UKR | RUS | DE ||
ДонНТУ >
Портал магистров ДонНТУ
Нікішина Ганна Леонідівна
Тема випускної роботи:
Досягнення та синтез автоматичної системи управління обробки злитків у зварювальної зоні методичної печі
Матеріали до теми випускної роботи:
Про автора
ЗМІСТ
Вступ
1. Мета проектування і потреби до приладу автоматизації
2. Технологічний процес як об’єкт автоматизації
3. Розробка структурної схеми приладу автоматизації
4. Розробка функціональної схеми приладу
5. Обґрунтування напрямку автоматизації технологічного процесу обробки злитків
6. Техніко-економічне обґрунтування ефективності прийнятих технічних рішень
Висновок
Перелік посилань
ВСТУП
Техніко-економічні показники роботи методичних печей залежать як від технічних можливостей, якими розполагають печі, так і від якості управління їх тепловим режимом. Технічні можливості методичної печі визначаються совокупністю її конструктивних і теплотехнічних характеристик.
При роботі печей ці характеристики являються наперед заданими, оскільки вони формуються при розрахунку, конструюванні і будівництві печей. Тому улучшение показників роботи діючих методичних печей може досягати шляхом совершенствования процесу управління їх тепловим режимом.
По виконуючим функціям широко застосовують системи автоматизації теплового режиму аналогічні і відрізняються між собою головним чином лише у деталях. За допомогою діючих систем автоматизації звичайно осуществляется автоматично контроль температури робочого простору печі по зонам, розхід палива і повітря, поступаючи до горілочних пристроїв окремих зон, і тиск газу в зоні, примикающій до вікна видачі, а також автоматичне регулювання температури по зонам шляхом зміни розходу палива, автоматичне підтримки зараннє заданого відношення палива-повітря і автоматична стабілізація тиску газів під сподом в районі вікна видачі нагрітих заготовок з печі.
По мере інтенсифікації процесів прокатного виробництва і підвищення вимог, які пред’являються до якості нагріву металу, виявилась необхідність видозмінення і розширення функції, які покладають на системи автоматизації теплового режиму методичних печей.
Об’єкт дослідження: процес нагріву заготовок в зварювальній зоні методичної трехзонной печі.
Ціль дослідження: підвищення ефективності регулювання тепловим режимом методичної трехзонной печі шляхом обґрунтування алгоритму і структури апаратури автоматизації і розробки.
1. МЕТА ПРОЕКТУВАННЯ І ПОТРЕБИ ДО ПРИЛАДУ АВТОМАТИЗАЦІЇ
Важливим завданням технологічного процесу на металургійних заводах являється широке впровадження високопродуктивних комплексів, які оснащені сучасним вибухобезпечним електрообладнанням. Їх впровадження забезпечує значне підвищення продуктивності роботи підприємства. Висока ефективність металу залежить від надійності роботи методичних печей, яка являється основним у процесі продуктивності металу.
Тому ціль роботи – підвищення ефективності управління температурними режимами методичної печі, шляхом впровадження нових технічних рішень у існуючу апаратуру управління.
Вимоги до системи автоматизації: необхідність визначення швидкості руху металу і при її зміненні автоматично змінювати температурний режим печі таким чином, щоб забезпечити необхідний нагрів металу у зварювальній зоні.
Вимоги до улаштування: підтримання температури у зварювальній зоні печі; вивід інформації на цифрове табло; здійснений прогнозування температури нагріву заготівок.
2. ТЕХНОЛОГІЧНИЙ ПРОЦЕС ЯК ОБ’ЄКТ АВТОМАТИЗАЦІЇ
В чорній металургії на перший план висовуються фактори, які забезпечують підвищення ефективності виробництва, подальше поліпшення якості і розширення сортаменту металопродукції. Один з основних шляхів рішення цих задач – автоматизація технологічних процесів у чорній металургії. Широке впровадження автоматизації технологічних процесів у чорній металургії диктується умовами металургійного виробництва і ростом потреби у високоякісній металопродукції.
Зі збільшенням потужності агрегатів і підвищенням потреб до якості металопродукції виявилась необхідність переходу від локальних засобів автоматичного регулювання окремих параметрів до багато зв’язаному автоматичному регулюванню і управлінню роботою всього агрегату.
Посеред технологічних агрегатів чорної металургії важну роль грають прокатні стани, випускаючі конечну продукцію металургійного вирабнитва. Якість продукції і продуктивності станів у багатьох визначається роботою нагрівальних печей, причому у більшість випадків помиски, виникненні при нагріві металу, вже не можуть бути виправлені. Та, проявляючись на наступних переділах, ці помилки приводять до зниження виходу придатної продукції.[2]
В умовах нагріву заготовлень з змінними геометричними і теплотехнічними параметрами, а також при змінному темпі заготівок з печі, получення потрібної якості нагріву заготівок можливе лише при автоматичним управлінні роботою ділянки нагрівальних печей. Існування раніше системи управління нагрівальними печами забезпечували лише стабілізацію деяких окремих параметрів теплового режиму роботи печей, таких як температура у зонах нагріву, відношення розходів палива і повітря і тиснення у робочому просторі печі. У цих системах завдання локальним регуляторам вказаних параметрів установлювались вручну зварником печі, виходячи з його досвіду, що під час в умовах напряжонної праці стану проводило до суб’єктивним помилкам. При цьому виникає недогрів заготівок, пере розхід палива, значне укалиноутворення та інше.
Бути начальною ланкою технологічної лінії прокатного виробництва, нагрівальні печі у своїй праці тісно зв’язані з ритмом праці прокатного обладнання, і на ряду з цим зберігають особливість, властиві усім теплотехнічним агрегатам. Основний час печі працює у перехідних режимах, які визвані зміненням сортаменту, матки нагрівних заготівок та темпу їх видачі, і зварник, навіть володіючи великим досвідом роботи, не у стані забезпечити припустиме управління. Крім того, слід обличити, що стан обслуговують декілька печей та необхідно забезпечити ідентичний нагрів заготівок в окремих печах і узгодити їх роботу між собою.
Методичні печі призначені для нагріву металу перед прокаткою і відносяться до печей непереривної дії. За час нагріву заготівок постійно переміщуються через усю піч від входу до виходу.
Методична піч складається з робочого просторі, де відбувається спалювання палива і нагрів металу, і ряд систем: опалення, транспортування заготівок, охолодження елементів печі, управління тепловим режимом і інші. На рисунку 2.1 зображена подовжий розтин штовхальної методичної печі.[1]
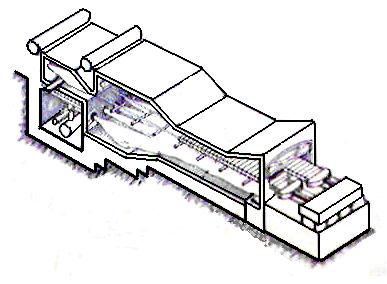
Рисунок 2.1 – Улаштування методичної печі
Методичні печі можуть розрізнятися кількістю опалювальних зон, формою робочого простору, засобами переміщення металу, підводу палива і повітря, спалення палива, а також по розміру та продуктивності, по вигляду нагріває мого металу, за типом обслуговуючих станів і ряду інших ознак.
Зміншення окислення і зневуглецювання поверхні заготівок з якісних сталей досягають при двох стадійному нагріві. При цьому використовуються звичайно декілька методичних печей. В одної з них метал повільно нагрівають до 850-900°C. Після цього заготовки подають у іншу піч, де відбувається їх «швидкий» нагрів до кінцевої температури.
Якісний нагрів металу характеризується наступними показниками:
1. Температура поверхні заготівки, усереднена за її довжині, на виході з печі відповідає заданому значенню з точністю ±10-15 К.
2. Заготівки прогріті у достатній мірі так, що перепади температур за товщиною заготівки не перевищують допущеним значенням. Цей розмір складає 20-40 К, а в місцях зіткнення заготівок з подовими трубами дорівнюється 50-70 К.
3. Перепади температур по довжині заготівок відповідає прийнятій технології прокатування.
4. Швидкість нагріву металу від вихідного становища до 500-700°C не перевищує максимального допустимого значення.[6]
В методичної печі, зокрема температури, можливо змірювати розхід газу і повітря, надмірність тиснення газу, теплоту згорання опалювального газу.
Тому ціллю проектування являється підвищення ефективність управління температурними режимами методичній печі, шляхом впровадження нових технічних рішень у існуючу апаратуру управління.
Технічними потребами до системи автоматизації являються забезпечення своєчасного якісного і економічного нагріву металу, збереженість кладіння печі і обладнання, безпечність роботи на печі і запобігання аварії, облегшення та скорочення роботи нагрівальників.
3. РОЗРОБКА СТРУКТУРНОЇ СХЕМИ ПРИЛАДУ АВТОМАТИЗАЦІЇ
Після розробки алгоритму обґрунтовую і розробляю структурну і функціональну схеми системи автоматизації.
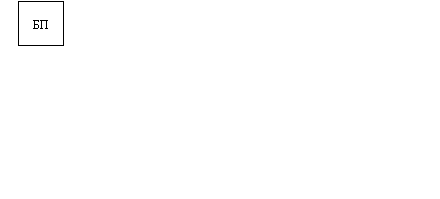
Рисунок 3.1 - Структурна схема приладу (анімація-9 кадрів, затримка 1сек, бесконечний цікл, о'бєм 20,5КБ, gif_animator.rar)
Структурна схема приладу складається з наступних основних вузлів:
БП – блок питання;
БВС – блок вхідних сигналів;
БУ – блок управління;
К – ключ;
БС – блок сигналізації;
БС ВМ – блок узгодження виконуючих механізмів;
ВМ – виконуючі механізми;
Робота структурної схеми здійснюється наступним чином: сигнал від датчиків поступає на блок вхідних сигналів БВС, а потім на блок управління БУ. Одночасно з цим з блоку сигналізації БС сигнал поступає оператору, який в свою чергу дає сигнал на ключ К. Далі сигнал передається на блок управління і через блок узгодження виконуючих механізмів БС ВМ подається на виконуючий механізм ВМ.
Усі вузли запитані напругою від блоку питання БП.
4. РОЗРОБА ФУНКЦІОНАЛЬНОЇ СХЕМИ ПРИЛАДУ
Функціональна схема приведена на рисунку 4.1 і принцип її роботи заклечається в наступному.
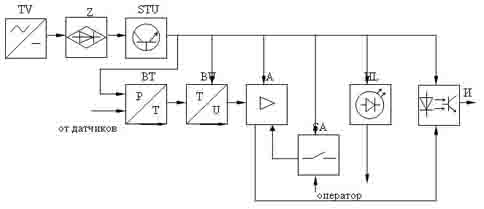
Рисунок 4.1 - Функціональна схема приладу
Тепловий сигнал, прийнятий датчиками температури BT і напруги BU, поступає на операційний підсилювач A. При увімкненні світового індікатору HL, оператор, получив сигнал, через перемикач SA подає сигнал на підсилювач A. Потім сигнал через оптопару VU поступає на виконуючий механізм.
Постачання схеми осуществляется через трансформатор TV.
Задача управління процесом нагріву металу у методичних печах заключається у виборі і підтримки режиму роботи, забеспечуючого получення металу заданої якості з мінімально можливим удільним розходам палива в умовах перемінної производительности агрегату.
5. ОБГРУНТУВАННЯ НАПРЯМКУ АВТОМАТИЗАЦІЇ ТЕХНОЛОГІЧНОГО ПРОЦЕСУ ОБРОБКИ ЗЛИТКІВ
Система автоматичного управління тепловим режимом методичної печі включає в себе вузли автоматичного регулювання (рис.5.1): температура у зоні 1, відношення розходів палива і повітря на зону 2, оптимізація горіння палива у зоні 3, тиск у робочому просторі 4. Для забезпечення якості роботи системи в умовах змінення продуктивності печі призначене вузол 5 корекції завдань зональним регуляторам температури.
Регулювання температури у зоні печі здійснюється типовим комплексом приладів по сигналу термопари. П- або ПІ-регулятор, змінюючи розхід палива на зону, приводить у відповідність діячу температуру у печі с заданою.[3]
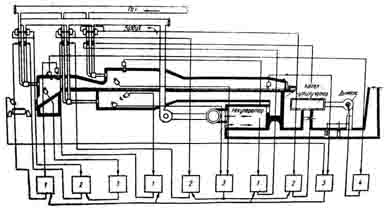
Рисунок 5.1 – Принципіальна схема системи автоматичного регулювання теплового режиму методичної печі
Система контролю і автоматичного регулювання тризонної печі, опаленої газом с постійною теплотою згорання. Схемою передбачається контроль і регулювання наступних параметрів:
1) температури у робочим просторі томильної, верхньої зварювальної зони і зони нижнього прогріву;
2) відношення палива-повітря у тих же зонах;
3) тиск у томильній зоні,
а також контроль:
1)температури диму після рекуператору;
2)температури гарячого повітря після ексгаустера;
3)температури хвостової частини печі;
Розхід газу і повітря на кожну зону.
Крім цих параметрів, можуть контролюватися ще цілий ряд інших (тиск газу і повітря, розхід газу на усю піч, температуру диму до рекуператору і тощо).
Автоматичний контроль і регулювання температури зон печі. Схеми автоматичного контролю і регулювання температури усіх зон однотипні.
Температура зон вимірюється платинородій – платиновими термопарами у фарфорових чохлах або радіаційними пірометрами, які візіруються на дно карбофраксових склянів. Показання і запис температури зони здійснювати за допомогою електронного потенціометру з убудованим реостатним датчиком. Потенціометр звичайно працює у комплекції з іподромним регулятором, який за допомогою електричного виконавчого механізму управляє дросельній заслоною, розташованої у трубопроводі, підводячем газ до зоні печі.
При відхиленні вимірювальної температури від заданого значення регулятор, який впливає на виконавчий механізм заслони, змінює розхід палива, який мчиться підтримувати температуру у зоні на даному рівні.
Завдання регулятору температури кожній зоні установлювається зварником вручну в залежності від температури металу, видаваємого з печі. У більшості випадків остання визначається на око. Для цього розробляється більш удосконалений прилад.
Функції системи автоматизації:
1) діапазон коефіцієнту розходу коливається у межі 1,05-1,25, а діапазон, до якого потрібно наближатися, щоб досягнути найкращий результат 1,05-1,1;
2) заміна морально застарілих локальних регуляторів на сучасні аналоги з розширеним набором функцій;
3) вимірювання основних технологічних параметрів: температури, подачи палива, коефіцієнт надлишку палива;
4) сигналізуючи прилад про не досягненні заданих технологічних параметрів.
6.ТЕХНІКО-ЕКОНОМІЧНЕ ОБГРУНТУВАННЯ ПРИЙНЯТИХ ТЕХНІЧНИХ РІШЕНЬ
Економічна служба приладу – одно з важних ланок управління приладом. Рівень економічної роботи методично печі характеризується, насамперед, організацією роботи всіх ланок управління. Об’єм і форма автоматизації повинні бути вибрані і установлені на основі відповідного аналізу. Важним критерієм при оцінці ефективності автоматизації, як і всякого виробничого удосконалення, являється окупність затрат на автоматизацію, утворювана за рахунок зниження собівартості і поліпшення якості продукції, а також зменшення виробничих затрат і втрат.
Явно, що при інших рівних умов окупність прийнятої автоматизації тим більше, чим значніше зниження собівартості продукції, отримане за рахунок автоматизації, і чим більший приріст виходу годного продукту дає автоматизацію.
Окупність можна вирахувати після завершення робот по автоматизації даної ділянки виробництва, але дуже тяжко зробити це на стадії вибору ефективного направлення автоматизації. Тому доцільно оперувати очікуваними зміненнями собівартості продукції і продуктивності процесу.
Встановлено, що найкращі умови окупності автоматизації створюються у неприливному процесі, в якому усякого роду непродуктивні утрати на холості і допоміжні операції, несуміщувані з робочим часом, мінімальні.
У переривистому (циклічному) виробництві, визначним параметром являється ритмічність роботи усіх елементів виробничого ланцюга. Це пояснюється, по крайній мірі, двома причинами:
– перша складається у інерційності процесів, які протікають у ряду виробничих елементів. У перехідному режимі звичайно знижується якість продукції, продуктивність процесу і його економічність.
– друга полягає у великої ролі транспортних засобів, які можуть забезпечити подачу необхідної сировини, відвід продукції тільки при ритмічної роботі усіх агрегатів, ділянок цеху.
У ході роботи був відбувся аналіз технологічного процесу нагріву заготівок у зварювальній зоні методичної печі як об’єкта автоматизації, сформульована ціль курсового проектування і вироблені потреби до системи автоматизації процесу. Зроблено критичний огляд відомих технічних рішень по автоматизації технологічного процесу нагріву заготівок, обґрунтовано подальше направлення автоматизації дослідженого процесу і сформульовані функції розробленого приладу автоматизації. Зроблена алгоритмізація системи автоматизації, при цьому виділені блоки, які підлягають зміненням у наслідок даної розробки. Відбулось обґрунтування і розробка схематехнічного рішення приладу автоматизації, а саме проаналізована структурна схема системи автоматизації технологічного процесу, розроблені структурна схема блоку регулювання швидкості подачі, а також розроблена і принципіальна електрична схема розробляємого блоку. Проведені необхідні розрахунки елементної бази приладу, розроблено програмне забезпечення для управління приладом за допомогою мікроконтролеру, а також відбувся розрахунок надійності даної схеми. Опрацьовані заходи по безпечній і безаварійній експлуатації розробленого технічного рішення, вчинено техніко-економічне обґрунтування ефективності прийнятих рішень.
ВИСНОВОК
Таким чином, розроблена система автоматизації методичної трехзонной печі задовольняє заданим технічним і технологічним потребам. Необхідно відмітити достоїнства і недостатки даного приладу. До достоїнств відносяться в першу чергу безпонтанне виміряння температури:
- проста елементна база;
- можливість збудувати пороги зношення на визначну температуру.
До недостатків відноситься:
- дорожнеча датчику;
- нелінійність сигналу датчика.
Разом з цим, розроблений блок має не закінченій варіант, і буде допрацьовуватися у магістерській роботі.
ПЕРЕЛІК ПОСИЛАНЬ
- Буглак Л.И., Вольфман И.Б., Ефроймович С.Ю. Автоматизация методических печей, М: Металлургия, 1981г.-195с
- Гусовский В.А., Оркин Л.Г., Тымчак В.М. Методические печи. М: Металл, 1970г.-430с
- Тайц Н.Ю., РозенгартЮ.И. Методические нагревательные печи. Москва: Металлургиздат, 1964.-408с.
- Каганов В.Ю., Блинов О.М., Беленький М.М. Автоматизация управления металлургическими процессами. М., «Металлургия», 1974.- 416с
- Евтихиев Н.Н., Купершмидт Я.А., Папуловский В.Ф., СкугоровВ.Н. Измерение электрических и неэлектрических величин. Москва: Энергоатомиздат, 1990. - 352 с.
- Климовицкий М.Д. Автоматизация методических печей. Москва: Металлургия, 1981. - 196с.
- Клаассен К.Б. Основы измерений. Электронные методы и приборы в измерительной технике. Москва: Постмаркет, 2000. - 352 с.
ДонНТУ >
Портал магистров ДонНТУ ||
Про автора