1.4.6 Закрепить заготовку в центрах станка, а в резцедержателе в место резца установить роликовый обкатник (рисунок 1.2).
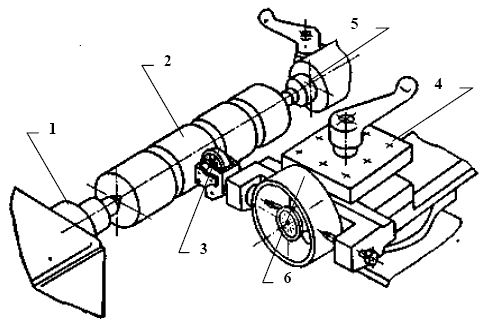
Рисунок 1.2 - Схема работы обкатника: 1 – патрон станка; 2 – заготовка; 3 – роликовый
обкатник; 4 – резцедержатель; 5 – центр; 6 - динамометр
1.4.7 Установить режимы обкатывания: s = 0,2 мм/об, v = 0,5 м/с.
1.4.8 Установить для первого пояска усилие обкатывания . Для этого, подвести обкатник до касания роликом поверхности первого пояска и вращением нагрузочного винта сделать подачу на 0,1 мм. Обкатать поясок за один рабочий ход. Повторить указанные приемы для остальных участков, последовательно изменяя давление обкатывания, каждый раз увеличивая подачу на 0,1 мм.
1.4.9 Обкатать различные участки с различной скоростью подачи s.
1.4.10 Измерить диаметры поясков и шероховатость их поверхности на всех участках.
1.4.11 Измерить твердость исходной и обкатанной поверхностей.
1.5 Содержание отчета
Отчет должен содержать:
1) эскизы образцов с указанием марки обрабатываемого материала, его характеристики, размеры до и после обработки;
2) схему установки, заготовки и обкатки;
3) расчеты теоретической высоты микронеровностей, полученные по формуле 1 и давления по формуле 2. Результаты опытов свести в таблицу 1.1.
Таблица 1.1 - Сводная таблица опытных данных
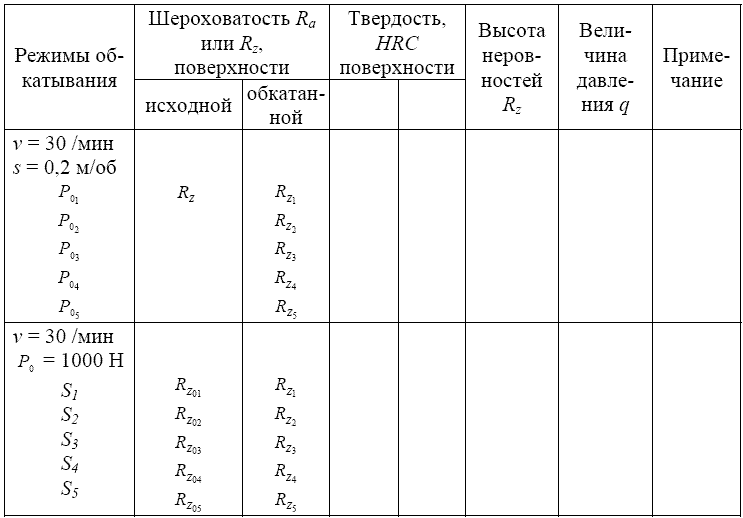
4) графики зависимостей шероховатости поверхности от усилия и подачи. На графике провести горизонтальные линии, соответствующие границам областей шероховатости;
5) сделать выводы.
1.6 Контрольные вопросы
1.6.1 Что в большей степени влияет на шероховатость обкатанной поверхности: величина давления или подачи?
1.6.2 От чего зависит глубина упрочненного слоя?
1.6.3 Как оценивается степень упрочнения детали?
1.6.4 Какие методы упрочняюще-калибрующей и формообразующей обработки металлов вы знаете?
Список рекомендуемой литературы
- Попов Е.А., Ковалев В.Г., Шубин И.Н. Технология и автоматизация листовой штамповки. - М.: Издательство МГТУ им. Баумана, 2000. - 480
- Аверкиев Ю.А., Аверкиев А.Ю Технология холодной штамповки. – М.: Машиностроение, 1989. - 304 с.
- Машины и технологии обработки металлов давлением: Лабораторные работы/ Под редакций Живова Л.И. и др. Киев: «Вища школа», 1975,196 с.
- Методическое пособие по лабораторным работам./ Под общ. ред. Фейгина М.М. Омск: «Омская правда», 1972, 188 с.
- Дальский А.М. Технология конструкционных материалов. - М: Машиностроение, 1990. – 352 с.
- Богоявленский К.Н., Елкин Н.М., Каспаров И.А. и др. Оптимизация режимов обработки при раскатке профильных колец // Кузнечно-штамповочное производство. – 1987. - № 10. – С.10.
- Елецкий С.А., Решетников В.А., Телеш В.В. и др. Внедрение технологии раскатки кольцевых заготовок для производства оборудования АЭС // Кузнечно-штамповочное производство. – 1987. - № 10. – С.16.
- Технология металлов и конструкционные материалы. / Под редакцией Б.А.Кузмина. - М.: Машиностроение, 1981. - 351 с.
- 9 Капорович В.Г. Ротационная обкатка металлоизделий из труб // Изобретатель и рационализатор. - 1992. - № 2. – С.2.
- Еленев С.А. Холодная штамповка. - М.: Высшая школа, 1988. - 220 с.