Исследование механизма разрушения нитридных включений в титановых сплавах при єлектрошлаковом переплаве под "активными" металлосодержащими флюсами
Пашинский В.В., Рябцев А.Д., Троянский А.А,Тарлов О.В. (ДонГТУ) Бенц М.Дж. ("Дженерал Електрик", США)
Источник:: Труды Донецкого государственного технического университета. Металлургия, Выпуск 18. - Донецк:ДонГТУ, 200. - с.65-69.
Установлено, что электрошлаковый переплав (ЭШП) под «активным» металлсодержащим флюсом может быть использован для рафинирования титановых сплавов от нитридных включений. Исследован механизм растворения нитридных включений, который включает массоперенос азота через шлаковую ванну от включения к пленке расплавленного металла на торце электрода с последующим переходом в твердый раствор в формирующемся слитке. Полученные экспериментальные данные и металлографические исследования подтвердили предложенный механизм.
Целью исследования являлось изучение механизма растворения нитридных включений при электрошлаковом переплаве (ЭШП) титановых сплавов под «активными» кальцийсодержащими флюсами.
Нитридные включения образуются практически на всех стадиях производства титановых сплавов (от получения губки до выплавки конечных слитков). Присутствие нитридных включений в титановых сплавах приводит к снижению усталостной прочности высоконагруженных деталей (например, в компрессорных и вентиляторных секциях авиационных реактивных двигателей, в компрессорных секциях газовых и паровых турбин электростанций, секциях крыльев или элементах каркаса самолетов, в медицинских инструментах).
Эти включения имеют, как правило, сердцевину из TiN, которая окружена слоем a-Ti, в свою очередь окруженную слоем b-Ti. Их часто называют «твердыми альфа» - включениями. В некоторых случаях сердцевина из TiN может отсутствовать и участок a-Ti может быть более протяженным. «Твердые альфа» - включения являются очень хрупкими по сравнению с окружающим сплавом и разрушаются первыми при интенсивных циклических нагрузках, формируя тем самым очаг зарождения трещин.
При этом проблемой является именно склонность нитридных включений к активации трещин, а не общее наличие азота в системе. Присутствие «твердых альфа» - включений часто является также причиной формирования несплошностей при ковке и горячей штамповке, что еще более увеличивает размер потенциального очага зарождения трещин [1,2].
Проблемой, таким образом, становится удаление или минимизация размеров нитридных включений.
Анализ фазовой диаграммы показывает, что нитридные включения плавятся при более высокой температуре, чем сам титан. Следовательно, все процессы, направленные на удаление нитридных включений при их погружении в жидкий титан, зависят скорее от скорости растворения, чем от скорости плавления. Кинетика скорости, растворения нитридных включений, погруженных в жидкий титан, была исследована во многих работах. Этот процесс относительно медленный, и скорость составляет приблизительно около 2,2 мкм/сек [3]. Такая низкая скорость ограничивает размер включений, которые могут быть удалены при используемых в настоящее время вакуумных переплавах.
Два основных кинетических фактора ограничивают скорость растворения нитридных включений — это термодинамическое ограничение скорости и транспортное ограничение (связанное со скоростью циркуляции шлака) [4]. Эксперименты, описанные в данной статье, в основном направлены на исследование термодинамического ограничения скорости. Чтобы избежать термодинамических ограничений, парциальное давление азота в атмосфере над шлаком должно быть снижено, до уровня 10 атм. Электрошлаковый переплав (ЭШП) под «активным» флюсом может быть использован для создания условий, когда парциальное давление азота составляет 10 атм. Это достигается сочетанием: (1) — выбора состава шлака, (2) — конструкции тигля и камеры установки ЭШП и (3) — процедуры плавления.
1. Состав шлака — использовался «активный шлак» на базе фтористого кальция (CaF2), содержащий избыточный металлический кальций (Са).
2. Тигель и камера установки ЭШП — водоохлаждаемые медные тигли двух
различных диаметров (95 мм и 135 мм) были использованы в работе. Оба имели длину
приблизительно 500 мм. Водоохлаждаемая камера электрода монтировалась непосредственно на верхней части тигля. Система была сконструирована с соответствующими уплотнениями, позволяющими создавать вакуум в комбинации тигель-камера.
3. Процедура плавления — перед плавкой пространство камеры и тигля откачивалось, а затем наполнялось аргоном. Во время плавления система поддерживалась под избыточным давлением аргона около 0,15 атм. Небольшой расход аргона устанавливался для компенсации потерь через различные уплотнения. После плавления шлака, пары кальция поднимались в электродную камеру над тиглем. В ней происходила реакция паров кальция с остаточными количествами азота и кислорода, присутствовавших в аргоне и снижение парциальных давлений азота и кислорода в атмосфере над шлаком до значений ниже 10 атм.
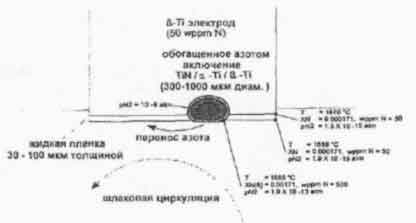
Рисунок 1 — Механизм растворения нитридных включений при электрошлаковом переплаве под кальцийсодержащим флюсом
Механизм растворения нитридного включения при «активном» электрошлаковом переплаве показан на рисунке 1. Он включает в себя следующие стадии:
— транспортировку азота от
обогащенного азотом включения в
шлак, в то время как шлак циркулирует возле поверхности ввключения,
подвергаемой обработке;
— транспортировку азота обратно к поверхности электрода (в виде разбавленного раствора в пленке жидкого металла вокруг обширной области свободной поверхности электрода), в то время как шлак циркулирует у поверхности электрода;
транспортировку азота от поверхности электрода в ванну расплавленного титана путем плавления торца электрода и формирования капель жидкого металла, содержащего растворенный азот, которые проходят через шлак;
затвердевание металлической ванны с формированием разбавленного раствора азота в твердом титане. Химическая активность азота в шлаке (10 атм.) устанавливается на уровне существенно ниже, чем во включении (10 атм.), однако выше, чем на границе «пленка жидкого металла — шлак», что создает термодинамическую движущую силу для транспортировки азота по описанному механизму.
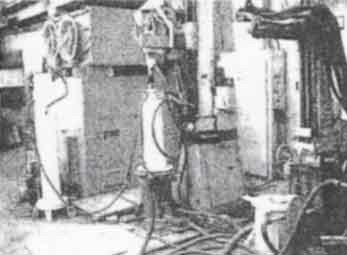
Рисунок 2 — Установка ЭШП А-550 для проведения переплава в контролируемой атмосфере под «активными» флюсами
Для практического осуществления и подтверждения данного механизма были проведены лабораторные эксперименты. Для этого была использована специально переоборудованная установка ЭШП А-550, позволяющая проводить процесс ЭШП в атмосфере инертных газов и использовать для переплава «активные» металлсодержащие шлаки (рисунок 2). В качестве образцов, имитирующих нитридные включения, были использованы искусственно приготовленные включения из азотированной титановой губки (30% азота) и прессованного порошка нитрида титана (49% азота). Особенностью этих экспериментальных плавок было использование части электрода, содержащей искусственное обогащенное азотом включение, расположенное вдоль оси электрода и имеющее значительные линейные размеры. Наличие протяженного включения устраняло возможность случайного выпадения полностью или частично нерастворенного включения, что наблюдалось на некоторых предыдущих экспериментах.
Для экспериментов был использован тигель диаметром 135 мм. Электроды изготавливались из сплава ВТ6-4 75 мм в диаметре и 770 мм длиной. Включения имели цилиндрическую форму от 3 до 10 мм в диаметре и 10-35 мм длинной, расположенные как по оси электрода в верхней его части путем сверления, вставки, электроннолучевой сварки и горячего изостатического прессования так и в виде локальных включений по всей длине электрода. Были использованы оба типа включений.
Переплав протекал достаточно стабильно. При входе в шлак части электрода, содержащей протяженное включение в центре, скорость переплава не снижалась. Переплав продолжался до сплавления около 100 мм части электрода, содержащей центральное включение. После переплава были получены слитки: 135 мм в диаметре и 265 мм длиной.
Исследовалась как структура остатков электродов, так и полученных слитков. При исследовании остатков электродов было установлено, что происходило стабильное растворение как 30%, так и 49% включений.
Металлографические образцы были отполированы, протравлены и подвергнуты исследованиям при низких (х5-х20) и средних (х200) увеличениях. Металл имел крупнозернистую структуру, типичную для литого металла. В процессе проведения различных видов термообработки металла полученного слитка было обнаружено интересное явление. При отжиге шлифованного поперечного образца, вырезанного на высоте 208 мм от дна слитка, в нагревательной печи на воздухе при 750°С в течении 2 ч и охлаждении на воздухе вне печи наблюдается различное окрашивание поверхностных зон как на торцевой так и на боковой поверхности слитка (рисунок 3).
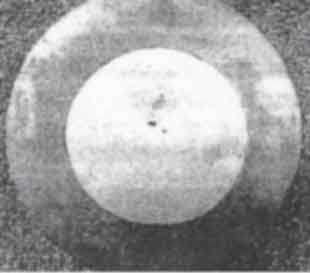
Рисунок 3 — Азотированная зона, зафиксированная методом окислительного травления
Дальнейшие исследования показали, что окрашивание соответствует сечению зафиксированной азотированной жидкой ванны металла, которое происходит в момент падения азотированной капли жидкого титана вызванной растворением на торце электрода азотсодержащего включения. После полировки и травления, в макроструктуре выявились 2 концентрические зоны. Твердость в радиальном направлении менялась сложным образом во время перехода через границу зон, однако не было выявлено никаких изменений в микроструктуре металла в районе границы зон. Две части одного кристаллита могут принадлежать различным зонам. Однако переходный участок между зонами имеет более сложное строение в сравнении с выявленным путем травления. После окислительного травления
мы можем видеть дополнительный промежуточный слои на границе между зонами. Склонность к окислению этого участка минимальна. Это явление может быть объяснено исходя из следующего предположения. Склонность к окислению титана снижается с ростом содержания азота в твердом растворе. Измерение твердости дает повышенные значения в участках, соответствующих ванне расплавленного металла в момент растворения включения. При этом, максимальные значения наблюдаются на границе зон (рисунок 4). Следовательно, промежуточный слой — это слой с максимальной концентрацией азота.Он формируется в результате быстрой кристаллизации обогащенного азотом жидкого титанового сплава в контакте с твердой частью слитка.
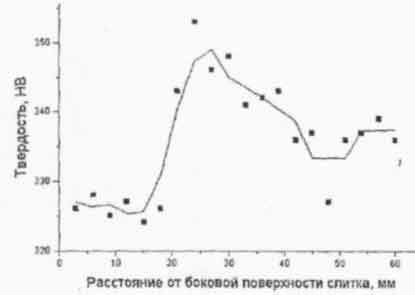
Рисунок 4 — Распределение твердости в поперечном сечении слитка (вдоль радиуса)
Маленькие остатки нерастворенных включений выявлялись как ультразвуковым контролем, так и металлографическими исследованиями (рисунок 5). Оценка показала, что выявленные остатки не превышают 10% переработанного объема включения. Остальные 90% распределились в твердом растворе в расплавленной ванне путем растворения на торце электрода и равномерного перераспределения в титане.
Микроструктурные исследования строения титанового сплава вокруг остатков включения в слитке подтвердили предположение, что это части центрального и единичного включения. Они попали в жидкую ванну и после их погружения в расплавленный металл, процесс растворения шел с очень низкой скоростью. Сформированная диффузионная зона вокруг включений имеет малую протяженность. Это подтверждает предположение, что процесс растворения происходит в результате взаимодействиямежду включением, расплавленным металлом и активным шлаком под воздействием
электрических дуг.
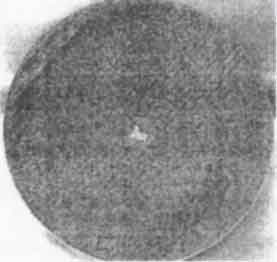
Рисунок 5 — Нерастворенный остаток китридного включения 3-4 мм длиной, обнаруженный в нижней части слитка на высоте 150 мм от дна
Таким образом, выполненные эксперименты показали возможность эффективного использования электрошлакового переплава для разрушения нитридных включений. Наличие кругов с различной окраской, формирование которых связано с переходом азота из компактного включения в твердый раствор подтверждает предложенный ранее механизм растворения нитридных включений.
Наличие большой азотированной зоны свидетельствует, что из-за высоких скоростей плавления продукты распада включения не успевают полностью удаляться из системы. Наличие в слитках остатков нерастворенных включений также свидетельствует о недостатке времени для завершения процессов растворения. Поэтому для повышения эффективности процесса необходимо снижение скорости плавления. Частично эту проблему можно решить на существующей установке А-550, однако для более полного и успешного решения этой проблемы (растворение включения и удаление продуктов) необходимо увеличивать диаметр электродов и слитков. Это позволит сохранить температурные режимы процесса и глубину металлической ванны при снижении скорости плавления включения до уровня, обеспечивающего его гарантированное разрушение.
|