Описаны особенности условий эксплуатации, характер и интенсивность износа строительных конструкций цехов рудо-подготовительного,
коксохимического и металлургического производств. Дана классификация указанных объектов по виду и интенсивности износа строительных
конструкций. Рассмотрены некоторые эффективные способы обеспечения долговечности строительных конструкций в условиях эксплуатационных
воздействий. Показана экономическая эффективность применения более долговечных конструкций и систем их защиты.
Заславский И. Н., Флакс В. Я., Чернявский В. Л.
Долговечность зданий и сооружений предприятий черной металлургии. М., Стройиздат, 1979.
3. КОКСОХИМИЧЕСКОЕ ПРОИЗВОДСТВО
Коксохимическое производство включает в себя комплексы по подготовке углей к коксованию (камеры размораживания,
отделения дробления, корпуса обогащения, силосные корпуса и т.д.), по коксованию углей (коксовые батареи, башни тушения кокса, здания и галереи
коксосортировки и т.д.), а также по улавливанию и переработке химических продуктов (отделения конденсации и улавливания газа, аммиачно-сульфатное
и смоло-перегонное отделения, сероочистка и тд.). Рассматриваемое производство характеризуется большим числом открытых сооружений (этажерки,
рабочие площадки, силосы и тд.), строительные конструкции которых подвергаются одновременно воздействиям производственных сред и климатических
факторов.
В условиях мокрого режима эксплуатируются строительные, конструкции башен мокрого тушения кокса, оросительных
холодильников, градирен, а также работающие сезонно камеры размораживания вагонов с углем. Внутри конвейерных галерей и перегрузочных узлов
для транспортировки свежего кокса, зданий коксосортировки, а также внутри силосов и бункеров угля и кокса относительная влажность воздуха в
холодное время года превышает 75%, а в теплое - находится в пределах 60-75%. Конструкции указанных объектов зимой обильно смачиваются
конденсатом водяных паров, причем в верхней части силосных банок выпадение конденсата на стенках и увлажнение бетона обычно больше, чем в
нижней. Во всех зданиях коксохимического производства относительная влажность воздуха обычно не превышает 60%.
Состав растворов, которыми смачиваются строительные конструкции разных объектов, различен. Для обогащения
угля и уборки пыли используют в основном техническую воду, химический состав которой, как и на обогатительных фабриках железной руды,
во многом зависит от источника водоснабжения. Для тушения кокса применяют обычно оборотную воду, содержащую значительное количество
агрессивных примесей. Так, концентрация, мг/л, ионов SО4-- в ней колеблется от 300 - 900 (при переработке
малосернистых кузнецких углей) до 5000 - 9000 (при переработке донецких углей), а содержание фенолов обычно находится в пределах 200-400.
Выбросами из башни тушения кокса смачиваются близлежащие строительные конструкции. В радиусе 50 м от башни тушения выпадает в
сутки до 1 л/м2 осадков, содержащих около 40% ионов SО4--.
Строительные конструкции оросительных холодильников цеха улавливания подвергаются воздействию надсмольной воды,
содержащей (в мг/л): до 7500 аммиака (свободного и связанного), 1200 сульфатов, 900 хлоридов и др. Несущие строительные конструкции и полы
помещений сульфатного отделения смачиваются маточными и рабочими растворами, надсмольной водой, концентрированной серной кислотой, а помещений,
бензольного отделения - раствором бензола, 92-96%-ной серной кислотой, 8-10%-ной щелочью. Бывают случаи, когда в складах реактивов, бензольных
продуктов, в помещениях насосных на строительные конструкции проливаются растворы 98%-ной серной кислоты, 40%-ной щелочи, бензола, толуола.
Грунтовые воды в районе коксохимических предприятий характеризуются в основном теми же агрессивными агентами,
что и в районе ГОКов, а также содержат аммиак и фенолы. Возможны существенные колебания состава грунтовых вод во времени. Так, на одном и том
же участке завода в течение 12 лет содержание ионов SО4-- в грунтовой воде изменилось от 2000 до 4000 мг/л.
Наибольшее содержание сернистого газа (40—60 мг/м3) наблюдается в помещениях сушильных барабанов и в воздухе
вблизи коксовых батарей. В помещениях коксосортировки его концентрация составляет 10—20 мг/м3, а в зданиях размораживания угля и
вагоноопрокидывателей, а также в окружающей атмосфере цехов не превышает 1 мг/м3. Во всех указанных местах обнаруживается также
сероводород в концентрациях, в 2-3 раза меньших, чем концентрации сернистого газа.
Больше всего аммиака содержится в воздухе помещений коксосортировки (до 40 мг/м3), а также в
наружной атмосфере в районе коксовой батареи и градирен для охлаждения оборотной воды (20-80 мг/м3). В этих же местах
обнаруживается и фенол, но концентрация его обычно на порядок меньше, чем аммиака. Внутри конвейерных галерей угля и кокса присутствуют
окислы азота в количестве до 10 мг/м3.
К наиболее запыленным относятся помещения вагоноопрокидывателей, коксосортировки, складов сульфата
аммония, а также коксовая рампа. В коксовой пыли может находиться до 20% сульфатов. Содержание ионов SО4-- в
водной вытяжке из коксового шлама, оседающего на конструкциях башен тушения, изменяется в зависимости от сернистости шихты от 50 до 1000 мг/л.
Высокой гигроскопичностью и растворимостью отличаются пылевые отложения сульфата аммония.
Интенсивность лучистого нагрева конструкций от раскаленного кокса обычно составляет 700-2000 Вт/м2
[~ 600 - 1800 ккал/(м2 * ч)]. Источником значительных тепловыделений служат также камеры размораживания и сушильные барабаны угля,
коксовые и пекококсовые батареи, отапливаемые коксо¬вым или доменным газом. Стационарному нагреву до 170°С подвергаются фундаменты коксовых батарей.
Температура поверхности бетона открытых обслуживающих площадок коксовых батарей достигает 80°С, но в холодное время года периодически опускается
ниже нуля.
В очень тяжелом температурно-влажностном режиме эксплуатируются конструкции башен мокрого тушения кокса.
Поверхность некоторых участков конструкции башен, например перемычек въездного проема и свода открылка, испытывает в сутки около 200 циклов
изменения температуры от 300 до 80-100°С при нелинейном характере распределения температуры по толщине конструкций [28, 80]. Еще в более
тяжелых условиях эксплуатируются конструкции тушильных башен пекококсовых батарей. Перерыв между тушением у них достигает 1,5-2 ч, и за это
время зимой конструкции успевают промерзнуть. Разрушения бетона (трещины, выколы) свода открылка и перемычки наблюдаются уже через нескольку
месяцев эксплуатации, а в верхней части вытяжной трубы через 1-2 года. Остальные участки тушильных башен повреждаются в меньшей степени.
Динамические воздействия на строительные конструкции связаны в основном с работой механического
оборудования (грохотов и дробилок в здании углеобогащения) и с движением) железнодорожных и завалочных вагонов (здания
вагоноопрокидывателей, рабочие площадки коксовых батарей). Амплитуда вертикальных колебаний конструкций перекрытий под грохотами и
дробилками, а также верхней плиты рабочей площадки коксовой батареи достигает 0,35 мм при частоте соответственно 600-700 и 400 кол/мин.
Силосные сооружения испытывают динамические воздействия в результате обрушения образующегося внутри силоса сводов сыпучего.
Скорость коррозии малоуглеродистой стали в атмосфере коксового цеха на расстоянии до 50 м от башни
тушения кокса равна 0,35-0,4 мм/год, а на расстоянии 100 м ее значение примерно в 2 раза меньше (рис.4). В открытой атмосфере цеха
улавливания стальные конструкции подвергаются коррозии со скоростью 0,2-0,25, а цеха ректификации - 0,1-0,15 мм/год.
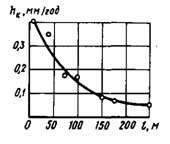
Рис.4. Средняя скорость коррозии hK малоуглеродистой стали СтЗсп в открытой атмосфере коксового цеха на
различном расстоянии l от башни мокрого тушения кокса
Срок службы противокоррозионных лакокрасочных покрытий стальных конструкций на основе битумного лака
или алкидных эмалей в атмосфере коксохимического производства не превышает 0,5-1 года. Многослойные перхлорвиниловые (5-7 слоев) и
эпоксидные (3-4 слоя) покрытия служат в атмосфере коксового цеха 1,5-2 года, химических цехов 2-3 года и цеха углеподготовки 3-4 года.
При воздействии проливов кислот срок службы перхлорвиниловых покрытий не превышает 1,5 лет.
Защита от коррозии стальных конструкций путем их бетонирования бетоном (который на практике не удается
получить достаточно плотным) и здесь оказалась неэффективной. Например, в бетоне защитного слоя стальной опоры трубопровода коксового
цеха через 3 года появились трещины шириной более 0,5 мм.
Капитальные ремонты стальных конструкций рабочих площадок и этажерок химических цехов проводятся
обычно каждые 3-4 года. Необходимость в усилении из-за коррозионных поражений стальных конструкций конвейерных галерей коксового
цеха возникает после 13-15 лет эксплуатации [37,46].
Значительному коррозионному износу подвержены стальные связи (закладные детали, соединительные планки,
опорные столики) сборных железобетонных конструкций. Так, внутри здания коксосортировки закладные детали стеновой панели разрушались с
внешней и с внутренней (обращенной к бетону) поверхности и со средней скоростью 0,2 мм/год. Узел крепления стеновой панели к колонне
был обетонирован неплотным бетоном, который через четыре года имел трещины.
В некоторых узлах закладные детали через 15—18 лет эксплуата¬ции полностью отделялись от стеновой
панели вследствие коррозионного разрушения сварных швов, которыми детали крепили к анкерным стержням.
Разрушения бетона рабочих площадок коксовых батарей вызваны в основном циклическими изменениями
температурно-влажностного режима в результате интенсивного лучистого нагрева и просачивания атмосферных осадков через верхнее перекрытие.
Наиболее быстро разрушаются места примыкания рабочих площадок к батарее и угольной башне. Через 1,5-2 года после капитального ремонта на
поверхности бетона появляются поперечные и продольные трещины, высолы и т.п. Через 3-4 года бетон защитного слоя разуплотняется на всю
глубину, легко крошится, а интенсивность коррозии арматуры составляет 0,3-0,7 мм/год. Сопоставление степени повреждения поверхностных
слоев бетона (трещиноватость, глубина карбонизации, скорость распространения ультразвуковых волн, прочность) и коррозии арматуры
конструкций, эксплуатировавшихся в условиях переменного температурно-влажностного режима (при температуре нагрева до 100°С),
показывает, что увеличение плотности бетона с марки В 2 и менее до В 4 повышает их долго¬вечность в 2-3 раза.
В отстойниках, резервуарах для технической воды и других сооружениях, испытывающих систематическое
воздействие жидких сред, разрушения в первую очередь появляются в зоне переменного уровня жидкости, где возможно многократное
замораживание насыщенного влагой бетона. Разрушение бетона оросительных холодильников наблюдается в основном на поддонах, через
которые происходит фильтрация воды.
В железобетонных конструкциях силосных корпусов повреждения проявляются в виде крупных трещин,
выколов бетона, нарушений защитного слоя. Стены силосов (особенно в верхней части) имеют нарушенную структуру. При прочих равных
условиях более разрыхленными являются внутренние поверхности стен. Повышение температуры внутри силоса в результате самовозгорания
шихты способствует трещинообразованию. Верхняя часть одной из силосных банок обрушилась вместе с надсилосной галереей после 18 лет
эксплуатации. На участках силоса, где марка бетона по водонепроницаемости была более В 4, степень повреждения бетона и коррозия
арматуры были значительно меньшими.
Характер и интенсивность разрушения железобетонных конструкций угольных башен аналогичны этим
показателям для описанных выше сооружений силосного типа. При использовании сухой шихты строительные конструкции угольныхбашен
находятся в удовлетворительном состоянии.
В главном корпусе по обогащению углей в помещениях отсадочных машин, моечных желобов, сепараторов,
обезвоживающих грохотов, элеваторов и др. разрушение железобетонных элементов связано главным образом с интенсивной коррозией арматуры.
Изменения в защитном слое вызваны процессами карбонизации и сульфатизации, а также выщелачивания СаО из бетона. Динамические воздействия
на перекрытия вызывают дополнительное раскрытие трещин, способствуют отслоению уже нарушенных участков бетона, облегчая тем самым доступ
влаги и агрессивных агентов к арматуре.
В подземной части здания вагоноопрокидывателей и в конвейерном тоннеле повреждения железобетонных
конструкций (высолы, трещины, отколы защитного слоя, коррозия арматуры) связаны с воздействием грунтовых вод, из-за нарушения
гидроизоляции и недостаточной плотностью бетона.
Утепленные железобетонные покрытия зданий, даже в помещениях с большим паровыделением (покрытия галерей
подачи влажного кокса от коксовых рамп на коксосортировку, помещений натяжных станций коксовых рамп и др.), значительных повреждений не
имеют после 10 и более лет эксплуатации. Неутепленные конструкции на аналогичных по условиям службы участках за такой же срок пришли в
аварийное состояние.
Повреждения конструкций объектов химических цехов (перекрытий этажерок и покрытий площадок) концентрируются
в местах непосредственного воздействия щелочей, кислот и маточных растворов. Например, бетон поясов ферм покрытия склада сульфата аммония,
на котором постоянно находится слой пыли толщиной в несколько сантиметров, не имел существенных повреждений после 8 лет эксплуатации. Но в
местах попадания влаги (из-за неисправности кровли) защитный слой бетона за тот же срок был полностью разрушен на глубину 1,5-2 см.
Разрушение полов открытых площадок и помещений химических цехов, выполненных из кислотоупорных штучных
материалов, происходит в результате проникания агрессивных растворов сквозь швы к основанию. Это вызывает разрушение основания и вздутие
покрытия пола. Периодичность капитальных ремонтов полов не превышает 2-3 лет.