен и связки, начиная с момента правки круга до его полного затупления, чему
соответствовало появление огранности или ожогов изделия.
В процессе износа рабочей поверхности круга можно наметить два периода: 1-ый период характеризуется
главным образом откалыванием и даже вырыванием из связки отдельных непрочных (консольно укрепленных)
абразивных зерен; 2-й период характеризуется главным образом расщеплением и округлением абразивных зерен,
а также забиванием пор круга металлической стружкой и абразивной пылью, что приводит круг к полной
потере его режущих свойств. Первый период шлифования является кратковременным. Второй период шлифования
сопровождается стабилизацией процесса износа, когда откалывания целых зерен, как правило не наблюдается
и происходит постепенное округление первоначально сравнительно острых зерен. После определенного времени
работы круга происходит окончательное «сглаживание» его рабочей поверхности [8].
Изучение расстояний между вершинами зерен и их разновысотности на установке, состоящей из оптической
делительной головки, центрального тубуса инструментального микроскопа и измерительной трубки оптиметра.
Измерения производились в такой последовательности: шлифовальный круг общепринятым способом крепился в
держатель круга, устанавливался на шлифовальный станок, правился алмазом и балансировался.
Измерение параметров (расстояние между вершинами абразивных зерен в направлении вращения круга;
разность высот между вершинами абразивных зерен по отношению к оси круга) производилось на свежезаправленных
и работавших кругах на установке, приведенной на рис. 5. Установка собрана из узлов следующих приборов:
оптической делительной головки 1, центрального тубуса инструментального микроскопа 3 с окулярной
головкой, измерительной трубки оптиметра 2. Указанные узлы установлены на станине 4 и салазках
5 прибора для комплексной проверки зубчатых колес в плотном зацеплении (межцентромере).

Рисунок 5.- Установка для измерения координат вершин абразивных зерен
Измерения проводились следующим образом. Перекрестие нитей окулярной пластинки центрального тубуса
микроскопа наводилось на вершину какого-либо зерна. Наводка осуществлялась путем поворота шпинделя
делительной головки и смещения каретки тубуса микроскопа. После наводки перекрестия нитей окулярной
головки на вершину первого абразивного зерна для удобства дальнейших отсчетов, шкалы делительной головки
и индикатора, фиксирующего положения салазок, устанавливались на ноль. Угловое положение первого
рассматриваемого абразивного зерна заносилось в ведомость, и его координаты были нулевым отсчетом.
Затем с помощью делительной головки шлифовальный круг медленно поворачивался до тех пор, пока
горизонтальная линия перекрестия окулярной головки не совмещалась с вершиной второго зерна. В этом
положении производился замер угловой координаты второго зерна относительно нулевого отсчета.
Аналогично производилось измерение координат последующих вершин абразивных зерен.
Измерения проводились при косом освещении с увеличением в 15 и 30 раз. При этих условиях в поле зрения
микроскопа хорошо различались компоненты круга (абразивные зерна, связка, поры круга, вкрапления частичек
металла).
Измерение разновысотности вершин абразивных зерен проводилось на той же установке и выполнялось следующим
образом. В круге на расстоянии, примерно равном половине ширины круга от его края, сверлилось отверстие
(диаметром 1мм) и в него запрессовывался стальной базовый штифт так, чтобы плоский верхний торец штифта
находился немного ниже (на 0,1-0,3 мм) рабочей поверхности круга. Затем перекрестие нитей окулярной
пластинки микроскопа наводилось на центр штифта и шкалы лимба делительной головки и индикаторы каретки
устанавливались на ноль. После этого способом, описанным выше, последовательно находились координаты
вершин абразивных зерен, расположенных на продольной граничной линии круга. Обычно измерялось положение
вершин 100 шт. абразивных зерен. Затем круг возвращался в первоначальное положение. После проверки
правильности совпадения центра перекрестия нитей с центром торца базового штифта, окулярную головку
микроскопа отводили в сторону и на ее оптиметра измерительный наконечник устанавливался так, чтобы его
центр, возможно, более точно совместился с центром базового штифта.
После выполнения указанной установки трубки оптиметра и ее измерительного наконечника последний
поднимался арретиром и с помощью делительной головки и каретки устанавливалась угловая координата
а1 вершины первого измеряемого абразивного зерна. Затем измерительный наконечник
опускался на эту вершину зерна и шкала оптиметра устанавливалась на ноль. Зафиксированное положение
вершины абразивного зерна являлось начальным для определения разновысотности вершин абразивных зерен.
После этого измерительный наконечник снова поднимался, на делительной головке устанавливалась угловая
координата а2 вершины второго абразивного зерна, наконечник опускался, его
измерительная плоскость ложилась на следующую вершину зерна и по шкале оптиметра определялась разность
высот между первым и вторым абразивным абразивными зернами относительно оси круга. Подобным образом
находились положения вершин других абразивных зерен. Результаты замеров заносились в соответствующие
протоколы наблюдений [9].
Недостатки методов исследования рельефа поверхности круга Отметим некоторые недостатки рассмотренных
методов исследования РПК.
Е.В. Маслов [8] и Н.И. Вольский [7] изучали и фотографировали поверхности кругов с помощью бинокулярного
микроскопа. Бинокулярный микроскоп имеет малые глубины резкости и поле зрения, вмещающее одновременно лишь
небольшое количество зерен. Кроме того, с помощью бинокулярного микроскопа нельзя измерить разновысотность
вершин абразивных зерен.
В.Д. Сильвестров [3] для этой цели применял микростереофотограмметрический метод, который чрезвычайно
громоздок, так как для выявления рельефа поверхности требует изготовления фотоснимков большого количества
участков поверхности, которые выполняются через бинокулярный микроскоп со специальной фотонасадкой, и
последующей обработкой фотоснимков на топографическом стереометре.
Определение микропрофиля круга путем шлифования лысок [3] имеет весьма существенный недостаток,
заключающийся в том, что на лысках могут быть отражены только неровности круга, получающиеся в результате
его перекрестной правки алмазом. Неровности, расположенные на винтовой линии при односторонней правки
алмазом, а также неровности, образующиеся на шлифовальном круге при правке круга твердосплавным роликом
или при его шлифовании алмазным заправочным кругом, не могут быть перенесены на лыску при неподвижном
образце, так как наиболее выступающие зерна при этих методах правки круга располагаются непосредственно
друг за другом и срезают все неровности на лыске.
Собственные результаты
На основании проведения анализа существующих методов изучения рельефа круга можно прийти к выводу, что метод
для определения координат вершин абразивных зерен должен:
а) позволять различать компоненты, расположенные на поверхности круга, например зерна, связку;
б) обеспечивать с определенной точностью измерение расстояний между вершинами зерен, расположенных на
поверхности круга, и разновысотность вершин зерен в радиальном направлении;
в) обеспечивать изучение изменения рельефа во времени.
Методика исследования рельефа режущей поверхности алмазных шлифовальных кругов методом профилографирования.[12]
Исследование РПК проводилось на установке, которая отвечает всем вышеперечисленным требованиям и описанной в
работе [10], модернизированной и представленной на рис.6, которая позволяет производить увеличение
измеряемого профиля по профилографу в 1тыс., 2тыс., 40 тыс., 100 тыс., 200 тыс. раз. Действительное увеличение
определяется путем тарировки.
Установка создана на базе профилометра-профилографа. Шлифовальный круг 7, снятый со станка, одевался на
коническую оправку. Оправка с кругом устанавливалась в центрах 6, которые крепятся к призмам 5. Призмы
закреплены на подвижных салазках 19, которые можно перемещать по направляющим корпуса 16. К салазкам
прикреплены кронштейны 20, обеспечивающие поджим ролика 21 электродвигателя с редуктором для перемещения
РПК со скоростью 1 мм/мин относительно ощупывающей иглы 12, закрепленной на коромысле 22, поворачивающемся
на оси 23. Для обеспечения надежного поджима приводного ролика к РПК служит круг 15. Положение алмазной иглы 13
регулируется винтом 24, торец которого упирается в текстолитовую пластину 25. Для точной установки начальной и
конечной точки трассы профилографирования служат магнитные стойки 11 с лупой Бринелля 8 или индикатором 26,
фиксирующим перемещение столика 14.
Для записи координат РПК с выделением зерна и связки служит устройство 9, к которому подводятся два провода –
один от шлифовального круга, другой от ощупывающей иглы. Запись профиля круга можно производить с различным
увеличением от 103 до 2x105 раз настройкой блока 2.
Координаты РПК поступают через согласующее устройство 9 на АЦП установленное в системном блоке 17. Начало и
конец записи управляется с монитора 18.
Данные обрабатываются с помощью программы, написанной на языке Delphi5.
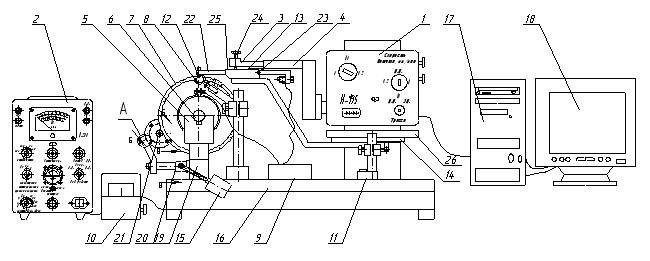
Рисунок 6. - Схема установки для исследования РПК методом профилографирования
Данная установка позволяет автоматизировать процесс регистрации данных и их обработки и в дальнейшем будет
использована для исследования рельефа алмазных кругов, заправленных электроэрозионным способом.
Заключение
Для повышения эффективности алмазного шлифования труднообрабатываемых материалов необходимо выполнение
двух основных требований: во-первых, прочного закрепления алмазных зерен в связке, что позволит полностью
использовать уникальные режущие свойства алмазов, во вторых – постоянного обновления параметров РПК во время
обработки, что обеспечит стабилизацию выходных технологических показателей обработки и расширение гаммы
материалов, обрабатываемых алмазным шлифованием. Эти два требования могут быть реализованы с помощью управляющих
воздействий на РПК, когда одновременно с обработкой изготавливаемых деталей поддерживаются в требуемых пределах
параметры рабочей поверхности круга, в результате чего стабилизируются выходные технологические показатели на
протяжении всего времени обработки. Поэтому есть необходимость в изучении методов исследования РПК, для того,
повысить производительность процесса шлифования, а также, чтобы иметь возможность прогнозировать качество готового
изделия.
Список используемых материалов:
- Редько С.Г. Количество абразивных зерен шлифовального круга, участвующих в резании.
Станки и инструменты, 1960, №12, с.10-12.
- Nakayama Karuo. Taper print method for the measurement of grinding wheel surface.
«Bull. Jap. Soc. Prices. Eng., 1973, 7, №2, с. 59-60.
- Сильвестров В.Д. Безалмазная правка шлифовальных кругов – М.: Оборонгиз, 1955, 128с.
- Байкалов А.К., Сукенник И.Л. Алмазный правящий инструмент на гальванической связке. -
Киев: Наукова думка, 1976, 202 с.
- Резников А.Н. Теплофизика резания. – М.: Машиностроение, 1969, 288с.
- Новосёлов Ю.К. Динамика формообразования поверхностей при абразивной обработке. –
Издательство Саратовского университета, 1979, 232 с.
- Вольский Н.И. Обрабатываемость металлов шлифованием. – М. – Л.: ГНТИ, Машгиз, 1950, 62с.
- Маслов Е.Н. Основы теории шлифования металлов. – М.: Машгиз, 1951, 177с.
- Казаков В.Ф. Шлифование при повышенных скоростях резания. – Киев: Техника, 1971, 171с.
- Матюха П.Г. Научные основы стабилизации выходных показателей алмазного шлифования с помощью управляющих
воздействий на рабочую поверхность круга. Автореф. дис. докт. техн. наук – Харьков, 1996, 48с.
- http://www.uran.donetsk.ua/~masters/2000/mehf/strelkov/rabota/stat2.htm
Шлифовальный алмазный круг с регулируемой высотой. Матюха П.Г., Стрелков В.Б. (ДонГТУ, Донецк, Украина)
- http://www.uran.donetsk.ua/~masters/2001/mech/rogkov/publ/art2/index.htm
Определение параметров рабочей поверхности алмазного круга при профилографировании. Гусев В.В., Рожков Д.Б.(ДонГТУ, г. Донецк, Украина)
|
Главная страница ДонНТУ|
Страница магистров ДонНТУ|