«Обоснование режимов шлифования стали Р6М5Ф3 эльборовыми кругами»
Научный руководитель:
Матюха Петр Григорьевич
Материалы по теме магистреской работы:
Об авторе |
Библиотека | Ссылки |
Отчет о поиске || Индивидуальный раздел
Реферат по теме выпускной работы
ВВЕДЕНИЕ
1. ЛИТЕРАТУРНЫЙ ОБЗОР ПО ЭЛЬБОРОВОМУ ШЛИФОВАНИЮ
1.1 Физико-механические свойства эльбора
1.2 Химические свойства эльбора
1.3 Геометрия зерен эльбора
1.4 Процессы дефектообразования в кубическом нитриде бора
1.5 Абразивный инструмент из эльбора
1.6 Качество обработанной поверхности при эльборовом шлифовании
2. ИССЛЕДОВАНИЕ ТЕМПЕРАТУРЫ ОБРАБАТЫВАЕМОЙ ПОВЕРХНОСТИ ПРИ ВРЕЗНОМ ШЛИФОВАНИИ СТАЛИ Р6М5Ф3 КРУГОМ ИЗ ЭЛЬБОРА
2.1 Анализ методик определения температуры на поверхности детали при плоском шлифовании
2.2 Назначение режимов резания
2.3 Определение коэффициента ввода тепла в шлифовальный круг из ельбора
2.4 Определение плотности теплового потока при шлифовании
2.5 Расчет температуры и температурных деформаций в среде «ANSYS»
ВЫВОДЫ
ЛИТЕРАТУРА
ВВЕДЕНИЕ
      Актуальность
      Первостепенное значение для ускорения технического прогресса и оснащения всех отраслей народного хозяйства новой техникой имеет дальнейшее быстрое развитие всех современных отраслей машиностроения.
      Шлифования, являясь одним из самых производительных методов обработки металлов, обеспечивает низкие высотные параметры шероховатости обрабатываемой поверхности, высокую точность формы и размеров деталей. Шлифованием можно обрабатывать практически все материалы.
      В связи с этим весьма актуальным и перспективным направлением является освоение эльборовых кругов на металлической связке. Эти шлифовальные круги обладают высокой режущей способностью, большим периодом стойкости, но нуждаются в постоянной правке электроэрозионным воздействием на связку круга.
    Так как современный парк шлифовальных станков практически не обладает средствами для электроэрозионной правки шлифовального круга, то модернизация существующих шлифовальных станков так же является на сегодняшний день весьма актуальной темой, особенно в условиях мирового кризиса.
      Цели и задачи магистерской работы
      При выполнении магистерской работы были поставлены следующие основ-ные задачи:
      - выполнить литературный обзор по назначению режимов шлифования эльборовыми кругами;
      - исследовать влияния положения шлифовального круга на заготовке при плоском шлифовании на температуру поверхности детали в среде «ANSYS»;
      - модернизировать внутришлифовальный станок для электроэрозионной правки круга и шлифования по упругой схеме;
      - определить силы поджима круга к образцу по критерию прочности зерен;
      - назначить режимы шлифования стали Р6М5Ф3 эльборовым кругом;
      - исследовать мгновенную режущую способность круга при внутреннем шлифовании Р6М5Ф3 по упругой схеме;
      - определить механические режимы и режимы электроэрозионных воздействий при внутреннем шлифовании Р6М5Ф3.
      Целью данного реферата является литературный обзор по эльборовому шлифованию и исследование положения ШК на поверхности заготовки на тем-пературу средствами «ANSYS»
1. ЛИТЕРАТУРНЫЙ ОБЗОР ПО ЭЛЬБОРОВОМУ ШЛИФОВАНИЮ
1.1 Физико-механичекие свойства эльбора
      Основной кристаллографической формой кубического нитрида бора является комбинация положительного и отрицательного тетраэдров [1]. Реже встречаются слабо развитые грани куба и ромбододекаэдра. Поверхность граней крупных кристаллов чаще всего несовершенна, зеркальные грани встречаются весьма редко, в основном на мелких кристаллах размером 0,06 - 0,08 мм. Рост кристаллов происходит плоскими слоями, пирамидками и бугорками на гранях тетраэдров разного знака. Грани положительного тетраэдра растут медленнее, имеют большее развитие и более разнообразный микро¬рельеф. В результате сублимации кубического нитрида бора вершины зерен крупных кристаллов притупляются, а их ребра имеют зазубренные очертания.
      Форма, размеры, минеральный состав и особенности внутренней структуры кристаллов эльбора обусловлены технологическими особенностями синтеза.
      Физико-механические свойства кристаллов приведены в таблице 1.1 [2]
Таблица 1.1 - Физико-механические свойства кристаллов
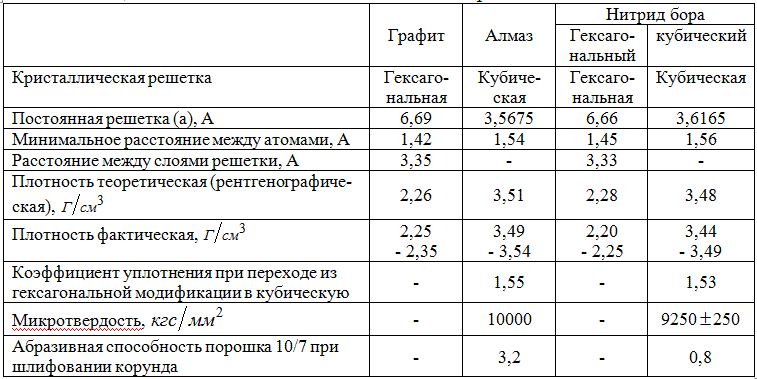
1.2 Химические свойства эльбора
      Абразивный материал эльбор состоит из кубического нитрида бора - BN (91 – 95 %) и сопутствующих ему примесей: гексагонального нитрида бора BN (1 - 2,5 %), кремния (0,05 - 0,15 %), железа (0,07 - 0,10 %), алюминия (0,05 - 0,25 %), кальция (0,05 - 0,20 %), магния (1 - 1,5%) и свободного углерода (0,6 – 1 %) [2].
      Исследования [3] на абразивных зернах из кубического нитрида бора, размер зерен основной фракции которых изменяется от (-5 +3) до (-250 +200) мк, показали, что концентрированные и разбавленные кислоты (соляная, серная, азотная, фосфорная, плавиковая), смесь концентрированной серной кислоты с сульфатом калия, окислители (смесь пергидроля с азотной кислотой и царская водка), а также растворы щелочей не оказывают химического воздействия на кубический нитрид бора. Химическая устойчивость наблюдалась при температурах кипения кислот с выдержкой от 1 до 24 ч.
      Кубический нитрид бора разлагается при сплавлении порошка со щелочами в интервале температур 400 - 700° С с образованием бо¬рата и выделением аммиака. При температуре 400° С в трубчатой печи в течение 30 мин микропорошок кубического нитрида бора крупностью (-5 +3) мк разлагался на 55 %, а крупностью (-250 + 200) мк — только на 6 %.
      При температуре 700° С разложение происходит более интенсивно: зерна (-5 +3) мк и зерна (-50 +40) мк разлагаются полностью, зерна (-100 + 80) мк — на 90 %, а зерна (-250 + 200) мк - на 88 %.
      Кубический нитрид бора не вполне устойчив к перегретому водяному пару при температуре 900° С: за 2 ч обработки разложилось 4,7 % зерен, за 4 ч —7 %, а за 6 ч— 10 %.
1.3 Геометрия зерен эльбора
      Установлено, что изометричность зерен эльбора выше, чем алмаза и электрокорунда [4]. Это связано со спецификой его измельчения и поликристаллическим строением зерен. Среднее значение коэффициента формы зерен, представляющего отношение длины зерна к его ширине (l:b), при наблюдении под микроскопом для алмаза АСО 16 - 25 равно 1,44 - 1,50, электрокорунда ЭБ 32 – 50 - 1,47 - 1,48 и эльбора Л12 - 1,38.
      С уменьшением номера зернистости зерен эльбора радиус округления и угол заострения режущих кромок уменьшаются, а процент острых углов возрастает (табл. 1.2).
Таблица 1.2 - Геометрия зерен эльбора
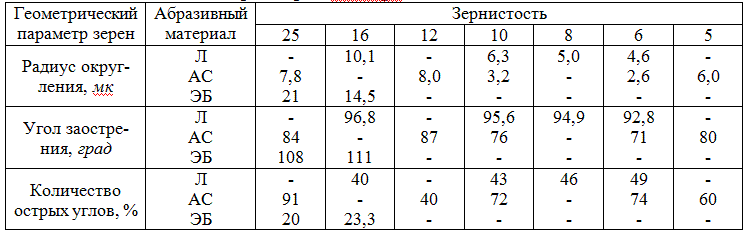
1.4 Процессы дефектообразования в кубическом нитриде бора
      Изменения физических характеристик СТМ в зависимости от параметров синтеза и внешних воздействий, например температурного отжига либо облучения, связываются с трансформацией дефектной структуры этих материалов, что позволило разработать физические принципы конструирования СТМ— направленные изменения их дефектной структуры, коррелирующие с изменением ме-ханических характеристик материалов. На этих принципах разработан ряд ори-гинальных технологий, существенным образом повышающих прочностные характеристики алмаза и BNK [5].
      В частности, в BN обнаружены закономерные осциллирующие изменения дефектной структуры при термообработке, коррелирующие с изменением его физических характеристик. Установлено существование узкой температурной зоны (870+10 К), разделяющей качественно различные состояния дефектной структуры BNKK. Показано, что при термообработке при 870 К в BNK формируется особое состояние дефектной структуры, при которой модуль упругости достигает наибольшего значения, а внутреннее трение становится минимальным в результате эффективной блокировки дислокаций закрепляющими центрами, происходящей вследствие их интенсивной миграции из объема к дислокациям. Показано, что реакция отжига дефектов имеет первый порядок и характеризуется различными механизмами взаимодействия дефектов: на низкотемпературном участке (770-870 К), характеризующемся небольшой величиной энергии активации (0,2 эВ), определяющим процессом является миграция собственных либо примесных междоузельных атомов; более высокое значение энергии активации (0,7 эВ) для второго участка (870-1020 К) приписано миграции вакансий или, что более вероятно, дивакансий.
      Выявлены центры люминесценции, в том числе мессбауэровского типа, обусловленные точечными дефектами, и развиты модельные представления о порождающих их дефектах. Установлено, что центры GC-1 и GC-2 с БФЛ энергией 1,76 и 1,63 эВ являются дефектами вакансионного типа на основе вакансий азота и бора соответственно и технологической примеси. Природа центров PF (2,8-3,6 эВ) интерпретирована в модели донорно-акцепторной рекомбинации. Предполагается, что центры PF— это донорно-акцепторные пары на основе междоузельных атомов бора и азотных вакансий. Центр PC -3(1,79 эВ) является дефектом примесного типа, порождаемым включением Al2O3:Cr3+. Установлена природа широких полос спектров катодолюминесценции: С - полоса (1,55-1,85 эВ) — дислокационная, полосы А и В (1,85 и 3,25 эВ) — примесно-вакансионные на основе вакансий по бору и азоту соответственно..
      По данным внутреннего трения установлено, что высокотемпературный фон внутреннего трения в BNK носит дислокационный характер и вызван дви-жением геометрических перегибов на дислокациях в присутствии закрепляющих центров, в качестве которых выступают вакансионные комплексы. Сделано заключение, что природа релаксационных пиков в спектре внутреннего трения обусловлена переориентацией неустойчивых вакансионных комплексов в примесном поле механических напряжений с энергией активации 0,7-2,2 эВ.
      Установлена природа относительно устойчивого к отжигу пика внутреннего трения при 360 К BNK, обусловленная переориентацией дивакансий бора в переменном поле упругих напряжений по типу параупругой релаксации Зинера. Показано, что характер температурных зависимостей коэффициента линейного расширения BNK, установленный из резонансных измерений, определяется состоянием его дефектной структуры. Обнаружено существование амплитудной зависимости внутреннего трения в BNK и показано, что при комнатной температуре движение дислокаций контролируется пайерлсовским механизмом. При повышенных температурах движение дислокаций определяется их взаимодействием, по меньшей мере, с двумя типами закрепляющих центров, представляющих собой вакансионные комплексы разной структуры.
      Технология повышения прочности порошков алмаза и BNK, основанная на модифицировании дефектной структуры СТМ, позволила повысить прочность порошков на 20 %.
1.5 Абразивный инструмент из эльбора
      Первые опытно-промышленные партии инструмента из эльбора были изготовлены на ленинградском абразивном заводе «Ильич» в 1964 г., а с 1965 г. началось их промышленное производство. В настоящее время выпускают из эльбора абразивный инструмент широкой номенклатуры: различные виды шлифовальных кругов, брусков, шлифовальную шкурку, пасты [6].
      Инструменты из эльбора выпускаются на керамических, органических и металлических связках. Создание специальных керамических связок во многом предопределило эффективное использование эльбора как абразивного материала в инструменте.
      Инструменты на керамических связках отличаются прочным закреплением эльбора в абразивном слое, высокой стойкостью профиля. Твердость инструмента из эльбора на керамических связках, как и твердость обыч¬ного абразивного инструмента из традиционных материалов, характеризует прочность удержания зерен связкой и измеряется согласно ГОСТ 3751 - 47.
      Промышленность выпускает инструмент следующих характеристик по твердости: М (М2, МЗ), CM (СМ1, СМ2), С (С1, С2), СТ (СТ1, СТ2, СТЗ), Т (Т1, Т2). Твердость эльборосодержащей части кругов и брусков определяется на приборе «Роквелл» шариком диамет¬ром дюйма при нагрузке 60 кгс, затем по средним значениям твердости, полученным на приборе, и по таблице 2 ГОСТ 3751 - 47.
      Структура инструмента из эльбора на керамических связках характеризуется содержанием эльбора и наполнителя в единице объема рабочей (эльборосодержащей) части круга, выраженным в процентах, и обозначается определенным номером (от № 6 до № 12) в зависимости от зернистости эльбора. Чем выше номер структуры, тем больше связки и меньше зерна в единице объема инструмента при одинаковой твердости. В общем объеме производства инструменты из эльбора на керамических связках составляют 60%.
      Круги из эльбора на органических связках по форме, характеристикам и технологии изготовления подобны аналогичному алмазному инструменту. Круги на металлических связках выпускаются, как правило, небольшими партиями по специальному заказу. Наряду с известными ранее способами изготовления инструментов из сверхтвердых материалов на металлических связках разработаны и применяются новые.
      Основные типы инструмента из эльбора, выпускаемые промышленностью:
        а) шлифовальные круги прямого профиля для внутреннего шлифования диаметром 3 - 60 мм;
        б) шлифовальные круги прямого профиля для круглого, наружного и плоского шлифования диаметром 70 - 400 мм;
        в) шлифовальные круги фасонного профиля для профильного шлифования, в том числе для резьбошлифования, диаметром 50—500 мм;
        г) шлифовальные круги тарельчатого профиля диаметром 75 - 125 мм для затачивания металлорежущего инструмента;
        д) шлифовальные круги чашечного профиля диаметром 50 - 200 мм для затачивания металлорежущего инструмента и плоского шлифования;
        е) бруски различных размеров и шлифовальная шкурка.
1.6 Качество обработанной поверхности при эльборовом шлифовании
      Закономерности влияния характеристики круга и режимов резания на количество остаточного аустенита аналогичны закономерностям, полученным для температуры шлифования. Выше было показано, что при шлифовании кругами из эльбора температуры, возникающие в поверхностном слое, значительно меньше, чем при шлифовании абразивными я алмазными кругами. В связи с этим при эльборовом шлифовании уменьшается опасность структурных изменений в поверхностном слое деталей и инструментов (табл. 1) [7].
Таблица 1.3 – Структурные изменения в поверхностном слое
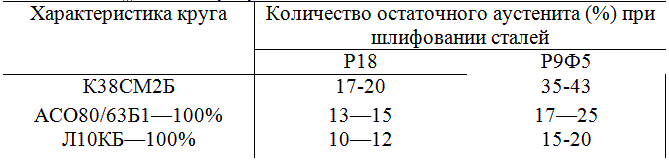
      Во ВНИИ было установлено, что при плоском шлифовании образцов из сталей Р18, Р6М5, Р9Ф5 кругами чашечной формы на органических связках в диапазоне режимов: VКР=15-30 м/сек, Sпр=1-4 м/мин, t = 0,01-0,04 мм/дв. ход, без охлаждения количество остаточного аустенита не превышает 20%. Следовательно, при этих условиях обработки в поверхностном слое быстро-режущих сталей не происходит существенных структурных изменений, которые могут привести к снижению стойкости инструмента. Эти дан¬ные согласуются с опытами по измерению температур. В условиях прерывистого шлифования без учета накопления тепла значения Т для исследованного диапазона режимов резания были меньше 700° С и не могли привести к структурным изменениям.
      Опыты показали, что в процессе алмазного и кубонитового шлифования наблюдается распад остаточного аустенита, образование мартенсита и мелкодисперсных карбидов. Количество оста¬точного аустенита уменьшается, а в поверхностных слоях отсутствует троосто-сарбитная (сталь 40Х) и троосто-мартенситная (сталь 111X15) зоны.
2. ИССЛЕДОВАНИЕ ТЕМПЕРАТУРЫ ОБРАБАТЫВАЕМОЙ ПОВЕРХНОСТИ ПРИ ВРЕЗНОМ ШЛИФОВАНИИ СТАЛИ Р6М5Ф3 КРУГОМ ИЗ ЕЛЬБОРА
2.1 Анализ методик определения температуры на поверхности детали при плоском шлифовании
2.1.1 Анализ методик определения температуры на поверхности теоретическим способом
      В общем случае существует две разновидности методик определения температуры на поверхности детали, а именно теоретическая и экспериментальная. Каждая из них имеет как пе-ревагы так и недостатки.
      Задача теоретических исследований состоит в определении общих закономерностей возникновения и распределения теплоты в процессе шлифования и температур, которые при этом развиваются. Теоретический расчет температуры шлифования в основном сводится к решению задачи Фурье.
      Систематическое изучение тепловых явлений при шлифовании началось с експерементального определения зависимости контактной температуры в зоне обработки от условий шлифования с использованием термопары [8]. В дальнейшем такой метод измерения температуры был значительно расширен и использован многими исследователями. Обобщенные результате можно получить только с помощью теоретического расчета температуры шлифования в сочетании с качественной экспериментальной проверкой.
      Созданию современной теплофизики шлифования способствовали теоретических исследований температур, которые развиваются при трении. В работе Дж. Иегера рассмотрены два основных случаи расчета температур при трении с постоянной скоростью. В первом случае считалось, что поверхность (источник) трения имеет форму полосы, а во втором случае - форму стержня квадратного сечения. Полученные формулы, с заданным приближением, дали возможность определить средние температуры, развивается при трении.
      С.Г. Редько [9] предложил метод определения температуры шлифования, который базируется на работе единичных абразивных зерен круга и последовательном наложении элементарных тепловых импульсов от зерен, причем нагрев шлифуемой поверхности принимается как результат такого многократного наложения.
      Из дифференциального уравнения теплопроводности получены уравнения для температуры на поверхности контакта абразивного зерна и в глубину детали; принятые во внимание форма, пространственное положение, скорость движения абразивного зерна и интервалы между действиями источнику теплоты. Например, максимальная температура в зоне контакта круга с деталью при суммарном действии тепловых импульсов от всех зерен, которые действуют в зоне контакта
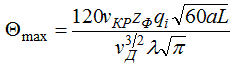
где VКР - окружная скорость круга;
        ZФ - количество абразивних зерен на одинице раб очей поверхности круга;
        qi - средняя напряженность теплового потока;
        L - длина контакта круга с деталью;
        а - температуропроводность материала детали;
        VД - скорость детали.
2.1.2 Экспериментальные методы определения температуры поверхности при шлифовании
      Экспериментально температуру шлифуемой детали измеряют с помощью термопар, по структурным преобразованиям в поверхностном слое шлифуемой детали и дистанционных датчиков [10]. Наиболее широко используется измерение температур при помощи искусственных и полуискусственных термопар (рис 2.1)
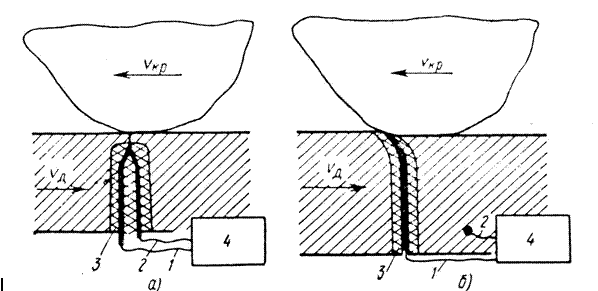
Рисунок 2.1 – Термопары:
а – искусственная; б – полуискусственная; 1 і 2 – проводники;
3 – электроизоляция (слюда); 4 – приспособление для регистрации термо-ЭДС.
      Искусственные термопары чаще всего изготавливают из хромель-конелевых проволочек диаметром 0,1 мм и соединяют с осциллографом (с усилием и без усилия). Между проволочкамы термопары вкладывают электроизоляционные прокладки (листочки слюды) толщиной 0,1-0,2 мм. Диаметр головки термопары 0,2-0,3 мм. Концы термопары подключают к шлейфу осциллографа (Н-700 и др.). Полуискусственная термопара образует спай в момент резки зерном.
2.2 Назначение режимов резания
      Назначеные режимы шлифования должны обеспечивать достижение в процессе обработки требуемых точности и качества шлифуемого поверхностного слоя детали (рис.2.1). Отсутствие. Отсутствие дефектов поверхностного слоя (прижогив и микротрещин) является главным условием успешного внедрения процесса шлифования в производство. Требования гарантированного достижения бездефектной обработки при глубинном шлифовании определены в ходе комплексных исследований качества поверхностного слоя деталей [11].
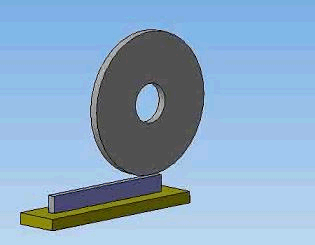
Рисунок 2.2 - Анимация процесса плоского шлифования:
кадров - 7, повторов - 7, размер - 130 КБ.
      Проведенные исследования температурного поля заготовки при глубинном абразивном шлифовании позволили установить, что при наклонно движущемся источнике тепла в условиях интенсивного охлаждения количество теплоты, которое идет в обрабатываемую поверхность, в зависимости от требований обработки составляют 32 - 83% общего количества теплоты, выделяемой в процессе обработки. Причем, чем больше угол наклона источника теплоты и меньше скорость заготовки, тем большее количество теплоты уходит в слой металла, который снимается с заготовки и тем ближе максимальные значения температуры на ее поверхности к передней границы источнику теплоты. Для обеспечения отвода как можно большего количества теплоты в слой металла, который снимается при глубинном шлифовании с заготовки, кинематическая параметры процесса должны удовлетворять следующему требованию:
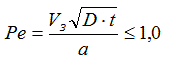
где VЗ - скорость заготовки, м/с;
        D - диаметр шлифовального круга, м;
        t - глубина шлифования, мм.
      Интенсивный теплообмен в зоне шлифовани, предельное значение коэффициента которого в условиях подачи СОЖ под давлением a0=(3.5...5)*103 Вт/м2 0C, является эффективной мерой снижения температуры на участке контакта круга с заготовкой.
2.3 Определение коэффициента ввода тепла в шдифовальный круг из эльбора
      Рассмотрим вопрос о доле тепла, которая идет в шлифовальный круг. Эта задача должна решаться из предложения дискретности контакта круга и детали. Если для шлифуемой поверхности быстрая смена тепловых импульсов на наиболее активных зернах сливается в сплошной фон, то для шлифовального круга контакт всегда является дискретным, который действует на протяжении кратного времени, который зависит от скорости круга. Преимущественное тепловыделение на зернах в сравнении со связкой, позволяет моделировать каждое зерно в виде полупространства, имеющего контакт на небольшом участке с вторым полупространством, движущимся относительно первого со скоростью периферии круга. Вопрос о распределении тепла между этими полупространствами решается на основе равентсва средних контактных температур. Это условие после небольших преобразований приведет к формуле для определения коэффициента ввода, показывающий какая часть тепла уходит в полупространство (в данном случае в деталь)[12]
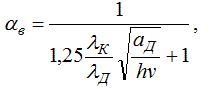
где LД - коэффициент теплопроводности детали, Вт/м 0C;
        LК - коэффициент теплопроводности круга, Вт/м 0C;
        аД - коэффициент температуропроводности детали, м2/с;
        h - средний радиус площадки контакта зерна с заготовкой.
2.4 Определение плотности теплового потока при шлифовании
      Так как шлифование ведется без использования СОЖ, можно ограничиться заданием на всех поверхностях граничных условий второго рода. Под источником необходимо задать усредненный по зоне контакта тепловой поток, а на других поверхностях - нулевой тепловой поток.
      Для определения плотности теплового потока рассчитаем составляющую силы резания по эмпирические зависимости [13]

      Плотность теплового потока будет равна:
q=Pz*Vк/S
где S - площадь контакта круга с заготовкой, м2.
2.5 Расчет температуры и температурных деформаций в среде «ANSYS»
      Чтобы исследовать влияние места работы шлифовальный круга на обрабатываемой поверхности на температуру, разбивает поверхность детали на доли, которые равны площади контакта круга и детали. На эти доли последовательно прилагаем плотность теплового потока, рассчитанную ранее и строим график распределения температуры в детали, в зависимости от места нахождения источника тепла (рис. 2.3)
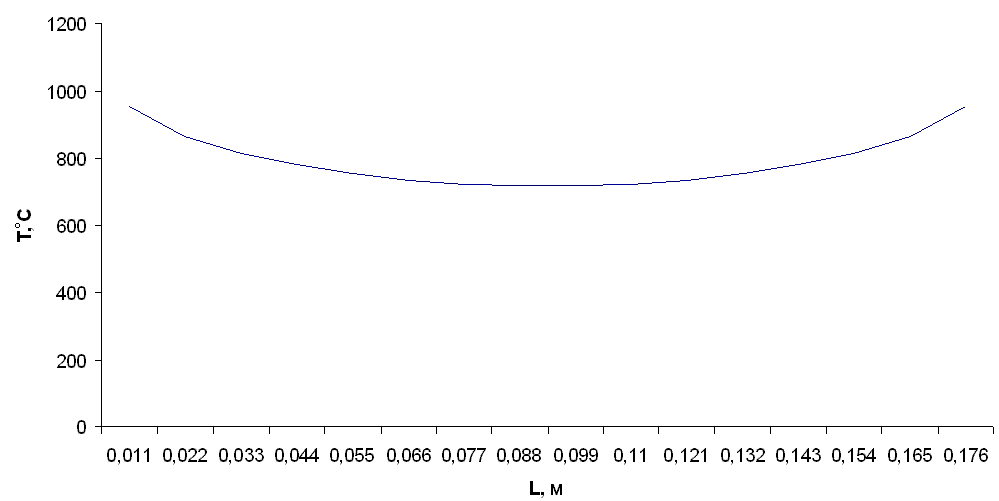
Рисунок 2.3 - График распределения температуры в зависимости от места нахождения источника теплоты
      Из графика видно, что максимальная температура возникает в начале и конце детали, что вызвано меньшым обьемом металла, в котором может распространяться тепло.
Минимальная температура возникает посередине детали, потому что тепло может распространяться в обе стороны и поэтому уменьшается его концентрация у источника теплоты (рис. 2.4).
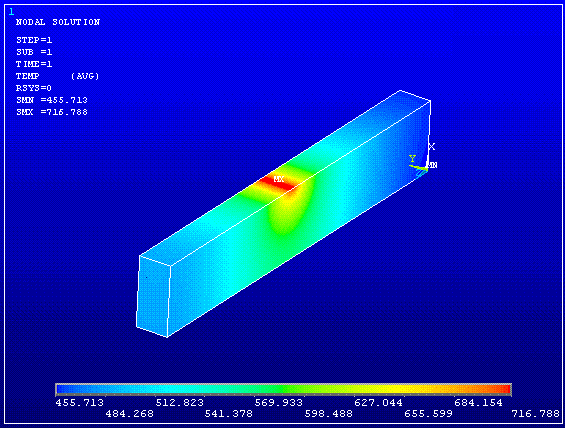
Рисунок 2.4 - Распределение температуры при расположении источника по середине
      После проведения опыта видим, что температура детали, при нахождении источника теплоты в начале и в середине детали, отличается на 33% и это нужно учитывать при назначена режимов, так как это может повлиять на качество обрабатываемой поверхности.
      Важно исследовать, как эта разница температуры будет влиять на точность обработки. Нам уже известно, что максимальная разница температур возникает при нахождении источника тепла в начале и середине детали, поэтому исследования тепловых деформаций проведем для этих двух положений. Для этого анализа закрепляем деталь по нижней поверхности от передвижения во всех направлениях, то есть имитирует магнитную плиту.
      После проведения исследования видим, что разница между максимальными температурными деформациями составляет 9%, что может визывать небольшую выпуклость поверхности, так как в местах с максимальными деформациями будет срезаться больше металла и после остывания в этих местах будет уменьшаться линейный размер.
ВЫВОДЫ
      1. Температура в начале и в конце детали превышает температуру в середине детали на 33%
      2. Температурные деформации в начале и в конце детали превышают температурные деформации в середине детали, что приводит к выпуклости обрабатываемой детали
     3. При определении критической температуры на поверхносты детали, во время назначения режимов, необходимо брать во внимание температуру, которая возникает возле торца по длине детали.
ЛИТЕРАТУРА
- Филоненко Н. Е. и др. Микроморфология граней кристаллов кубического нитрида бора. Труды ВНИИМАШ, 1968, №8.
- Бакуль В. Н., Прихна А. И. Состав, структура и свойства кубического нитрида бора. Науч.-произв. сб. «Синтетические алмазы», вып. 1, Киев, 1971.
- Харитонова М. В., Ривлин И. Я. О химических свойствах кубического нитрида бора. Науч.-техн. реф. сб. «Абразивы», вып. 5. М., НИИМАШ, 1968.
- Лавров И. В. Ермакова Т. Б. К вопросу от унификации микроскопических методик анализа зернового состава. Науч.-техн. реф. сб. «Абразивы», вып. 6. М., НИИМАШ, 1969.
- П.А Сверхтвердые материалы [Электронный ресурс]: монография /П.А. Витязь, Н.М. Олехнович, В.Б. Шипилло /http://www.itmo.by/jepter/sci-bel/183-206.pdf
- Лысанов В. С. Высокопроизводительный инструмент из эльбора. М., «Машиностроение», 1975.
- Дегтяренко Н.С. Пути повышения качества заточки режущего инструмента на заводах инструментальной промышленности. М., НИИМАШ, 1969.
- Маслов Е.Н. Основы теории шлифования металлов. М., Машгиз, 1951.- 190 с.
- Редько С.Г. Процессы теплообразования при шлифовании металлов. Изд-во Саратовского университета, 1962, - 231 с.
- Маслов Е.Н. Теория шлифования материалов. М., Машиностроение, 1974, - 320 с.
- Оптимизация технологии глубинного шлифования/ С.С. Силин, Б.Н. Леонов, В.А. Хрульков и др.; Редкол.: П.Н. Орлов (пред.). – М.: Машиностроение, 1989 – 120 с.
- Сипайлов В.А. Тепловые процессы при шлифовании и управление качеством поверхности.- М.: Машиностроение, 1978 - 167 с.
- Абразивная и алмазная обработка материалов. Справочник. Под ред. д-ра техн. наук проф. А.Н. Резникова. - М.: Машиностроение, 1977 – 384 с.
ДонНТУ > Магистры ДонНТУ ||
Об авторе |
Библиотека | Ссылки |
Отчет о поиске || Индивидуальный раздел