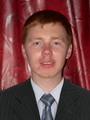 |
Кривоплясов Євген Леонідович
|
Тема магістерської роботи:«Дослід руху змащувальних матеріалів в підшипникових вузлах металургійних машин»
Науковий керівник: доцент
Сидоров Володимир Анатолійович
Автореферат за темою магістерської роботи
Вступна частина
Актуальність работи
У сучасному металургійному
устаткуванні, як і в будь-якому іншому, виникають різного роду несправності. Найбільш поширеною
причиною відмов (близько 50 % від загального числа) є проблеми з мастилом. В даний час важкі
умови (висока запиленість і температура) роботи вузлів металургійних машин примушують шукати
все нові шляхи вдосконалення якості і необхідних властивостей змащувального матеріалу, правильний
вибір якого прямо впливає на надійність і довготривалість роботи змащуваного вузла машини. Як
теоретичні так і практичні дослідження показали, що правильно вибраний сорт змащувального матеріалу
і його кількість дозволяє продовжити термін служби і експлуатації механізму, що у свою чергу веде
до мінімальних витрат на ремонт і до підвищення прибутку.
Цілі і завдання роботи
Метою даної роботи є дослідження
руху змащувальних матеріалів в підшипникових вузлах металургійного устаткування. Одним з головних
завдань є визначення властивостей і стану змащувального матеріалу в підшипниковому вузлі. Знання
властивостей матеріалу безпосередньо у вузлі і умов роботи вузла дозволяють поліпшити умови і
продовжити час роботи машини, підвищити надійність і легкість технічного обслуговування.
Завдання:
1. Визначити експлуатаційні властивості сучасних пластичних мастил.
2. Розглянути конструкції і параметри роботи підшипникових вузлів.
3. Провести розрахунок руху змащувального матеріалу в підшипниковому вузлі.
4. Розробити правила вибору і дозування необхідної кількості змащувального матеріалу.
5. Визначити раціональний метод подачі мастила (періодичність, терміни заміни, напрям і якість).
Наукова новизна
На зміну використовуваних
раніше змащувальних матеріалів прийшли сучасні, якісніші. Саме цей факт є
підставою для перегляду існуючих норм дозування і методів подачі змащувального матеріалу
у підшипникові вузли металургійних машин. Проведені розрахунки і отримані на підставі
теоретичних і практичних досліджень результати допоможуть краще розібратися і зрозуміти всю
схему роботи підшипникового вузла з використанням сучасного пластичного мастила у важких
умовах роботи металургійних машин. Буде розроблений комплексний підхід до оцінки стану
підшипникового вузла на основі аналізу використовуваного пластичного мастила.
Основна частина
Пластичні мастила є мінеральним
маслом (до 90%), сполученим із загусником. Як загусник виступає мило. Мила - це солі вищих жирних
кислот, що включають іони лужних металів (кальцію, натрію). Робота пластичного мастила: загусник
(металеве мило) утворює місткість для масла (гратчастий волоконний каркас), заповнений маслом.
Витискування масла з цієї місткості відбувається під впливом механічних сил і температур. Залежно
від загусника розрізняють пластичні мастила: кальцієві, натрієві, літієві. Залежно від температури
краплепаденія розрізняють: низькотемпературні, середньотемпературні, високотемпературні. За
призначенням пластичні змащувальні матеріали бувають: антифрикційні, захисні, ущільнювальні.
Пластичні мастила характеризуються: температурою краплепаденія, консистенцією (пенетрацією),
змістом води, змістом вільних кислот або лугів, кількістю золи, кількістю механічних домішок.
Малюнок 1. Загальна схема основних
елементів створення конструкції, вузлів тертя
Показники властивостей
За своїми властивостями пластичні
(консистентні) мастила займають проміжне місце між твердими мастилами і маслами. В основному, мастила
складаються з двох компонентів: рідкої основи (мінеральні, рослинні, синтетичні і інші масла) і загусника
(тверді вуглеводні, різні солі високомолекулярних жирних кислот—мила, високодисперсні силікагелі і бентоніти,
інші продукти органічного і неорганічного походження). Крім того, в своєму складі вони містять присадки,
що поліпшують експлуатаційні характеристики. Нерідко до складу мастил вводять різних наповнювачів: графить,
дісульфід молібдену, порошкоподібні метали або їх оксиди, слюду і ін. Загусники, зокрема мила, в процесі
приготування мастила утворюють її тривимірний структурний каркас, в осередках якого утримується масло.
Завдяки наявності структурного каркаса мастила поводяться при невеликих навантаженнях як тверді тіла
(під дією власної ваги не розтікаються, утримуються на похилих і навіть вертикальних площинах), а під
впливом критичних навантажень, що перевищують міцність структурного каркаса, вони течуть подібно до
масел. Основними перевагами мастил є: здатність утримуватися в негерметичних вузлах тертя, працездатність
в ширших температурному і швидкісному діапазонах, краща змащуюча здатність, вищі захисні властивості від
корозії, працездатність у контакті з водою і іншими агресивними середовищами, велика економічність
застосування. До недоліків мастил слід віднести: погану охолоджуючу здібність, вищу схильність до
окислення, складність подачі до вузла тертя.
Механічна стабільність
Зміна об'ємно-механічних властивостей
мастил, наприклад межі міцності, в результаті механічної обробки і подальшого їх відпочинку називають
механічною стабільністю мастил. Механічна стабільність — важливий експлуатаційний показник властивостей
мастил,які вживаються особливо в шарнірах, плоских опорах, підшипниках ковзання, оскільки в цьому випадку
в роботу залучається весь запас мастила. Механічно нестабільне мастило, тобто що сильно руйнується і не
поновлює своїх первинних властивостей після зняття деформуючих навантажень, витече з такого вузла тертя
і приведе до передчасного його пошкодження. Механічну стабільність регламентує ДСТУ 19295—73.
Колоїдна стабільність
Здатність мастила під впливом зовнішніх
сил утримувати в осередках свого структурного каркаса масло називають колоїдною стабільністю. Колоїдну
стабільність визначають по ДСТУ 7142—74 у відсотках масла, що виділилося (що відпресувалося).
Колоїдно-стабільні мастила можуть не виділяти масла при зберіганні і експлуатації тривалий час. Невелике
виділення масла з мастила при його роботі у вузлі тертя завжди корисно, оскільки це сприяє поліпшенню
умов змазування деталей, що труться. Проте надмірно велике виділення масла з мастила (низька колоїдна
стабільність) приведе до витікання масла з вузла тертя і утворення в ній затверділої маси загусника,
тобто до порушення режиму змащування.
Випаровування визначається по ДСТУ 9566-74
у відсотках масла, що випарилося, при заданій температурі в строго регламентований час. Втрата масла через його
випаровування призводить до відносного підвищення змісту загусника в мастилі і, отже, збільшенню її межі
міцності, в'язкості, а також зміні інших експлуатаційних властивостей мастил.
Несуча здатність змащувальної плівки
Поняття несуча здатність (працездатність)
змащувальної плівки або змащувальна здатність мастила тісно пов'язана з питаннями тертя і зносу, а отже, із
законами, яким вони підкоряються. Це дуже важлива характеристика змащувального матеріалу, що акумулює сукупність
властивостей, визначуваних у граничних шарах контакту мастила з поверхнею металу, тобто в умовах граничного
тертя. Тут враховують критичну температуру руйнування змащувальної плівки, критичний тиск, який вона здатна
витримати, її пластифікуючу дію і адгезіонні сили, антифрикційні і протизносні властивості, протизадирні і
інші характеристики. У зв'язку з тим, що мастила в своєму складі завжди містять поверхнево-активні речовини,
не говорячи вже про спеціальні присадки, їх змащувальна здатність значно вища, ніж масла, на якому вони
виготовлені.
Зміст механічних домішок
Содержание механических примесей в смазках
определяют несколькими методами по ГОСТ 1036—75, растворяя смазку в углеводородных растворителях с последующей
фильтрацией растворителей и взвешиванием осадка на фильтре. В этом случае для разных смазок допускается
содержание отфильтровавшегося осадка не более 0,1-0,5%; ГОСТ 6479-73 предусматривает определение содержания
механических примесей, не растворимых в соляной кислоте, присутствие таких примесей, как правило, не допускается.
По ГОСТ 9270—59 с помощью микроскопа в тонком слое смазки, нанесенной на предметное стекло, определяют количество
и размер посторонних включений. Первые два метода используют в основном при оценке смазок общего назначения, а
последний—при определении механических примесей смазок, применяемых в прецизионных парах трения, приборных
подшипниках и т. п.
Конструкции узлов с пластичной смазкой
Розрізняють змазування з постійним мастилом на
весь термін служби підшипника і з періодичним додаванням і зміною мастила.
У першому випадку термін використання мастила
рівний або більше терміну служби підшипників або циклу ремонту машин із змонтованими в них підшипниками. До цього
виду змазування відносяться закриті підшипники, заповнені пластичним мастилом (малюнок 2).
Малюнок 2 - Закриті підшипники, заповнені пластичним
мастилом (червоним показано пластичне мастило)
Як стандартні змащувальні матеріали для закритих
підшипників використовуються пластичні мастила на основі літієвого загусника і мінерального масла з консистенцією
NLGI 2 або 3, що забезпечують роботу в діапазоні температур -20 ... 100 °С. У разі експлуатації в особливих
умовах застосовуються спеціалізовані пластичні мастила.
Якщо закритий підшипник працює в тяжких умовах
(високі температури, вода, пил), то доцільно застосовувати не тільки спеціалізовані пластичні мастила, але і
посилені конструкції вбудованих ущільнень, інакше в результаті змішування із сторонніми речовинами термін служби
стандартних пластичних мастил різко падає.Подача пластичного мастила в підшипниковий вузол і розміщення його
усередині вузла є найважливішою складовою ефективного змазування. Головну роль тут грає внутрішня конструкція
підшипникового вузла.
Малюнок 3 - Спеціальна захисна шайба із збільшеною
кишенею для мастила
Подача пластичного мастила в підшипниковий вузол
і розміщення його усередині вузла є найважливішою складовою ефективного змазування. Головну роль тут грає внутрішня
конструкція підшипникового вузла.
Якщо в корпусі підшипникового вузла є отвір
для подачі мастила до підшипника, коли необхідні збільшені інтервали між додаванням мастила і перекачування
змащувального матеріалу, то при великих окружних швидкостях кількість пластичного мастила з боку подачі в підшипник
може виявитися недостатнім, оскільки швидко витікатиме під дією відцентрового ефекту (малюнок 4, а).
Для запобігання цього застосовуються відбивні кільця (малюнок 4, би і в), що встановлюються по наружному
діаметру підшипника. Залежно від кількості мастила, яка повинна бути постійно присутньою в підшипнику
діаметр відбивного кільця може бути разним.
Рисунок 4. Малюнок 5 - Відбивні кільця, що
встановлюються по зовнішньому діаметру підшипника
Також можливі і складніші конструкції, особливо,
коли необхідно забезпечити в підшипнику постійну заміну відпрацьованого мастила на нове і виключити попадання забруднень
(малюнок 5).
Малюнок 5 - Деякі конструкції систем подачі пластичного
мастила, що забезпечують в підшипнику постійну заміну відпрацьованого мастила, а також що виключають попадання
в підшипник забруднень
Висновок
      В процесі виконання роботи був проведений аналіз існуючих змащувальних
матеріалів і конструкцій підшипникових вузлів. Також було розглянуто поведінку пластичного мастила в підшипниковому
вузлі металургійної машини у зв'язку з утворенням застійних зон. В результаті будуть прийняті рекомендації по
дозуванню необхідного для використання мастила і способам його подачі в підшипниковий вузол.
Література
      1. Седуш В.Я. Надежность,ремонт и монтаж металлургических машин:Учеб./Рец.А.В.Гордиенко;ДПИ.-К.:УМК ВО,1992.-368с.
      2. Гедык П. К., Калашникова М.И. Смазка металлургического оборудования. Издательство «Металлургия», 1971, 376 с.
      3. Механическое оборудование сталеплавильных цехов / Левин М.З., Седуш. В.Я., Мачикин В.И. и др. - Киев; Донецк: Вища шк., 1985. 165 с.
      4. Трение, изнашивания и смазка : Справочник. В 2-х кн./Под. ред. И. В. Крагельского, В.В. Алисина. – М.: Машиностроение, 1978 – кн. 400с., ил.
      5. Основы трибологии (трение, износ, смазка): Учебник для технических вузов. 2-е изд. переработ. и доп./ А. В, Чичинадзе, Э. Д. Браун, Н. А. Буше и др.; Под общ. ред. А. В. Чичинадзе. - М.: Машиностроение, 2001.- 664 с., ил.
      6. http://www.snr.com.ru/e/lubrications_1_5.htm
      7. http://www.masters.donntu.ru/2000/mehf/galkyn/andreismaz.html