Совершенствование кристаллизаторов современных МНЛЗ
Источник://Журнал "Сталь",№2. 2005 г., с.33-36
УДК 621.746
Г. Н. Еланский, И. Ф. Гончаревич, К. Штурм
Совершенствование кристаллизаторов современных МНЛЗ
За последнее десятилетие произошли значительные изменения в производстве непрерывнолитых стальных заготовок. Коренным образом изменились и оборудование, и технология непрерывного литья. Проведенные преобразования диктовались актуальными запросами практики: стремлением увеличить скорость литья при одновременном улучшении качества поверхности отливки и желанием усовершенствовать МНЛЗ, в первую очередь в части уменьшения их массогабаритных характеристик, а также упрощения и улучшения системы подвески кристаллизатора. Были разработаны и запущены в производство резонансные и виброкристаллизаторы; оба типа кристаллизаторов перешли на высокочастотные с малыми амплитудами (вибрационные) режимы работы. Стали широко использоваться высокоэффективные в технологическом отношении асимметричные колебания кристаллизаторов.
Если проанализировать результаты прошедших преобразований традиционных кристаллизаторов с концептуальных позиций, то можно заметить, что их сущность в машинном аспекте состоит в переходе от использования принципов механики машин с жесткими звеньями к машинам с деформируемыми связями и свободным движением ('вибрационным машинам). В отношении преобразования технологических процессов несомненен переход в область вибрационных технологий (высокочастотные колебания асимметричной конфигурации с малыми амплитудами).
Произошедшие преобразования кристаллизаторов МНЛЗ следуют логике развития систем с периодическими движениями и прогнозировались специалистами еще в 1970-х годах.
Рассмотрим основные запросы практики, которые диктуют необходимость использования новых подходов в создании кристаллизаторов. Стремление улучшить качество поверхности непрерывнолитой заготовки (уменьшить риски от качаний) вызывает необходимость в оптимизации режимов движения кристаллизатора. Состояние поверхности литых металлов существенно зависит от условий формирования оболочки отливки в кристаллизаторе. Важный фактор в данном случае — напряжения в оболочке, которые создаются силами трения, действующими между ее поверхностью и стенками кристаллизатора. Оптимизируя режимы колебаний и подбирая параметры процесса литья в зависимости от химического состава стали, стремятся уменьшить силы трения и таким способом ослабить напряжения в оболочке отливки. На характер и величину этих напряжений влияют также отклонения кристаллизатора от поступательных перемещений. Колебательные движения должны происходить строго в направлении линии вытяжки отливки. Это особенно важно для слябовых кристаллизаторов, поперечные перемещения которых должны быть полностью исключены. Любые перекосы увеличивают силы трения и действующие напряжения в оболочке отливки.
Однако обычные эксцентриковые приводы и рычажная многошарнирная подвеска подвижных частей кристаллизатора, имеющие технологические люфты и подверженные интенсивному износу в процессе эксплуатации, не обеспечивают необходимой точности перемещений. Стремление преодолеть эти проблемы привело к развитию систем подвески кристаллизаторов на гибких элементах (пластинчатых рессорах). Основные черты современного кристаллизатора определяются результатами развития именно этого направления.
Поиски эффективных конфигураций и параметров скоростей качаний кристаллизаторов приводят к внедрению в практику негармонических скоростных диаграмм, имеющих в своем составе высшие гармоники. При этом ускорения перемещений кристаллизатора и зависящие от них силы инерции возрастают пропорционально квадрату частоты колебаний. Рост поперечного сечения отливки приводит к увеличению подвижных масс механизма кристаллизатора. Тенденция постоянного увеличения скорости литья влечет за собой необходимость повышения частоты его качаний.
Решение возникающих проблем снижения динамической нагруженности МНЛЗ (от возрастания подвижных масс и частот колебаний кристаллизаторов) достигается созданием для массивных отливок резонансных кристаллизаторов, в которых силы инерции уравновешиваются восстанавливающими силами пружин, а для отливок меньших размеров — уменьшением массы подвижных частей и сообщением качаний только гильзе.
Главные особенности современного кристаллизатора для крупных отливок — подвеска его, а также системы его водоохлаждения с двух сторон на спаренных пакетах направляющих пластинчатых рессор и, кроме того, уменьшение массы подвижных частей (более чем на 50 % вследствие замены громоздкой рычажно-шарнирной подвески компактной рессорной). Применение спаренных рессорных пакетов со специальной высокоточной системой установки на опорной раме обеспечивает перемещение кристаллизатора строго параллельно самому себе без каких-либо перекосов.
Новый принцип конструктивного исполнения, более высокие частоты колебаний с регулируемыми размахами в режиме как гармонических. так и негармонических колебаний, были реализованы при использовании следящего гидравлического привода. Исполнительными органами привода служат два гидроцилиндра, непосредственно управляемые соединенными с ними сервоклапанами. Гидропривод оснащен датчиками положения кристаллизатора, которое непрерывно сравнивается с соответствующими заданными параметрами. Любые отклонения фактического положения кристаллизатора от заданного незамедлительно компенсируются приводом. Одновременно контролируется и выполнение заданной конфигурации колебаний кристаллизатора (гармонической или какой-либо другой). Гидропривод рассмотренной системы позволяет также оперативно устанавливать новый режим работы кристаллизатора при изменении технологического процесса. Такой сравнительно дорогой привод применяется в целях оптимизации режимов качаний по критериям уменьшения сопротивлений прохождению отливки через кристаллизатор и улучшения качества ее поверхности.
В современном резонансном кристаллизаторе вследствие обеспечения строго поступательных перемещений, более точного управления режимом его работы и возможности модификации (преимущественно ослабления) действующих на отливку сил трения затвердевшая оболочка непрерывно подвергается меньшим напряжениям, что создает возможность оптимизации процесса формирования меток колебаний на поверхности отливки.
Второе направление в модернизации традиционных кристаллизаторов представлено так называемыми виброкристаллизаторами. Эти автономные устройства блочной конструкции предназначены для отливок небольшого поперечного сечения. Проблемы динамики и повышения рабочих частот здесь решены путем радикального уменьшения массы колеблющихся частей — колебания сообщаются только гильзе встроенным в корпус кристаллизатора приводным цилиндром, соединенным шлангами с гидравлическим насосом.
Проводятся исследования и по разработке кристаллизатора нового типа — управляющего структурой непрерывнолитой заготовки. В МГВМИ при участии ОАО МЗ "Серп и молот" в течение ряда лет разрабатываются принципиально-конструктивные основы создания вибрационных и виброударных кристаллизаторов для заготовки небольшого сечения, способные решать проблемы управления ее структурой и улучшать качество поверхности. В отличие от традиционных разрабатываемый кристаллизатор предназначен не только для предотвращения разрывов корки слитка и улучшения качества его поверхности, но и для модифицирования структуры в процессе кристаллизации. Исследования проведены на уровне заводского и компьютерного математического эксперимента и содержат новые технические решения, базирующиеся на опыте создания современных резонансных и вибрационных кристаллизаторов, а также использования методов вибрационной техники и технологии.
Цель проведенных исследований — разработка вибрационных методов модификации структуры металла в процессе кристаллизации отливки и автономного модуля вибрационного резонансного кристаллизатора нового поколения, реализующего эти методы. В исследовании были поставлены задачи: синтеза эффективных режимов вибрационных воздействий. модифицирующих структуру металла в процессе кристаллизации; разработки принципиально-конструктивной схемы реализующего их автономного мо-дуля вибрационного резонансного кристаллизатора с колеблющимися элементами уменьшенной массы; создания резонансной упругой системы, обеспечивающей точность перемещений гильзы, и специальных вибровозбудителей повышенной мощности, обусловливающих эффективное воздействие вибрационных импульсов на процесс формирования структуры заготовки и устойчивую работу системы на эффективных резонансных режимах.
Блочно-модульный принцип построения и автономность вибрационного резонансного кристаллизатора, малые габариты. устойчивый резонансный режим работы при небольшой колеблющейся массе и повышенной мощности вибровозбудителей допускают достаточно простую установку кристаллизатора на действующих МНЛЗ и в перспективе обработку непрерывнолитых заготовок большего сечения на вновь создаваемых машинах.
Едва затвердевшая корка испытывает достаточно значительные сопротивления, обусловленные трением о стенки гильзы. Нередко происходят разрывы корки и выбросы жидкого металла, что приводит к созданию аварийной ситуации. Создание высокоэффективных кристаллизаторов предполагает управление действующим в них трением. Управление трением в зоне контакта заготовки со стенка-ми гильзы кристаллизатора обеспечивается сообщением ему продольных качаний различной конфигурации и частоты, которые преобразовывают трение таким образом, что на отдельных этапах перемещения кристаллизатора оно превращается в движущую силу (при этом уменьшается усредненная за цикл сила трения). Задача оптимизации режимов качаний кристаллизатора сводится к тому, чтобы увеличивать эффективность модифицирования трения в движущую силу. Процесс трения заготовки о стенки кристаллизатора достаточно сложен и формирует комбинацию сил трения, зависящих и не зависящих от скорости, хотя преобладающий вклад принадлежит силам сухого трения. Проблема осложняется еще тем, что контактные поверхности взаимодействуют в условиях высоких переменных температур. Отливка, находящаяся между стенками гильзы, представляет собой сложную изменяющуюся по высоте твердо-жидкую упруго-вязко-пластичную реологическую систему. На верхнем уровне это полностью жидкая среда; по мере перемещения через кристаллизатор она постепенно, начиная с контактной области, затвердевает, образуя твердую оболочку, в которой заключена жидкая фаза. Дисперсная среда, находящаяся внутри оболочки, представляет собой физико-химическую структуру, обладающую сложными реологическими свойствами: часть объекта исследования находится в жидком состоянии, Другая — в разных фазах затвердевания. Толщина оболочки по мере прохождения через кристаллизатор постепенно нарастает, а объем жидкой фазы сокращается. На некотором удалении от верха кристаллизатора фронты затвердевшей оболочки смыкаются, и жидкая фаза полностью переходит в твердую (это уже за пределами кристаллизатора).
Опубликованные данные промышленных экспериментальных исследований кристаллизатора фирмы "Demag" в общих чертах подтверждают достоверность результатов расчетов влияния параметров и конфигураций колебаний на формирование сил трения оболочки отливки о стенки кристаллизатора. Однако традиционный анализ проблемы ограничивается лишь рассмотрением кинематики взаимодействия линейной скорости перемещения отливки в кристаллизаторе с несколькими конфигурациями его колебаний. Кроме того, известные подходы не позволяют с необходимой физической достоверностью разобраться в механизмах такого сложного процесса, как прохождение отливки через кристаллизатор, и получить информацию, требуемую для оптимизации режимов работы существующих установок и создания принципиально новых кристаллизаторов. Следует учитывать также, что на характер сопротивления определенное влияние могут оказывать упруго-инерционно-гистерезисные характеристики всей динамической системы непрерывнолитая отливка — кристаллизатор - тяговая система, которые не учитываются в традиционных расчетах.
Замена в резонансных и вибрационных кристаллизаторах жестких кинематических звеньев упругими связями привела к тому, что система резонансный (вибрационный) кристаллизатор – привод – отливка стала характеризоваться особо сильными связями между составляющими ее элементами и, по существу, представляет собой единый органический комплекс, функционирующий по общим законам. Вторая важная особенность такой системы – ярко выраженные собственные свойства, главными из которых следует считать спектр частот собственных колебаний, коэффициенты демпфирования и динамическую конфигурацию рабочей машины.
Еще одна из причин, побудивших авторов разработать физически более достоверную феноменологическую модель системы кристаллизатор - непрерывнолитая заготовка, является стремление выяснить. можно ли оценивать эффективность режима качаний кристаллизатора с точки зрения ослабления напряжений в оболочке отливки при прохождении через кристаллизатор только по степени уменьшения сил трения, действующих между его стенками и оболочкой, или нужны какие-либо дополнительные уточняющие критерии.
Углубленное понимание особенностей механизма взаимодействия непрерывнолитой заготовки со стенками кристаллизатора позволит разработать физически обоснованные критерии оптимального управления режимом его работы при разных технологических процессах литья. Практическое осуществление этих рекомендаций может быть легко реализовано следящим гидроприводом современных МНЛЗ.
Разработаны феноменология объемных инерционно-упруго-вязко-пластичных реологических моделей непрерывнолитой заготовки и динамическая модель кристаллизатора с приводом, что реализует возможность квалифицированного анализа системы кристаллизатор - непрерывнолитая заготовка. Этот программный продукт сопровождается методикой идентификации компьютерных характеристик движения и деформации модели с натурой. Предложенная феноменологическая модель непрерывнолитой заготовки, идентифицированная с натурой, позволяет достаточно достоверно оценивать ее кинематические, силовые и энергетические закономерности взаимодействий с гильзой при известных параметрах внешних воздействий. С использованием этой модели и ее математической интерпретации (систем нелинейных дифференциальных уравнений) описываются движения, деформации, напряжения, затраты энергии при перемещении отливки через кристаллизатор при любых режимах и параметрах колебаний, а также характеристиках привода и тяговой системы.
В качестве иллюстрации возможностей разработанной программы приведем несколько примеров. Чтобы придать универсальность выполненным расчетам, все приводимые данные отнесены к единице массы отливки. Для получения конкретных значений любого параметра данные, полученные из графика, следует умножить на реальную массу отливки, находящуюся в кристаллизаторе. На рис. 1 приведены текущие и средние значения напряжения в корке, текущие и средние энергозатраты на деформирование корки в процессе вытягивания, а также скорости деформирования отливки в кристаллизаторе. Расчеты показывают, что при колебаниях кристаллизатора со средней интенсивностью (400 колебаний в минуту и амплитуда 5 мм) пиковые значения напряжений колеблются в пределах 40 % в большую и меньшую стороны. Анализ аналогичных графиков при отсутствии качаний кристаллизатора и при колебаниях с разными параметрами показывает, что средние значения рассматриваемых параметров не меняются.
Сопоставление значений действующих на отливку в кристаллизаторе сил трения (в общем случае сухого и вязкого) и напряжений в ней, полученных в большом числе компьютерных экспериментов, показывает, что между ними нет достаточно сильной корреляции. Зафиксированы режимы, в которых при резком снижении сил трения не происходит адекватного изменения напряжений в отливке.
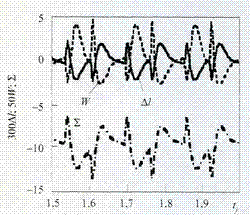
Рисунок 1 – Напряжения, энергозатраты и скорость деформирования отливки в кристаллизаторе
Одно из возможных объяснений этого состоит в том, что вибрационные воздействия на процессы трения и формирование напряжений при внешней схожести (и в том и в другом случаях возбуждаются пульсации около средних значений) имеют разные последствия. Так, снижение усредненных сопротивлений перемещению благоприятно влияет на прохождение отливки через кристаллизатор.
На рис. 2 приведены силы вязкого трения суммарные (сухие и вязкие) силы трения. действующие на нижнюю часть и на верхнюю часть отливки при прохождении ее через кристаллизатор. Из графиков следует, что все эти силы постоянно меняют направление своего действия: то они тормозящие движение заготовки (знак минус), то движущие (знак плюс). При этом меняется среднее значение сил трения. Если при прохождении через стационарный кристаллизатор они равны -0,683. то при качаниях в указанном режиме они снижаются до значений -0,034. В то же время периодические возрастания напряжений в отливке сверх средних значений могут негативно сказываться на формировании ее поверхности.
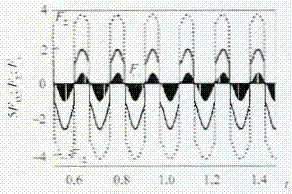
Рисунок 2 – Силы вязкого трения, суммарные силы трения, действующие на нижнюю и верхнюю части отливки при прохождении ее через кристаллизатор.
На рис. 3 представлены сила тяги привода протяжки отливки и энергозатраты приводов качания кристаллизатора и протяжки отливки .
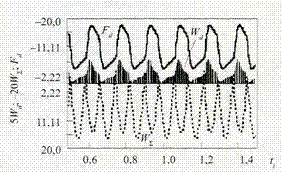
Рисунок 3 – Сила тяги привода протяжки и энергозатраты приводов качания кристаллизатора и протяжки отливки.
Надежность компьютерных методов расчета обусловливается в немалой степени физической достоверностью и достаточной точностью воспроизведения феноменологическими моделями основных параметров технологических процессов, реализуемых с помощью вибрации, и достаточной простотой описания исследуемого комплекса, гарантирующей их применение в инженерной практике. На изложенных принципах в среде Mathcad и Matlab сформировано программное обеспечение для идентификации феноменологических моделей технологических процессов.
|