ДонНТУ >
Портал магистров ДонНТУ
Швец Мария Михайловна
Факультет экологии и химической технологии
Кафедра химической технологии топлива
Специальность: химической технологии топлива и углеродных материалов
Тема выпускной работы:
Исследование технологии утилизации жидкоподвижных отходов коксохимического производства
Научный руководитель профессор кафедры ХТТ, д.т.н., профессор Саранчук Виктор Иванович
Материалы по теме выпускной работы:
Об авторе | Библиотека | Ссылки |
Отчет о поиске | Индивидуальный раздел
Реферат по теме выпускной работы
Введение
Задача охраны природы от вредного влияния выбросов промышленного производства в настоящее время приобретает все большее значение. В связи с этим все чаще возникает необходимость создания так называемого безотходного производства, свободного от выбросов вредных веществ в атмосферу и водоемы
Создание подобного производства возможно как путем рационального использования существующих отходов, так и путем совершенствования технологии с целью сокращения их количества и коренного изменения технологии, предполагающего полное предотвращение образования отходов.
Отходы производства образуются в процессе получения основных продуктов коксования. Их количество и качество зависят, прежде всего, от применяемой технологии и условий производства. Существенное значение имеют и возможные нарушения технологического процесса, а также несовершенство применяемой аппаратуры, низкое качество сырья и недостаточная культура производства.
Рациональная утилизация отходов связана, прежде всего, с наиболее полным использованием их ценных свойств или содержащихся в них веществ. Поскольку отходы содержат значительные количества продуктов коксохимического производства, то одним из основных направлений их использования может быть возврат их в технологический процесс – путем добавления в шихту при коксовании. Это может быть как непосредственное добавление к шихте при загрузке в камеры коксования, так и изменение технологии подготовки шихты, например использование брикетов. При этом отходы коксохимического производства могут выступать в качестве связующего материала.
Цель работы – определить брикетирующую способность и механическую прочность брикетов полученных из каменного угля различных марок с жидкими отходами коксохимического производства.
Объект исследования – брикеты полученные из отдельных марок угля в смеси с жидкими отходами коксохимического производства.
Актуальность работы. При коксовании каменных углей образуется значительное количество отходов, которые до настоящего времени не находят своего эффективного применения. Среди отходов коксохимического производства выделяются жидкие отходы: фусы, кислая смолка, полимеры и др. Долгое время они накапливались в хранилищах, которые уже заполнены и не могут принять новые отходы или просто добавлялись в шихту без предварительной технологической подготовки. Кроме того, значительно изменилась сырьевая база коксования и замена коксующихся марок угля на слабоспекающие марки требует изменений в технологии подготовки шихты. Одним из выходов может быть использование частично брикетируемой шихты, что даст возможность увеличить количество слабоспекающихся марок угля при коксовании и утилизировать жидкоподвижные отходы производства.
Практическая ценность. Использование жидких отходов коксохимического производства в качестве связующих веществ позволит сократить количество отходов при коксовании каменных углей, дополнительно вводить в шихту низкоспекающиеся компоненты, за счет использования частично брикетируемой шихты и получать дополнительно количество продуктов за счет переработки отходов производства.
Методы исследования – стандартные методики определения состава угля, брикетирование, физические методы определения качества брикетов.
1 Характеристика отходов коксохимического производства
1.1 Фусы каменноугольные
Общее содержание в фусах твердой фазы (веществ, не растворимых в толуоле) составляет 40-50% на безводную массу, остальное представляет собой каменноугольную смолу. Влажность фусов колеблется в пределах 5-11%. Безводная масса фусов имеет плотность 1,29-1,35 г/см3; зольность колеблется в пределах 4-6%; содержание общей серы составляет 1,6-2,5%. В табл. 1 приведен фракционный состав фусов при дистилляции.
Выход твердого остатка 73,73%, зольность твердой фазы фусов 9-10%. В табл. 2 приведен ситовый состав твердой фазы.
Таблица 1 – Фракционный состав фусов при дистилляции
Показатели |
Интервал температур, °С |
170-270 |
270-300 |
300-360 |
Выход фракции, % |
6,53 |
4,10 |
9,5 |
Фенолы, % |
0,38 |
0,26 |
– |
Нафталин, % |
2,25 |
0,51 |
– |
Таблица 2 – Ситовый состав твердой фазы
Класс, мм |
>3 |
2-3 |
1-2 |
0,43-1 |
0,20-0,43 |
0,088-0,20 |
<0,088 |
Содержание, % |
11,1 |
2,58 |
4,34 |
4,58 |
5,60 |
44,7 |
27,1 |
Ситовый состав твердой фазы фусов непостоянен и может меняться в зависимости от интенсивности паро- или гидроинжекции на коксовых печах и других условий.
1.2 Кислая смолка сульфатного отделения
Кислая смолка, образующаяся в сатураторах сульфатного отделения, после отстоя маточного раствора до содержания его в смолке 2,7% имеет кислотность 1,3% и почти не растворяется в воде. Кислая смолка имеет следующий средний состав приведенный в табл. 3 [1]. В органической массе содержится 4-12% нафталина.
При нейтрализации кислой смолки аммиачной водой в производственных условиях была получена нейтральная смолка с характеристикой приведенной в табл. 4 [2].
Таблица 3 – Состав кислой смолки
Показатель |
Содержание, % |
Растворимые в толуоле |
50-70 |
Зола |
5-10 |
Железо |
2-3 |
Циан |
1-3 |
Сера |
2-12 |
Таблица 4 – Характеристика нейтральной кислой смолки
Показатель |
Содержание |
рН |
6,5-7 |
Плотность при 20 °С, г/см3 |
1,2 |
Вязкость, ед. Ву |
20 |
Содержание, %:
свободного углерода
сульфата аммония
нафталина
фенолов
воды
|
18,9
3,6
3,0
3,1
0,5
|
Фракционный состав, %, при отгоне до температуры, °С:
170
270
300
|
1,4
10,5
20,6
|
Температура размягчения, °С, остатка после отгона до 300 °С |
45 |
1.3 Полимеры бензольного отделения
Полимеры, получаемые при регенерации поглотительного масла в бензольных отделениях, являются высоко ароматизированным продуктом, содержащим небольшие количества инденкумароновых смол и высших фенолов. Их состав зависит от условий работы регенераторов и может довольно сильно различаться на отдельных заводах. Полимеры имеют следующую характеристику табл. 5 [3].
Таблица 5 – Характеристика полимеров
Показатель |
Содержание, % |
Плотность при 50 °С, г/см3 |
1,12-1,15 |
Зольность, % |
0,1-0,3 |
Содержание серы, %:
свободной
общей
|
0,1-0,2
2,0-3,0
|
Начало кипения (н.к.), °С |
124-230 |
Отгон до 160 °С, % |
1,0-5,0 |
Остаток выше 300 °С, % |
50-60 |
Не растворимые в толуоле, % |
1,2-2,5 |
2 Утилизация отходов коксохимического производства
Одним из наиболее простых путей ликвидации отходов коксохимического производства является передача их в угольную шихту, идущую на коксование. Для этого они должны быть соответствующим образом подготовлены и смешены, чтобы полученная масса удовлетворяла следующим общим требованиям:
а) состав смеси и ее свойства должны быть равномерными и, кроме того, достаточно постоянными и устойчивыми;
б) вязкость смеси должна обеспечивать возможность равномерной подачи в угольную шихту;
в) коксование отходов не должно влиять на сохранность коксовых печей;
г) в отходах должно быть минимальное содержание легкоиспаряющихся при обычной температуре веществ (бензола, тиофена, пиридина, сероуглерода и других) или газов (Н2S, SO2, HCN и других), ухудшающих санитарно-гигиенические условия работы;
д) смесь должна иметь рН=7-8;
е) зольность смеси не должна заметно влиять на зольность получаемого кокса;
ж) серусодержащие компоненты должны при коксовании разлагаться с преимущественным выделением серы в газ[4],[5].
3 Общие сведения о процессе брикетирования
Брикетирование углей представляет собой процесс механической переработки угольной мелочи в кусковое топливо – брикеты, имеющие определенную геометрическую форму, размеры и массу.
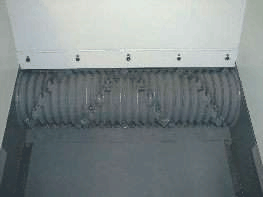
Рисунок 3.1 - Брикетное производство
Брикетированию подвергаются бурые угли, торф, отсевы каменных углей и антрацитов, коксовая и полукоксовая мелочь и другие углеродистые материалы. Брикетирование применяется также для окускования руд и рудных концентратов различного типа, комбикормов и других материалов.
Сущность брикетирования состоит в том, что измельченный до определенной крупности уголь или естественная угольная мелочь, подвергаются сушке и затем прессованию. Различают два способа брикетирования углей: без связующих веществ при повышенном давлении прессования (выше 80 МПа) и со связующим веществом при малом давлении прессования (15-25 МПа). По первому способу брикетируются молодые (мягкие) бурые угли и торф, по второму способу – мелочь каменных и старых (твердых) бурых углей, антрацитов и штыб, полукоксовая и коксовая мелочь.
Требования, предъявляемые к брикетам:
а) угольные брикеты должны иметь необходимую прочность и выдерживать механические нагрузки различного типа;
б) брикеты, которые применяются как энергетическое топливо и после изготовления транспортируются или продолжительное время хранятся на топливных складах, или у потребителя, кроме механической прочности, должны обладать еще определенной влагостойкостью и не изменять свою прочность под влиянием атмосферных условий;
в) угольные брикеты должны обладать термической стойкостью, то есть сохранять необходимую прочность и кусковую форму в топке при горении;
г) брикеты, изготовляемые со связующим веществом, не должны слипаться в вагоне и при длительном хранении в штабеле под открытым небом.
Образование брикетов со связующим происходит в результате сцепления частиц со связующим веществом. Процесс брикетирования состоит из трех стадий:
– адсорбция связующего вещества брикетируемым материалом и образования на поверхности частиц тонкой пленки связующего;
– прессования шихты;
– затвердевание брикета при охлаждении.
Прочность брикета зависит от силы сцепления пленки связующего после затвердевания с поверхностью материала (силы адгезии или прилипания) и прочности самой пленки (силы когезии)[6].
Прочность сцепления частиц зависит от свойств связующего и брикетируемого материала, его крупности, гранулометрического состава, влажности, давления прессования, расхода связующего и равномерности распределения его в массе шихты, а также температуры нагрева шихты.
С уменьшением крупности частиц прочность сцепления их в брикете возрастает. Крупность и гранулометрический состав шихты определяет величину поверхности, которая должна быть покрыта связующим. Чем мельче размер зерен угля, тем больше требуется связующего для брикетирования. Если брикетируются крупные зерна, то укладка их получается неплотной. Вследствие этого при прессовании происходит разрушение зерен и образование новых поверхностей, непокрытых связующим. Наличие этих поверхностей вызывает снижение прочности брикетов. Поэтому для получения необходима определенная крупность угольных зерен, обеспечивающая достаточно плотную укладку и наименьшую величину суммарной поверхности зерен. исходя из этого, крупность угля не должна превышать 6-8 мм, содержания в нем тонкой пыли (0-0,5 мм) является крайне нежелательным, а содержание угля класса 0,5-1 мм должно составлять примерно 40-45% [7].
Расход связующих веществ зависит от крупности угля и его гранулометрического состава, а также от зольности угля. При высокой зольности расход связующих как правило, повышается.
Давление прессования должно быть достаточным для уплотнения шихты и сближения угольных зерен на расстояния, при которых проявляется эффективное действие связующего. При малом давлении брикеты получаются рыхлыми и имеют пониженную прочность. Высокое давление приводит к сцеплению брикетов со стенками пресс-формы, в результате чего после снятия давления они не выходят из пресса.
При избытке в угле влаги затрудняется прилипание связующего к поверхности частиц и прочность брикетов снижается. Однако при очень сухом угле смачиваемость поверхности частиц связующим ухудшается и расход его увеличивается. Оптимальная влажность соответствующая наименьшему расходу связующего, определяется опытным путем, и составляет 3-5%[8].
Температура нагрева шихты зависит от температуры плавления связующего. Она должна быть несколько выше ее, чтобы связующее при нагревании перешло в жидкое состояние. В этом случае обеспечивается тщательное перемешивание связующего с углем и равномерное распределение его в шихте. Слишком высокая температура нагрева шихты вызывает ее пережег и потерю связующих свойств. Оптимальная температура нагрева шихты при пропарке должна быть на 20-30° выше температуры плавления связующего.
Связующее вещество для брикетирования должно удовлетворять следующим требованиям:
– иметь хорошие спекающиеся свойства и предавать брикетам необходимую термическую устойчивость;
– обладать хорошей связующей способностью и предавать брикетам достаточную прочность при его небольшом расходе;
– быть устойчивым к влаге;
– быстро затвердевать и предавать брикетам устойчивость в летнее время года;
– быть безвредным как при производстве брикетов, так и при их использовании;
– быть недорогим и не усложнять процесс брикетирования;
– не увеличивать содержания балласта в топливе и не понижать его теплоту сгорания;
– быть доступным и применяться при малом расходе[9].
Каменные угли при прессовании мало поглощают энергии уплотнения и пластических деформаций. Они накапливают энергию в потенциальной форме вследствие упругих деформаций и отдают ее по мере снятия давления и происходящего при этом упругого расширения. В связи с этим каменные угли могут брикетироваться лишь с применением связующих веществ или при тонком помоле, высоком нагреве и высоком давлении прессования [7].
4 Экспериментальная часть работы
Для проведения исследований были отобраны пробы угля марок „К”, „Г”, „СС”, заводской шихты на Макеевском коксохимическом заводе. Характеристика марок угля приведена в табл. 4.1. Также были отобраны пробы отходов производства: фусы, кислая смолка сульфатного отделения, полимеры бензольного отделения, отходы нафталинового отстойника. Отходы коксохимического производства использовались в качестве связующего материала при приготовлении брикетов, как индивидуально, так и в смеси.
Таблица 4.1 – Характеристика угля
Марка угля |
Wr |
Ad |
Sd |
Vd |
Vdaf |
Помол |
---|
+6 |
6-3 |
3-0
|
Шихта |
9,9 |
7,8 |
1,34 |
31,2 |
33,8 |
21,3 |
17,6 |
61,1 |
Г |
9,9 |
7,5 |
1,45 |
34,4 |
37,2 |
- |
- |
- |
СС |
12,1 |
6,4 |
0,44 |
24,3 |
25,9 |
- |
- |
- |
К |
8,2 |
7,9 |
0,75 |
27,1 |
29,5 |
- |
- |
- |
Для исследования использовалась фракция угля 0-3 мм, как рабочей влажности, так и аналитической. Количество связующего, которое добавлялось к углю составляло 10-15%. Это количество является наиболее целесообразным для брикетирования и было получено опытным путем многими исследователями [19] и нашло подтверждения также в наших опытах. При меньшем количестве брикеты получаются очень непрочными и рассыпаются еще на стадии выдавливании из пресса. Повышенные содержания связующего (более 15%) приводят к залипанию матрицы для прессования и брикеты получаются пересыщенные связующим и также непрочными.
Предварительно взвешенное связующее (фусы, кислая смолка), подогревалось на водяной бане до его размягчения, после чего добавлялась навеска угля и тщательно перемешивалась до однородной массы (чтобы не было сгустков связующего). При этом уголь также прогревался, что способствовало лучшему распределению связующего в навеске. Отходы нафталина перемешивались в холодном состоянии, поскольку по своему агрегатному состоянию они твердые и довольно неплохо усредняются с углем. Полимеры при комнатной температуре жидкие, поэтому их прогрев был ниже. Нагрев смеси угля со связующим осуществлялся примерно до температуры 50 °С внутри смеси, что контролировалось ртутным термометром. После этого смеси давали остыть до комнатной температуры.
Брикетирование угля проводили на ручном механическом прессе, Давление прессования контролировали с помощью динамометра. Интервал давления соответствовал 300-1000 атм. Нижний интервал примерно соответствует давлению в заводских условиях которое создается на экструдере и более низкое давление прессования ведет к получению непрочных брикетов или к перерасходу связующего. Верхний предел обусловлен техническими возможностями ручного пресса с одной стороны, с другой увеличения давления не приводит к улучшению качества брикетов и его использование в промышленных условиях приведет к большому перерасходу электрической энергии и соответственно увеличению себестоимости продукции. Размеры полученных брикетов соответственно равны: диаметр 16,3 мм, длина от 24 до 31 мм (в зависимости от приложенного давления и количества загрузки матрицы прессования). Масса брикетов колебалась в пределах 6-7,5 г. Были исследованы на брикетирующую способность как отдельные марки угля, так и их смесь; то же касается и связующих компонентов.
Прочность брикетов определяли на этом же прессе путем определения усилия, которое выдерживает брикет на раздавливания в горизонтальном и вертикальном положении. Сжимающего усилия брикетов определяли как свежеприготовленных, так и выдержанных определенное время.
Для исследования были отобраны брикеты полученные в заводских условиях. Они имеют цилиндрическую форму, диаметром 30 мм и длиной около 150 мм. Также были отобраны образцы шихты со связующим из которой не получились брикеты. Брикетирование на производстве осуществляют с помощью экструдера. Принципиальная схема экструдера приведена на рис. 4.1
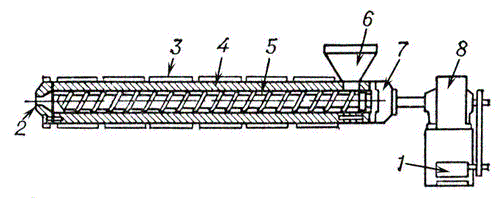
1 – двигатель привода; 2 – формующее устройство; 3 – нагревательный элемент; 4 – гильза; 5 – шнек; 6 – загрузочный бункер; 7 – упорный подшипник; 8 – редуктор
Рисунок 4.1 - Экструдер
Захватывая исходный материал (гранулы, порошок, ленту и др.) из загрузочного устройства, шнек перемещает его вдоль корпуса. При этом материал сжимается (давление в экструдере достигает 15-50 Мн/м2 (150-500 кгс/см2), разогревается, пластицируется и гомогенизируется. По такому же принципу экструдеры работают с углем и связующим. Рассчитать давление сжатия в экструдере, которому подвергается уголь – вызывает сложности. Поэтому давление прессования было оценено приблизительно по плотности получаемых брикетов. Плотность заводских брикетов составила 1,17 г/см3, что соответствует примерно давлению 300-400 атм. На механическую прочность были взяты брикеты длиной около 5-7 см. Их прочность составила 500-700 ус. единиц.
Анализируя шихту со связующим из которой не получились заводские брикеты следует отметить, что в ней довольно большое количество довольно крупных (видимых) включений связующего. Это говорит о плохом смешении связующего с шихтой. Поскольку в заводских условиях используется непосредственно смесь всех отходов, консистенция этого связующего для лучшего взаимодействия с шихтой предполагает его подогрев, чего не предусмотрено в настоящей технологии брикетирования. Поэтому данная шихта была исследована в лабораторных условиях. Она брикетировалась непосредственно в холодном состоянии, с небольшим подогревом и перемешиванием и с тщательным перемешиванием при подогреве до полного исчезновения видимых включений частиц связующего. Полученные смеси подверглись брикетированию и были испытаны на прочность. Зависимость плотности от приложенного давления приведена на рис. 4.2
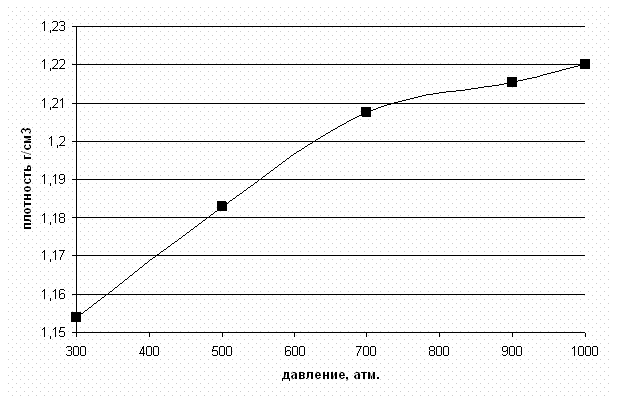
Рисунок 4.2 – Изменение плотности брикетов от давления прессования
При малых давлениях прессования плотность меняется линейно пропорционально завися от давления, при давлении выше 700 атм. эти изменения замедляются. Частицы угля сближаются очень близко между собой и возникают в брикете напряжения, которые препятствуют значительному увеличению плотности. Дальнейшее увеличение давления (>1000 атм) к изменению плотности практически не приводит, постепенно приближаясь к плотности угля в монолите – около 1,29 г/см3.
Образцы брикетов подвергнутые испытанию сразу после приготовления и после выдержки в течение суток отличаются по прочности на 5-17%. В процессе выдержки образцов происходит, по-видимому, их полимеризация, частичное испарение влаги и схватывание брикета, что делает его более прочным. Для брикетов полученных из свежеприготовленной шихты и связующего это упрочнение составляет до 45% в зависимости от связующего и марки угля.
Брикеты, которые были получены при тщательном перемешивании при нагревании оказались самыми прочными. Это упрочнение составило около 30% (табл. 4.2). Из этого можно сделать выводы, что существующая технология брикетирования в заводских условиях нуждается в корректировки. То есть введении дополнительного прогрева шихты и аппарата ее смешения со связующим.
Таблица 4.2 – Характеристика брикетов полученных из остатков заводской шихты со связующим
Условия брикетирования |
Прочность брикетов при давлении, ус. дел. |
300 |
500 |
700 |
900 |
1000 |
брикетирование холодной шихты |
248 |
298 |
337 |
310 |
377 |
прогрев шихты до 40 °С |
260 |
393 |
445 |
475 |
445 |
прогрев шихты с тщательным перемешиванием |
295 |
435 |
470 |
490 |
460 |
В некоторых опытах наблюдается уменьшение прочности брикетов полученных при 1000 атм. по сравнению с 900 атм., при этом плотность брикетов практически не меняется. Это может быть связано с тем, что при данном добавлении связующего частицы угля сближены довольно близко друг с другом и дальнейшее увеличение давления приводит только к увеличению напряжения внутри брикета и раздавливанию частиц угля.
Анализируя смесь, которая получена в заводских условиях следует отметить, что из нее можно получить довольно прочные брикеты, только необходимо большее ее усреднение.
Полученные брикеты планируется использовать для коксования в коксовых печах. Это позволит получить целый ряд преимуществ. Происходит утилизация отходов коксохимического производства, которые в данное время продаются практически за бесценок (что тоже неплохо, если нет других вариантов использования, поскольку за отходы и их утилизацию нужно платить). Их использование в виде брикетов, а не простого смешения с шихтой путем полива на конвейерной ленте уберет загрязнение конвейерных лент, бункеров, коксовой печи. Поскольку в виде брикетов связующие не производят загрязнения всех перечисленных элементов. И кроме того кокс получается однородным в виду тщательного перемешивания и однородности полученной смеси. Брикетирование позволяет без ухудшения качества кокса вводить угли неспекающихся марок, более низкого качества, ввиду увеличения плотности загрузки. Отходы в конечном итоге дают прирост кокса и их использование окупается с расходами на их утилизацию.
Заключение
Значительные количества отходов коксохимического производства, требуют рационального подхода к их использованию. Одним из основных направлений их использования – может быть добавление их шихту. Фусы, кислая смолка, полимеры, как показали исследования являются неплохим связующим материалом и могут быть использованы для брикетирования угля. При этом брикеты обладают достаточной прочностью, которая обеспечивает возможность их доставки в камеру коксования.
В работе рассмотрены характеристики отходов производства и существующие способы их утилизации, теоретические основы процесса брикетирования угля со связующим материалом и методы испытания полученных брикетов.
Приведены результаты исследования по образцам заводской шихты со связующим материалом и даны рекомендации по улучшению процесса брикетирования. Основная причина получения брикетов плохого качества – это недостаточное усреднение угля со связующим материалом. Хорошее усреднение не может быть достигнуто при обычной температуре и смешением только в экструдере. По этому необходим дополнительный подогрев шихты и связующего и аппарат смеситель.
Литература
- Лебедева Г.Н. – Современные схемы и технические решения при проектировании коксохимических предприятий. М., Металургиздат. 1963 (Гипрококс, Вып, 29), С. 49-63.
- Соркин М. М., Войтковская Е. А., Боярская Р. Р. – Кокс и химия, 1971, №1, С. 51-54.
- Вопросы улавливания и переработки продуктов коксования. Сб. №4. М., Металургия, 1975.
- Юкельсон И. И., Федотова Л. В., Легачева В. В., и др . - Кокс и химия, 1968, 6, С. 39-41.
- Коляндр Л. Я., Андреева В. С., Дивиденко И. Д., и др . - Кокс и химия, 1969, № 9, С. 34-37.
- Смоляков Э. В., Златин Л. Е., Штейн А. Л., - Кокс и химия, 1972, № 6, С. 46-48.
- Ремесников И.Д. Брикетирование угля. – М.: Углетехиздат, 1957. – 240 с.
- Десенко С. Г.Информация ин-та «Черметинформация», сер. 10, инф. №6, 1971. 15 с.
- Лазорин С. Н., Папков Г. И., Литвиненко В. И., - Обезвреживание отходов коксохимических заводов. М., Металургиздат, 1977. 238с.
- Паршин В. Д. - Кокс и химия, 1962, №12, С. 37-39.
- Тютюнников Ю. Б., Синцерова Л. Г., Гречко Ю. И. и др.- Органичні добавкиу виробництві коксу. Київ, Техніка, 1971, 94с.
- Кроль В. Л., Дорогобид Г. М., Праздникова В. А. – Кокс и химия, 1961, № 9, С. 12-16.
- Швед В. Г. – Кокс и химия, 1971, № 2, С. 33-39.
- Макаров Г. Н.- Производство кокса в кольцевых печах. М., Металургия, 1973. 320с.
- Глазунов А. А. – Кокс и химия, 1971, № 6, С. 47-50.
- Белоножко А. М. – Кокс и химия, 1971, № 9, С. 47-49.
- Войтковская Е. А., Касьян В. В., Кучер А. Г. и др – Кокс и химия, 1975, № 12, С. 41-42.
- Белоножко А.М. Кокс и химия, 1971, №9, С. 47-49.
- Юкельсон И.И., Федотова Л.В., Легачова В.В. и др. Кокс и химия, 1968, №6, С. 39-41.
- Крохин В.Н. Брикетирование углей. – М.: Недра, 1984, 224 с.
©
ДонНТУ Швец М.М. 2009
ДонНТУ >
Портал магистров ДонНТУ ||
Об авторе | Библиотека | Ссылки |
Отчет о поиске | | Индивидуальный раздел
|