Thermodestruction of brown coals of different genetic types
Fuel Processing Technology 77-78 (2002)-p.145-150
Ludmila Butuzovaa,*,Lubov Isaevaa,Oksana Turchaninab
Andrzej Krztonc
aL.M. Litvinenko Institute of Physical Organic and Coal Chemistry, National Academy of Sciences of the Ukraine,
70 R. Luxemburg str., Donetsk 83114, Ukraine
bDonetsk National Technical University, 48 Artema str, Donetsk 83000, Ukraine
cInstitute of Coal Chemistry, Polish Academy of Sciences, 5 Sowinskiego, 44-102, Gliwice, Poland
Received 4 February 2002; received in revised form 7 March 2002; accepted 8 April 2002.
Abstract
The influence of brown coal genetic type and method of chemical pre-treatment on its behavior in pyrolysis processes has been shown. An important role of brown coal reductivity in coal thermal decomposition has been ascertained. It has been found that chemical pre-treatment permits variation of the rate of pyrolysis, the yields of pyrolysis products and structure of semi-cokes. © 2002 Elsevier Science B.V. All rights reserved.
Keywords: Brown coal; Structure; Pyrolysis; Additives.
1. Introduction
It has been noted that coals from several seams display aberrant coking properties and elemental composition compared with coals above and below the succession. Such anomalous properties have been detected for Plessey coal in the Northumberland and Durham coal fields, the Katharina seam of the Ruhr coal field and h10, k8, l21, l5, m2, m51 seams of the Donets basin and others, which at the time of their deposition, were marine-influenced [1,2].
Depositional environments and primary transformations of vegetal material at the peat stage define the differences in composition and properties of coal matter, which are known as the peculiarities of coal types by reductivity [2-5]. The coals of the same rank and petrographic composition but with aberrant properties are called low-reduced (LRC) and reduced (RC) type (GOST 17070-87, USSR) or perhydrous and subhydrous coals [1,6,7]. The properties of brown coals are determined by primary factors of coalification more than properties of high rank coals. Therefore, the properties of genetic type obviously prevail upon the properties, which were acquired during coalification at the brown coal stage. Nevertheless, the peculiarities of chemical composition for the LRC and RC brown coals were found comparatively recently [3,5]. The reason is that up to the present, no pair of isometamorphic samples of different genetic types have been found in the same brown coal basin. Accordingly, there are no criterion which can characterize the type by reductivity at the brown coal stage [5].
By analogy with hard coals, it could be expected that the different behavior of LRC and RC types of brown coals in the processes of thermal and thermochemical destruction. Now, special attention is given to coal thermochemical processing using organic additives for direct control of the yield and composition of products [6,7].
The aim of this paper is to study the effect of brown coal genetic type upon the semi-coking products yield and semi-coke structure. The paper also describes the effects of the chemical pre-treatment of LRC and RC coals on its reactivity in pyrolysis processes.
2. Experimental
Brown coals of different genetic types from the Kansk-Achinsk (Berezovsk deposit) and Dneprovsk (Aleksandriya deposit) basins were examined (Table 1).
Investigated brown coals are uniform by petrographic composition, but they are differed by the type of reductivity, i.e. they are the appropriate subjects for comparison. The limestone of a layers roof and finely crystalline pyrite were used for selecting and testing of LRC and RC samples as reliable signs of type by reductivity [8].
The thermal behavior of coals was studied by differential thermal analyses and classical Fisher method.
Brown coals produce the powder-like semi-cokes and cokes. The caking ability of coals is bound up with its ability to form liquid products during thermal destruction, which are not evolved enough from non-caking coals. Thus, semi-coking is carried out in the presence of the products of coal-tar distillation (absorber oil) and the radical polymer¬isation initiator (acrylic acid dinitrile-AAD) to strengthen an agglomeration and other lacing processes in the solid residue. Oil was used as component, which is known to be responsible for synthesis reactions during coking. The radical polymerisation initiator.
Table 1 - Characteristics of initial coals
Basin |
Type |
|
Ultimate
|
analysis (%) daf
|
|
Petrographic |
analysis (%) |
|
Rm0 (%)
|
H/C, at
|
Wa |
Ad |
Vdaf |
Std |
C |
H |
(O+N) |
Vt |
L |
I |
Kansk-Achinsk |
LRC |
10.9 |
8.6 |
46.8 |
0.36 |
72.7 |
4.9 |
22.0 |
96 |
1 |
3 |
0.46 |
0.81 |
Dnepropetrovsk |
RC |
7.2 |
11.7 |
55.8 |
3.93 |
69.0 |
6.0 |
21.1 |
94 |
5 |
1 |
0.38 |
1.04 |
was introduced to affect the course of radical reactions. Coals were pre-treated with solutions of AAD and absorber oil (2:1 and 1:1) and dried at room temperature to constant weight.
Differential thermal analysis of the samples was carried in a Paulic-Paulic-Erdei Q-1500D thermobalance at the heating rate of 100C min-1 in a closed platinum crucible.
The petrography, proximate and ultimate analysis of the samples was determined according to standard procedures.
X-ray spectra of thermally treated coals were taken with the apparatus "Kristalloflex Siemens" using filtered cuprum radiation. d002, Lc and other parameters were calculated with an accuracy of d002 ± 0.01 A and Lc ± 1A within angles from 50 to 1100.
IR-spectra of the solid samples were recorded on a FT-IR "Bio-Rad" FTS-7 spectrometer with DRIFT technique. The samples were prepared in the form of 5% mixture of coal with potassium bromide. Multipoint baseline correction was performed using a standard software package.
3. Results and discussion
As can be seen from Figs. 1 and 2, chemically pre-treated samples are distinguished by their thermostability. Comparison of values of the relative mass loss (Fig. 1) for the Kansk-Achinsk coal at the presence of different oil contents shows that the behavior of coal during heating depends on the presence and concentration of liquid components. Fig. 2 shows the temperature dependencies of the rates of weight gain or loss. They are plotted by way of graphic differentiation of the mass loss curves (TG). The curves have one extreme, which is located in the field of 430 °C. The shift of the maximum mass loss rate.
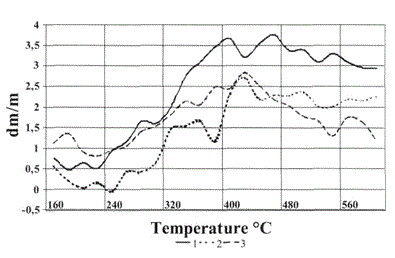
Fig. 1. Temperature-dependence of the relative mass loss for oil-treated Kansk- Achinsk brown coal (1-0.02%; 2-0.13%; 3-1.6% oil)
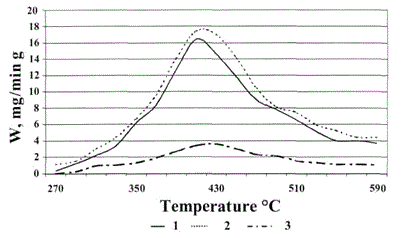
Fig. 2. Temperature-dependence of the mass loss rates for the original (1), oil-treated (2) and AAD-treated (3) Kansk-Achinsk brown coal.
after coal pre-treatment indicates the great possibility of managing pyrolysis by injection of the compounds responsible for radical processes.
As can be seen from Table 2 during semi-coking of Kansk-Achinsk LRC products with a smaller content of tar and higher content of semi-cokes are formed in contrast with the products of RC semi-coking. Introduction of the radical polymerisation initiator (AAD) results in an increase of the solid residue yield and in a change of liquid and gaseous products relation. The effect is expressed stronger at semi-coking of pre-treated RC.
An increase in the yield of semi-cokes, liquid products and decreases in the water quantity are observed under the action of absorber oil.
It should be noted that more intense interaction of the above additives is characterized for RC. Especially a significant increase in the tar yield is detected for the pre-treated RC. It is possible to get up to 17.8% of the resin yield.
Table 2 - Yield of the semi-coking products for the original and chemically treated brown coals
Coal, method of pre-treatment |
Type |
Semi-coke |
Water |
Tar |
Gas+losses |
Kansk-Achinsk |
Original |
LRC |
53.5 |
12.4 |
8.6 |
25.5 |
1% AAD |
56.6 |
10.0 |
12.9 |
20.5 |
1% oil |
56.5 |
12.4 |
9.2 |
21.9 |
Dnepropetrovsk |
Original |
RC |
32.1 |
27.8 |
14.4 |
25.7 |
1% AAD |
46.8 |
11.4 |
13.7 |
28.1 |
1% oil |
46.7 |
10.7 |
17.7 |
24.9 |
Table 3 - X-ray characteristics of samples
Method of coal pre-treatment |
t (0C) |
d002, nm |
Δd002, (%) |
ΔLC, (nm) |
ΔLC, (%) |
La, (nm) |
ΔLa, (%) |
h/l |
n |
nγ |
Original |
- |
0,404 |
|
0,69 |
|
2,5 |
|
0,74 |
3 |
1 |
420 |
0,421 |
4,2 |
0,52 |
-24,3 |
2,8 |
12,0 |
0,83 |
3 |
1 |
550 |
0,421 |
4,2 |
0,78 |
13,8 |
2,3 |
-8,5 |
0,49 |
3 |
3 |
1% AAD |
420 |
0,433 |
7,2 |
0,56 |
0 |
2,5 |
18,8 |
0,74 |
2 |
1 |
550 |
0,365 |
-9,7 |
0,96 |
-12,0 |
2,2 |
39,1 |
1,62 |
4 |
2 |
1% oil |
420 |
0,421 |
1,7 |
0,64 |
-24,0 |
1,9 |
-7,2 |
1,01 |
3 |
2 |
550 |
0,395 |
-2,2 |
0,76 |
-20,0 |
2,0 |
10,1 |
1,27 |
3 |
2 |
Lathe aromatic units diameter; n-number of layers in a stack; n-number of γ-bands.
The influences of chemical additives are most clearly seen from the X-ray analysis of the semi-cokes. It follows from Table 3 that pre-treatment of coal results in decrease of the network distance (d002) and the extent of the lattices (La), an increase in the stack height (Lc) of semi-cokes. An increase of the degree of order (h/l), a decrease of d002 index testify about the justification of the carbon nets, the network lacing and improvement of the cross-linking processes in the coal carbonization products. These processes carry out more intensively in a sample treated by AAD.
These facts support the conclusion that the influence of chemical additives on the yield of semi-cokes and its structure is also related to a coal genetic type.
Table 4 shows the DRIFT results of studying of the original and oil-treated coals before and after heating up to different temperatures. As seen from the Table, the samples differ by relative intensities (areas) of the absorption bands of individual components, with the structures having cross C-O bonds retained in the oil-modified sample. Its semi-coke is distinguished for the greater ratio number of the reactive oxygen-containing groups to that of the aliphatic groups, the greater strength of intermolecular interactions and a more developed polyconjugation system.
Table 4 - Variations of the relative content of the functional groups during thermal treatment of original and oil-treated coals by DRIFT method
|
T (0C) |
I1700/I2920 |
SC-O/SC-C |
SCHàã/SC-C |
Original coal |
20 |
1,8957 |
0,2831 |
0,2150 |
350 |
2,0897 |
0,1389 |
0,2990 |
420 |
1,4824 |
0,1446 |
0,3080 |
450 |
3,5203 |
0,0952 |
0,3260 |
500 |
2,6122 |
0,0875 |
0,4430 |
20 |
1,5176 |
0,3026 |
0,2170 |
350 |
1,2259 |
0,2701 |
0,3470 |
Oil-treated coal |
420 |
0,9202 |
0,3020 |
0,5100 |
450 |
1,0043 |
0,3301 |
0,5520 |
500 |
3,6632 |
0,1573 |
0,3200 |
4. Conclusions
Hereby, the presence of organic additives results in a significant change in the semi-coking product's yield and structure. The results of this paper prove that the carbonization of the oil-and AAD-treated coals improve the cross-linking processes in coal carbon¬ization products. The dependence of the coal structure and reactivity on genetic type is fairly strong.
References
- D. Murchison, J. Pearson, The anomalous behaviour of properties of seams at the Plessey (M) horizon of the Northumberland and Durham coalfields, Fuel 79 (2000) 865.
- I.I. Ammosov, Geology of coal and oil deposits in the USSR, Gos. NTI literatury po geologii i okhranc ncdr, Moscow, 1963.
- L. Butuzova, G. Matsenko, S. Skirtochenko, L. Isajeva, O. Turchanina, V. Saranchuk, Relation between the petrographic and chemical properties of low-reduced and reduced coals of Donetsk basin, Proceedings of the 2000 Int. European Coal Conference, Polish Geological Institute, Sosnowiec, Poland, 2000, pp. 13-14..
- L.V. Pashchenko, V.I. Saranchuk, Low-temperature oxidation of tending and non-tending to self-ignition Ukraine coals of reduced and low-reduced types with atmospheric oxygen, in: J.A. Pajares, J.M.D. Tascon (Eds.), Coal Science, Proc. Eight Int. Conference Coal Science, Elsevier, Amsterdam, 1995, pp. 493-497.
- V.M. Bogdanova, Chemical Peculiarities and Genesis of Brown Coals of Kazakhstan, Nauka, Moscow, 1966.
- M.J. Iglesias, MJ. Cuesta, F. Laggoun-Defarge, I. Suarez-Ruiz, The influence of impregnation by hydro¬carbons on coal structure during its thermal evolution, J. Anal. Appl. Pyrolysis 58-59 (2001) 841.
- M.J. Iglesias, J.C. del Rio, F. Laggoun-Defarge, M.J. Cuesta, I. Suarez-Ruiz, Control of the chemical structure of perhydrous coals; FTIR and Py-GC/MS investigation, J. Anal. Appl. Pyrolysis 62 (2002) 1.
- G.P. Matsenko, Finely dispersed pyrite concretion as a petrographic parameter of types by reductivity of Donetsk coals, Khim. Tverd. Topi. 1 (1983) 13.
|