Вернуться к списку публикаций
УДК 622. 5
ОЦЕНКА ТЕХНОГЕННОЙ БЕЗОПАСНОСТИ ТЕХНОЛОГИЧЕСКИХ КОМПЛЕКСОВ
Топоров А.А., Парфенюк А.С., Власов Г.А.
Донецкий национальный технический университет
В статье представлены основные направления оценки техногенной безопасности технологических комплексов и предложен ряд комплексных критериев, использующих энергетический и информационный подходы.
В настоящее время в связи с увеличением энергопотоков и усложнением современных комплексов технологического оборудования и повышением общего уровня требований безопасности возникает необходимость оценки их техногенной опасности /1/. Как правило, в таких технологических объектах создают условия, которые значительно отличаются от условий окружающей среды (давления, температуры, концентрации веществ, действующих нагрузок, напряжений и т.п.). Неравновесное состояние или наличие разности потенциальных величин внутри и снаружи объекта, делает технологический объект в той или иной степени потенциально опасным. При возникновении цепочки неблагоприятных событий растет вероятность неконтролируемого высвобождения накопленного потенциала, что может привести к возникновению техногенно опасных ситуаций и аварий. К техногенно опасным ситуациям относят такие изменения в функционировании и структуре технического объекта, которые могут вызвать нарушения технологического режима, уменьшение уровня надежности ниже заданной величины, появлению возможностей выбросов, утечек, возгорания, взрывов, а также нанесения ущерба человеку, окружающей среде и другим техническим объектам.
Для современных технологических комплексов ситуация осложняется тем, что большинство из них исчерпали ресурс, и деградация продолжается, зачастую не учитываются взаимовлияние близрасположенного оборудования и т.д. /2/. Существующие методики оценки уровня опасности технологических комплексов, в основном, основаны на экономических показателях и направлены на оценку риска, что не дает достаточных обоснований для принятия решений при проектировании таких объектов.
Для эффективной оценки уровня безопасности технологических комплексов необходимо решить ряд задач:
- представление технологического комплекса в обобщенном виде;
- выбор комплексного, пригодного для различных по типу объектов, критерия;
- оценка деградации объекта на всех стадиях его работы;
- определение показателей опасности;
- зонирование территории по уровням опасности;
- оптимизация структуры и работы комплекса.
Весьма показательной составляющей техногенной безопасности является уровень производственного травматизма, который зависит от многих факторов, среди которых можно выделить специфику и уровень организации производства, характер труда и профессиональную подготовку рабочего персонала, степень опасности различных зон производственной территории, зависящую во многом от уровня изношенности оборудования, контроль за безопасностью со стороны администрации и инженерных служб.
Так, например, на основе статистической информации службы охраны труда и техники безопасности коксохимического производства был проведён комплексный анализ травматизма в коксовых цехах, который позволил установить основные причины опасностей, наиболее опасные профессии и опасных зоны на территории коксового цеха. В результате обработки статистической информации установлено, что наиболее травмоопасными профессиями являются (в %): дверевые – 26, слесари-ремонтники – 18, люковые и барильетчики – 16, машинисты коксовых машин – 8 %, ИТР. На десяток других профессий приходится – 32 %.
Наиболее типичные причины травматизма(в %): нарушение соответствующих инструкций и правил по технике безопасности – 54, нарушение технологии процесса – 12, конструктивные недостатки механизмов, машин и конструкций – 10, неисправности механизмов и машин – 10, другие причины – 14.
Последствия травматизма следующие: лёгкие травмы – 36, тяжёлые травмы – 33, смертельные травмы – 26, групповые травмы – 5. В /3/ представлены описания наиболее характерных аварийных и травмоопасных ситуаций в коксовом цехе и предложены мероприятия по их предотвращению.
Одним из наиболее эффективных путей изучения процесса функционирования сложных технических объектов является системный анализ /4/. В соответствии с принципами системного анализа любой технический объект можно представить как систему - совокупность элементов, обладающих связями и свойствами, которых не было до объединения элементов в систему. Учет современных требований к уровню безопасности при системном подходе, требует рассмотрения видов возможных изменений в структуре системе и ее функционировании, а также причины их вызывающих. Для оценки общего состояния системы представляется целесообразным принять информационную энтропию, которая для систем с непрерывным изменением величины параметров принимает вид:
,
где pi(x) - вероятность состояния x для i-го параметра.
При определении уровня опасности представляется целесообразным основываться на технических параметрах, характеризующих объект. Эти параметры можно разбить на три группы: физические, отражающие физические свойства объекта; химические, характеризующие химические свойства среды в объекте и геометрические, отражающие соотношения характерных размеров объекта. К физическим параметрам можно отнести перепад давлений внутри и снаружи объекта Р, разность температур внутри и снаружи объекта Т, величина общей кинетической энергии движущихся частей в объекте Е. К химическим параметрам относят количество химически активного вещества в объекте V и его предельно допустимые концентрации (ПДК). Если вещества в объекте являются пожаро- и взрывоопасными, то вместо ПДК используется величина минимальной взрывоопасной концентрации. К геометрическим параметрам относят объем объекта Vo, гидравлический радиус R и периметр П стыковочных узлов, величина удельной поверхности объекта А.
На основании этих технических параметров разработан ряд показателей влияющих на уровень опасности U технических объектов. В общем виде уровень U определяется по формуле:
U=P*Q*V,
где Р - показатель потенциала опасности; Q - показатель состояния объекта (вероятность реализации потенциала опасности); V – уровень тяжести последствий.
Для техногенной зоны уровень техногенной опасности можно определить по формуле:
,
где: j - коэффициент, зависящий от среды распространения опасного техногенного воздействия; L- расстояние от объекта до рассматриваемой точки пространства.
Если в пространстве техногенной зоны находится несколько техногенно-опасных объектов то уровень техногенной опасности в каждой точке пространства определяется как:
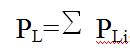
При создании технических объектов обычно рассматриваются несколько вариантов их конструкций. В этих условиях возникает необходимость определения наилучшего варианта, т.е. оптимального.
В качестве показателя, позволяющего оценить уровень техногенной опасности производства (объекта), на этапе его эксплуатации, может быть принят критерий уровня опасности объекта (U), который состоит из произведений показателей потенциала опасности и состояния.
Условно уровень U подразделен на шесть подуровней: состояние объекта оценивается как отличное – 1; хорошее – 2; нормальное – 3; опасное – 4; аварийное – 5, катастрофическое -6.

где - n1 … n6 – порог уровня опасности.
Показатель состояния объекта отражает склонность объекта к реализации накопленной энергии в техногенно-опасных состояниях и влияет на уровень опасности.
Сам объект, можно рассматривать как техническую систему, состоящую из множества элементов (опоры, обшивка, каркас, болтовые соединения, теплообменные поверхности и т.п.), каждый из которых вносит вклад в уровень опасности объекта. Все эти элементы обладают набором параметров (толщина стенки, площадь поперечного сечения, коэффициент запаса прочности и т.п.), которые с течением времени изменяются - деградируют. Поэтому, показатель состояния объекта определятся как средне арифметическое показателей состояния элементов:

Деградация элементов для большинства агрегатов заключается в изменении геометрических размеров и формы (толщины стенок, пары трения) элементов объекта под действием внешних и внутренних сред, т.е. происходят процессы коррозии и трения. В более редких случаях происходят изменения физико-механических и химических свойств материала, из которого изготовлены эти элементы.
Для этого предлагается использовать гамма – процентный ресурс. Эта методика реализует традиционно сложившийся подход, базирующийся на предположении, что средняя скорость коррозии, определенная на момент прогнозирования, сохранится и в будущем. Однако практика доказывает, что скорость коррозии, как правило, не постоянна, а реальная картина развития коррозионного процесса выглядит следующим образом.
Поскольку в каждой точке поверхности элемента происходит случайный процесс изменения толщины металла во времени, то изменение толщины металла есть функция от времени S = f(t). Тогда показатель состояния каждого элемента:

где Тэ – время эксплуатации элемента;
Тобщ – общий срок службы элемента, определяющийся по показаниям
истинной скорости деградации.
При приближении величины Q к единице состояние объекта приближается к аварийному состоянию, а следовательно и техногенная опасность производства возрастает.
В технологических агрегатах присутствуют узлы стыковки футеровочных и металлических элементов, обеспечивающие загрузку-выгрузку сырья и продукта, отвод-подвод газов, контроль, очистку, ремонт и т.д. Стыковочные узлы находятся в контакте с внутренними рабочими объемами и внешней средой и работают в условиях постоянных температурных перепадов, механических и химических воздействий.
Общей для всех этих конструкций является проблема обеспечения надежности и герметичности. Их элементы в общем случае находятся в поле воздействия различных по характеру нагрузок: давление перерабатываемого материала и газов, образующихся в процессе переработки; нагрузки от воздействия обслуживающих машин; температурные перепады при загрузке - выгрузке материала; при изменении направления тепловых потоков в отопительной системе; воздействие агрессивной среды при высоких температурах. Кроме того, в узлах протекают термомеханические процессы, представляющие собой взаимодействие элементов в переменном температурном поле при циклическом нагреве и охлаждении, в результате чего происходит изменение напряженно-деформированного состояния с постепенным разрушением материала. Это усложняет учет влияния перечисленных выше факторов на состояние элементов узла.
Для оценки уровня техногенной опасности стыковочных узлов использована система критериев работоспособности конструкции, учитывающая влияние конструктивных, температурно–механических и технологических факторов.
В качестве параметра принят показатель прочности элементов узла *, для огнеупорных элементов - это предел прочности на растяжения, для металлических элементов - предел выносливости:
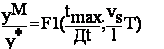
Критерий для оценки прочности элементов:
;
где м - действующие напряжения, МПа;
К1 - комплексная функция, учитывающая влияние на прочность узла основных действующих факторов: температурного, механического, технологического.
В общем виде критерий разрушения представляет собой:
.
Оценка состояния стыковочных узлов по критериальному уравнению позволяет выявить неработоспособные участки и моменты времени их отказа.
Для получения численных критериев работоспособности использована математическая модель температурного и напряженно–деформированного состояния узла.
Так как в настоящее время основным требованием, предъявляемым к техническим объектам, является низкий уровень техногенной опасности, то выберем его в качестве целевой функции:
В этом случае ограничениями служит показатель производительности технического объекта, капитальные затраты на создание, себестоимость получаемой продукции, энергозатраты на производство и др. Граничными условиями являются пределы изменения входящих в модель технических параметров, характеризующих объект.
Оптимизация технического объекта по показателю уровня техногенной опасности U, позволяет определить наиболее приемлемый вариант при заданных ограничениях.
Разработанный подход является универсальным, как для проектируемого оборудования, так и для существующего. В частности, численные исследования различных технологических комплексов по показателю U для заданных технологических процессов и проектных параметров, их структур, размещения в пространстве и внешних условий показали значительные преимущества ряда новых и модернизированных технологий и конструкций основных агрегатов коксового производства, комплексов по переработке твердых промбытотходов, систем магистральных трубопроводов для транспортирования жидких и газообразных энергоносителей, прежде всего в части их безопасности.
Список использованной литературы:
- Белов П.Г. Теоретические основы системной инженерии безопасности –М.: ГНТБ “Безопасность” МИБ СТС. –1996, 424с.
- Чубенко А.В., Топоров А.А. Оценка техногенной безопасности урбанизированных территорий / Экологические проблемы индустриальных мегаполисов: Материалы международной научно-практической конференции. В 2-х томах. Донецк, 2004. Т.1. С.269 – 274.
- Семеренко С.В., Парфенюк А.С., Топоров А.А. Пути повышения техногенной безопасности в коксовых цехах / Экологические проблемы индустриальных мегаполисов: Материалы международной научно-практической конференции. В 2-х томах. Донецк, 2004. Т.1. С.287 – 291.
- Топоров А.А. Новый подход к анализу техногенно опасных ситуаций на технологических производствах. // Наукові праці ДонНТУ. Серія: Хімія і хімічна технологія. Випуск 95 / Донецьк: ДонНТУ, 2005. С.126 – 130.
Вернуться к списку публикаций
|