Семенюк Дмитро Юрійович
    Факультет: «Механичний»
    Спеціальність: «Металорізальні верстати та системы»
    Керівник:
Гусєв Володимир Владиленовичд.т.н., проф.
Автореферат за темою магістерської роботы:
«Обгрунтування технології та розробка технологічного обладнання
для обробки сферичних поверхнонь деталей з кераміки»
Зміст:
Актуальність
Мета та задачі магістерської роботи
Аналіз існуючих схем і методів шліфування і доведення сферичних поверхонь
Обробка сферичних поверхонь деталей з кераміки
Основні очікувані результати магістерської роботи
Висновки та перспективи майбутніх досліджень
Перелік використаної літератури
Актуальність розробки верстатного устаткування для обробки сферичних поверхонь деталей машин.
      Питання обробки деталей машин, які містять фасонні (зокрема сферичні) поверхні завжди асоціювався із спеціальним інструментом і устаткуванню, яке робить складні руху формоутворення. Деталі, які мають сферичні поверхні застосовуються не тільки в машинобудуванні, але і в медицині, сільському господарстві і інших галузях промисловості (хімічна, гірничо геологічна, суднобудування, приладобудування і так далі). Тому на сьогоднішній день актуальне питання розробки ефективного високопродуктивного верстатного устаткування, яке дозволяє проводити якісну механічну обробку таких деталей. Існує безліч способів отримання сферичних поверхонь механічною обробкою (точіння, шліфування, фрезерування і так далі), проте особливу увагу до себе привертають саме способи шліфування, як найбільш продуктивні процеси фінішної обробки, які дозволяють забезпечити не тільки високу геометричну точність, але і високу якість поверхневого шару обробленої деталі.
      В даний час в світі спостерігається тенденція виробництва виробів з неметалічних і композиційних матеріалів, які все ширше замінюють метали в багатьох галузях промисловості. Ця тенденція пов'язана із зниженням собівартості продукції при одночасному підвищенні їх терміну служби, надійності і екологічної чистоти. Особливе місце серед неметалічних матеріалів займає кераміка. Физико-механические властивості кераміки в порівнянні зі всіма видами металів, які в даний час застосовуються як головні матеріали для виготовлення деталей машин, мають такі відмінні риси, як висока температура плавлення, твердість, легкість, зносостійкість, корозійна стійкість, стійкість проти хімікатів і так далі При цьому физико-механические властивості кераміки стабільні у великому інтервалі температур, що не маловажно при використанні її у вузлах тертя і утворення високих температур. З іншого боку виникає багато складнощів з механічною обробкою керамічних матеріалів, оскільки вони по суті є абразивами.
Мета і задачі магістерської роботи
      В умовах розвитку ринкової економіки в Україні найважливішим чинником успішної діяльності підприємства є зниження собівартості продукції (за рахунок збільшення серійності виробництва), що випускається, при забезпеченні високих експлуатаційних характеристик виробів (за рахунок застосування прогресивних методів і схем обробки).
У конструкціях виробів для електромашинобудування, приладобудування, ядерної енергетики, ракетобудування, літакобудування, космічної техніки і загального машинобудування часто присутні складні сферичні поверхні, які необхідно обробити з високою точністю. Спостерігається тенденція виробництва виробів з неметалічних і композиційних матеріалів, які все ширше замінюють метали в багатьох галузях промисловості. Одним з матеріалів, який задовольняє перерахованим вимогам, є кераміка. При її застосуванні знижується собівартість виробів при одночасному підвищенні їх терміну служби і надійності. Роботи по керамічних матеріалах у всьому світі безперервно інтенсифікуються, зростають капіталовкладення в їх розробку, розширюються області застосування цих матеріалів. Кожні п'ять років виробництво керамічних виробів подвоюється.
У даній роботі буде розглянуто питання проектування спеціалізованого верстатного устаткування для шліфування і хонінгування сферичної поверхні деталі типу кульовий клапан промислового крана з конструкційної кераміки, а також притирання пари куля-сідло (мал. 1.1)
Рисунок 1.1 – Конструкція кульового крана: 1-шаровий клапан; 2-полімерні кільця; 3,4-корпус; 5-ущільнения; 6-гумове кільце; 7-мідне кільце; 8-гвинт; 9-гвинт М4; 10-гайка; 11-ручка.
Аналіз існуючих схем і методів шліфування і доведення сферичних поверхонь
      Потреба в точній обробці сферичних поверхонь величезної кількості різноманітних деталей з давніх часів і до цих пір примушує інженерів розробляти нові схеми шліфування і удосконалювати старі. У наслідку цього, до нашого часу накопичилися багато різних способів точної обробки сферичних деталей, проте всі вони схожі в тому, що засновані або на використанні фасонного інструменту (що приводить до збільшення витрат на інструмент), або вимагають «зв'язки» декількох складних рухів формоутворення (що приводить до ускладнення і дорожчання устаткування). Найбільш продуктивними методами на сьогоднішній день є методи, представлені на малюнках 2.1, 2.2.
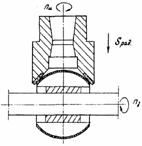
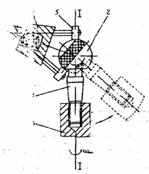
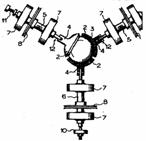
Рисунок 2.1 – Cхеми шліфування сферичних поверхонь, що існують на сьогоднішній день
      Проаналізувавши вище приведені схеми, можна зробити вивід, що для наших умов найбільш підходить схема шліфування внутрішньою конічною поверхнею шліфувального круга (Рисунок 2.1,в), оскільки ця схема забезпечує високу продуктивність і має величезний потенціал в області автоматизованого виробництва. Твірна конічній поверхні алмазоносного шару співпадає з дотичній до створюючої сфери на її межі з торцевими площинами, що обмежують сферу.
      Такий процес шліфування конічним шліфувальним кругом можна віднести до тих небагатьом випадкам, коли головним рухом є обидва обертальні рухи, які в сукупності визначають необхідну для здійснення шліфування результуючу швидкість різання. Конкретно питання повинне вирішуватися доцільністю того або іншого конструктивного рішення.
      Даний процес повинен забезпечити знімання припуска, достатнє для досягнення необхідної точності розміру, форми, а так само компенсації погрішностей базування. Зменшуючи зернистість круга, наближаємо процес шліфування до чистового і отделочному. Але тоді доцільність його здійснення на жорстких осях пристосування і інструменту стає сумнівною. Навпаки, необхідно звільнити один з елементів – шліфувальну головку надати їй можливість самоустанавливаться по оброблюваній поверхні, що забезпечить процес хонінгування і доведення або притирання.
3. Запропонована конструкція верстата для обробки неповних сферичних поверхонь деталей машин
      Провівши аналіз існуючих схем обробки, ми зупинилися на схемі, показаній на малюнку 3.1, тобто на шліфуванні сфери чашковими кругами, але ми вестимемо обробку відразу двома інструментами.
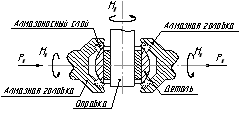
Рисунок 3.1 – Схема шліфування конічним кругом
      Даний процес повинен забезпечити знімання припуска, достатнє для досягнення необхідної точності розміру, форми, а так само компенсації погрішностей базування. Дана схема обробки дозволяє використовувати як інструмент конічні діамантові круги з різною зернистістю, що необхідне при обробці керамічних куль, тому саме така схема обробки буде покладена в основу спеціалізованого устаткування для виробництва кульових клапанів промислових кранів.
      Ще однією перевагою є можливість встановити замість інструменту кільце-сідло крана, а замість деталі – чавунний притир і провести обробку кільця, після чого притерти безпосередньо кулю і сідло, застосувавши мелкодисперсный вільний абразив у вигляді пасти.
      Розрахунок необхідних режимів різання при шліфуванні проводитимемо виходячи з умов забезпечення необхідної якості поверхні і точності форми деталі. При розрахунку частоти обертання деталі і інструменту використовуватимемо розрахункову схему (Рисунок 3.2).
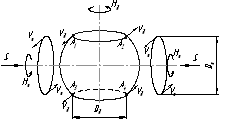
Рисунок 3.2 – Схема шліфування сферичної поверхні
      З даної схеми бачимо, що напрями векторів лінійних швидкостей на різних точках деталі і інструменту відрізняються. При цьому лінійні швидкості в точках А1 і А4 маю один напрям, тому результуюча швидкість різання визначатиметься різницею окружних швидкостей, і навпаки.
      Для забезпечення необхідної якості обробленої поверхні і стійкості інструменту, максимальна швидкість різання не повинна перевищувати допустиму для даного оброблюваного і інструментального матеріалу. У нашому випадку обробляється конструкційна кераміка на основі оксиду алюмінію (Al2O3) діамантовим абразивним і інструментом, для якого максимальна швидкість різання складає 15 – 20 м/с [1]. При цьому досвід використання даної схеми обробки показує, що якнайкраща якість поверхні на одній і тій же швидкості різання досягається при співвідношенні частот обертання деталі і інструменту : 1/2.
      Шліфування буде проводиться по пружній схемі, а нормальний тиск на оброблюваній поверхні складатиме PN : 0,05 – 0,1МПа, що забезпечить необхідну якість обробленої поверхні. Для визначення складових сили різання скористаємося розрахунковою схемою (Рисунок 3.3).
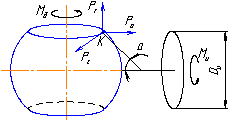
Рисунок 3.3 – Схема розкладання сил різання при обробці
      Знайдемо площу контакту інструменту і деталі по якій розповсюджується тиск з урахуванням наступних допущень: а) контакт деталі і інструменту безперервний за всією площею контакту; б) тиск на деталь з боку інструменту розподіляється рівномірно по всьому майданчику контакту.
      Проведені розрахунки показали, що ефективна потужність шліфування буде:
      Як видно з малюнка 3.2 для обробки деталі необхідно забезпечити три формоутворювальні рухи – два обертальні головні рухи і одну поступальну ходу подачі. Ці рухи (Вz, Ву і Пу) можна реалізувати застосувавши компоновку верстата як на малюнку 3.4. Для підвищення продуктивності і компенсації силових чинників, ми оброблятимемо деталь одночасно з двох сторін двома інструментами.
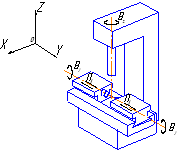
Рисунок 3.4 – Компонувальна схема верстатної системи для обробки сферичних деталей
      Для обробки сферичних поверхонь деталей на проектованому устаткуванні необхідно забезпечити три формоутворювальні рухи, отже, необхідно розробити кінематичні схеми трьох приводів:
      а) Привід обертання деталі (Рисунок 3.5);
      б) Привід обертання інструменту(Рисунок 3.6);
      в) Привід подачі інструменту(Рисунок 3.7).
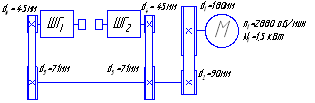
Рисунок 3.5 – Кінематична схема приводу обертання деталі
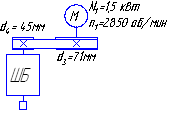
Рисунок 3.6 – Кінематична схема приводу обертання деталі
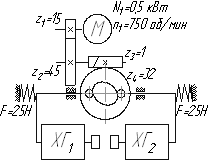
Рисунок 3.7 – Кінематична схема приводу подач інструменту
      Загальна потужність верстатної системи склала 3,5 кВт.
      Розроблена верстатна система (рисунок 3.8) призначена для шліфування, хонінгування або притирання сферичних поверхонь. Всі ці процеси можуть бути реалізовані на одному і тому ж верстаті після зміни виконавського робочого органу (рухомої інструментальної головки) і перенастроювання на розмір. Це не створить незручностей при експлуатації верстатів в автоматичних лініях, але одночасно уніфікація всіх вузлів значно вартість виробництва і ремонту даних верстатів.
Верстат призначений для обробки неповних сферичних поверхонь діаметром (25.55) мм деталей з металів, кераміки і інших матеріалів. При певній модернізації і настройці механічної частини і системи управління він може вбудовуватися в автоматичні лінії обробки деталей, що містять сферичні поверхні.
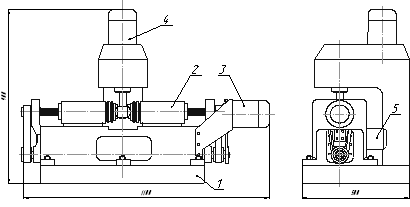
Рисунок 3.8 – Загальний вид верстата для обробки сферичних поверхонь
      Основними вузлами системи є механізми здійснення обертання і подачі інструменту. Складальне креслення цих механізмів приведене на малюнку 3.9.
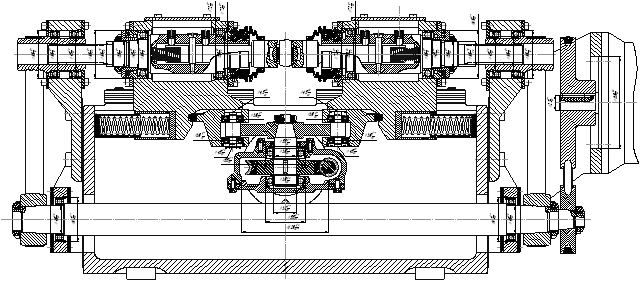
Рисунок 3.9 – Збірка хонинговального модуля
      При проектуванні був проведений силовий розрахунок найбільш відповідальних вузлів системи, таких як клиноременная передача, плоскоременная передача, що направляють кочення, черв'ячний редуктор, а також виконаний динамічний розрахунок приводу обертання інструменту. Використовувалася література [2, 3, 4]. Розрахунки підтвердили працездатність основних вузлів що входять до складу верстатної системи.
Фізичне моделювання і дослідження температурного стану деталі і інструменту в процесі діамантового шліфування кульового клапана
      Одним з найважливіших параметрів функціонування системи різання є температура, що визначає як працездатність ріжучого інструменту, так і якість поверхонь оброблюваних деталей. Разом з експериментальними дослідженнями, в даний час всього більшого поширення набувають теоретичні методи дослідження, що дозволяють розрахувати рівень температур на поверхні і усередині контактуючих тіл.
У роботі вирішується завдання визначення температурного стану поверхневого і внутрішнього шару кульового клапана при шліфуванні його зовнішньої сферичної поверхні інструментом, оснащеним синтетичним алмазом з метою розробки рекомендації за призначенням раціональних режимів різання, що забезпечують необхідну якість обробленої поверхні.
      На початковому етапі рішення задачі була розроблена геометрична 3D модель деталі і інструменту (рисунок 4.1), а також задані властивості матеріалу деталі (конструкційна оксидна кераміки Al2O3) і облямовування (сталь 45).
      Після побудови геометричної моделі деталі, було проведено її розбиття на сітку кінцевих елементів (рис.4.2).
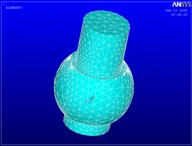
Рисунок 4.1 – Геометрична 3D модель деталі і оправкою
      Після цього ми задаємо тепловий потік на майданчику контакту інструменту і деталі розбитою на 20 окремих майданчиків. Тепловий потік заздалегідь розрахований залежно від швидкості різання і тиску на цих майданчиках контакту.
      Після зміни швидкостей різання (змінюючи частоту обертання шліфувального круга) і розрахунку температури, був побудований графік залежності температури від швидкості різання (рисунок 4.3).
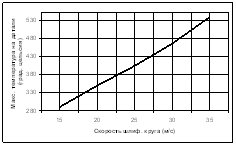
Рисунок 4.3 – Графік залежності максимальної температури на поверхні деталі від швидкості обертання шліфувального круга.
      Для забезпечення необхідної якості поверхневого шару деталі (по параметру трещиноватости) необхідно, щоб температура при обробці не перевищувала критично допустиму (300 - 350 °С). На графіці бачимо, що дана температура утворюється на швидкості круга : 25 м/с, тому для забезпечення нормальних умов обробки призначимо швидкість круга 20 м/с.
      Досліджуємо вплив сили притиску шліфувального круга до деталі на температуру на поверхні деталі. За отриманими даними побудуємо графік залежності tmax = f(Ру), представлений на малюнку 4.4.
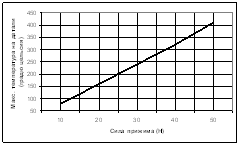
Рисунок 4.4 – Графік залежності максимальної температури на поверхні деталі від сили притиску шліфувального круга.
      На побудованому графіку бачимо, що для забезпечення якості поверхневого шару необхідне, щоб зусилля притиску не перевищувало 45 Н.
      Ми бачимо, що температура росте із збільшенням швидкості круга і зусилля притиску інструменту до деталі. Є декілька варіантів можливих режимів, проте з погляду зменшення шорсткості поверхні нам потрібно збільшувати швидкість круга і зменшувати силу притиску інструменту. Тому призначимо швидкість круга 18 Vкр м/с, а зусилля притиску 20 Н і проведемо контрольний дослід. Результати приведені на малюнку 4.5.
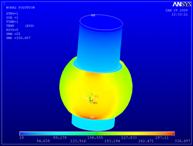
Рисунок 4.5 – Тепловий стан кульового клапана при обробці на наступних режимах:
Py = 20 Н, Vкр = 18 м/с, Vд = 7 м/с.
Висновок
      В результаті проведеної роботи був спроектований спеціалізований верстат для обробки сферичних поверхонь деталей машин. Як приклад деталі, був узятий кульовий клапан промислового крана. У роботі був проведений аналіз існуючих методів і схем обробки неповних сферичних поверхонь і вибраний найбільш продуктивний (шліфування внутрішньою поверхнею конічного шліфувального круга). Для вибраної схеми обробки були розраховані швидкості різання на різних ділянках майданчика контакту. Для забезпечення необхідних рухів формоутворення була розроблена компонувальна схема верстата. На наступному етапі бувальщини розроблені кінематичні схеми приводів обертання деталі і інструменту, а також приводу подачі шліфувального круга, для яких були розраховані потужності електродвигунів. У конструкторській частині роботи були розроблені конструкції приводу обертання деталі і подачі інструменту, для яких були виконані необхідні силові розрахунки відповідальних вузлів і деталей.
      Для призначення режимів різання, що забезпечують відсутність утворення дефектів обробки під впливом температурного чинника, був проведений температурний аналіз стану деталі при її обробці. Для цієї мети був використаний програмний пакет ANSYS. Проведені розрахунки показали, що максимальна температура в зоні контакту не перевищує допустимих значень.
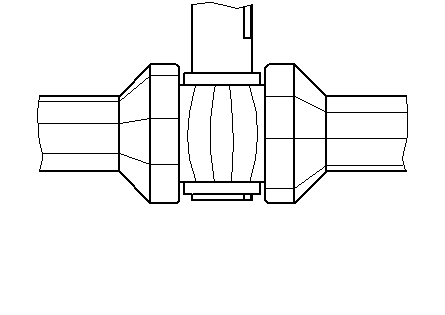
Рисунок 5. - Анімоване зображення процессу обробки сферичної поверхні на спроектованому верстаті (89 кБ, 21 кадр, 10 циклів повторення)
Перелік використаної літератури
     1. Абразивная и алмазная обработка материалов. Справоч¬ник. Под ред. д-ра техн. наук проф. А. Н. Резникова. M. «Маши построение», 1977 – 391с.
     2. Кочергин А. И. Конструирование и расчет металлорежущих станков и станочных комплексов. Курсовое проектирование: Уч. пособие для вузов. – Минск: Высш. шк., 1991 – 382с.
     3. Детали и механизмы металлорежущих станков: в 2-х т., Т.1. под ред. Д.Н. Решетова. М.: Машиностроение, 1972 – 664с.
     4. Расчет динамических характеристик металлорежущих станков : учебное пособие / В.А. Ванин, А.Н. Колодин, Ю.В. Кулешов, Л.Х. Никитина. – Тамбов : Изд-во Тамб. гос. техн. ун-та, 2007. – 104 с.
     5. Гусев В.В. Назначение режимов резания при алмазном шлифовании конструкционной керамики/Наукові праці ДонНТУ. Серія: Машинобудування і машинознавство. Випуск 110. Донецк: ДонНТУ, 2006. С. – 6 - 16.
     6. Братан С.М., Каинов Д.А. Сазонов С.Е. Оценка параметров качества поверхности при доводке свободным абразивом/ Наукові праці ДонНТУ. Серія: Машинобудування і машинознавство. Випуск 124. Донецк: ДонНТУ, 2007. С. – 9 - 15.
     7. Дитиненко С.А., Снисаренко И.Н., Машко А.А., Черненко А.В. Условия уменьшения шероховатости обработки при шлифовании / Наукові праці ДонНТУ. Серія: Машинобудування і машинознавство. Випуск 139. Донецк: ДонНТУ, 2008. С. – 16 - 23.
ДонНТУ |
Портал магистрів ДонНТУ |
Реферат |
Библіотека |
Посилання |
Звіт про пошук |
Индивідуальне завдання
|