Режущий инструмент: безвольфрамовые перспективы.
Владимир Крикун Харьковсий инструментальный завод
Источник: http://www.metalika.ua/bulletin.php
В отечественном и зарубежном машиностроении при механической обработке деталей большую часть операций выполняют лезвийным инструментом. Обрабатывают элементы корпусов двигателей, поршни автомобилей, детали ходовой; крепежные элементы, роторы, рабочие и сопловые лопатки, детали клапанов паровых и газовых турбин и многие другие. Требуется обрабатывать как конструкционные углеродистые и низколегированные стали, так и жаропрочные стали (имеющие в своем составе присадки легирующих элементов: хрома, алюминия, никеля, титана, молибдена, ванадия, вольфрама и других металлов). Такие материалы способны работать длительное время при температурах порядка 850 градусов. В процессе обработки деталей из жаропрочных сталей на их поверхностности и на передней поверхности инструмента образуется деформированный слой.
Это, в свою очередь, весьма отрицательно влияет на подачу резца в зону обработки, на скорость резания и, в конечном счете, – на производительность процесса металлообработки. А основными показателями любого (в том числе и металлообрабатывающего) лезвийного инструмента являются его долговечность и производительность.
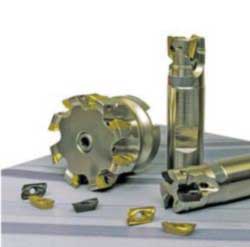
Для улучшения вышеназванных характеристик при производстве инструмента в настоящее время применяют инструментальные стали (инструментальные углеродистые, инструментальные легированные и быстрорежущие стали) и твердые сплавы:
- Углеродистые инструментальные стали применяются для различных инструментов, но они имеют недостаточно высокую температуру красностойкости (способность материала сохранять свои физические свойства при нагреве) – порядка 200°С. Обозначаются они буквой У (углеродистая) и числом, обозначающим содержание углерода в десятых долях процента. Например, У8 - качественная углеродистая инструментальная сталь с содержанием углерода 0,8%. Легирование углеродистых сталей позволяет повысить прокаливаемость (способность стали после термической обработки повышать свою твёрдость, за счет изменения структуры).
- Инструмент из быстрорежущих сталей имеет скорость резания в несколько раз выше, а стойкость такого инструмента - в десятки раз выше. Главной отличительной особенностью быстрорежущих сталей является их красностойкость при температурах 600-700°С при наличии высокой твердости и износостойкости. Марки быстрорежущих сталей начинаются с буквы "Р", за ней следует цифра, указывающая содержание вольфрама. Во всех быстрорежущих сталях содержится около 4% Сг , но в обозначении марки буквы «X» нет. Например, сталь Р6М5ФЗ - содержит 5,5-6% вольфрама; 4,6-5,2% молибдена; 1,8-2,4% ванадия.
- Твердые сплавы для пластин, напаянных на режущий инструмент, получают из твердых карбидов вольфрама W, титана Ti, тантала Ta и вязкой связки кобальта Со методом порошковой металлургии. Чем выше содержание кобальта в сплаве, тем выше ударная вязкость (способность материала не крошиться при ударном воздействии, которое испытывает инструмент при работе), но ниже твердость. Температура красностойкости таких сплавов до 1000-1050°С. Примерами твердых сплавов являются: ВК2 – вольфрамокобальтовый твердый сплав, содержащий 2% Со и 98% W; Т5К10 - вольфрамотитанокобальтовый твердый сплав, содержащий 10% Со, 5% TiС и 95% WC; ТТ10К8 - вольфрамотитанотанталокобальтовый твердый сплав, содержащий 8% Со, 10% TiС +TаС , 82% WC.
Вследствие того, что вольфрам дорогостоящий и дефицитный металл, хорошо зарекомендовали себя новые твердые сплавы, не содержащие его. Порошки карбидов тантала и титана смешиваются с порошкообразными кобальтом и никелем, затем формуются холодным прессованием и спекаются. В результате получаются твердые металлокерамические материалы (цементированные карбиды), пригодные для обработки металлов резанием и для бурения горных пород. Таким образом, дефицит вольфрама стимулировал создание новых инструментальных материалов, которые бы не уступали по своим характеристикам инструментальным сталям и твердым сплавам. Такими материалами являются безвольфрамовые твердые сплавы, в которых используют карбид титана TiС и связку из никеля Ni и молибдена Мо. Примерами таких сплавов служат: ТН20 и КНТ16, которые выпускаются серийно и успешно применяются в производстве при обработке углеродистых сталей.
Изучение производственного опыта показывают, что некоторые безвольфрамовые твердые сплавы можно успешно использовать для обработки жаропрочных сталей и сплавов, работающих при высоких температурах. Известно, что высокая контактная температура, развивающаяся при соприкосновении режущего инструмента и обрабатываемой поверхности, способствует «слипаемости» материала детали и частиц твердосплавного инструмента. В результате этого на режущей кромке образуется нарост, который в процессе резания скалывается и приводит к износу резца. В то время как при обработке жаропрочных сталей резцами из твердого сплава (например, ВК8) и обработке резцами из безвольфрамового твердого сплава (например, ТН20) «слипаемость» обрабатываемого материала и материала инструмента наблюдается в значительно меньшей степени. Но резцы из сплава ВК8 содержат 92% вольфрама, поэтому экономически выгоднее применять твердый сплав ТН20 для обработки жаропрочных материалов.
Ещё одним фактором, способным повысить износостойкость инструмента, кроме свойств и характеристик самого материала, является нанесение упрочняющих сверхтвердых покрытий. Благодаря покрытиям появилась возможность конструировать режущий инструмент, в котором сочетались бы достаточно высокая прочность основы с высокой стойкостью рабочих поверхностей. Наиболее перспективными твердыми покрытиями для режущего инструмента считаются покрытия карбидами и нитридами переходных металлов (титана, циркония и др.), а также оксидами алюминия, кремния, оксидом и нитридом бора. В частности, для покрытия режущих пластин из твердых сплавов в настоящее время широко применяются нитрид титана (TiN), карбонитрид титана (TiCN), титан нитрид алюминия (TiAlN), нитрид хрома (CrN), нитрид циркония (ZrN) и т.п. Наиболее эффективны покрытия, состоящие из комбинации твердых и мягких слоев. Но в любом случае общая толщина покрытия составляет величину, не превышающую, как правило, 5–15 мкм. Только при этих условиях удается избежать проявления собственной высокой хрупкости сверхтвердых материалов.
Чаще всего для покрытия режущего инструмента применяется нитрид титана TiN. Он наносится ионно-плазменным методом на установках типа «Булат». Суть метода заключается в том, что в камере, заполненной азотом, газ разогревается до состояния плазмы. Инструмент, на который заранее наносится титановое покрытие, также находится в этой камере. Под воздействием высокой температуры плазмы атомы азота, имеющие высокую энергию, замещают собой атомы титана. Вследствие этого процесса получается покрытия «золотого» цвета из нитрида титана. Обладая высокой твердостью, коррозионной стойкостью, низким коэффициентом трения с обрабатываемыми материалами, такое покрытие служит диффузионным барьером, уменьшая износ инструмента, силы резания (при обработке резанием) и усилия деформирования (при операциях штамповки). Защищая от перегрева подложку (материал под пленкой нитрида титана), покрытие снижает склонность инструмента к свариванию с обрабатываемым материалом, уменьшает или исключает налипание на инструмент, улучшает качество обработанной поверхности. Как показывают результаты экспериментов, при работе инструмента в цеховых условиях напыленные сверла имеют более высокую стойкость в сравнении с ненапыленными даже после переточки. Аналогичные результаты получены и при определении стойкости напыленных нитридом титана зуборезных червячных фрез из стали Р6М5 при нарезании шестерен из стали 40Х модулем (сверлом) 3,5 мм: до снятия со станка одной фрезой с напылением можно нарезать 68 шестерен против 27 фрезами без покрытия, т.е. повышение стойкости составляет 2,5 раза.
Таким образом, замена вольфрамсодержащих материалов в режущем инструменте экономически выгодна и технологически оправдана. А, значит, подорожание вольфрама – не экономическая угроза, а хороший повод к модернизации и развитию производства.
|