«Обгрунтування режимів шліфування сталі Р6М5Ф3 ельборовими кругами»
Науковий керівник:
Матюха Петр Григорович
Матеріали на тему магістреської роботи:
Про автора
Реферат на тему магістерської роботи
ВСТУП
1. ЛІТТЕРАТУРНИЙ ОГЛЯД ПО ЕЛЬБОРОВОМУ ШЛіФуВАННЮ
1.1 Фізико-механічні властивості ельбора
1.2 Хімічні властивості ельбора
1.3 Геометрія зерен эльбора
1.4 Процеси дефектоутворення в кубічному нітриду бору
1.5 Абразивний інструмент з ельбора
1.6 Якість обробленої поверхні при ельборовом шліфуванні
2. ДОСЛІДЖЕННЯ ТЕМПЕРАТУРИ ОБРОБЛЮВАЄМОЇ ПОВЕРХНІ ПРИ ВРІЗНОМУ ШЛІФУВАННІ СТАЛІ Р6М5Ф3 КРУГОМ З ЕЛЬБОРУ
2.1 Аналіз методик визначення температури на поверхні деталі при плоскому шліфуванні
2.2 Призначення режимів різання
2.3 Визначення коефіцієнта введення тепла в шліфувальний круг із ельбору
2.4 Визначення щільності теплового потоку, що виникає при шліфуванні
2.5 Розрахунок температури і температурних деформацій в середовищі «ANSYS»
ВИСНОВКИ
ЛІТЕРАТУРА
ВСТУП
      Актуальність
      Першорядне значення для прискорення технічного прогресу і оснащення всіх галузей народного господарства новою технікою має подальший швидкий розвиток усіх сучасних галузей машинобудування.
      Шліфування, будучи одним з найбільш продуктивних методів обробки металів, що забезпечує низькі висотні параметри шорсткості оброблюваної поверхні, високу точність форми і розмірів деталей. Шліфуванням можна обробляти практично всі матеріали.
      У зв'язку з цим досить актуальним і перспективним напрямком є освоєння ельборових кругів на металевій зв'язці. Ці шліфувальні круги володіють високою ріжучою здатністю, великим періодом стійкості, але потребують постійної правки електроерозійним впливом на зв'язку круга.
    Так як сучасний парк шліфувальних верстатів практично не володіє засобами для електроерозійні правки шліфувальне кола, то модернізація існуючих шліфувальних верстатів так само є на сьогоднішній день досить актуальною темою.
      Цілі і завдання магістерської роботи
      При виконанні магістерської роботи були поставлені наступні основні завдання:
      - виконати літературний огляд за призначенням режимів шліфування ельборовими кругами;
      - дослідити вплив положення шліфувального кола на заготівці при плоскому шліфуванні на температуру поверхні деталі в середовищі «ANSYS»;
      - модернізувати внутрішліфовальний верстат для електроерозійні правки круга та шліфування за пружною схемою;
      - визначити сили підтискання круга до зразка за критерієм міцності зерен;
      - призначити режими шліфування сталі Р6М5Ф3 ельборовим кругом;
      - дослідити миттєву ріжучу здатність круга при внутрішньому шліфуванні Р6М5Ф3 за пружною схемою;
      - визначити механічні режими і режими електроерозійних впливів при внутрішньому шліфуванні Р6М5Ф3.
      Метою даного реферату є літературний огляд по ельборовому шліфуванню і дослідження впливу положення ШК на поверхні заготовки на температуру засобами «ANSYS»
1. ЛІТТЕРАТУРНИЙ ОГЛЯД ПО ЕЛЬБОРОВОМУ ШЛіФуВАННЮ
1.1 Фізико-механічні властивості ельбора
      Основою крісталлографічної форми кубічному нітриду бору є комбінація позитивного і негативного тетраедров [1]. Рідше зустрічаються слабко розвинені грані куба і ромбододекаедра. Поверхня граней великих кристалів найчастіше недосконала, дзеркальні грані зустрічаються досить рідко, в основному на дрібних кристалах розміром 0,06 - 0,08 мм. Зростання кристалів відбувається плоскими шарами, пірамідки і горбки на гранях тетраедров різного знака. Грані позитивного тетраедра ростуть повільніше, мають більший розвиток і більш різноманітний мікрорельєф. В результаті сублімації кубічного нітриду бора вершини зерен великих кристалів притупляют, а їх ребра мають зазубрені обриси.
      Форма, розміри, мінеральний склад та особливості внутрішньої структури кристалів ельбора обумовлені технологічними особливостями синтезу.
      Фізико-механічні властивості кристалів наведені в таблиці 1.1 [2]
Таблиця 1.1 - Фізико-механічні властивості кристалів
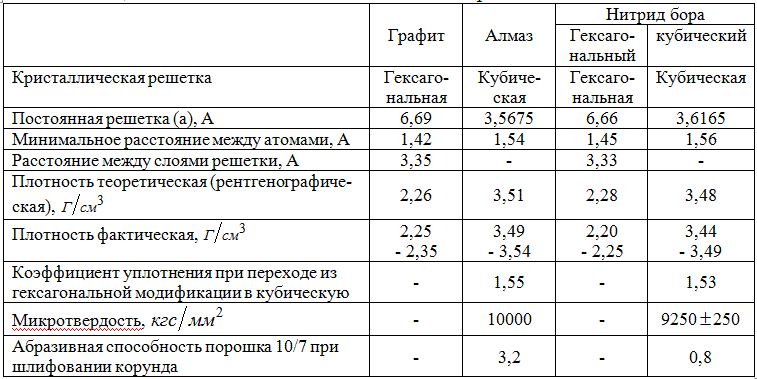
1.2 Хімічні властивості ельбора
      Абразивний матеріал ельбор складається з кубічного нітриду бору - BN (91 - 95%) і супутніх йому домішок: гексагонального нітриду бору BN (1 - 2,5%), кремнію (0,05 - 0,15%), заліза (0, 07 - 0,10%), алюмінію (0,05 - 0,25%), кальцію (0,05 - 0,20%), магнію (1 - 1,5%) і вільного вуглецю (0,6 - 1 %) [2].
      Дослідження [3] на абразивних зернах з кубічному нітриду бору, розмір зерен основної фракції яких змінюється від (-5 3) до (-250 +200) мк, показали, що концентровані і розбавлених кислоти (соляна, сірчана, азотна, фосфорна, плавіковая), суміш концентрованої сірчаної кислоти з сульфатом калію, окислювачі (суміш пергідроля з азотної кислотою і царська горілка), а також розчини лугів не роблять хімічного впливу на кубічний нітрид бору. Хімічна стійкість спостерігалася при температурах кипіння кислот з витримкою від 1 до 24 ч.
      Кубічний нітрид бору розкладається при сплавленіі порошку з лугами в інтервалі температур 400 - 700 ° С з утворенням Борат та виділенням аміаку. При температурі 400 ° С в трубчастою печі протягом 30 хв мікропорошок кубічному нітриду бору крупності (-5 3) мк розкладається на 55%, а крупності (-250 + 200) мк - тільки на 6%.
      При температурі 700 ° С розкладання відбувається більш інтенсивно: зерна (-5 3) мк і зерна (-50 +40) мк розкладаються повністю, зерна (-100 + 80) мк - на 90%, а зерна (-250 + 200 ) мк - на 88%.
      Кубічний нітрид бору не цілком стійкий до перегрітого водяного пару при температурі 900 ° С: за 2 години обробки вдалося розкласти 4,7% зерен, за 4 ч -7%, а за 6 ч-10%.
1.3 Геометрія зерен эльбора
      Встановлено, що ізометричність зерен ельбора вищя, ніж алмаза і електрокорунда [4]. Це пов'язано зі специфікою його подрібнення і полікрісталлічною будовою зерен. Середнє значення коефіцієнта форми зерен, що представляє відношення довжини зерна до його ширині (l: b), при спостереженні під мікроскопом для алмаза АСТ 16 - 25 дорівнює 1,44 - 1,50, електрокорунда ЕБ 32 - 50 - 1,47 - 1, 48 і ельбора Л12 - 1,38.
      Зі зменшенням номера зернистості зерен ельбора радіус округлення і кут загострення ріжучих кромок зменшуються, а відсоток гострих кутів зростає (табл. 1.2).
Таблица 1.2 Геометрія зерен эльбора
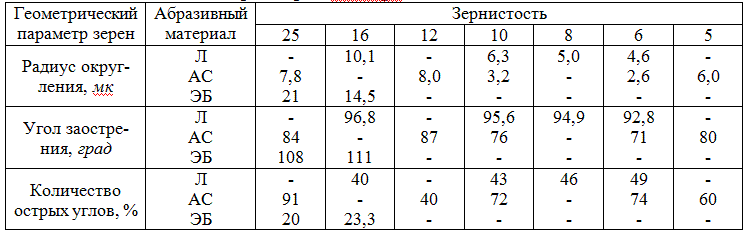
1.4 Процеси дефектоутворення в кубічному нітриду бору
      Зміни фізичних характеристик ВТМ в залежності від параметрів синтезу і зовнішніх впливів, наприклад температурного відпалу або опромінення, пов'язані з трансформацією дефектної структури цих матеріалів, що дозволило розробити фізичні принципи конструювання СТМ спрямовані зміни їх дефектної структури, корелюють із зміною механічних характеристик матеріалів. На цих принципах розроблений ряд оригінальних технологій, істотним чином підвищують міцнісні характеристики алмаза і BN K [5].
      Зокрема, в BN виявлені закономірні осціллірующіе зміни дефектної структури при термообробці, корелюють зі зміною його фізичних характеристик. Встановлено існування вузької температурної зони (870 10 К), що розділяє якісно різні стану дефектної структури BN K, і виявлений механізм взаємодії дефектів на нізкотемпе-ратурном (770-870 К) і високотемпературних (870-1020 К ) ділянках термообробки BN K. Показано, що при термообробці при 870 К в BN K формується особливий стан дефектної структури, при якій модуль пружності досягає найбільшого значення, а внутрішнє тертя стає мінімальним в результаті ефективної блокування діслокацій закріплюються центрами, відбувається внаслідок їх інтенсивної міграції з обсягу до дислокації. Показано, що реакція відпалу дефектів має перший порядок і характеризується різними механізмами взаємодії дефектів: на низькотемпературному ділянці (770-870 К), що характеризується невеликою величиною енергії активації (0,2 еВ), визначальним процесом є міграція власних або прімесних междоузельних атомів; більш високу значення енергії активації (0,7 еВ) для другої дільниці (870-1020 К) приписано міграції вакансій або, що більш імовірно, дівакансій.
      Виявлено центри люмінесценції, у тому числі мессбауеровскього типу, зумовлені крапковими дефектами, і розвинені модельні уявлення породжують їх дефекти. Встановлено, що центри GC-1 і GC-2 з БФЛ енергією 1,76 і 1,63 еВ є дефектами вакансіонного типу на основі вакансій азоту і бору відповідно і технологічної домішки. Природа центрів PF (2,8-3,6 еВ) інтерпретовані в моделі донорно-акцепторній рекомбінації. Передбачається, що центри PF-це донорно-акцепторні пари на основі міжвузольних атомів бору та азотних вакансій. Центр PC -3 (1,79 еВ) є дефектом прімесного типу, породжувані включенням Al2O3: Cr3 +. Встановлена природа широких смуг спектрів катодолюмінесценціі: С - смуга (1,55-1,85 еВ) - дислокаційної, смуги А і В (1,85 і 3,25 еВ) - прімесно-вакансіонне на основі вакансій по бору та азоту відповідно.
      За даними внутрішнього тертя встановлено, що високотемпературний фон внутрішнього тертя в BNK носить дислокаційної характер і викликаний рухом геометричних перегинів на дислокації в присутності закріплюються центрів, в якості яких виступають вакансіонние комплекси. Зроблено висновок, що природа релаксаційний піків в спектрі внутрішнього тертя обумовлена переорієнтацією нестійких вакансіонних комплексів в прімесном поле механічних напружень з енергією активації 0,7-2,2 еВ.
      Встановлена природа щодо стійкого до отжигу піка внутрішнього тертя при 360 К BN K, зумовлена переорієнтацією дівакансій бору в змінному полі пружних напружень по типу параупругой релаксації Зінера. Показано, що характер температурних залежностей коефіцієнта лінійного розширення BNK, встановлений з резонансних вимірювань, визначається станом його дефектної структури. Виявлено існування амплітудної залежності внутрішнього тертя в BNK і показано, що при кімнатній температурі рух діслокацій контролюється пайерлсовскім механізмом. При підвищених температурах рух діслокацій визначається їх взаємодією, по меншій мірі, з двома типами закріплюються центрі, що представляють собою вакансіонні комплекси різної структури.
      Технологія підвищення міцності порошків алмазу і BN, sub> K sub>, заснована на модифікування дефектної структури СТМ, дозволила підвищити міцність порошків на 20%.
1.5 Абразивний інструмент з ельбора
      Перші дослідно-промислові партії інструменту з ельбора були виробленні на Ленінградському абразивному заводі «Ілліч» в 1964 р., а з 1965 р. почалося їх промислове виробництво. В даний час випускають з ельбора абразивний інструмент широкої номенклатури: різні види шліфувальних кіл, брусків, шліфувальну шкірку, пасти [6].
      Інструменти з ельбора випускаються на керамічних, органічних та металевих зв'язках. Створення спеціальних керамічних связок багато в чому зумовило ефективне використання ельбора як абразивного матеріалу в інструменті.
      Інструменти на керамічних зв'язках відрізняються міцним закріпленням ельбора в абразивному шарі, високою стійкістю профілю. Твердість інструменту з ельбора на керамічних зв'язках, як і твердість звичайного абразивного інструменту з традиційних матеріалів, характеризує міцність утримання зерен зв'язкою і вимірюється згідно ГОСТ 3751 - 47.
      Промисловість випускає інструмент наступних характеристик по твердості: М (М2, МЗ), CM (СМ1, см2), С (С1, С2), СТ (СТ1, СТ2, СТЗ), Т (Т1, Т2). Твердість ельборомістячий частини кіл та брусків визначається на приладі «Роквелл» кулькою діаметром 2 дюйми при навантаженні 60 кгс, потім по середнім значенням твердості, отриманими на приладі, і по таблиці 2 ГОСТ 3751 - 47.
      Структура інструменту з ельбора на керамічних зв'язках характеризується вмістом ельбора і наповнювача в одиниці об'єму робочої (ельборомістячий) частини кола, вираженим у відсотках, і позначається певним номером (від № 6 до № 12) залежно від зернистості ельбора. Чим вище номер структури, тим більше зв'язки і менше зерна в одиниці об'єму інструменту при однаковій твердості. У загальному обсязі виробництва інструменти з ельбора на керамічних зв'язках складають 60%.
      Круги з ельбора на органічних зв'язках за формою, характеристикам і технології виготовлення подібні аналогічно алмазному інструменту. Круги на металевих зв'язках випускаються, як правило, невеликими партіями за спеціальним замовленням. Поряд з відомими раніше способами виготовлення інструментів з надтвердих матеріалів на металевих зв'язках розроблені і застосовуються нові.
      Основні типи інструменту з ельбора, що випускаються промисловістю:
        а) шліфувальні круги прямого профілю для внутрішнього шліфування діаметром 3 - 60 мм;
        б) шліфувальні круги прямого профілю для круглого, зовнішнього та плоского шліфування діаметром 70 - 400 мм;
        в) шліфувальні круги фасонного профілю для профільного шліфування, у тому числі для резьбошліфування, діаметром 50—500 мм;
        г) шліфувальні круги тарельчатого профілю діаметром 75 - 125 мм для заточування металорізального інструмента;
        д) шліфувальні круги чашкового профілю діаметром 50 - 200 мм для заточування металорізального інструмента і плоского шліфування;
        е) бруски різних розмірів і шліфувальна шкурка.
1.6 Якість обробленої поверхні при ельборовом шліфуванні
      Закономірності впливу характеристики кола і режимів різання на кідькість остаточного аустеніту аналогічні закономірностям, отриманим для температури шліфування. Вище було показано, що при шліфовуванні кругами з ельбору температури, що виникають в поверхневому шарі, значно менше, ніж при шліфуванні абразивними і алмазними колами. У зв'язку з цим при ельборовом шліфуванні зменшується небезпека структурних змін в поверхневому шарі деталей та інструментів (табл. 1.3) [7].
Таблица 1.3 – Структурні зміни в поверхневому шарі
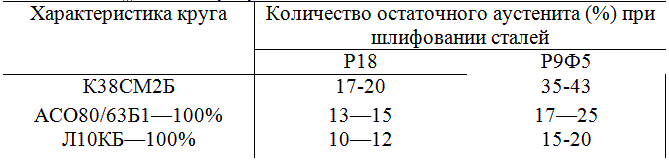
      Під ВНДІ було встановлено, що при плоскому шліфуванні зразків із сталей Р18, Р6М5, Р9Ф5 колами чашкові форми на органічних зв'язках в діапазоні режимів: V КР = 15-30 м/хв, Sпр = 1-4 м/хв, t = 0,01-0,04 мм/дв.хід, без охолодження кількість остаточного аустеніту не перевищує 20%. Отже, при цих умовах обробки в поверхневому шарі швидкорізальних сталей не відбувається істотних структурних змін, які можуть привести до зниження стійкості інструменту. Ці дані узгоджуються з досвідами по вимірюванню температур. В умовах переривчастого шліфування без обліку накопичення тепла значення Т для дослідженого діапазону режимів різання були менше 700 ° С і не могли призвести до структурних змін.
      Досліди показали, що в процесі алмазного і кубонітового шліфування спостерігається розпад остаточного аустеніту, мартенсіта та дрібнодисперсних карбідів. Кількість залишкового аустеніту зменшується, а в поверхневих шарах відсутній троостосарбітна (сталь 40х) і троосто-мартенситних (сталь 111X15) зони.
2. ДОСЛІДЖЕННЯ ТЕМПЕРАТУРИ ОБРОБЛЮВАЄМОЇ ПОВЕРХНІ ПРИ ВРІЗНОМУ ШЛІФУВАННІ СТАЛІ Р6М5Ф3 КРУГОМ З ЕЛЬБОРУ
2.1 Аналіз методик визначення температури на поверхні деталі при плоскому шліфуванні
2.1.1 Аналіз методик визначення температури на поверхні теоретичним способом
      В загальному випадку існує два різновиду методик визначення температури на поверхні деталі, а саме теоретична і експериментальна. Кожна з них має як пе-реваги так і недоліки.
      Завдання теоретичних досліджень полягає в визначенні загальних закономірностях виникнення і розподілу теплоти в процесі шліфування і температур, які при цьому розвиваються. Теоретичний розрахунок температури шліфування в основному зводиться до рішення задачі Фур’є. Спочатку про температуру деталі судили по характеру і інтенсивності фазових перетворень в поверхневому шарі при шліфуванні.
      Систематичне вивчення теплових явищ при шліфуванні почалося з експери-ментального визначення залежності контактної температури в зоні обробки від умов шліфування з використанням термопари []. В подальшому такий метод виміру температури був значно розширений і використаний багатьма дослідниками. Узагальнені результаті можно отримати тільки за допомогою теоретичного розрахунку температури шліфування у поєднанні з якісною експериментальною перевіркою.
      Створенню сучасної теплофізики шліфування сприяли теоретичні дослідження температур, які розвиваються при терті. В роботі Дж. Иєгера [] розглянуті два основних випадки розрахунку температур при терті з постійною швидкістю. В першому випадку вважалось, що поверхня (джерело) тертя має форму полоси, а в другому випадку – форму стержня квадратного перетину. Отримані формули, з заданим приближенням, дали змогу визначити середні температури, які розвиваються при терті.
      С.Г. Редько [9] запропонував метод визначення температури шліфування, який базується на роботі одиничних абразивних зерен круга і послідовному накладенні елементарних теплових імпульсів від зерен, причому нагрів шліфуємої поверхні приймається як результат такого багатократного накладення.
      Із диференціального рівняння теплопровідності отримані рівняння для температури на поверхні контакту абразивного зерна і в глибину деталі; прийняті до уваги форма, просторове положення, швидкість руху абразивного зерна і інтервали між діями джерела теплоти. Наприклад, максимальна температура в зоні контакту круга с деталлю при сумарній дії теплових імпульсів від усіх зерен, що діють в зоні контакту
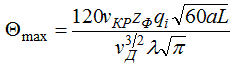
где VКР - окружная швидкість круга;
        ZФ - кількість абразивних зерен на одиниці робочої поверхні круга;
        qi - середня напруженість теплового потоку;
        L - довжина контакту круга с деталлю;
        а - температуропровідність матеріалу деталі;
        VД - швидкість деталі.
2.1.2 Експериментальні методи визначення температури поверхні при шліфуванні
      Експериментально температуру шліфуємої деталі виміряють за допомогою термопар, по структурним перетворенням в поверхневому шарі шліфуємої деталі і дистанційних датчиків [10]. Найбільш широко використовується вимір температур за допомогою штучних і напівштучних термопар (рис 2.1)
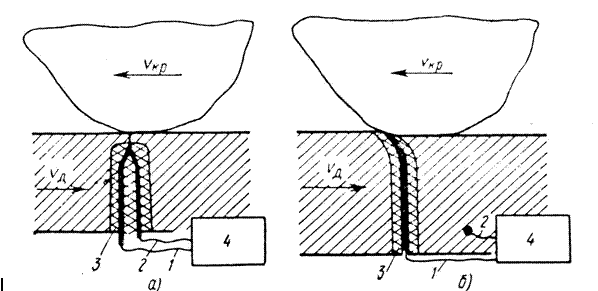
Рисунок 2.1 – Термопари:
а – штучна; б – напівштучна; 1 і 2 – провідники;;
3 – електроізоляція (слюда); 4 – прилад для реєс трації термо-ЕДС.
.
      Штучну термопару найчастіше виготовляють із хромель-конелевих проволочок діаметром 0,1 мм і з’єднують з осцилографом (з зусиллям або без зусилля). Між проволочками термопари вкладають електроізоляційні прокладки (листочки слюди) товщиною 0,1-0,2 мм. Діаметр голівки термопари 0,2-0,3 мм. Кінці термопари підключають до шлейфу осцилографа (Н-700 та інш.). Напівштучна термопара образовує спай в момент різання зерном.
2.2 Призначення режимів різання
      Призначені режими шліфування повинні забезпечувати досягнення в процесі обробки потрібні точність і якість поверхневого шару деталі, що шліфується. Відсутність. Відсутність дефектів поверхневого шару (прижогів та мікротріщин) є головною умовою успішного впровадження процесу шліфування в виробництво. Вимоги гарантованого досягнення бездефектної обробки при глибинному шліфуванні визначені в ході комплексних досліджень якості поверхневого шару деталей [11].
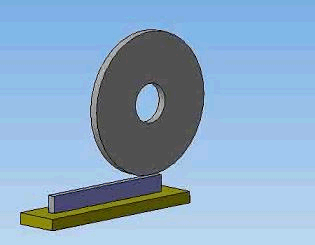
Рисунок 2.2 - Анімация процесу плоского шліфувания:
кадрів - 7, повторів - 7, розмір - 130 КБ.
      Проведені дослідження температурного поля заготовки при глибинному абразивному шліфуванні дозволили встановити, що при похилому русі джерела тепла в умовах інтенсивного охолодження кількість теплоти, що йде в обробляємо поверхню, в залежності від вимог обробки складають 32 – 83 % загальної кількості теплоти, що виділяється в процесі обробки. Причому, чим більше кут нахилу джерела теплоти і менша швидкість заготовки, тим більша кількість теплоти йде в шар металу, що знімається с заготовки і тим ближчі максимальні значення температури на її поверхні до передньої границі джерела теплоти. Для забезпечення відводу як можна більшої кількості теплоти в шар металу, що знімається при глибинному шліфуванні с заготовки, кінематичні параметри процесу повинні задовольняти наступній вимозі:
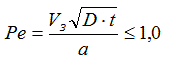
где VЗ - швидкість заготовки, м/с;
        D - діаметр шліфувального круга, м;
        t - глибина шліфування, м.
      Інтенсивний теплообмін в зоні шліфування, граничне значення коефіцієнта якого в умовах подачі МОР під тиском a0=(3.5...5)*103 Вт/м2 0C, є ефективною мірою зниження температури на дільниці контакту круга с заготовкою.
2.3 Визначення коефіцієнта введення тепла в шліфувальний круг із ельбору
      Розглянемо питання про долю тепла, яка йде в шліфувальний круг. Це за-вдання повинно рішатися із запропонування дискретності контакту круга і деталі. Якщо для шліфуємої поверхні швидка зміна теплових імпульсів на найбільш активних зернах зливається в суцільний фон, то для шліфувального круга контакт завжди є дискретним, який діє на протязі кратного часу, який залежить від швидкості круга. Переважне тепловиділення на зернах у зрівнянні із зв’язкою, дозволяє моделювати кожне зерно у вигляді напівпростору, яке має контакт на невеликій ділянці с другим напівпростором, що рухається відносно першого зі швидкістю периферії круга. Питання о розподіленні тепла між цими напівпросторами вирішується на основі равентсва середніх контактних температур. Ця умова після невеликих перетворень приведе до формули для визначення коефіцієнта введення, що показує яка частка тепла йде в напівпростір (в даному випадку в деталь)[12]
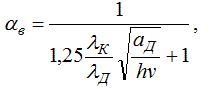
где LД - коефіцієнт теплопровідності деталі, Вт/м 0C;
        LК - коефіцієнт теплопровідності круга, Вт/м 0C;
        аД - коефіцієнт температуропровідності деталі, м2/с;
        h - середній радіус площадки контакту зерна с виробом.
2.4 Визначення щільності теплового потоку, що виникає при шліфуванні
      Так як шліфування ведеться без використання МОР, можна обмежитися за-вданням на всіх поверхнях граничних умов другого роду. Під джерелом необхідно задати усереднений по зоні контакту тепловий потік, а на інших поверхнях - нульовий тепловий потік.
      Для визначення щільності теплового потоку розрахуємо складову сили різання по емпіричній залежності [13]

      Щільність теплового потоку буде рівнятися:
q=Pz*Vк/S
где S - площина контакту круга з заготівкою, м2.
2.5 Розрахунок температури і температурних деформацій в середовищі «ANSYS»
      Щоб дослідити вплив місця роботи шліфувального круга на оброблюваної поверхні на температуру, розбиваємо поверхню деталі на частки, які дорівнюють площі контакту круга і деталі. На ці частки послідовно прикладаємо щільність теплового потоку, розраховану раніше і будуємо графік розподілу температури в деталі, в залежності від місця знаходження джерела тепла (рис. 2.3)
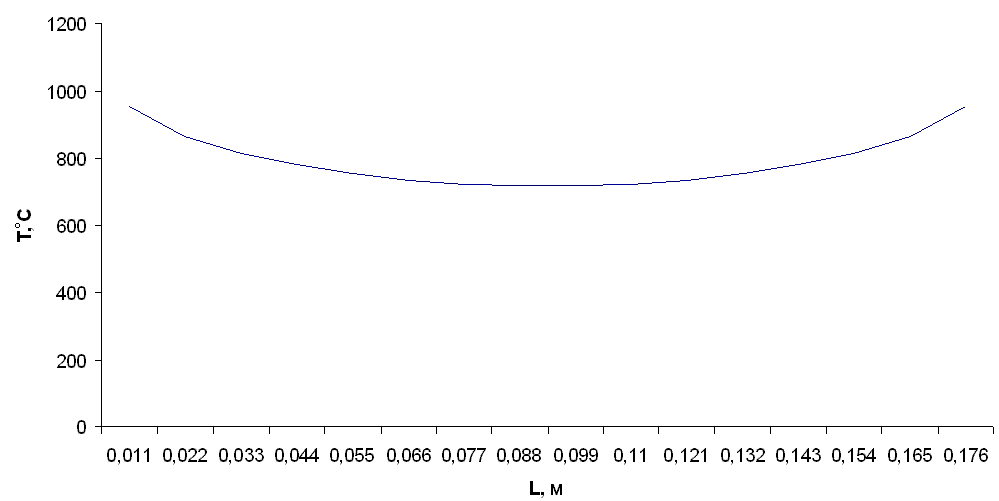
Рисунок 2.3 - Графік розподілу температури в залежності від місця знаходження джерела теплоти
      З графіку бачимо, що максимальна температура виникає на початку і кінці деталі, що визвано наявністю меншої кількості металу, в якому може розповсюджуватися тепло.
Мінімальна температура виникає посередині деталі, тому що тепло може розповсюджуватися в обидві сторони і тому зменшується його концентрація біля джерела теплоти (рис. 2.4).
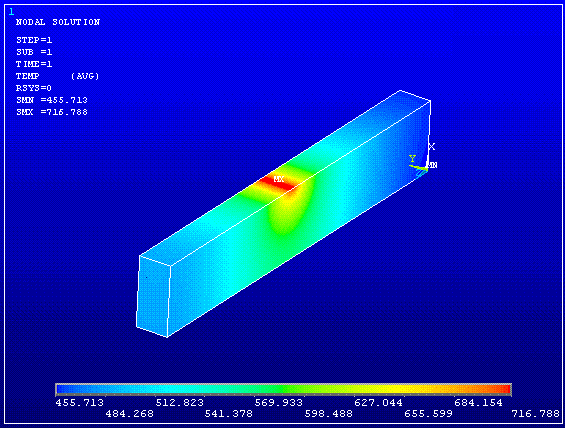
Рисунок 2.4 - Розподіл температури при знаходженні джерела по середині
      Після проведення досліду бачимо, що температура деталі, при находженні джерела теплоти на початку і в середині деталі, відрізняється на 33% і це потрібно враховувати при назначені режимів, так як це може вплинути на якість оброблюваної поверхні.
      Важливо дослідити, як ця різниця температури буде впливати на точність обробки. Нам вже відомо, що максимальна різниця температур виникає при нахо-дженні джерела тепла на початку і середині деталі, тому дослідження теплових деформацій проведемо для цих двох положень. Для цього аналізу закріпляємо деталь по нижній поверхні від пересування в усіх напрямках, тобто імітуємо магнітну плиту.
      Після проведення досліду бачимо, що різниця між максимальними температурними деформаціями складає 9%, що може визивати невелику випуклість поверхні, так як в місцях з максимальними деформаціями буде зрізатися більше металу і після охолодження в цих місцях буде зменшуватися лінійний розмір.
ВИСНОВКИ
     1. Температура на початку і в кінці деталі перевищує температуру в середині деталі на 33%.
     2. Температурні деформації на початку і в кінці деталі перевищують температурні деформації в середині деталі, що призводить до опуклості оброблюваної деталі
     3. При визначенні критичної температури на поверхні деталі, під час призначення режимів, необхідно брати до уваги температуру, яка виникає біля торця по довжині деталі.
ЛІТЕРАТУРА
- Филоненко Н. Е. и др. Микроморфология граней кристаллов кубического нитрида бора. Труды ВНИИМАШ, 1968, №8.
- Бакуль В. Н., Прихна А. И. Состав, структура и свойства кубического нитрида бора. Науч.-произв. сб. «Синтетические алмазы», вып. 1, Киев, 1971.
- Харитонова М. В., Ривлин И. Я. О химических свойствах кубического нитрида бора. Науч.-техн. реф. сб. «Абразивы», вып. 5. М., НИИМАШ, 1968.
- Лавров И. В. Ермакова Т. Б. К вопросу от унификации микроскопических методик анализа зернового состава. Науч.-техн. реф. сб. «Абразивы», вып. 6. М., НИИМАШ, 1969.
- П.А Сверхтвердые материалы [Электронный ресурс]: монография /П.А. Витязь, Н.М. Олехнович, В.Б. Шипилло /http://www.itmo.by/jepter/sci-bel/183-206.pdf
- Лысанов В. С. Высокопроизводительный инструмент из эльбора. М., «Машиностроение», 1975.
- Дегтяренко Н.С. Пути повышения качества заточки режущего инструмента на заводах инструментальной промышленности. М., НИИМАШ, 1969.
- Маслов Е.Н. Основы теории шлифования металлов. М., Машгиз, 1951.- 190 с.
- Редько С.Г. Процессы теплообразования при шлифовании металлов. Изд-во Саратовского университета, 1962, - 231 с.
- Маслов Е.Н. Теория шлифования материалов. М., Машиностроение, 1974, - 320 с.
- Оптимизация технологии глубинного шлифования/ С.С. Силин, Б.Н. Леонов, В.А. Хрульков и др.; Редкол.: П.Н. Орлов (пред.). – М.: Машиностроение, 1989 – 120 с.
- Сипайлов В.А. Тепловые процессы при шлифовании и управление качеством поверхности.- М.: Машиностроение, 1978 - 167 с.
- Абразивная и алмазная обработка материалов. Справочник. Под ред. д-ра техн. наук проф. А.Н. Резникова. - М.: Машиностроение, 1977 – 384 с.
ДонНТУ > Магистры ДонНТУ ||
Про автора