Автобиография | Библиотека | Ссылки |
Отчет о поиске | Достопримечательности Узбекистана
АКТУАЛЬНОСТЬ ТЕМЫ
К числу основных проблем современного машиностроения относится получение на этапе изготовление деталей машин таких характеристик качества, которые соответствовали бы требованиям к эксплуатационным свойствам. При этом в процессе обработки необходимо исключить образование причин отказов и научиться участвовать в формировании заранее заданных эксплуатационных свойств. Известно, что основной причиной выхода из строя машин является не их поломка, а износ подвижных сопряжений под действием сил трения. Износостойкость трущихся пар, особенно в начальный период их работы, в существенной степени определяется микрорельефом поверхностных слоев, полученных в результате механической обработки, микротвердостью и остаточными напряжениями. Наиболее сложно управлять процессом формирования эксплуатационных свойств деталей машин, изготовляемых из материалов, склонных к фазовым превращениям в процессах механической обработки, отличающихся высокой теплосиловой напряженностью. К числу таких процессов относят, прежде всего, шлифование, в зоне которого возникают мгновенные контактные температуры, достигающие 800-1000 0С, и давления, превышающие в 2-3 раза предел текучести материала.
ЦЕЛЬ И ЗАДАЧИ МАГИСТЕРСКОЙ ДИССЕРТАЦИИ
Цель – повысить качество абразивной обработки тонкостенных изделий и разработать технологическое обеспечение, которое даст возможность обработать тонкостенные изделия.
Задачи:
- Обзор средств технологического снаряжения, которые используются при внутреннем шлифовании отверстий в деталях типа втулок.
- Обзор и анализ путей решения проблем обеспечения точности размеров в деталях типа втулок и качества поверхностей отверстий.
- Исследование процесса взаимодействия шлифовальный круга с обрабатываемой заготовки при внутреннем шлифовании.
- Формулировка перечня признаков и критериев, по которым разрабатывается система технологической оснастки при внутреннем шлифовании отверстий в деталях типа втулок.
- Разработка конструкции средств и элементов технологического оснащения, которые могут применяться при внутреннем шлифовании отверстий в деталях типа втулок.
ОСНАСТКА ПРИМЕНЯЕМАЯ ПРИ ВНУТРЕННЕМ ШЛИФОВАНИИ
На внутришлифовальных станках применяют двух-, трех- и четырехкулачковыепатроны с ручным и механизированным приводом зажима. В двухкулачковых самоцентрирующих патронах закрепляют различные фасонные отливки и поковки; кулачки таких патронов, как правило, предназначены для закрепления только одной детали. В трехкулачковых самоцентрирующих патронах закрепляют заготовки круглой и шестигранной формы или круглые прутки большого диаметра. В четырехкулачковых самоцентрирующих патронах закрепляют прутки квадратного сечения, а в патронах с индивидуальной регулировкой кулачков - детали прямоугольной или несимметричной формы.Наиболее широко применяют трехкулачковый самоцентрирующий патрон (рисунок1). Кулачки 1, 2 и 3 патрона перемещаются одновременно с помощью диска 4. На одной стороне этого диска выполнены пазы (имеющие форму архимедовой спирали), в которых расположены нижние выступы кулачков, а на другой - нарезано коническое зубчатое колесо, сопряженное с тремя коническими зубчатыми колесами 5. При повороте ключом одного из колес 5 диск 4 (благодаря зубчатому зацеплению) также поворачивается и посредством спирали перемещает одновременно и равномерно все три кулачка по пазам корпуса 6 патрона. В зависимости от направления вращения диска кулачки приближаются к центру патрона или удаляются от него, зажимая или освобождая деталь. Кулачки обычно изготовляют трехступенчатыми и для повышения износостойкости закаливают. Различают кулачки крепления заготовок по внутренней и наружной поверхностям; при креплении по внутренней поверхности заготовка должна иметь отверстие, в котором могут разместиться кулачки.
Рисунок 1- трехкулачковый самоцентрирующий патрон
Кулачковые патроны могут оснащаться механизированным приводом - тяговым или встроенным. Патроны с тяговым приводом имеют зажимные элементы, связанные цельными или пустотелыми тягами с пневмо- или гидроцилиндром. На (рисунке2) представлена конструкция двухкулачкового рычажного патрона со сменными кулачками 14, которые предварительно устанавливаются по заготовке (относительно оси вращения) путем смещения сухарей 12 (скрепленных с кулачками 14 винтами 13) по пазам в ползунах 11. Ползуны 11 перемещаются к центру патрона рычагами 10, которые при движении упора 15 (вместе с тягой 3) поворачиваются вокруг оси 9 в корпусе 8. При повороте рычаги 10 опираются на поверхности 7. Перемещение ползунов 11 (вместе с кулачками 14) от центра патрона производится конической поверхностью упора 15 при обратном движении тяги 3, связанной с упором посредством направляющей втулки 6 и соединительных деталей 2, 4 и 5. Патрон крепится к станку винтами 1.
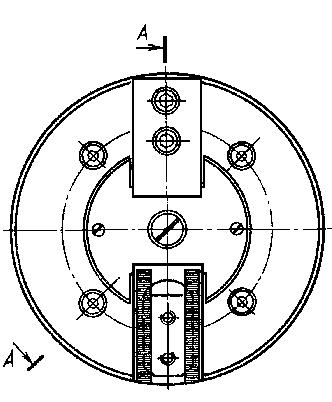
Рисунок 2- Кулачковые патроны с механизированным приводом
Четырехкулачковый патрон с независимым перемещением кулачков (рисунок 3) состоит из корпуса 1, в котором выполнены четыре паза, в каждом пазу смонтирован кулачок 4 с винтом 3, используемым для независимого перемещения кулачков по пазам в радиальном направлении. От осевого смещения винт 3 удерживается сухарем 2. При повороте кулачков на 180 градусов патрон может применяться для крепления заготовок по внутренней поверхности. На передней поверхности патрона нанесены концентричные круговые риски (расстояние между рисками 10-15 мм), с помощью которых кулачки выставляются на одинаковом расстоянии от центра патрона.
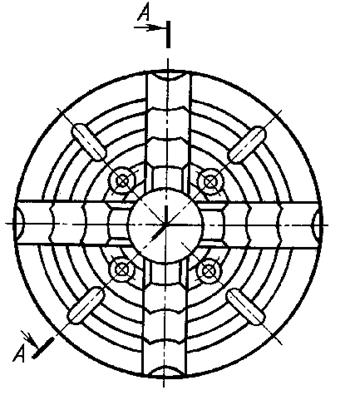
Рисунок 3 -Четырехкулачковый патрон с независимым перемещением кулачков
В массовом и серийном производстве целесообразно применять мембранные патроны (рисунок 4), обеспечивающие более точную установку обрабатываемой детали
Рисунок 4- Схемы наладки для шлифования отверстия и торца: а-мембранный патрон; б- схема установки зубчатого колеса на роликах; в- схема измерения обрабатываемого отверстия автокалибром.
 Мембранные патроны применяют при шлифовании колец шарикоподшипников (рисунок 5). Они отличаются большим количеством кулачков, расположенных по окружности , что способствует более точному центрированию заготовки.
Рисунок 5- Мембранный патрон с винтовым центрированием обрабатываемой детали: 1-планшайба; 2- мембрана; 3- упоры; 4-винты; 5- обрабатываемая деталь; 6- гайка; 7- кулачки
Шлифование на жестких опорах (башмаках) применяют для обработки отверстий во втулках, имеющих шлифовальный торец. Заготовка лежит на жестких опорах А и Б (рисунок 6) и поджимается плоским шлифовальным торцом к вращающемуся электромагнитному патрону на шпинделе передней бабки. Сила трения между контактирующими поверхностями патрона и заготовки вращает последнюю. Заготовка на опорах А и Б располагается эксцентрично относительно оси вращения шпинделя. Этим создается проскальзывание между планшайбой и заготовкой , необходимое для поджатия наружной базы и обеспечивает равностенность втулки. Шлифование на жестких опорах широко применяют при обработке колец шарикоподшипников.
Рисунок 6. Схема внутреннего шлифования на жестких опорах: 1- обрабатываемая деталь; 2- ведущая планшайба;
ПОВЫШЕНИЕ ТОЧНОСТИ И КАЧЕСТВА ОБРАБОТКИ ПРИ ВНУТРЕННЕМ ШЛИФОВАНИИ ПУТЕМ СТАБИЛИЗАЦИИ СИЛОВЫХ ПАРАМЕТРОВ ПРОЦЕССА.
 Повышение требований к точности линейных и угловых размеров, качеству поверхности рабочих элементов деталей машин, ужесточение допусков формы и расположения поверхностей в последнее время привело к расширению области применения различных видов абразивной обработки, из которых наиболее распространенным является шлифование. Для окончательной обработки внутренних поверхностей вращения, в случае невозможности или нецелесообразности использования осевого инструмента, основным методом обеспечения точности размеров 5-6 квалитета и шероховатости поверхности Rа = 0,4-1,6 мкм является внутреннее шлифование [7]. Однако внутреннее шлифование характеризуется рядом особенностей, отличающих его от других видов шлифования и влияющих на получение заданных показателей точности и качества обработанной поверхности. Выделим основные из этих особенностей :
— малая жесткость шпинделя шлифовальной головки;
— относительно малые размеры шлифовального круга по сравнению с обрабатываемой поверхностью;
—следствие интенсивного износа и засаливания шлифовального инструмента применение мягких кругов с открытой структурой;
— большая площадь зоны контакта шлифовального круга с обрабатываемой заготовкой;
— затрудненные условия подвода смазочно-охлаждающей жидкости в зону резания.
Малые жесткость шпинделя шлифовальной головки и размеры шлифовального круга вынуждают на операциях внутреннего шлифования снимать минимальные припуски. Несмотря на это, при колебаниях значений радиальной составляющей силы резания наблюдаются отклонения размеров обрабатываемых отверстий от настроечных значений, значительные погрешности формы обрабатываемой поверхности в продольно и поперечном сечении.
В то же время из-за относительно быстрой потери режущей способности мягкого шлифовального круга в условиях обработки на высоких скоростях резания (35 м/с и более), больших размеров зоны контакта круга с заготовкой внутреннее шлифование сопряжено с опасностью возникновения в контактной зоне высоких мгновенных температур, способных вызвать структурно-фазовые превращения в поверхностном слое заготовки. Последнее, как правило, сопровождается образованием в этом слое прижогов, нежелательных растягивающих технологических остаточных напряжений и даже появлением микротрещин [8].
Воздействие перечисленных факторов, оказывающих влияние на точность и качество обработки при внутреннем шлифовании, обусловлено в первую очередь нестабильностью значений составляющих сил резания в процессе обработки, т.е. нестационарностью этого процесса. В связи с этим важной научно-практической задачей является поиск эффективных путей стабилизации силовых параметров процесса внутреннего шлифования.
Укажем вначале те условия, без соблюдения которых не удастся добиться точности микро и макрогеометрии обработанной поверхности и задача стабилизации силовых параметров процесса обработки будет неразрешимой:
— геометрическая точность и состояние внутришлифовального станка должны соответствовать установленным нормам точности и жесткости;
— установка и закрепление обрабатываемой заготовки должны обеспечивать необходимую жесткость системы СПИД;
— выбор элементов режима шлифования должен соответствовать заданным параметрам точности в качества обработки и не приводить к нарушению нормальной работы станка;
— характеристика шлифовального круга должна соответствовать обрабатываемому материалу и заданным показателям и качества обработки.
При соблюдении перечисленных условий появляется техническая возможность добиться стабильности значений силовых показателей процесса.
для определения пути достижения поставленной цели воспользуемся выдвинутым П.Е.Дьяченко и Л.А.Глейзером на основании изучения закономерностей процесса шлифования предположением о том, что фактором, определяющим ход этого процесса, является радиальное давление круга на изделие. От величины радиального давления непосредственно зависят: наличие прижогов на шлифуемой поверхности; производительность, износ и затупление шлифовального круга. На основании этой гипотезы был предложен способ шлифования с заданной радиальной силой прижима шлифовального круга к изделию (шлифование по упругой схеме).
При плоском шлифовании по упругой схеме условия обработки определяются режимами резания: скоростью круга Vк, скоростью деталиVд, продольной подачей Sп, и силой поджима рабочей поверхности круга к заготовке Рn, которая уравновешивается радиальной составляющей силы резания Рy,. Так как с помощью соответствующих нагрузочных устройств обеспечивается постоянство величины сил Рn=Рy, на протяжении всего времени обработки, то изменение параметров рабочей поверхности круга в процессе шлифования приводит к уменьшению глубины шлифования t и, соответственно, к уменьшению производительности обработки, сохраняя, однако, при этом стабильными показатели качества обработанной поверхности [9].
По сравнению со шлифованием по жёсткой схеме шлифование с определенным радиальным давлением представляет собой достаточно устойчивый процесс, обладающий большей степенью детерминированности. Тем самым появляется возможность перейти от нестационарного процесса к квазистационарному. Шлифование по упругой схеме с заданной силой прижима Рn шлифовального круга к заготовке позволяет исключить влияние на совокупность силовых и тепловых параметров процессам непостоянства припуска, нестабильности физико-механических свойств материала детали и изменения режущей способности шлифовального круга за период его стойкости. Применение процесса шлифования по упругой схеме обеспечивает снижение силовой и термической напряженности процесса обработки, повысить точность микро и макрогеометрии обработанной поверхности, качество поверхностного слоя обработанной детали. Постоянная нормальная сила прижима заготовки к кругу может быть реализована с помощью различных конструктивных решений, среди которых наиболее часто используются: создание постоянной силы с помощью пружины, с помощью рычажного механизма и путём применения гидравлического устройства. Эта сила может использоваться как критерий управления процессом внутреннего шлифования в системах активного контроля.
Упругая схема обработки при внутреннем шлифовании может быть применена как непосредственно на технологической операции, так и для определения зависимости текущей режущей способности круга от времени, которая проявляется в виде уменьшения в ходе процесса обработки фактической глубины резания при условии постоянства остальных элементов режима. Соответствующие значения поперечной подачи могут быть использованы для программирования обработки на внутришлифовальных станках с ЧПУ.
ВЛИЯНИЕ ЖЕСТКОСТИ СИСТЕМЫ СПИД НА ВЫБОР ЧАСТОТЫ ВРАЩЕНИЯ КРУГА ПРИ ВНУТРЕННЕМ ШЛИФОВАНИИ
На внутришлифовальных станках оправка, как одно из звеньев технологической системы СПИД, обладает ограниченной жесткостью, что - может явиться причиной возникновения значительных колебаний кругов. Известно, что колебания инструмента, которые в значительной степени определяются частотой их вращения, в процессе резания оказывают существенное влияниё на точность геометрической формы и качество обработанной поверхности [1, 2], а также на работоспособность инструмента[3].
В работе [4] указывается о принципиальной возможности выбора частоты вращения круга в зависимости от параметров жестокости системы СПИД, но конкретных путей решения этого вопроса не указывается.
В данной работе сделана попытка аналитически определить оптимальную частоту вращения шлифовального круга при внутреннем шлифовании в зависимости от жесткости технологической системы СПИД.
При шлифовании внешние нагрузки на режущих зернах характеризуются и кратковременностью действия. Они являются быстроприлагаемыми и иногда их относят к ударным нагрузкам [5], что дает основание для использования решений теоретической механики виброударных систем к рассматриваемому процессу.
Для теоретического анализа представим динамическую систему внутришлифовального станка в виде механической модели [6]. Динамическая система станка состоит из двух колебательных систем; шлифовальный круг— задняя бабка и обрабатываемая заготовка передняя бабка станка.
Принимаем, что массы системы перемещаются только горизонтально без трения, считаем массы бабок станка большими а их перемещения приравниваем к нулю. Так как модуль упругости детали из твердого сплава ВК8 равен 60 10 МПа, что значительно больше модуля упругости шлифовального круга, долей деформации детали в общей деформации контактов можно пренебречь. Ввиду малой поверхности контакта круга с обрабатываемой деталью можно рассматривать их как идеальные, (нулевые массы) недемпфирующие пружины.
При рассмотрении первой колебательной системы массой шлифовального круга пренебрегаем ввиду малости по сравнению с массой бабки станка.
Основное влияние на точность обработки отверстия при шлифовании оказывает горизонтальная составляющая усилия резания Рy, обуславливающая смещение оси круга. Она в 3—4 раза больше составляющей Рz и при шлифовании постоянно изменяется, так как на нее влияют вынужденные колебания технологической системы СПИД. Главными источниками последних при алмазном внутреннем шлифовании изделий из твердых сплавов, обрабатываемых после спекания, являются некруглость и дисбаланс спеченной заготовки, а также шлифовального круга.
В связи с малой массой шлифовального круга (15—20 г) и небольшой частотой вращения обрабатываемой детали (5—6с-1) центробежные силы, возникающие из-за их дисбаланса, не учитываем.
Шлифовальный круг и обрабатываемая деталь, выведенные из положения равновесия, могут колебаться совместно. При этом движение системы описывается обычным линейным дифференциальным уравнением и она совершает гармонические колебания с частотой, не зависящей от начального возмущения,
где С1, С2 — приведенные жесткости колебательных систем круга и обрабатываемой детали. Однако при определенной величине начального возмущения, либо при определенных соотношениях между параметрами системы и параметрами периодического возбуждения, сила начального натяга оказывается недостаточной для поддержания контакта между обеими частями системы. Появляется возможность возникновения разрывов системы, которые характеризуются соударениями масс.
Интересующее нас условие возникновения разрыва имеет вид:
где Нк1 — максимальная некруглость формы шлифовального круга или обрабатываемой детали,
Ру— радиальная составляющая силы резания.
Анализ выражения (2) позволяет определить пути уменьшения возможности разрывов системы при внутреннем шлифовании. Так, при равенстве частот собственных колебаний отдельных частей системы разрыв контакта круга с деталью невозможен, а шлифование при режимах обработки, обеспечивающих увеличение Рy, уменьшает возможность возникновения разрыва, что должно способствовать стабилизации процесса шлифования. Однако эти способы регулирования не могут гарантировать шлифование без разрывов, так как возможности их ограничены технологической системой СПИД.
Таким образом, становится очевидным, что данные колебательные системы необходимо рассматривать с учетом разрывов.
Исходя из указанного, перейдем к рассмотрению колебательной системы станка с учетом возможных разрывов. Предположим, что в результате действия колебаний установилось периодическое движение, сопровождающееся соударениями круга с деталью, частота которых равна или кратна частоте вынужденных колебаний. Диссипацию энергии при соударениях учитываем, считая, что коэффициент восстановления при ударе может принимать любые значения в пределах 0<R<1.В интервалах между соударениями движение круга и детали описывается уравнениями:
где К1 — частота собственных колебаний круга,
К2 —частота свободных колебаний детали,
φ— фазовый сдвиг внешнего перемещения с момента соударения
ω— частота вращения круга или детали,
Н — величина натяга системы шлифовальный круг обрабатываемая деталь.
В процессе решения уравнений движения системы при опрелелении постоянных интегрирования использовано уравнение удара [б].
Суммарная величина перемещений шлифовального круга при возмущении системы из-за некруглости формы круга имеет вид:
где
Анализ этого уравнения показывает, что перемещения системы будут уменьшаться со снижением коэффициента восстановления контактируемых тел при ударе. В идеальном случае процесс шлифования будет стабилизироваться при нулевом значении этого перемещения, что выполнимо при условии:
Для проверки сделанного вывода применительно к конкретным условиям рассчитана оптимальная частота вращения шлифовального круга для станка мод. 3А227. Исходные данные для расчета по формуле (5); С1=6·105Н/М; С2=45·105 Н/м; m1= 1,2 кг; m2=25 кг.
Таким образом, ?1=538 с-1. Оптимальная частота вращения круга на указанном станке составляет 5570 об/мин.
Проведенный теоретический анализ показал, что для повышения эффективности внутреннего шлифования целесообразно определение рациональной частоты вращения круга с учетом жесткости системы СПИД, что подтвердилось проведенными исследованиями в работе [7].
ВЫВОДЫ
Современное машиностроение и приборостроение характеризуются широким применением конструкционных материалов, обладающих специальными физико-механическими свойствами.
Широкое использование материалов со специальными свойствами, высокие требования к точности размеров и геометрической формы, сложность конструкции деталей часто приводят к тому, что традиционные методы формообразования поверхностей деталей резанием оказываются малоэффективными, а иногда и неприменимыми.
В машиностроении непрерывно растет применение деталей из металлических и неметаллических материалов, получаемых штамповкой, прессованием, прокаткой, точным литьем и т. д., что вызывает необходимость создания большого количества штампов, литейных форм, прокатных валков, матриц, пресс-форм. Обычно такая оснастка имеет сложную форму и конструкцию, ее изготовление трудоемко и требует применения труда высококвалифицированных слесарей-лекальщиков и значительных материальных затрат.
Главная цель финишного или тонкого шлифования – получить требуемую конечную форму и точность. Шлифовальные круги периодически правятся (очищаются), что обусловлено необходимостью поддержания остроты кромок, удаления налипания металла на зерна или засаливания шлифовального круга (когда металлические стружки занимают пространство между зернами) и чтобы поддерживать цилиндричность шлифовального круга
Для повышения эффективности внутреннего шлифования целесообразно определение рациональной частоты вращения круга с учетом жесткости системы СПИД
СПИСОК ИСПОЛЬЗУЕМОЙ ЛИТЕРАТУРЫ
- Колен К. с., Горчаков л.М. Точность обработки и режимы резания.— М.; Машиностроение, 1976.— 144 с..
- Пономарев А. С., Митин В. И. Синтез СПИД как вибрационной системы по заданному ограничению на максимум амплитуды колебаний режущего инструмента// Резание и инструмент.— 1972.— Вып. 5, с. 135—139.
- Шульман П. А.. Созин Ю. И., Колесниченко Н. Ф. и др. качество поверхности, обработанной алмазами. Киев; Техника, 1972—118 с.
- Урывский Ф. П., Маркунин Е. М., Валандин Г. П. Вибрации при внутреннем шлифовании и волнистость обработанной поверхности// Исследование обрабатываемости жаропрочных и титановых сплавов.— Куйбышев._ 1976.— Вып. 4.С. 110—119
- , Попов С. А., Малевский Н. П., Терещенко Л.М, Алмазноабразивная обработка металлов и твердых сплавов. М,; Машиностроение.
- Кобринский А. Е., Кобринский А. А. Виброударные системы.— М.; Наука, 1973.— 591 с.
- Ковыженко Г. И. Выбор скорости алмазного круга при внутреннем шлифовании твердого сплава ВК8// сверхтвердые материалы.— 1979.— К 3. С. 63—4.
- Акимов В.Л. Внутреннее шлифование. Л.: Машиностроение, 1986.— 125 с.
- Худобин Л.В. Минимизация засаливания шлифовальных кругов/ Л.В.Худобин, А.Н.Унянин. — Ульяновск: УлГТУ, 2007. — 298 с.
- Матюха П.Г. Анализ способов стабилизации технологических показателей шлифования по упругой схеме / П.Г. Матюха, В.В.Полгавец // Вiсник Iнженерноi академii Украiни. № 2. —2002. — С. 60-65.
Рис7.- Имитация внутреннего шлифования(19 картинок,9 кадров,интервал 0,2 с, 47,3 кБ )
Автобиография
Электронная
библиотека Перечень ссылок Отчёт
о поиске Достопримечательности Узбекистана
|