Реферат по теме выпускной работы
Введение
Топливно-энергетический комплекс является основой развития экономики любого государства. В настоящее время для получения энергии в большинстве случаев используется органическое топливо (уголь, нефть, природный газ и др.). Особенную роль играет коксохимическое производство, которое производит продукцию, искусственно получаемую из угольного сырья, — бензол, каменноугольную смолу, ее химические продукты, пек, пековий кокс и др.
Коксохимические заводы являются достаточно крупными предприятиями на которых осуществляется термохимическая переработка сырья с целью получения разных видов кокса. Процесс коксования сопровождается образованием веществ, которые в дальнейшем могут использоваться в качестве сырья для получения товарных продуктов. Авдеевский коксохимический завод является одним из многих крунпых производителей в отрасли.
Существует огромное количество способов переработки сырья и обезвреживания газовых выбросов. Выбор метода зависит от многих показателей: химического состава сырья или газа, который очищается наличие механических примесей, желательной степени очистки газа или степена превращения сырья в продукт и тому подобное.
Цель
Целью данной работы является исследование эффективности использования каталитических методов в коксохимической промышленности.
Задачи
Для того, чтобы достичь цели были поставлены следующие задачи:
- рассмотреть механизм катализа и каталитических реакций при участии разных веществ;
- рассмотреть существующие каталитические процессы в условиях ОАО «АКХЗ»
- определить недостатки рассмотренных процессов и предложить пути их устранения;
- определить возможность применения каталитических методов для очистки выбросов при грануляции электродного пека.
Актуальность
Актуальной проблемой на сегодняшний день является совершенствование установки мокрого катализа. Эффективными методам повышения степени конверсии SO2 в SO3 есть двойной катализ и окисление SO2 под давлением. Отходящие газы от участка грануляции и расфасовки электродного пека на ОАО «АКХЗ» на данный момент отводятся в атмосферу без надлежащей очистки, поэтому является необходимым строительство установки термокаталитического обезвреживания газовых выбросов.
1 АНАЛИТИЧЕСКИЙ ОБЗОР КАТАЛИТИЧЕСКИХ МЕТОДОВ[выдержки]
1.1 Понятие катализа
Катализ имеет большое значение в природе и современной жизни: каталитическими являются почти все биохимические процессы, большинство реакций, которые изучают у лаборатории, и технологических процессов которые реализованы в промышленности.
Первым случаем использования катализаторов считается образование этилового эфира из спирта с помощью серной кислоты, открытое в VIII столетии нашей эры. Первое большое промышленное использование катализа осуществлено в 1746 году по нитрозному (камерному) способу производства серной кислоты. Причина каталитического действия разных веществ заключается в изменении механизма реакции в присутствии катализатора, то есть возникновении нового или нескольких путей реакции, которые быстро протекают. Механизм реакции — это совокупность элементарных химических стадий, которые имеют место в реакционной системе при переходе от исходных веществ к продуктам.
Классификацию каталитических процессов можно провести по нескольким отличиям. По фазовому составу компонентов каталитические реакции обычно относят к гомогенному катализу (если исходные вещества, продукты реакции и катализаторы находятся в единственной фазе) или к гетерогенному катализу (реакционная смесь и катализатор находятся в разных фазах).
В гомогенном катализе даже очень маленьких количеств катализатору (от 10-13 моль) достаточно для ускорения превращения большого количества реагентов в продукты, потому что катализатор может использоваться многократно. Экспериментально установлено, что скорость гомогенной химической реакции прямо пропорциональная концентрации катализатору. Этот факт подтверждает, что катализатор действительно принимает участие в реакции, при этом он образует неустойчивые промежуточные соединения, и определяет протекание реакции по другому, чем при его отсутствии, пути.
Каталитическое действие при гетерогенном катализе связывают с наличием на поверхности твердых тел активных центров, природа и число которых часто неизвестно[1].
В качестве катализаторов обычно используют твердые вещества и изучают в основном системы «газ-твердое тело» и «жидкость-твердое тело». Реже используют жидкие катализаторы, которые являют собой кислоты (например, H2SO4 или H3PO4), иногда растворы активных веществ в воде или органические растворители.
Важное место в теории и практике гетерогенного катализа занимает «правило Борескова» о приблизительном постоянстве удельной каталитической активности веществ. Исследования показали что удельная каталитическая активность (для ряда однокомпонентных оксидных и металлических катализаторов) не зависит от дисперсности активного компоненту и способу приготовление при неизменном составе катализатору.
Правило Борескова, которое выполняется, как правило, для стадийного механизма при повышенных температурах, базируется на представлениях о катализаторе и реагирующих веществах как единой каталитической системы, в которой химические превращения претерпевают не только реагенты под влиянием катализатора, но и катализатор изменяет свой состав и свойства в результате взаимодействия с реактивами. В результате под воздействием реакционной смеси устанавливается стационарный состав какой определяет удельную каталитическую активность, которая не зависит от исходного состояния поверхности катализатору, то есть от условий его приготовления и предыдущей обработки[3].
Исследования гетерогенного катализа показали, что каталитическая реакция протекает на поверхности катализатора, потому для объяснения сущности вопроса необходимо прежде всего понимание процесса адсорбции. Адсорбция — это процесс самовольного изменения концентрации вещества на грани распределения фаз, которое сопровождается уменьшением энергии Гиббса. В гетерогенном катализе адсорбентом является катализатор, адсорбатом — молекула реагирующего вещества. Различают физическую адсорбцию и хемосорбцию, хотя между ними нет четкого предела. Из двух процессов адсорбции только хемосорбция приводит к заметному изменению энергетического состояния адсорбируемой молекулы и существенному увеличению ее реакционной способности за счет снижения энергии активации, что и объясняет каталитический эффект. Однако физическая адсорбция может предшествовать хемосорбции и является стадией каталитического процесса[1].
Гетерогенно-каталитическая реакция являет собой сложный процесс, который состоит из следующих стадий (рис. 1), :
- диффузия исходных веществ из объема газовой или жидкой фазы до внешней и внутренней поверхностям катализатору;
- адсорбция реагирующих веществ на поверхности катализатора;
- химическая реакция на поверхности катализатора;
- десорбция продуктов реакции;
- диффузия продуктов реакции от внутренней и внешней поверхностей катализатора в объем.
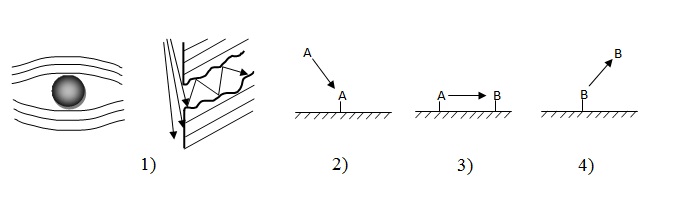
Рисунок 1 — Упрощенная схема каталитического процесса на поверхности твердого катализатора
Общая скорость такого сложного процесса определяется скоростью наиболее медленной стадии, которая часто имеет название лимитирующей стадии.
На внешнюю диффузию влияют размер и форма частей катализатору, соотношение между объемом и диаметром реактора и объемная скорость. От них зависит образования каналов, по которым протекают реагенты, режимы этих потоков, степень обратного перемешивания и времени контактирования. Внутренняя диффузия зависит от пористой структуры катализатора. По размеру поры условно разделяются на три категории: микропоры диаметром < 15 A, мезопори диаметром от 15 к 150 A и макропоры диаметром > 150 A. Диаметр пор обусловливает внутреннюю диффузию. Основную часть общей поверхности многих катализаторов складывает внутренняя поверхность, потому именно на ней происходит большая часть взаимодействий и столкновений молекул реагентов[5].
О подобии механизмов гетерогенного и гомогенного катализа можно судить по тому, что стадия хемосорбции в первом аналогична стадии образования промежуточного соединения во втором. Отличие их заключается в том, что на поверхности гетерогенного катализатора, благодаря наличию нескольких типов активных центров, могут образоваться разные типы активированных комплексов, которые приводят к появлению разных продуктов реакции.
1.2 Катализаторы в промышленных процессах
В промышленности катализаторы представляют собой как правило, многокомпонентные системы.
Добавлеие к катализаторам в небольших количествах веществ, которые называются промоторами, повышает его активность за счет увеличения поверхности, выборочности и срока действия.
Промотором (активатором) называют добавку к катализатору небольшого количества вещества, которое сам по себе может быть каталитически неактивными по отношению к определенной реакции, но очень повышает активность собственно катализатора. Эффективность действия промоторов зависит от их количества. При определенном соотношении активного компонента и промотора наблюдается максимум активности.
По классификации, данной Ч. Сеттерфилдом, промоторы разделяют на два основных класса: текстурные, которые предпринимают физическое действие, и структурные, природа влияния которых химическая.
Текстурные промоторы присутствуют в катализаторе, как правило, в виде мелких частиц и имеют тормозящее действие на спекание активной фазы. Структурные (химические) промоторы изменяют химический состав катализатора.
Катализаторы на носителях являются широко распространенным типом сложных контактных масс. При подборе носителей следует иметь в виду их определенные характеристики: необходимые механические свойства, в том числе прочность на раздавливание и стирание, твердость; стабильность в условиях реакции и регенерации (в том числе термостойкость и коррозийная стойкость); пористость, которая определяется средним размером пор и распределением объема пор по радиусам.
На данный момент широко используются синтетические носители какие имеют сравнительно с природными материалами ряд преимуществ. К таким можно отнести: постоянство химического состава; возможность регуляции пористой структуры, что позволяет ее оптимизировать; возможность получения катализаторов в виде гранул заданных формы, размеров и т.д.
Носитель не должен спекаться в условиях реакции. Спекание обычно начинается при температуре, которая составляет 0,5 от температуры плавления. Следовательно, носитель должен иметь очень высокую температуру плавления. У металлов заметная подвижность поверхностных частей появляется при температурах втрое меньших температуры плавления[2].
Промышленные катализаторы используют обычно в форме гранул или цилиндров диаметром ~10-3 м, которые должны иметь определенную механическую прочность, пористость и высокие значения удельной поверхности.
Переходные металлы (особенно VIII группы) способны катализировать много химических реакций гидрирования, дегидрирования, окисление важных промышленных процессов, например: окисление NH3 в NO на Pt в сплаве из Rh, Rd; гидрирование CO к CH4 (Ni на Cr2O3, Al2O3); получение водорода конверсией метана с водяным паром и кислородом (Ni на носителях)[1].
Широкое применение в реакциях гидрирования, дегидрирования, изомеризации находят катализаторы кислотно-щелочного типа. К твердым кислым катализаторам относят:
- Нелетучие минеральные кислоты (H3PO4, H3BO3) на инертных носителях — силикагель, уголь, кизельгур и тому подобное;
- Натуральные минералы (монтморилонит, каолинит, бентонит);
- Смешанные оксиды (Al2O3 - SiO2, Al2O3 - B2O3 и тому подобное);
- Соли сильных кислот (AlCl3, CuSO4, NiSO4, TiCl4 и др.).
К твердым щелочным катализаторам относят: неорганические щелочи и амиды (NaOH, KOH, KNH2 и тому подобное), нанесенные на инертные носители; неорганические соли и оксиды щелочного характера (BaO, CaO, MgO, K2CO3, CaCO3 и тому подобное).
К гетерогенным кислотно-щелочным катализаторам следует отнести ионообменные смолы (иониты). Иониты — это сшитые полимеры, которые имеют в своем составе функциональные ионогенные группы, которые могут генерировать катионы и анионы. Реакции, которые катализируются ионитами, аналогичны реакциям какие ускоряют растворимые кислоты и щелочи. К недостаткам большинства таких ионитов следует отнести их относительно низкую термическую стабильность, приблизительно 150-180 °С.
Особенное место среди гетерогенных катализаторов занимает цеолит, который широко используется в процессах крекинга углеводородов и гидрокрекинга и многих других кислотно-щелочных процессах. Естественный цеолит — алюмосиликати, которые содержат в своем составе оксиды щелочных и щелочноземельных металлов, которые отличаются сурово регулярной структурой пор. Общая химическая формула цеолита Me2/nO — Al2O3 — xSiO2 — yH2O, где Ме — катион металла; n — его валентность[7].
1.3 Выбор катализатора
Катализатор может использоваться в промышленном процессе, только если он отвечает определенным требованиям по отношению к активности, селективности и сроку службы.
Достоинства промышленного катализатора определяются прибылью, которую может дать его использование. Для оценки этого необходимо знать: производительность, которая ожидается, чтобы высчитать капиталовложение на оборудование; селективность, чтобы найти расходы сырья; тепловой эффект каталитической реакции, чтобы провести расчет энергозатрат или прибыли от тепла, которое выделяется; ожидаемый срок действия катализатора; стоимость[4].
Прежде чем выбрать катализатор, необходимо внимательно рассмотреть условия, при которых он будет работать в реакторе. Для этого путем термодинамического расчета сначала надо определить подходящие интервалы температуры, давления и состава сырья, которое подается к реактору. Необходимо также учесть конкурирующие побочные реакции и процессы распада продуктов. Принимаются в расчет также и экономические факторы, в том числе стоимость сырья и реактору, а также рациональное использование энергии. На выбор условий проведения процесса может влиять ценность побочных продуктов, которые образуются, или сложность их отделения. Когда условия осуществления реакции определены, приступают к подбору катализатора из веществ, которые стойкие при этих условиях. При определении стабильности работы катализатора задача усложняется тем, что в разных зонах реактора условия далеко не одинаковые. Хороший катализатор должен быть стойким во всех условиях[3].
При выборе подходящего катализатора необходимо учитывать нежелательные побочные реакции, которые он может ускорять. Важно выучить химические свойства продукта чтобы установить или будет он стойкий в условиях реакции при наличии данного катализатора.
При создании нового катализатора или модификации того, который имеется с целью повышения срока службы следует учитывать такие обстоятельства, как: простой при замене катализатора; размеры промышленного реактора; стоимость замены катализатора; потери, связанные со снижением производственной мощности и сложность приготовления высокоэффективного катализатора. Необходимо учитывать, что катализатор должен владеть химическим сродством хотя бы с одним из компонентов реакции. Исключаются химически инертные вещества и те из химически активных для данной системы, которые образуют крепкие соединения с реагентами. Пригодность того или иного вещества в качестве катализатора оценивается определенными термодинамическими соотношениями. Исследователи максимально активным образцом считают тот, у которого адсорбционный потенциал равняется полусумме энергий реагирующих связей[3].
1.4 Каталитические процессы в коксохимической промышленности
Производство, в котором одна или несколько основных химических реакций реализуется при участии катализаторов, называют каталитическим. Но по объему реакционного пространства, габаритами и сложностью аппаратов, количества обслуживающего персонала и общей стоимости эксплуатации собственно каталитические процессы и аппараты складывают в большинстве случаев незначительную часть такого производства.
Типичная технологическая схема каталитического производства ориентировочно может быть представлена следующей последовательностью операций и процессов:
- первичная переработка сырья с получением основных реагентов для каталитического процесса;
- очистки реакционной смеси от примесей, которые засоряют (пыль) или отравляют (яды) катализаторы;
- нагнетания газов или транспортировки жидких реагентов к реактору;
- подогрев реагентов до температуры катализа;
- катализ, который обычно сопровождается отведением или подведением тепла;
- переработка продуктов катализа в целевые продукты производства.
Содержимое этих операций различается в отдельных каталитических производствах[3].
В коксохимической промышленности каталитические процессы используют для очистки технологических газов или для получения товарных продуктов.
Каталитические методы очистки газов основаны на взаимодействии веществ, которые удаляются, с одним из компонентов газа, который очищается, или с веществом, которое специально добавляется к смеси на твердых катализаторах, в результате чего образуются новые вещества какие легко удаляются из газа методами абсорбции или адсорбции.
Для очистки газа от сероводорода используют хинонные методы очистки. К ним относят процесс Такахакс, процесс Фумакс-Родакс. Первый метод являет собой абсорбцию сероводорода щелочным раствором (карбоната натрия или аммиака), который содержит в качестве катализатора окисления натриевую соль 1,4-нафтохинон-2-сульфокислоты. Этот катализатор дает возможность удалять из газа 99,8-99,9 % сероводорода и получать серу высокой степени чистоты без примесей токсичных веществ и металлов. Второй метод включает промывку коксового газа аммиачным раствором, который содержит в качестве катализатоа пикриновую кислоту.
Также для очистки газа от соединений серы используют сухие окислительные процессы. Они основаны на поглощении соединений серы твердыми веществами и последующим окислением с получением элементарной серы или диоксида серы. При обычных температурах скорость этих реакций слишком маленькая, потому их проводят в присутствии катализаторов. Примером таких процессов является очистка на активированном угле и синтетическом цеолите[6].
Производство кокса сопровождается выделением токсичных составляющих коксового газа, в том числе — аммиака. Традиционный путь его утилизации с получением сульфата аммония исчерпал себя из-за насыщенность и переориентации рынка удобрений. В то же время ограничение на выбросы аммиака и введение европейских стандартов на его содержимое в коксовом газе (менее 0,03 г/м3) вынуждают искать новые пути переработки коксохимического аммиака без образования неликвидных продуктов.
Решением проблемы может стать очистка коксового газа по методу Carl Still, который включает улавливание аммиака водным раствором и каталитическое разложение аммиачного пара с получением азота и водорода, который потом возвращается в сырой коксовый газ. Этот способ был создан на основе работ фирмы Heinrich Koppers GmdH, которые были использованы еще в конце 1930х гг. (запатентованный в 1965 г.), а после того, как окончился срок действия патента, началось его промышленное использование[8].
Не менее распространенным компонентом в коксовом газе являются оксиды азота, которые также подлежат удалению из газа. Существует огромное количество каталитических методов очистки от оксидов азота.
Первый способ позволяет повысить степень очистки газов при повышении температуры и объемной скорости газового потока. Газ смешивается с аммиаком в соотношении 1:1 (NO: NH3=1:1) со следующим пропусканием газовой смеси через слой металофталоцианинового катализатору на носителе - оксиде алюминия[9].
Этот способ позволяет достичь степени очистки газа (99-100) % при температуре (20-150) °С. Также метод позволяет в этих же условиях повысить объемную скорость газового потока от 1,5*103 ч-1 до (2,6-5,2)*103 ч-1 при сохранении высокой степени очистки газа (99-100) %. Второй способ очистки заключается в возобновлении газов, которые отходят аммиаком при повышенной температуре на модифицированном алюмованадиевом катализаторе, который отличается тем, что с целью повышения степени очистки, используют катализатор, модифицированный трёхокисью железа в количестве (4-5) %масс.
Третий способ очистки газовой смеси от NO заключается в возобновлении NO до азоту оксидом углерода на катализаторе с содержимым оксидов алюминия, меди, хрома и переходного металла. Для снижения температуры процесса используют катализатор, который содержит в качестве оксида переходного металла оксид никеля при следующем соотношении ингредиентов в молярных долях[10]:
- оксид алюминия (0,645-0, 665)
- оксид никеля (0,134-1, 194)
- оксид хрома (0,032-0, 067)
- оксид меди (0,129-0, 134)
Четвертый способ используется для снижения содержимого горючих примесей и окчида углерода путем возобновления их горючими газами. Возобновление происходит на двухслойном катализаторе, первым слоем которого служит паладированый оксид алюминия, в качестве второго слоя используют природный материал — дунит. Недостатком способа является повышенное содержание оксида углерода в очищенном газе, которое равняется (0,1-0, 2) % и дороговизна процесса. Для его удешевления используются катализаторы которые не содержат благородных металлов. В этом случае используют двухслойные катализаторы, которые содержат Al2O3, при этом используют катализаторы, которые дополнительно содержат NiO, CaO, BaO и TiO2.
2 Использования каталитических методов в условиях ОАО «АКХЗ»
На Авдеевском КХЗ каталитические методы находят широкое применение. В случае правильного подбора катализатора можно получить желательный результат при минимальных экономических расходах. Катализаторы используются для получения фталевого ангидрида методом парофазного окисления нафталина. Процесс осуществляется на ванадий-калий-сульфатном катализаторе. Фталевый ангидрид используется в производстве алкидных, полиэфирных смол, синтетических лаков и красителей.
Реакция парофазного каталитического окисления нафталина кислородом воздуха во фталевый ангидрид, которая проходит с выделением тепла, сопровождается рядом побочных реакций на скорость которых влияют разные факторы практического ведения технологического процесса (чистота исходного вещества, температура реакции окисления, давление, скорость потока реакционной массы, качество катализатора и т.д.).
Вместе с основной реакцией (образование фталевого ангидрида) :
С10Н8 + 4,5О2 = С8Н4О3 + 2СО2 + 2Н2О
имеют место следующие реакции:
а) образование малеинового ангидрида:
С10Н8 + 9О2 = С4Н2О3 + 6СО2 + 3Н2О
б) образование 1,4-нафтохинона:
С10Н8 + 1,5О2 = С10Н6О2 + Н2О
в) полное сгорание нафталина:
С10Н8 + 12О2 = 10СО2 + 4Н2О
Кроме того, возможные реакции, которые не влияют на выход, но, в зависимости от степени загрязнения нафталина, могут влиять на чистоту готового продукта.
Процесс проходит при температуре 370-420 °С. Степень превращения нафталина при использовании данного метода составляет 84 %[11].
Также при абсорбционно-десорбционных методах очистки коксового газа от сероводорода получают сероводородные газы, которые содержат 40-90 %(об.) сероводорода, который не является товарным продуктом. На основе этих газов возможно получить сульфиды аммония, натрия, бария и других продуктов, но большая часть их перерабатывается в серную кислоту.
Получение серной кислоты осуществляется по методу мокрого катализа. Метод заключается в окиснлении сероводорода в SO2 и воды путем сжигания в печах при температуре 1100-1300 °С со следующим окислением SO2 в SO3 на катализаторе при 450-600 °С и конденсацией серной кислоты при охлажденные контактных газов до 60-80 °С. Процесс происходит на ванадиевом катализаторе СВД(К-Д, К)[12].
3 Термокаталитическая очистка выбросов при грануляции электродного пека
Особенное место как источник загрязнения окружающей среды занимает пекококсове производство в том числе и установка для грануляции и расфасовки электродного пека.
Пилегазовые выбросы при производстве гранулированного пека очень токсичны. При получении гранулированного пека в атмосферу выделяется большое количество аэрозолей и паров полициклических ароматических углеводородов (ПАУ), фенола нафталина, коксовой пыли и других загрязняющих веществ. Для очистки выбросов, которые образуются в данном производстве возможно использования термокаталитического очистки на палладиевом катализаторе.
Смешан с оксидами жидких металлов алюмоникель-паладиевый катализатор предназначенный для очистки отходящих газов производств: пластмасс, нефтехимических, коксохимических, асфальто-бетона, линий покраски, автомобильного, железнодорожного транспорта и мусоросжигательных заводов путем окисления паров органических веществ, оксида углерода, водорода и восстановление оксида азота. Катализатор используется в реакторах с полочными кассетами и радиального типа с рекуперацией тепла и регенерацией.
Таблица 1 — Степень очистки от некоторых веществ при 300-600 °С
Вещества от которых проводится очищение |
Диапазон концентраций, мг/м3 |
Степень очищения, % |
Фенол, формальдегид, этанол, уайтспирит, толуол, метилэтилкетон, циклогексанол, нафталин |
0,5-5000 |
97 |
Полициклические углеводороды |
0,5-5000 |
95-97 |
Бенз(а)пирен |
0,001-0,5 |
97-99 |
Оксид азота |
1,0-5000 |
70 |
Фуран, диоксины |
0,1-0,5 |
99 |
Аммиак |
10,0-5000 |
95 |
Цианистый водород |
0,1-1000 |
95 |
Сернистый ангидрид, сероводород |
0,1-1000 |
90 |
Оксид углерода |
0,1-3000 |
98 |
Сажа, пиль кокса |
0,5-1000 |
90 |
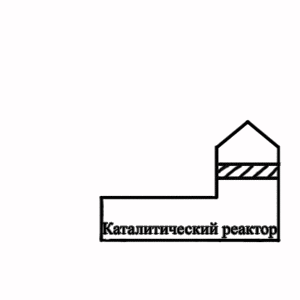
Рисунок 2 — Технологическая схема термокаталитического обезвреживания отхохящих газов от участка грануляции электродного пека
Анимация: кадров — 7, циклов повторений — 7, размер — 30,5 кБ
Литература
- Байрамов В.М. Основы химической кинетики и катализа: Учеб. пособие для студ. высш. учеб. заведений/В.М. Байрамов. — М.: Издательский центр «Академия», 2003. — 256с.
- Дж. Андерсон Структура металлических катализаторов/ Перевод с английкого к.х.н. Э.Э. Рачковского, под ред. академика Г.К. Борескова. — М.: «Мир», 1978. — 485с.
- Технология катализаторов/ И.П.Мухленов, Е.И.Добкина, В.И.Дерюжкина, В.Е.Сороко; под ред. проф. И.П.Мухленова. 3-е изд., перераб. — Л.: Химия, 1989 — 272с.
- Катализ в промышленности: в 2х т. Т.1. Пер. с англ./ Под ред. Б. Лига. — М.: Мир, 1986. — 324с.
- Катализ в промышленности: в 2х т. Т.2. Пер. с англ./ Под ред. Б. Лига. — М.: Мир, 1986. — 291с.
- Улавливание химических продуктов коксования: учебное пособие для вузов: в 2ч./ А.Ф. Гребенюк, В.И. Коробчанский, Г.А. Власов, С.И. Кауфман. — Донецк: Восточный изд. дом, 2002.
- Попова Н.М. Катализаторы очистки газовых выбросов промышленных производств. — М.:Химия, 1991. — 176с.
- Платонов О.И. Промышленный опыт и перспективы развития технологии каталитического разложения коксохимического аммиака // Журнал «Кокс и химия», 2008. — Вып. 1. — сс.22-27.
- Платонов О.И. Особенности промышленной технологии каталитического разложения коксохимического аммиака/Платонов О.И., Егоров В.Н., Лутохин Н.Н., Мельников И.И., Чистяков Н.П., Егоров М.А., Криницын Е.Н., Щукина Р.И.// Журнал «Кокс и химия», 2005. — Вып. 5. — сс.37-41.
- А.с. 1324681 СССР, кл. В 01 37/02. Способ очистки отходящих газов от оксида азота/ В.Е. Майзлиш, А.В. Величко, Ф.П. Снегирева, Н.Л. Мочалова, Г.П. Шапошников, Р.П. Смирнов, В.Л. Ивасенко. — №4464169/31-26; Заявлено 20.07.88. Опубл. 07.12.90. Бюл. №45. — 3с.
- Гуревич Д.А. Фталевый ангидрид. — М.: Химия, 1968 — 232с.
- Амелин А.Г., Яшке Е.В. Производство серной кислоты: Учебник для проф.-техн. учеб. заведений. — 2-е изд., перераб. и доп. — М.: Высш. школа, 1980 — 245с.
|