ДонНТУ>
Портал магістрів ДонНТУ
Швець Марія Михайлівна
Факультет экологии и химической технологии
Кафедра химической технологии топлива
Специальность: химической технологии топлива и углеродных материалов
Тема выпускной работы:
Исследование технологии утилизации жидкоподвижных отходов коксохимического производства
Научный руководитель профессор кафедры ХТТ, д.т.н., профессор Саранчук Виктор Иванович
Матеріали до теми випускної роботи:
Про автора
Реферат з теми випускної роботи
Вступ
Завдання охорони природи від шкідливого впливу викидів промислового виробництва на даний час набуває все більшого значення. У зв'язку з цим все частіше виникає необхідність створення так званого безвідходного виробництва, вільного від викидів шкідливих речовин в атмосферу і водоймища.
Створення подібного виробництва можливе як шляхом раціонального використання існуючих відходів, так і шляхом вдосконалення технології з метою скорочення їх кількості і корінної зміни технології, що припускає повне запобігання утворенню відходів.
Відходи виробництва утворюються в процесі отримання основних продуктів коксування. Їх кількість і якість залежать, перш за все, від вживаної технології і умов виробництва. Істотне значення мають і можливі порушення технологічного процесу, а також недосконалість вживаної апаратури, низька якість сировини і недостатня культура виробництва.
Раціональна утилізація відходів зв'язана, перш за все, з якнайповнішим використанням їх цінних властивостей або речовин, що містяться в них. Оскільки відходи містять значні кількості продуктів коксохімічного виробництва, то одним з основних напрямів їх використання може бути повернення їх в технологічний процес – шляхом додавання в шихту при коксуванні. Це може бути як безпосереднє додавання до шихти при завантаженні в камери коксування, так і зміна технології підготовки шихти, наприклад використання брикетів. При цьому відходи коксохімічного виробництва можуть виступати як матеріал, що пов'язує.
Мета роботи – визначити брикетуючу здатність і механічну міцність брикетів отриманих з кам'яного вугілля різних марок з рідкими відходами коксохімічного виробництва.
Об'єкт дослідження – брикети отримані з окремих марок вугілля в суміші з рідкими відходами коксохімічного виробництва.
Актуальність роботи. При коксуванні кам'яного вугілля утворюється значна кількість відходів, які до теперішнього часу не знаходять свого ефективного застосування. Серед відходів коксохімічного виробництва виділяються рідкі відходи: фуси, кисла смолка, полімери і ін. Довгий час вони накопичувалися в сховищах, які вже заповнені і не можуть прийняти нові відходи або просто додавалися в шихту без попередньої технологічної підготовки. Крім того, значно змінилася сировинна база коксування і заміна марок вугілля, що коксувалися, на слабоспікливі марки вимагає змін в технології підготовки шихти. Одним з виходів може бути використання шихти, що частково брикетується, що дасть можливість збільшити кількість слабоспікливих марок вугілля при коксуванні і утилізувати рідкорухомих відходи виробництва.
 Практична цінність. Використання рідких відходів коксохімічного виробництва як речовини, що пов'язують, дозволить скоротити кількість відходів при коксуванні кам'яного вугілля, додатково вводити в шихту малоспікливі компоненти, за рахунок використання шихти, що частково брикетується, і отримувати додаткова кількість продуктів за рахунок переробки відходів виробництва.
 Методи дослідження – стандартні методики визначення складу вугілля, брикетування, фізичні методи визначення якості брикетів.
1 Характеристика відходів коксохімічного виробництва
1.1 Фуси кам'яновугільні
Загальний зміст у фусах твердої фази (речовин, не розчинних в толуолі) складає 40-50% на безводну масу, інше є кам'яновугільною смолою. Вологість фусів коливається в межах 5-11%. Безводна маса фусів має щільність 1,29-1,35 г/см3; зольність коливається в межах 4-6%; зміст загальної сірки складає 1,6-2,5%. У табл. 1 приведений фракційний склад фусів при дистиляції.
Таблиця 1 – Фракційний склад фусів при дистиляції
Показники |
Інтервал температур, °С |
170-270 |
270-300 |
300-360 |
Вихід фракції, % |
6,53 |
4,10 |
9,5 |
Феноли, % |
0,38 |
0,26 |
– |
Нафталін, % |
2,25 |
0,51 |
– |
Таблиця 2 – Ситовий склад твердої фази
Клас, мм |
>3 |
2-3 |
1-2 |
0,43-1 |
0,20-0,43 |
0,088-0,20 |
<0,088 |
Вміст, % |
11,1 |
2,58 |
4,34 |
4,58 |
5,60 |
44,7 |
27,1 |
Ситовий склад твердої фази фусів непостійний і може мінятися залежно від інтенсивності паро- або гидроїнжекциі на коксових печах і інших умов.
1.2 Кисла смолка сульфатного вітділення
Кисла смолка, що утворюється в сатураторах сульфатного відділення, після відстою маткового розчину до вмісту його в смолінні 2,7% має кислотність 1,3% і майже не розчиняється у воді. Кисла смолка має наступний середній склад приведений в табл. 3 [1]. У органічній масі міститься 4-12% нафталіну.
При нейтралізації кислої смолки аміачною водою у виробничих умовах було отримано нейтральна смолка з характеристикою приведеною в табл. 4 [2].
Таблиця 3 – Склад кислої смолки
Показники |
Вміст, % |
Розчинні у толуолі |
50-70 |
Зола |
5-10 |
Залізо |
2-3 |
Циан |
1-3 |
Сірка |
2-12 |
Таблиця 4 – Характеристика нейтральної кислої смолки
Показники |
Вміст |
рН |
6,5-7 |
Щільність при 20 °С, г/см3 |
1,2 |
В'язкість, ед. Ву |
20 |
Вміст, %:
вільного вуглецю
сульфату аммонию
нафталину
фенолів
води
|
18,9
3,6
3,0
3,1
0,5
|
Фракційний склад, %, при відгоні до температури, °С:
170
270
300
|
1,4
10,5
20,6
|
Температура размэякшення, °С, залишка пысля выдгона до 300 °С |
45 |
1.3 Полімери бензолового відділення
Полімери, що отримують при регенерації поглинального масла в бензолових відділеннях, є високо ароматизованим продуктом, що містить невеликі кількості інденкумаронових смол і вищих фенолів. Їх склад залежить від умов роботи регенераторів і може досить сильно розрізнятися на окремих заводах. Полімери мають наступну характеристику табл. 5 [3].
Таблиця 5 – Характеристика полімерів
Показники |
Вмыст, % |
Щільність при 50 °С, г/см3 |
1,12-1,15 |
Зольність, % |
0,1-0,3 |
Вміст сірки, %:
вільної
загальної
|
0,1-0,2
2,0-3,0
|
Початок кипіння(п.к.), °С |
124-230 |
Відгон до 160 °С, % |
1,0-5,0 |
Залишок вишче 300 °С, % |
50-60 |
Не розчинні у толуолі, % |
1,2-2,5 |
2 Утилізація відходів коксохімічного виробництва
Одним з найбільш простих шляхів ліквідації відходів коксохімічного виробництва є передача їх у вугільну шихту, що йде на коксування. Для цього вони повинні бути відповідним чином підготовлені і змішані, щоб отримана маса задовольняла наступним загальним вимогам:
а) склад суміші і її властивості повинні бути рівномірними і, крім того, достатньо постійними і стійкими;
б) в'язкість суміші повинна забезпечувати можливість рівномірної подачі у вугільну шихту;
в) коксування відходів не повинне впливати на збереження коксових печей;
г) у відходах повинен бути мінімальний вміст легковипаровуваних при звичайній температурі речовин (бензолу, тіофена, піридину, сірковуглеця і інших) або газів (Н2S, SO2, HCN і інших), що погіршують санітарно-гігієнічні умови роботи;
д) суміш повинна мати рН=7-8;
е) зольність суміші не повинна помітно впливати на зольність отримуваного коксу;
ж) сірковмісні компоненти повинні при коксуванні розкладатися з переважним виділенням сірі в газ.
3 Загальних відомості про процес брикетування
Брикетування вугілля є процес механічної переробки вугільного дріб’язку в кускове паливо – брикети, що мають певну геометричну форму, розміри і масу.
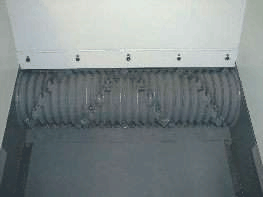
Рисунок 3.1 - Брикетне виробництво
Брикетуванню піддаються буре вугілля, торф, відсів кам'яного вугілля і антрацитів, коксовий і напівкоксовий дріб’язок і інші вуглецеві матеріали. Брикетування застосовується також для згрудкування руди і рудних концентратів різного типу, комбікормів та інших матеріалів.
Суть брикетування полягає в тому, що подрібнене до певної великої вугілля або природна вугільна дрібниця, піддаються сушці і потім пресуванню. Розрізняють два способи брикетування вугілля: без речовин, що пов'язують, при підвищеному тиску пресування (вище 80 МПа) і з речовиною, що пов'язує, при малому тиску пресування (15-25 МПа). За першим способом брикетуються молоде (м'які) буре вугілля і торф, за другим способом – дрібниця кам'яного і старого (твердих) бурого вугілля, антрацитів і штиб, напівкоксовий і коксовий дрібязок.
Вимоги, що пред'являються до брикетів:
а) вугільні брикети повинні мати необхідну міцність і витримувати механічні навантаження різного типу;
б) брикети, які застосовуються як енергетичне паливо і після виготовлення транспортуються або тривалий час зберігаються на паливних складах, або у споживача, окрім механічної міцності, повинні володіти ще певною вологостійкістю і не змінювати свою міцність під впливом атмосферних умов;
в) вугільні брикети повинні володіти термічною стійкістю, тобто зберігати необхідну міцність і кускову форму в топці при горінні;
г) брикети, що виготовляються з речовиною, що пов'язує, не повинні злипатися у вагоні і при тривалому зберіганні в штабелі просто неба.
Утворення брикетів відбувається в результаті зчеплення частинок з речовиною, що пов'язує. Процес брикетування складається з трьох стадій:
– адсорбція речовини, що пов'язує, матеріалом, що брикетується, і освіти на поверхні частинок тонкої плівки того, що пов'язує;
– пресування шихти;
– твердіння брикету при охолоджуванні.
Міцність брикету залежить від сили зчеплення плівки що пов'язує після твердіння з поверхнею матеріалу (сили адгезії або прилипання) і міцності самої плівки (сили когезії)[6].
Міцність зчеплення частинок залежить від властивостей матеріалу, що пов'язує і брикетується, його великої, гранулометричного складу, вологості, тиску пресування, витрати того, що пов'язує і рівномірності розподілу його в масі шихти, а також температури нагріву шихти.
Із зменшенням великої частинок міцність зчеплення їх в брикеті зростає. Велика і гранулометричний склад шихти визначає величину поверхні, яка повинна бути покрита таким, що пов'язує. Чим дрібніше розмір зерен вугілля, тим більше потрібний що пов'язує для брикетування. Якщо брикетуються крупні зерна, то укладання їх виходить нещільною. Внаслідок цього при пресуванні відбувається руйнування зерен і утворення нових поверхонь, непокритих що пов'язує. Наявність цих поверхонь викликає зниження міцності брикетів. Тому для отримання необхідна певна велика вугільних зерен, що забезпечує достатньо щільне укладання і найменшу величину сумарної поверхні зерен. виходячи з цього, велика вугілля не повинна перевищувати 6-8 мм, вмісту в нім тонкого пилу (0-0,5 мм) є украй небажаним, а зміст вугілля класу 0,5-1 мм повинен складати приблизно 40-45%[7].
Витрата речовин, що пов'язують, залежить від великої вугілля і його гранулометричного складу, а також від зольності вугілля. При високій зольності витрата тих, що пов'язують як правило, підвищується.
Тиск пресування повинен бути достатнім для ущільнення шихти і зближення вугільних зерен на відстані, при яких виявляється ефективна дія того, що пов'язує. При малому тиску брикети виходять рихлими і мають знижену міцність. Високий тиск приводить до зчеплення брикетів із стінками прес-форми, внаслідок чого після зняття тиску вони не виходять з преса.
При надлишку у вугіллі вологи ускладнюється прилипання сполучної речовини до поверхні частинок і міцність брикетів знижується. Проте при дуже сухому вугіллі змочуваність поверхні частинок сполучною речовиною погіршується і витрата його збільшується. Оптимальна вологість відповідна найменшій витраті що пов'язує, визначається досвідченим шляхом, і складає 3-5%.[8].
Температура нагріву шихти залежить від температури плавлення того, що пов'язує. Вона повинна бути декілька вище за неї, щоб що пов'язує при нагріванні перейшло в рідкий стан. В цьому випадку забезпечується ретельне перемішування що пов'язує з вугіллям і рівномірний розподіл його в шихті. Дуже висока температура нагріву шихти викликає її перепалив і втрату властивостей, що пов'язували. Оптимальна температура нагріву шихти при пропарюванні повинна бути на 20-30° вище за температуру плавлення того, що пов'язує.
Речовина, що пов'язує, для брикетування повинна задовольняти наступним вимогам:
– мати хороші спікливі властивості і зраджувати брикетам необхідну термічну стійкість;
– володіти хорошою здатністю, що пов'язує, і зраджувати брикетам достатню міцність при його невеликій витраті;
– бути стійким до вологи;
– швидко тверднути і зраджувати брикетам стійкість в літню пору року;
– бути нешкідливим як при виробництві брикетів, так і при їх використанні;
– бути недорогим і не ускладнювати процес брикетування;
– не збільшувати вмісту баласту в паливі і не знижувати його теплоту згорання;
– бути доступним і застосовуватися при малій витраті[9].
Кам'яне вугілля при пресуванні мало поглинає енергії ущільнення і пластичних деформацій. Вони накопичують енергію в потенційній формі унаслідок пружних деформацій і віддають її у міру зняття тиску і пружного розширення, що відбувається при цьому. У зв'язку з цим кам'яне вугілля може брикетуватися лише із застосуванням речовин, що пов'язують, або при тонкому помелі, високому нагріві і високому тиску пресування [7].
4 Експериментальна частина роботи
Для проведення досліджень були відібрані проби вугілля мазкий „К”, „Г”, „СС”, заводської шихти на Макіївському коксохімічному заводі. Характеристика марок вугілля приведена в табл. 4.1. Також були відібрані проби відходів виробництва: фуси, кисла смолка сульфатного відділення, полімери бензолового відділення, відходи нафталінового відстійника. Відходи коксохімічного виробництва використовувалися як матеріал, що пов'язував, при приготуванні брикетів, як індивідуально, так і в суміші.
Таблиця 4.1 – Характеристика вугілля
Марка вугілля |
Wr |
Ad |
Sd |
Vd |
Vdaf |
Помел |
---|
+6 |
6-3 |
3-0
|
Шихта |
9,9 |
7,8 |
1,34 |
31,2 |
33,8 |
21,3 |
17,6 |
61,1 |
Г |
9,9 |
7,5 |
1,45 |
34,4 |
37,2 |
- |
- |
- |
СС |
12,1 |
6,4 |
0,44 |
24,3 |
25,9 |
- |
- |
- |
К |
8,2 |
7,9 |
0,75 |
27,1 |
29,5 |
- |
- |
- |
Для дослідження використовувалася фракція вугілля 0-3 мм, як робочій вологості, так і аналітичною. Кількість що пов'язує, яке додавалося до вугілля складало 10-15%. Ця кількість є найбільш доцільною для брикетування і було отримано досвідченим шляхом багатьма дослідниками [19] і знайшло підтвердження також в наших дослідах. При меншій кількості брикети виходять дуже неміцними і розсипаються ще на стадії витискуванні з преса. Підвищений вміст що пов'язує (більше 15%) приводять до злипання матриці для пресування і брикети виходять пересичені що пов'язує і також неміцними.
Заздалегідь зважена сполучна речовина (фуси, кисла смолка), підігрівалося на водяній лазні до його розм'якшення, після чого додавалося навішування вугілля і ретельно перемішувалася до однорідної маси (щоб не було згустків того, що пов'язує). При цьому вугілля також прогрівалося, що сприяло кращому розподілу що пов'язує в навішуванні. Відходи нафталіну перемішувалися в холодному стані, оскільки по своєму агрегатному стану вони тверді і досить непогано усереднюються з вугіллям. Полімери при кімнатній температурі рідкі, тому їх прогрів був нижчий. Нагріваючи суміші вугілля з тим, що пов'язує здійснювався приблизно до температури 50 °С всередині змішай, що контролювалося ртутним термометром. Після цього суміші давали остигнути до кімнатної температури.
Брикетування вугілля проводили на ручному механічному пресі, Тиск пресування контролювали за допомогою динамометра. Інтервал тиску відповідав 300-1000 атм. Нижній інтервал приблизно відповідає тиску в заводських умовах яке створюється на екструдері і нижчий тиск пресування веде до отримання неміцних брикетів або до перевитрати того, що пов'язує. Верхня межа обумовлена технічними можливостями ручного преса з одного боку, з іншою збільшення тиску не приводить до поліпшення якості брикетів і його використання в промислових умовах приведе до великої перевитрати електричної енергії і відповідно збільшенню собівартості продукції. Розміри отриманих брикетів відповідно рівні: діаметр 16,3 мм, довжина від 24 до 31 мм (залежно від прикладеного тиску і кількості завантаження матриці пресування). Маса брикетів коливалася в межах 6-7,5 р. Були досліджені на брикетуючу здатність як окремі марки вугілля, так і їх суміш; то ж стосується і компонентів, що пов'язують.
Міцність брикетів визначали на цьому ж пресі шляхом визначення зусилля, яке витримує брикет на роздавлювання в горизонтальному і вертикальному положенні. Стискаючого зусилля брикетів визначали як свіжовиготовлених, так і витриманих певний час.
Для дослідження були відібрані брикети отримані в заводських умовах. Вони мають циліндрову форму, діаметром 30 мм і завдовжки близько 150 мм. Також були відібрані зразки шихти з тим, що пов'язує з якої не вийшли брикети. Брикетування на виробництві здійснюють за допомогою екструдера. Принципова схема екструдера приведена на мал. 4.1
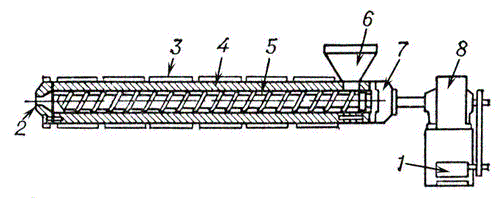
1 – двигун приводу; 2 – формуючий пристрій; 3 – нагрівальний елемент; 4 – гільза; 5 – шнек; 6 – завантажувальний бункер; 7 – наполегливий підшипник; 8 – редуктор
Рисунок 4.1 - Екструдер
Захоплюючи початковий матеріал (гранули, порошок, стрічку і ін.) із завантажувального пристрою, шнек переміщає його уздовж корпусу. При цьому матеріал стискається (тиск в екструдері досягає 15-50 Мн/м2 (150-500 кгс/см2), розігрівається, пластицируєтся і гомогенізується. За таким же принципом екструдери працюють з вугіллям і що пов'язує. Розрахувати тиск стиснення в екструдері, якому піддається вугілля, – викликає складнощі. Тому тиск пресування був оцінений приблизно по щільності отримуваних брикетів. Щільність заводських брикетів склала 1,17 г/см3, що відповідає приблизно тиску 300-400 атм. На механічну міцність були узяті брикети завдовжки близько 5-7 див. Їх міцність склала 500-700 вус. одиниць.
Аналізуючи шихту з тим, що пов'язує з якої не вийшли заводські брикети слід зазначити, що в ній досить велика кількість досить крупних (видимих) включень того, що пов'язує. Це говорить про погане змішення що пов'язує з шихтою. Оскільки в заводських умовах використовується безпосередньо суміш всіх відходів, консистенція що цього пов'язує для кращої взаємодії з шихтою припускає його підігрів, чого не передбачено в справжній технології брикетування. Тому дана шихта була досліджена в лабораторних умовах. Вона брикетувалася безпосередньо в холодному стані, з невеликим підігрівом і перемішуванням і з ретельним перемішуванням при підігріві до повного зникнення видимих включень частинок того, що пов'язує.Отримані суміші піддалися брикетуванню і були випробувані на міцність. Залежність щільності від прикладеного тиску приведена на мал. 4.2
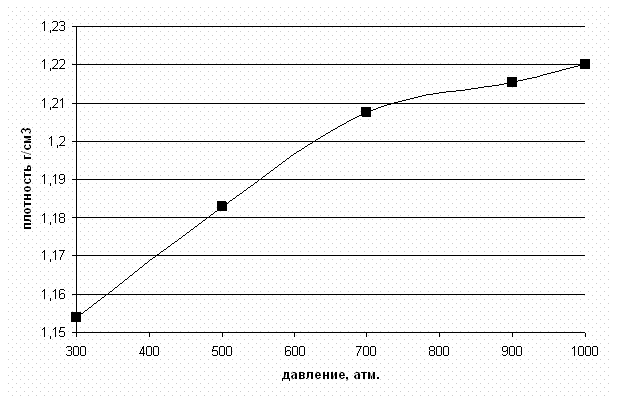
Рисунок 4.2 – Зміна щільності брикетів від тиску пресування
При малому тиску пресування щільність міняється лінійно пропорційно залежавши від тиску, при тиску вище 700 атм. ці зміни сповільнюються. Частинки вугілля зближуються дуже близько між собою і виникає в брикеті напруга, яка перешкоджає значному збільшенню щільності. Подальше збільшення тиску (>1000 атм) до зміни щільності практично не приводить, поступово наближаючись до щільності вугілля в моноліті – близько 1,29 г/см3.
Зразки брикетів піддані випробуванню відразу після приготування і після витримки протягом доби відрізняються по міцності на 5-17%. В процесі витримки зразків відбувається, мабуть, їх полімеризація, часткове випаровування вологи і схоплювання брикета, що робить його міцнішим. Для брикетів отриманих з свіжевиготовленої шихти і що пов'язує це зміцнення складає до 45% залежно від того, що пов'язує і марки вугілля.
Брикети, які були отримані при ретельному перемішуванні при нагріванні виявилися найміцнішими. Це зміцнення склало близько 30% (табл. 4.2). З цього можна зробити висновки, що існуюча технологія брикетування в заводських умовах має потребу в коректування. Тобто введенні додаткового прогріва шихти і апарату її змішення з тим, що пов'язує.
Таблиця 4.2 – Характеристика брикетів отриманих із залишків заводської шихти з тим, що пов'язує
Умови брикетування |
Міцність брикетів при тиску, ум. діл. |
300 |
500 |
700 |
900 |
1000 |
брикетуванне холодної шихти |
248 |
298 |
337 |
310 |
377 |
прогрів шихти до 40 °С |
260 |
393 |
445 |
475 |
445 |
прогрів шихти з перемішуванням |
295 |
435 |
470 |
490 |
460 |
У деяких дослідах спостерігається зменшення міцності брикетів отриманих при 1000 атм. в порівнянні з 900 атм., при цьому щільність брикетів практично не міняється. Це може бути пов'язано з тим, що при даному додаванні вугілля, що пов'язує частинки, зближують досить близько один з одним і подальше збільшення тиску приводить тільки до збільшення напруги усередині брикета і роздавлювання частинок вугілля.
Аналізуючи суміш, яка отримана в заводських умовах слід зазначити, що з неї можна отримати досить міцні брикети, тільки необхідне більше її усереднювання.
Отримані брикети планується використовувати для коксування в коксових печах. Це дозволить отримати цілий ряд переваг. Відбувається утилізація відходів коксохімічного виробництва, які зараз продаються практично за безцінь (що теж непогано, якщо немає інших варіантів використання, оскільки за відходи і їх утилізацію потрібно платити). Їх використання у вигляді брикетів, а не простого змішення з шихтою шляхом поливу на конвейєрній стрічці прибере забруднення конвейєрних стрічок, бункерів, коксової печі. Оскільки у вигляді брикетів ті, що пов'язують не проводять забруднення всіх перерахованих елементів. І крім того кокс виходить однорідним з причини ретельного перемішування і однорідності отриманої суміші. Брикетування дозволяє без погіршення якості коксу вводити вугілля неспікливих марок, нижчої якості, зважаючи на збільшення щільності завантаження. Відходи зрештою дають приріст коксу і їх використання окупається з витратами на їх утилізацію.
Висновок
Значні кількості відходів коксохімічного виробництва, вимагає раціонального підходу до їх використання. Одним з основних напрямів їх використання – може бути додавання їх шихту. Фуси, кисла смолка, полімери, як показали дослідження є непоганим матеріалом, що пов'язує, і можуть бути використані для брикетування вугілля. При цьому брикети володіють достатньою міцністю, яка забезпечує можливість їх доставки в камеру коксування.
У роботі розглянуті характеристики відходів виробництва і існуючі способи їх утилізації, теоретичні основи процесу брикетування вугілля з матеріалом, що пов'язує, і методи випробування отриманих брикетів.
Приведені результати дослідження по зразках заводської шихти з матеріалом, що пов'язує, і дани рекомендації по поліпшенню процесу брикетування. Основна причина отримання брикетів поганої якості – це недостатнє усереднювання вугілля з матеріалом, що пов'язує. Хороше усереднювання не може бути досягнуте при звичайній температурі і змішенням тільки в екструдері. По цьому необхідний додатковий підігрів шихти і сполучної речовини.
Література
- Лебедева Г.Н. – Современные схемы и технические решения при проектировании коксохимических предприятий. М., Металургиздат. 1963 (Гипрококс, Вып, 29), С. 49-63.
- Соркин М. М., Войтковская Е. А., Боярская Р. Р. – Кокс и химия , 1971, №1, С. 51-54.
- Вопросы улавливания и переработки продуктов коксования. Сб. №4. М., Металургия, 1975.
- Юкельсон И. И., Федотова Л. В., Легачева В. В., и др . - Кокс и химия , 1968, 6, С. 39-41.
- Коляндр Л. Я., Андреева В. С., Дивиденко И. Д., и др . - Кокс и химия , 1969, № 9, С. 34-37.
- Смоляков Э. В., Златин Л. Е., Штейн А. Л., - Кокс и химия , 1972, № 6, С. 46-48.
- Ремесников И.Д. Брикетирование угля. – М.: Углетехиздат, 1957. – 240 с.
- Десенко С. Г.Информация ин-та «Черметинформация», сер. 10, инф. №6, 1971. 15 с.
- Лазорин С. Н., Папков Г. И., Литвиненко В. И., - Обезвреживание отходов коксохимических заводов. М., Металургиздат, 1977. 238с.
- Паршин В. Д. - Кокс и химия , 1962, №12, С. 37-39.
- Тютюнников Ю. Б., Синцерова Л. Г., Гречко Ю. И. и др.- Органичні добавкиу виробництві коксу. Київ, Техніка, 1971, 94с.
- Кроль В. Л., Дорогобид Г. М., Праздникова В. А. – Кокс и химия , 1961, № 9, С. 12-16.
- Швед В. Г. – Кокс и химия , 1971, № 2, С. 33-39.
- Макаров Г. Н.- Производство кокса в кольцевых печах. М., Металургия, 1973. 320с.
- Глазунов А. А. – Кокс и химия , 1971, № 6, С. 47-50.
- Белоножко А. М. – Кокс и химия , 1971, № 9, С. 47-49.
- Войтковская Е. А., Касьян В. В., Кучер А. Г. и др – Кокс и химия , 1975, № 12, С. 41-42.
- Белоножко А.М. Кокс и химия, 1971, №9, С. 47-49.
- Юкельсон И.И., Федотова Л.В., Легачова В.В. и др. Кокс и химия, 1968, №6, С. 39-41.
- Крохин В.Н. Брикетирование углей. – М.: Недра, 1984, 224 с.
©
ДонНТУ Швець М.М. 2009
ДонНТУ>
Портал магістрів ДонНТУ
Про автора
|