ИССЛЕДОВАНИЕ РАСПРЕДЕЛЕНИЯ МАРГАНЦА И КИСЛОРОДА МЕЖДУ ЖИДКИМ ЖЕЛЕЗОМ И МНОГОКОМПОНЕНТНЫМИ
ОКСИДНЫМИ РАСПЛАВАМИ
Явойский В.И., Савов П.Х., Лузгин В.П., Иванчев И., Еринин Хр.
Источник:Изв. высш. учеб. заведений "Черная металлургия", 1976, 3, с.28-32.
В последние годы во всем мире возрастает дефицит марганца, поэтому особое значение
приобретает вопрос извлечения марганца из марганцовистых чугунов и получения высокомарганцовистых шлаков, пригодных для
выплавки ферромарганца или силикомарганца. Такая проблема стоит сейчас перед болгарской металлургией и, очевидно, в
ближайшее время встанет в Советском Союзе в связи с необходимостью переработки устиновских и других марганецсодержащих
руд железа. В связи с этим определенный интерес представляют состав, строение и термодинамические свойства богатых
марганцем окисных расплавов.
Равновесному распределению марганца и кислорода между жидким металлом и двух- и
трехкомпонентными шлаками посвящен ряд экспериментальных исследований. В связи с повышенным содержанием закиси
марганца в шлаках, образующихся при переделе чугунов с повышенным содержанием марганца (2—6% Мn), равновесное распределение
марганца и кислорода в сложных системах Fе—Мn—О—FеО—МnО—СаО—SiO2—Аl203 имеет большое практическое значение. Целью
настоящей работы было
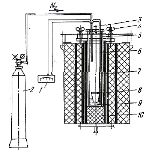
Рисунок 1 - Общий вид опытной установки:
1 — потенциометр; 2 — азот; 3 — трубка из Аl203; 4 — крышка из SiO2; 5 — реакционная
труба; 6 — термопара; 7 — наконечник из Аl203; 8 — тигель; 9 — подставка
из Аl203; 10 — графитовая подставка.
не только исследовать равновесие между металлом и шлаком для этих систем, но и за счет экспериментального определения
активностей закиси железа и закиси марганца добиться обобщающих термодинамических характеристик многокомпонентных шлаков
с повышенным содержанием МnО.
Для изучения равновесного распределения марганца и кислорода и опытного определения
активностей закиси железа и закиси марганца производили химический анализ проб контактирующих металлической и шлаковой
фаз. Достижение равновесия определяли неизменностью состава отбираемых проб.
Исследование проводили на установке (рис. 1), состоящей из печи Таммана,
реакционной трубки из плавленой окиси алюминия, подвесной системы с тиглем и систем продувки нейтрального газам
измерения температуры с помощью термопары ПР 30/6. Установление температуры на заданном уровне осуществляли специальным
тиристорным устройством и трансформатором. Все эксперименты проводили в атмосфере очищенного азота под небольшим
избыточным давлением.
Порядок работы был следующим. В тигле расплавляли около 50—60 г высокочистого электролитического железа. Сразу после
расплавления металла в ванну сбрасывали 20 г смеси шлакообразующих компонентов в виде таблеток, изготовленных из чистых
окислов. Для надежного установления равновесия опыт продолжался 50—60 мин после достижения заданной температуры. Пробы
металла отбирали засасыванием кварцевой трубкой диаметром 4 мм пробы шлака намораживанием его на стальной пруток. Содержание кислорода в металле определяли методом
газа-носителя на установке «Леко».
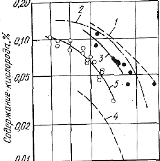
Рисунок 2 - Равновесие Мn—О в жидком железе в зависимости от состава шлака
при 1550 и 1600°С:
1 — в жидком железе под шлаками системы FеО—МnО (опыты в тиглях из закиcи
марганца); 2 — в жидком железе под шлаками системы FеО—МnО—SiO2, насыщенными кремнеземом; 3 — данное исследование —
опытные результаты первой серии плавок при 1650°С (º—º) и второй серии плавок при 1660°С (•—•);
4 — опытные результаты работы системы FеО—МnО—Аl2О3 (15% Аl2О3) 1560°С; 5 — данное исследование — опытные результаты
по шлакам системы FеО—МnО—СаО—SiO2.
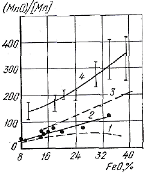
Рисунок 3 - Зависимость коэффициента распределения марганца от содержания
закиси железа в шлаке:
1 — шлаки системы FеО—МnО—Аl2О3 насыщены твердыни растворами FеО—МnО при
1530°С; 2 — опытные результаты второй серии плавок, 1600°С; 3 — опытные результаты работы,
1625°С, шлаки системы FеО—МnО—СаО—SiO2 насыщены 3СaO*SiO2; 4 — опытные результаты первой серии плавок, 1550°С.
Провели две серии экспериментов, всего 26 плавок. Эксперименты первой серии проводили в тиглях из окиси алюминия при
1550°С, а второй серии в тиглях из окиси магния. Число опытов по исследованию равновесного распределения [Мп] и [О]
между жидким железом и основными шлаками системы FеО—МnО—СаО—SiO2 при 1600°С (второй серии) было ограничено из-за
впитывания жидкого шлака тиглем. Кроме основных составляющих компонентов, в этих шлаках обнаружено 2—4 % МgО и 3—8%
Fе2О3. Общую концентрацию окислов железа (FеО) рассчитывали по уравнению

Результаты химического анализа шлака приведены к 100 % состава FеО—МnО—СаО—SiO2—Аl2О3.
Пределы изменения содержания закиси марганца в шлаках первой серии 6,5—24,0%, второй серии 16—30%. Зависимость между
равновесными концентрациями марганца и кислорода на основе экспериментальных данных, полученных в двух сериях опытов,
представлена на рис. 2. Полученные данные сопоставлены с результатами других работ при тех же температурах.
Из рис. 3 видно, что опытные значения коэффициента распределения марганца для плавок
первой серии лежат значительно выше по сравнению с результатами плавок, относящихся к системе FеО—МnО—Аl2О3 при температуре
1530±20°С по данным работы. Это можно объяснить, если допустить более сильное положительное отклонение активности закиси
железа в исследуемой пяти компонентной системе под влиянием СаО в присутствии Аl2О3 и SiO2. Разброс опытных точек
является следствием колебания химического состава шлаков первой серии.
Как видно из рис. 3, результаты опытов второй серии удовлетворительно согласуются
с данными недавно опубликованных исследований равновесного распределения марганца между жидким железом и основными
насыщенными 2СаО·SiO2 и 3СаО·SiO2 шлаками той же системы FеО—МnО—СаО—SiO2 с содержанием закиси марганца ниже 10%.
Следовательно, наличие в основных шлаках кислородно-конверторного процесса повышенных концентраций закиси марганца не
изменяет термодинамических характеристик процесса окисления марганца.
Литература
- Самарин А.М. Физико-химические основы раскисления стали. М., изд. АН СССР, 1956, с.185.
- Иванчев И., Бел М., Сомервил П. - "Рудобив и металлургия", 1974, №1, с.34-39.
|