Âåðíóòüñÿ ê ñïèñêó ïóáëèêàöèé
EQUIPMENT, POWER
EVALUATION OF EFFECT OF MECHANISMS OF COKE OVEN MACHINES ON PLANT RELIABILITY
A. S. Parfenyuk, A. A. Bulatov, N. A. Khromov, S. P. Veretel'nik, G. A. Vlasov, and E. P. Romanenko .
Koks i Khimiya, No. 2, pp. 28-32,1990
UDC 662.74.002.5:044.2
The reliability of equipment is governed by the design and process parameters of the machines, as well as the operating conditions, quality of repair and technical servicing. It is known that failures of mechanisms of coke oven machines have different effects on failures of the plant. Breakdown of some mechanisms leads immediately to shutdowns and losses of production, while failure of others permits continuation of the processing operation and only after a certain time has elapsed can it lead to plant shutdowns. For this reason, the analyze reliability and develop an effective system of technical servicing and repair (TSP), formulation of requirements on machines and mechanisms in terms of improvement or design, a method is required for classification of machines and mechanism according to their degree of influence on failure of a coke plant.
In the present article we used a specific example to demonstrate the use of the new method of "tree of failures" (MTF) set forth in [1-3] to evaluate the effect of reliability of mechanisms of coke oven machines on the reliability of a coke plant with respect to development of a system for technical servicing and repair of coke oven machines.
MTF enables us to focus our attention on specific types of failures, i.e., to construct the tree of failures for those events, whose appearance is connected to a certain specific cause (group of causes). For example, for equipment designers it offers the possibility of evaluating the effect of failures of mechanisms caused by design imperfection on the production process. The main principles of constructing the tree of failures are as follows:
- failure of a machine leading to failure of the plant is considered the concluding even in the structure of
the tree of failures;
• failures of mechanisms and devices of coke oven machines are considered initial events;
- the undesirable events that lead to failure of the plants are viewed as a sequence of events of different levels;
- the functional properties of the higher level events are determined by isolating the causes for defects and the intermediate events are analyzed to determine the logical relation between initial events that lead to failure of the plants;
- the tree of failures is plotted by means of logic symbols of the events as a structural depiction of logically-connected events.
To evaluate the probability of appearance of initial events we conducted quantitative analysis of a tree of failures based on statistical information concerning failures of mechanisms and devices of coke oven machine determined on the basis of analysis of each case by an expert commission composed of representatives of administration, the mechanical and operational services of the plant. Quantitative analysis of the tree of failures consists of determining, the number of minimal emergency combinations; the probability of appearance of an event "failure of a coke plant"; the significance of failures of each of the initial elements.
The event "failure of the coke plant" can depend on both failure of one individual mechanism and on the result of a simultaneous combination of failures of several elements. In the second case failure of one of the elements generally does not lead to failure of the production process. To evaluate the effects of these mechanisms on functioning of the machine we must determine the probability of appearance of such a combination.
The structure of an emergency combination in the tree of failures is determined by the number of initial events connected by the symbol U. The probability of appearance of an emergency combination QAB in this case
© 1990 by Allerton Press, Inc.
(1)
where Q, is the probability of failure of mechanism i in a given emergency combination; II is the total number of mechanisms in the combination.
Determination of the significance of failures of mechanisms is made to correspond with the significance factor Fi(t) [1]:
(2)
where g[Q(t)]— is the probability that the i-th mechanism will promote the development of failure in an emergencyì
combination at time t; g[Q(t)]— is the probability of appearance of failure of machines at time t.
(3)
Here k is the number of emergency combinations in which the i-th mechanism participates; QABj is the probability of appearance of the j-th emergency combination; is the probability of failure of the i-th mechanism in the
emergency combination with one element.
For optimization of TSP a machine in which all the mechanisms would have the same time to failure is ideal, Le., the same frequency of failures, probability of appearance of failure and, consequently, significance factor. However, if for any mechanism i the significance factor is greater than the average value F„ for the machine then special attention must naturally be devoted to this mechanism. Practice in solving TSP problems at the Avdeevka Plant has shown that for effective repairs it is sufficient to divide mechanisms into two categories.
Quantity Fsv can be determined by dividing the total significance factor of failures of all mechanisms of the
machines by their number m:
(4)
The mechanism of coke oven machines were classified based on the number of failures n of these mechanisms in emergency combinations and by comparison with the average structural significance factor The first category includes mechanisms for which the following conditions must be fulfilled:
- the appearance of the concluding event in an emergency combination with one mechanism directly leading to failure of the plant;
- the structural significance factor of the mechanism greater than or equal to the average structural significance factor of the machine.
Failures of such mechanisms directly lead to shutdown of the plant and require immediate elimination. The second category includes mechanisms for which two conditions must be met:
- the appearance of the concluding event in an emergency combination with two and more mechanisms;
• the significance factor is less than the average structural significance factor of the machine.
Failures of these mechanisms lead directly to failure of the plant and for this reason their repair can be
conducted with a time delay, combining it with repair of equipment in the first category.
In other cases, for example, in solving problems of design improvement of machines, the number of categories can be greater.
The general principles for analysis of reliability using MTF are universal and their efficiency has repeatedly been confirmed in solving different problems of improvement of coke oven equipment.
We analyzed reliability for coke oven machines, anchoring elements, doors, the lining of coke ovens and confirmed the feasibility of widespread use of this method. The design and process characteristics of the equipment and process, the operating characteristics, the climatic influences at different plants are easily allowed for by changes in the structure of the tree of failures.
Let us demonstrate bow a problem is solved specifically, using one of the coke oven machines as an example - the door-lifting machine. In constructing the tree of failures in this case the initial events associated with failures of the electrical part, monitoring and measurement instruments and automation, operator errors are not considered.
"Failure of the plant" Z, associated with nonfulfillment of the principal functions of the door-lifting; machines occurs when one of the following events arrives: coke cake is not produced T1; charging is not ensured T2 repair work is not ensured T3 , and can be represented in the form of a Boolean identity
(5)
The event "coke cake is not produced" Tt occurs on arrival on an intermediate event, when "lifting of the door is not carried out" F1 and "sending of the coke cake into the coke transport care is not ensured" F2 Intermediate event F1 in turn occurs during failures of the following mechanisms: removal • supply of doors A2; movement of the machine A1; rotation of the door lifting device A3, lifting of the door A4; metal structures A5 , and also during occurrence with a certain time lag of event G1 - "inadmissible force of door lifting."
Event G1 will occur if "cleaning of the door is not carried out" V, and "cleaning of the frames is not carried out" V2. The initial events for V1 will be failures of the door cleaning mechanisms A7 , rotation A3, removal-supply A2, metal structures A5; for event V2: failures of the frame cleaning mechanisms A8, movement of the frame cleaning equipment A9; movement A1 rotation A3, metal structures A5.
For intermediate event F2 - "sending of coke cake is not ensured" - the initial events should be considered failures of the mechanisms for movement of the machine A1, movement of the skuddle A6, rotation A3, metal structures A5.
Thus, event T1 can be represented in the form of the expression:
(6)
Event T2 will occur under the condition "impossibility of door installation" F3. The initial events for F3 will be the events A6, A1, A2, À3, A4, A5, as well as event G2 - "inadmissible force of door installation," which occurs with a time lag, when event T2 can be represented in the form of the identity:
(7)
Event T3 - "repair work not ensured" - leads to failure of the production process if "replacement of the door is not fulfilled" F4 or "reinforcement work is not carried out" F5. The event F4 will occur when intermediate events V3 occur - "lifting of the door is not fulfilled" or "installation of the door is not fulfilled" V4.
The initial events for V3 will be À1, A2, A3, A5, and for V4 - events À1, À2, À4, À5.
For event F3 the initial events will be À1, À2, À4, À5,À3.
Then,
(8)
Finally, failure of the production process will appear as follows:
(9)
The tree of failures of the door-lifting machine is shown in the figure.
Using the main laws of Boolean algebra, we obtain the expression
(10)
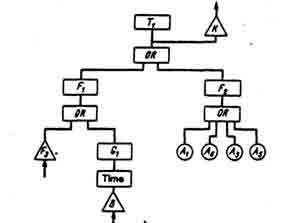
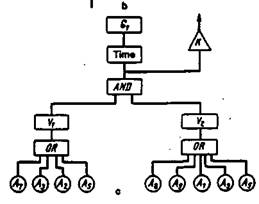
Tree of failure of door-lifting machine: a-c) initial and intermediate events.
which enables us to analyze in sequence the reliability of the door-lifting machine allowing for each specific type of failure of mechanisms and devices. The probability of failure of mechanisms of the door-lifting machines Q(A1) during a month (2167 deliveries), calculated according to the data of [4], is shown in Table 1.
It is apparent from the obtained tree of failures that the final event - "failure of the coke plant" - can occur with a different combination of initial and intermediate events. Consequently, to reduce the probability of plant

Table 1
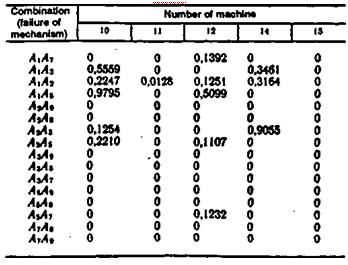
Table 2
failure we must determine the most probable types of failures and eliminate them if possible determined by the principle of minimal emergency combinations [1],
For the given tree of failures the total number of found emergency combinations is 23, six combinations of one mechanism and 17 - combinations of failures of two mechanisms:
Emergency combinations with one mechanism
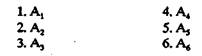
Emergency combbations with two mechanisms
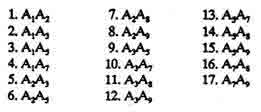
The probability of appearance of emergency combinations with two mechanisms calculated according to formula (1) is shown in Table 2. As is apparent, emergency combinations with one mechanism create the principal potential threat to reliability of the door-lifting machine.
Table 3
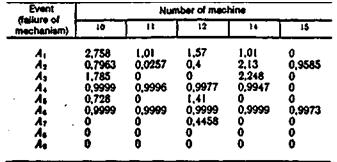
Table 4
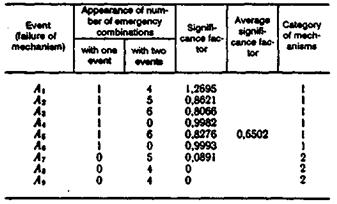
Table 3 shows the structural significance factor of the mechanisms of the door-lifting machine calculated according to formula (2).
Classification of mechanisms is carried out according to the proposed method. Quantity F(t) is calculated according to formula (4). The results of classification are shown in Table 4.
The possibilities of using MTF are not limited merely to obtaining the initial data for optimization of the TSP system. The average structural significance factor Fsv(see Table 4) is as arbitrary as division of the mechanisms into two categories according to their degree of vulnerability. With data on the number of emergency Combinations with one or two mechanisms at our disposal and the significance factors F(t) for the corresponding mechanisms, we can propose a second variant for division, for example, into three categories, in order to ensure a differential approach to operation and improvement in the design of the most important mechanisms. In this case the first category will include the mechanisms of motion of the machine, lifting of the door and motion of the scuttle of the coke guide, for which the significance factor is close to one. The second category should include the mechanisms for removal-supply of the door-lifting device, rotation of the door and metal structures of the machine, and the third category should include the other mechanisms.
The proposed method offers a possibility of qualitative-quantitative evaluation of reliability, universal and more objective in comparison with the usual statistical analysis, since it allows for the effect of equipment reliability on the production process as a whole.
CONCLUSIONS
The results of analysis of operational reliability of coke oven machines using the method of tree of failures substantiate the need to change the designs of the most vulnerable mechanisms in order to increase their functional reliability. This will assist in developing an effective TSF system for coke oven machines allowing for the different level of vulnerability of mechanisms.
REFERENCES
- J. Hartley and H. Kumamoto, Reliability of Technical Systems and Evaluation of Risk, K Mashinostroenie, 1984.
- V. A. Kravets, Systems Analysis of Safety in the Oil and Gas Industry, Moscow, Nedra, 1984.
- B. Dillon and Ch. Singkh, Engineering Methods for Ensuring System Reliability [Russian tran Moscow, Mir, 1984.
- V. M. Grebenik and V. K. Tsapko, Reliability of Metallurgical Equipment (Evaluation of Ope Reliability and Lifetime): Handbook, Moscow, Metallurgjya, 1980.
- G. A. Vlasov et al., "Introduction of a control system for technical servicing and repair of co machines,'' Koks i Khimiya [Coke and Chemistry USSR], no. 6, pp. 20-23,1986.
Âåðíóòüñÿ ê ñïèñêó ïóáëèêàöèé
|