РАСЧЕТ ЭНЕРГОСИЛОВЫХ ПАРАМЕТРОВ СИСТЕМ КОВШОВЫХ ЗАТВОРОВ
С.П. ЕРОНЬКО Донецкий национальный технический университет, НПО «ДОНИКС»
Источник: "Металлургия и горная промышленность". - 2006. - № 5. - с.62-63.
Увеличение объемов стали, производимой по прогрессивной технологии, включающей выплавку полупродукта в электродуговой печи или кислородном конвертере с последующей его доводкой до нужной кондиции на установках "ковш-печь", а также повышение серийности непрерывной разливки металла на современных высокоскоростных МНЛЗ явились главными причинами проведения коренной модернизации парка разливочных ковшей, связанной с оснащением их затворами последнего поколения [1, 2].
Существенные изменения, внесенные в последовательность операций по подготовке к работе ковшовых затворов, многообразие их конструктивного исполнения и применение в них огнеупорных плит нового класса, имеющих относительно малую толщину (30 – 35 мм), требуют пересмотра некоторых положений, составляющих основу методов расчета шиберных систем [3].
Как известно, главными силовыми факторами, определяющими нагрузки, действующие в конструктивных элементах скользящего затвора, а также энергетические характеристики его привода (мощность электродвигателя или давление рабочей жидкости в гидроцилиндре при заданном диаметре его поршня), являются требуемая сила прижатия подвижной огнеупорной плиты и сопротивление ее перемещению во время работы разливочного устройства [4, 5].
Технологическая нагрузка на привод скользящего затвора, в первую очередь, зависит от конструктивного исполнения его узла, обеспечивающего прижатие подвижного огнеупорного элемента к неподвижному. В эксплуатируемых в настоящее время шиберных системах, разработанных зарубежными и отечественными специалистами, подвижная металлическая обойма перемещается либо по направляющим полозьям, изготовленных из износостойкой стали, либо установлена на тела качения, которые позволяют снизить износ контактных поверхностей в кинематических парах и действующие в них силы сопротивления. При этом сила, сжимающая огнеупорные плиты, возникает под действием блоков сжатых тарельчатых или витых пружин, а также может развиваться за счет контролируемой затяжки специальных болтов [6].
Силу, необходимую для перемещения подвижной обоймы с огнеупорной плитой при различных схемах ее опорного узла, показанных на рис. 1, определяют по следующим формулам.
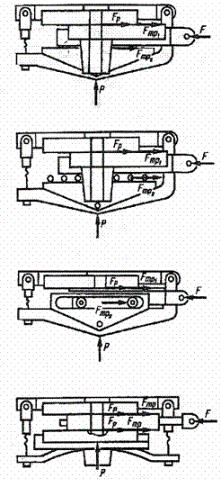
Рис. 1. Схемы нагружения подвижной обоймы
а – двухплитный затвор с опорными поверхностями скольжения;
б – двухплитный затвор с линейными роликоподшипниками;
в – двухплитный затвор с роликовыми опорами; г – трехплитный
затвор.
Для двухплитных затворов:
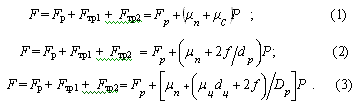
Для трехплитного затвора
(4)
В этих выражениях Fр – сила, необходимая для срезания образовавшейся в канале затвора металлической корки; Fтр1 – сила трения между рабочими поверхностями плит; Fтр2 – сила сопротивления в опорных узлах; mп – коэффициент трения скольжения между рабочими поверхностями огнеупорных плит; m с – коэффициент трения скольжения между подвижной металлической обоймой и ее опорой; mц – коэффициент трения скольжения между цапфой и роликом; f – коэффициент трения качения; dц – диаметр цапфы; dр и Dр – соответственно диаметры ролика, установленного в линейный сепаратор и размещенного на цапфе; Kн – коэффициент, учитывающий дополнительную нагрузку из-за трения подвижной металлической обоймы трехплитного затвора о направляющие при вталкивании подвижной плиты; Р – сила прижатия огнеупорных плит.
В опубликованных ранее работах [5, 7] значение силы FP принимали по опытным данным в пределах 27-44 кН, а силу прижатия плит рассчитывали из условия допустимых изгибных деформаций металлических обойм затвора и продольных деформаций болтов, прижимающих его подвижную обойму.
Как оказалось, такой подход не отвечает в полной мере условиям работы остальных элементов систем скользящих затворов. Многолетний опыт их эксплуатации показал, что механическое разрушение металлических деталей разливочного устройства происходило крайне редко и к тому же из-за скрытых дефектов или нарушения технологии их изготовления, а причиной большинства аварийных ситуаций был выход из строя менее прочных огнеупорных плит.
Поэтому значение силы прижатия керамических частей затвора, по нашему мнению, должно составлять (0,7 - 0,8)Рдоп , рассчитанному из условия возникновения в огнеупорных плитах предельно опасных напряжений. В соответствии с ранее полученными результатами физического и математического моделирования [8-10], а также экспериментальных исследований напряженно-деформированного состояния керамических плит ковшовых затворов [11], допустимые значения силы прижатия, при которых может произойти нарушение целостности огнеупорного изделия, можно определить, используя следующие зависимости.
Для двухплитной шиберной системы
(5)
Для трехплитной шиберной системы
(6)
Здесь Впл, Нпл, Lпл – ширина, высота и длина огнеупорной плиты
соответственно; lх – относительное перекрытие плит, равное отношению хода подвижной плиты к ее длине; [s] – допускаемое напряжение материала плиты.
Для определения значений силы Fp можно воспользоваться зависимостью, приведенной в работе [12],
(7)
где к – коэффициент, равный отношению максимального сопротивления
срезу к пределу прочности стали;
[s]в – предел прочности стали, закристаллизовавшейся на стенках
разливочного канала;
Sp – площадь поперечного сечения срезаемой металлической корки.
Площадь поперечного сечения срезаемой металлической корки в канале шиберного затвора
(8)
Здесь Dк – диаметр канала затвора на участке контакта рабочих поверхностей огнеупорных плит, d – толщина образующейся металлической корки.
В соответствии с рекомендациями работ [6, 12, 13], значения величин, входящих в уравнения (1) - (8), при расчетах силы страгивания подвижной обоймы затвора можно принять: sп = 0,3 – 0,7; f = 0,010 – 0,015 см; кн = 1,5 – 2; Р = (0,7 – 0,8)Рдоп ; к = 0,6; sв = 300 – 500 МПа; d = 3 – 5 мм.
Расчетные значения силы страгивания F подвижной обоймы затвора используют для определения энергосиловых параметров его привода.
В качестве примера на рис.2 приведена диаграмма нагрузок, действующих на подвижную обойму затвора во время его закрытия при использовании магнезитовых плит длиной 370 мм, шириной 200 мм, с диаметром отверстия 50 мм и допускаемом напряжении материала [s]= 8 – 24,5 МПа.

В соответствии с полученным графиком, в начальный момент страгивания подвижной обоймы на нее действует сила сопротивления, в два раза превышающая свое значение на участке установившегося движения. Указанная неравномерность силы сопротивления, приложенной к подвижной обойме затвора, по-разному сказывается на нагрузке, действующей на привод затвора в зависимости от его типа.
Поскольку у затворов с гидравлическим или пневматическим приводом подвижная обойма связана с силовым цилиндром непосредственно или через двуплечий рычаг, характер изменения нагрузки на привод будет в точности таким же, как и у силы сопротивления F. Поэтому наличие пикового значения нагрузки при закрытии затвора может вызвать стопорение гидравлического или пневматического привода, что часто наблюдается на практике.
В приводе скользящих затворов обычно используют гидроцилиндры двухстороннего действия с односторонним выходом штока. Поскольку в процессе работы таких цилиндров усилия, развиваемые при выталкивании и втягивании штока, разнятся на 15 – 17 %, диаметр их поршня рассчитывают из условия преодоления максимальной технологической нагрузки для случая втягивания штока. Одновременно с этим следует учитывать разницу скоростей движения штока в зависимости от направления его перемещения.
Необходимость в принятии указанных мер отпадает при замене поршневого гидроцилиндра двухплунжерным. Усовершенствованный гидропривод затвора (рис. 3) состоит из двух плунжерного цилиндра, неподвижно закрепленного на монтажной плите соосно с затвором и помещенного внутрь рамки, имеющей возможность перемещения в направляющих и посредством оси связанной с подвижной обоймой затвора. Продольный размер проема рамки равен длине плунжерного цилиндра, когда один из его плунжеров полностью выдвинут, а другой полностью задвинут. Причем ход каждого из плунжеров равен ходу подвижной обоймы затвора. При поочередной подаче под давлением рабочей жидкости в одну из камер цилиндра соответствующий плунжер воздействует своей торцевой частью на перемычку рамки, перемещая ее вместе с подвижной обоймой затвора из одного крайнего положения в другое. Второй плунжер в это же время под воздействием противоположной перемычки рамки вдавливается в полость своей камеры и вытесняет из нее рабочую жидкость. Проем рамки закрыт крышкой (условно не показана), благодаря чему поверхность плунжеров во время работы привода защищена от попадания абразивной пыли и не подвергается интенсивному износу [14].
Механический привод шиберного затвора менее чувствителен к перегрузкам, возникающим в момент разрушения движущейся огнеупорной плитой корки металла, застывшего на стенках канала ковшового затвора. Благодаря специфическому характеру силовых процессов, протекающих при взаимодействии звеньев кривошипно-шатунного механизма, входящего в состав электромеханического привода затвора, вероятность стопорения последнего очень низка, так как при положениях механизма, близких к конечным, плечо силы сопротивления, действующей на шатун, относительно кривошипа очень мало, а момент, препятствующий его повороту, значительно меньше номинального момента, развиваемого приводным двигателем. В связи с этим пиковая нагрузка на него в начальный период закрытия затвора не передается, что способствует повышению надежности работы всей системы разливочного устройства ковша.
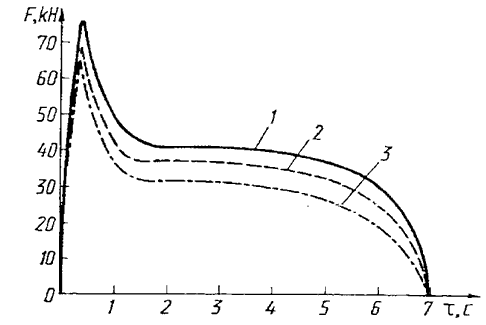
Вместе с этим к недостаткам такого привода следует отнести наличие расклинивающей силовой нагрузки, действующей на элементы конструкции скользящего затвора из-за отклонения продольной оси шатуна на определенный угол от направления поступательного перемещения подвижной обоймы. Для уменьшения боковой составляющей силы, передаваемой шатуном, в состав электромеханического привода, как правило, дополнительно вводят двуплечий рычаг и тягу или прямило, что влечет увеличение габаритов шиберной системы. В результате поиска технического решения, направленного на устранение указанного недостатка, разработан вариант модернизированной конструкции электромеханического привода (рис. 4). Он содержит электродвигатель, кинематически связанный с быстроходным валом 1 редуктора, включающего корпус 2 коробчатой формы с двумя внутренними продольными стенками 3. В стенках размещены подшипниковые опоры зубчатых передач 4 и тихоходного одноколенного вала 5, снабженного шатуном 6. На шейках 7 этого вала неподвижно закреплены зубчатые колеса 8, находящиеся во внутреннем зацеплении с зубчатыми венцами 9, выполненными во внутренних продольных стенках 3. При этом шейки установлены эксцентрично с возможностью вращения в дисках 10, снабженных зубчатыми венцами и размещенных в опорах, выполненных во внутренних продольных стенках соосно с зубчатыми венцами внутреннего зацепления. Причем радиус кривошипа одноколенного вала 5 и эксцентриситет его шеек относительно осей дисков 10 равны радиусу делительных окружностей зубчатых колес 8, который в свою очередь равен половине радиуса делительной окружности зубчатых венцов 9 внутреннего зацепления. Благодаря таким соотношениям геометрических параметров элементов редуктора привод функционирует по принципу действия гипоциклоидального механизма, что обеспечивает прямолинейное возвратно-поступательное движение шатуна 6 и исключает возможность появления нагрузок на связанную с ним подвижную. обойму затвора 11, способных вызвать образование зазора между рабочими поверхностями огнеупорных плит [15].
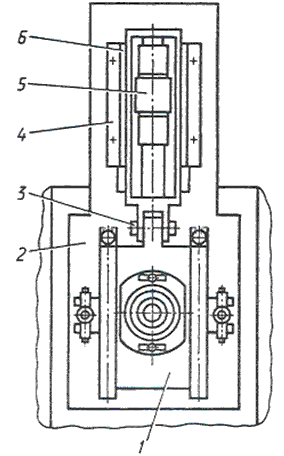
Таким образом, полученные уточненные зависимости для расчета основных энергосиловых параметров систем скользящих затворов позволили обосновать допустимые значения нагрузок на их элементы во время сборки и эксплуатации, выбрать оптимальные технические решения при проектировании перспективных образцов разливочных устройств шиберного типа, а также гидравлических и электромеханических приводов, которые способствовали повышению эффективности применения сталеразливочных ковшей, используемых в составе комплекса оборудования установок "ковш-печь" и высокоскоростных машин непрерывного литья заготовок.
Литература
- Золотухин В.И., Соломин Н.П., Полубесов С.Г. Шиберные системы
нового поколения // Металлург.- 2000.-№ 1,- С. 40 – 42.
- Отечественные ковшовые затворы нового поколения / С.П. Еронько,
А.Н. Смирнов, А.Ю. Цупрун и др. // Металлургическая и горнорудная
промышленность.- 2005.- № 1.- С. 95 – 100.
- Еронько С.П., Быковских С.В. Разливка стали: Оборудование.
Технология.- К.: Техніка, 2003.- 216 с.
- Исследование и разработка эффективной системы двухплитного скользя-
щего затвора балансирного типа / С.П. Еронько, В.Я. Седуш, Е.В. Ошовская
и др. // Теория и практика металлургии.- 2002.- № 5 – 6.- С.75 – 79.
- Расчет усилий в элементах скользящего ковшового затвора /
В.Н. Шестопалов, В.И. Мачикин, М.З. Левин и др. // Изв. вузов. Черная
металлургия.- 1985.- № 2.- С. 135 – 138.
- Еронько С.П. Рациональные системы скользящих затворов // Металлург.-
2003.- № 4.- С. 45 – 47.
- Еронько С.П. Совершенствование системы шиберного затвора для выпускного канала дуговой сталеплавильной печи // Металлургическая и горнорудная промышленность.- 2001.-№ 2.- С. 98-100.
- Повышение эффективности работы и надежности шиберных затворов при
разливке стали / Л.Н. Боканова, В.Ф. Берзов, А.А. Зубакин и др. // Сталь.-
1992.- № 5.- С. 37 – 39.
- Исследование напряженного состояния плит шиберного затвора /
С.П. Еронько, Н.Т. Лифенко, Р.В. Руденко и др. // Металлургическая и
горнорудная промышленность.- 2000.- № 2.- С. 90 – 93.
- Моделирование напряжений в плитах скользящих затворов методом
конечных элементов / С.П. Еронько, Е.В. Ошовская, С.В. Быковских и
др. // Металл и литье Украины.- 2002.- № 7- 8.- С. 39 – 42.
- Еронько С.П., Ошовская Е.В., Цупрун А.Ю. Исследование напряженно-
деформированного состояния огнеупорных плит ковшовых затворов //
Металл и литье Украины.- 2006.- № 7 – 8.- С. 16 – 19.
- Исследование предельно опасных нагрузок в элементах трехплитного
ковшового затвора / С.П. Еронько, Р.В. Руденко, Е.В. Ошовская и др. //
Межвузовский тематический сборник научных трудов "Защита
металлургических машин от поломок".- Мариуполь: ПГТУ.- 1999.-
Вып. 4.- С. 100 – 108.
- Машины и агрегаты металлургических заводов. В 3-х томах. Т. 3.
Машины и агрегаты для производства и отделки проката / А.И. Целиков,
П.И. Полухин, В.М. Гребеник и др.- М.: Металлургия, 1981.- 576 с.
- Огнеупорное производство. Справочник / Под ред. Д.И. Гавриша. В 2-х
томах. Т. 2.-М.: Металлургия, 1965.- 584 с.
- Еронько С.П. Совершенствование системы скользящего затвора для
выпускного канала дуговой сталеплавильной печи // Металлургическая и
горнорудная промышленность.- 2001.- № 2.- С. 98 - 100.
- . Еронько С.П. Совершенствование электромеханического привода
скользящего затвора для дозированной подачи металла // Металлург.-
2002.- № 3.- С.51 – 52.
|