As far as development of engineer, foremost, the most difficult and labour intensive operations, related to the changes of form and sizes of wares, were automatized. A load and unloading of technological equipment was carried out usually by hand or by the simplest facilities of mechanization. Lately in connection with the tasks of the complex computer-aided and mastering of new areas of activity of man manufacturing large attention is spared automation of operations of manipulation are moving and orientations of wares and instrument.
The modern automated assembling equipment (AAE) is a complex of the difficult dynamic systems. Complication them conditioned rigorists to the productivity and exactness of work of assembling equipment, and also by the variety of executable by him functions. One of major questions which must be decided at planning and exploitation of such watching systems, there is a question about stability of the system. Other no less important question of development - it providing without the salutatory mode of operations of the system and smoothness of transitional processes in the control system.
The origin of jumps on an executive axis negatively tells on quality of work and dynamic exactness of the watching system of AAE. Realization of the smooth mode of operations of the watching systems of AAE possibly by either the change of structural parameters of the system or input in this system of correcting devices. The last way is more preferable.
The engineering’s methods of synthesis, enabling to define the presence of the smooth mode of operations in all working range of speeds in the designed watching system of AAE, are considered in this work, and, in the case of his absence, necessary types of correcting devices. By correcting devices in the watching system simultaneously labour for the large supplies of stability of the system, without the salutatory mode of operations of executive axis in the working range of speeds and smoothness of transitional processes in the control system. The use of concrete type of correcting devices is determined both possibility of effective increase of range of smooth speeds and terms of realization of correction in the concrete watching systems of AAE.
In the task of traffic of manipulator regulation the construction of dynamic model of manipulator is included and choice on the basis of this model of management laws, providing the set conduct of the system.
At the synthesis of the control of modern industrial robots systems it is accepted to examine the drives of joining of manipulator as servo-mechanisms. Such approach reflects variable dynamic descriptions of manipulator inadequately, as does not take into account motion and configuration of manipulator on the whole.
The questions of synthesis of management laws, enabling on the base of the built dynamic models to carry out an effective management a manipulator are examined in this work. The use allows obtaining it as a mathematical vehicle of management of modern methods of management theory, namely method of space of problems and theory of modal management. Application of methods of space of problems for the discrete dynamic systems to mathematical description of manipulator is more preferable by comparison to methods for the continuous systems, as the real management any manipulator is carried out digital computer by a discrete method. In this connection, consideration of dynamics of manipulator in discrete time allows to avoid the errors of the signals related to the quantum in analog-digital transformers, plugged in the control system.
Mathematical model of drive of manipulator as a transmission function
the analysis of one joining of manipulator at first will examine as a continuous linear system which the vehicle of transformation of Laplasa can be applied to.
Most industrial robots with an electric drive are more frequent than all equipped the engines of direct current with independent excitation in every joining. The engines of direct current combine in itself such qualities, as high power, smoothness of motion, possibility of work on small speeds, linearness of loading description and small permanent time. On a fig. 1 the equivalent chart of the loaded engine of direct current is resulted with a management in the chain of anchor which can be used in joining of manipulator.
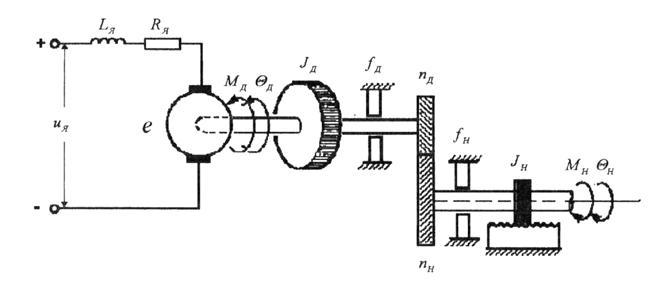
Figure 1 - Equivalent chart of the loaded engine of direct current with an anchor management
Basic variables:
uja – tension, attached to the anchor puttee of engine, V;
ija – a current is in the chain of anchor, А;
Lja – inductance of anchor chain, Gn;
Rja – resistance an anchor chain, Оhm;
е – tension of back emf, V;
Md – moment of engine, attributed to the billow of engine, Н*m/rad;
Θd – angular moving of billow of engine, rad;
Θn – angular moving of billow of loading, rad;
Jd – the moment of inertia of engine is resulted to the billow of engine, Н*m*с2/rad;
Jn – the moment of inertia of loading is resulted to the billow of loading, Н*м*с2/рад;
fd – the coefficient of viscid friction in bearings of engine is resulted to the billow of engine, Н*м*с/рад;
fn – the coefficient of viscid friction in bearings of loading is resulted to the billow of loading, Н*м*с/рад;
nd – number of teeth of cog-wheel of reducing gear on the billow of engine;
nn – number of teeth of cog-wheel of reducing gear on the billow of loading.
The current angular moving of joining can be measured by a photo-electric primary transformer with blocking light - optical encoding device, included on the chart of accumulating type. In this case given on the entrances of microprocessor the compared tensions are proportional the desired and actual corners of turn of joining of manipulator, and set in a digital kind.
Thus, for the watching systems of robots of manipulators with a microprocessor management the corners of turn are set equivalent tensions. The proper flow diagram of the watching system of one joining of robot of manipulator is presented on a fig. 2.
Transmission function for the broken a secret system linking given on the entrance of strengthener of power tension of error of uум(f) ) and tension the sensor of position of uн(t),proportional the corner of turn of billow of joining it is possible to write down expression:
(1)
where Кr - a coefficient of transmission of measuring device of error, including the coefficient of transmission of sensor of corner of turn of output billow, resulted to the billow of engine.
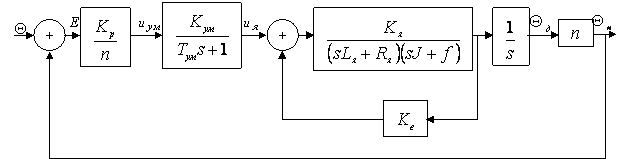
Figure 2 – Watching system of hinge of robot of manipulator
Description of the discrete watching system of hinge of manipulator is in space of parameters of the states.
In discrete time recurrent victories-matrix equalization of this object and equalization of output look like:
(2)
where x(k) - vector of the state,
u(k) - vector of the control,
Ф(T) - matrix of transition of the state of the discrete system,
Н(Т) - vector of the guided transition of the discrete system,
Т - a period of epoch, equal to the time domain, through which microprocessor at lower level of the control system reads information about current coal of turn a sensor.
Synthesis of the estimator state
At the decision of practical tasks of management the methods of theory of space of problems often there are cases, some time all variable states, or part component of vector of the state appear immeasurable. In order to take advantage of theory of modal management for such objects, it is necessary to estimate the immeasurable states of object on his measurable co-ordinates of entrances and outputs.
If in the watching system one of component of vector of the state of measurable and known, the remaining variable states can be recovered by the determined estimator state of the lowered order.
In general case victories-matrix equalization of dynamics of estimator looks like:
(3)
As the desired poles of estimator will set the roots of characteristic polynomial. Thus, estimator must behave even in five times quick what the closed system, that an aperiodic transitional process for estimator must be completed approximately after time equal to three to the steps of discreteness of the system. This result can be obtained in tom case if the roots of characteristic polynomial will be equal to the zero, then an aperiodic process will be finished for the amount of steps equal to the dimension of estimator. In conduct higher said for the characteristic polynomial of estimator will set three zero roots of z1=z2=z3=0.
To analyses exactness of calculation of looking after device will confront the exact meanings component of vector of the state of the discrete watching system and estimation got in accordance with the shown out equalizations of observer.
Below presented the graphs of dynamics restored through projected estimator of state of management object variables.
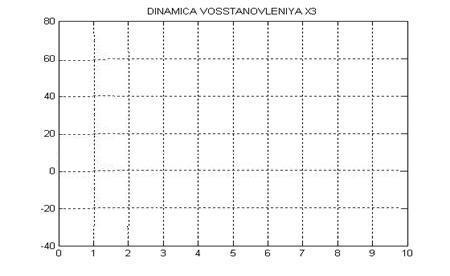
Figure 3 – A dynamics of renewal components of x3
Research of object with a dynamic regulator
The dynamic regulator projected in this work for the watching system of drive of hinge of manipulator plugs a modal regulator and estimator states in the composition. The flow diagram of the adjusting system with a dynamic regulator is presented on a fig. 4.
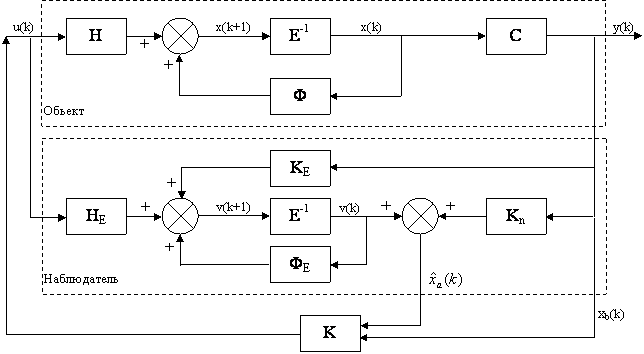
Figure 4 – Guided object with a dynamic regulator
Will conduct research of dynamic properties of regulator by the estimation of influencing of changes of some parameters of the system on the conduct of transitional description, at the permanent parameters of dynamic regulator.
Basic changing parameters during work of robot of manipulator it is been: moment of inertia, changing because of change of kinematics of manipulator and mutual influencing of his links, coefficient of viscid friction multiplying which is conditioned the wear of bearings, and also time of discreteness of the system, depending on frequency of reading of information from the sensor of corner of turn.
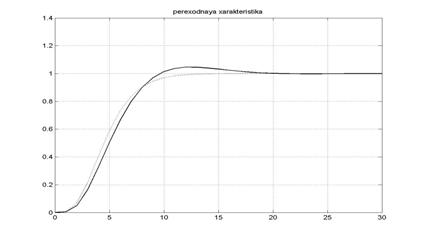
Figure 5 - Transitional description at multiplying J on 50 %
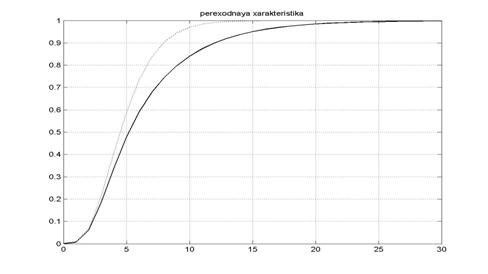
Figure 6 - Transitional description at multiplying f on 50 %
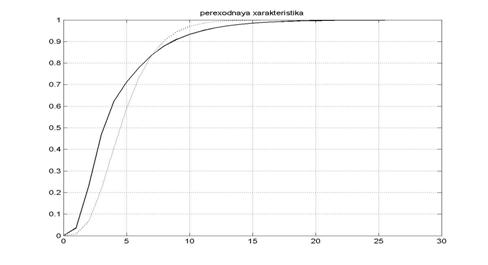
Figure 7 – Transitional description at multiplying T in 2.5 time and multiplying f on 100%
Watching system a drive of hinge of the robot manipulator considered in this work as a control object is described equalizations of 4th order. The system is one-dimensional, that has one entrance and one output as a corner turn of link of manipulator.
In order that the watching system had necessary for control a robot manipulator indexes of quality, that a control was conducted with minimum possible override and set time of adjusting, a dynamic regulator, plugging in the structure a modal regulator as a matrix of linear stationary feed-backs to on to the state of object and estimator state variables, is synthesized. The control system got thus has satisfying set the problem indexes, namely time of adjusting of less set 140 msek. and override is near to the zero.
At this moment work is not completed. In the near future it is planned to add the point of "Robast control".
List of references
1.
Фу, Кисан и др. Робототехника. М,: Мир 1989г.
2.
Шахинпур, Мозен. Курс робототехники. М.: Мир 1990 г.
3.
В.Г. Домрачев В.Р. Матвеевский и др. Схемотехника цифровых преобразователей перемещениям.: Машиностроение 1987г.
4.
Синтез дискретных регуляторов при помощи ЭВМ / В.В. Григорьев, В.Н.
Дроздов, В.В. Лаврентьев, А.В. Ушаков. Л.: Машиностроение 1983 г.
5.
К.И. Палк. Системы управления механической обработкой на станках Л. : Машиностроение 1984 г.
6.
Н.Т. Кузовков. Модальное управление и наблюдающие устройства. М. : Машиностроение 1976 г.
7.
Н. И. Соколов. Аналитический метод синтеза линеаризованных систем автоматического регулирования. М.: Машиностроение 1966 г.
8.
Стрейц В. Метод пространства состояний в теории дискретных линейных систем управления. - М.: Наука, 1985г.