Реферат на тему випускної роботи
Вступ
Паливно-енергетичний комплекс є основою розвитку економіки будь-якої держави. В даний час для отримання енергії в більшості випадків використовується органічне паливо (вугілля, нафта, природний газ і ін.). Особливу роль виконує коксохімічне виробництво, що виробляє продукцію, штучно одержувану з вугільної сировини - бензол, кам'яновугільну смолу, її хімічні продукти, пек, пековий кокс і ін.
Коксохімічні заводи є достатньо крупними підприємствами, на яких здійснюється термохимічна переробка сировини з метою отримання різних видів коксу. Процес коксування супроводжується утворенням речовин, які надалі можуть використовуватися в якості сировини для отримання товарних продуктів. Авдіївский коксохімічний завод є одним з багатьох великих виробників в отраслі.
Існує безліч способів переробки сировини та знешкодження газових викидів. Вибір методу залежить від багатьох показників: хімічного складу сировини або газу, що очищується, наявність механічних домішок, бажана ступінь очищення газу або ступінь перетворення сировини в продукт і т.п.
Мета
Метою даної роботи є дослідження ефективності використання каталітичних методів в коксохімічній промисловості.
Задачі
Для того, щоб досягнути мети були поставлені наступні задачі:
- Розглянути механізм каталізу і каталітичних реакцій за участю різних речовин;
- Розглянути існуючі каталітичні процеси в умовах ВАТ «АКХЗ»;
- Визначити недолікі розглянутих процесів та запропонувати шляхи їх усунення;
- Визначити можливість застосування каталітичних методів для очищення викидів при грануляції електродного пеку.
Актуальність
Актуальною проблемою на сьогоднішній день є вдосконалення установки мокрого каталізу. Ефективними методам підвищення ступеню конверсії SO2 в SO3 є подвійний каталіз та окиснення SO2 під тиском.
Відходящі гази від ділянки грануляції та розфасовки електродного пеку на ВАТ «АКХЗ» на даний момент відводяться в атмосферу без належного очищення, тому є необхідним будівництво установки термокаталітичного знешкодження газових викидів.
1 АНАЛІТИЧНИЙ ОГЛЯД КАТАЛІТИЧНИХ МЕТОДІВ[витримки]
1.1 Поняття каталізу
Каталіз має велике значення в природі і сучасному житті: каталітичними є майже всі біохімічні процеси, більшість реакцій, які вивчають в лабораторії, і технологічних процесів, які реалізовані в промисловості.
Першим випадком використання каталізаторів вважається утворення етилового ефіру зі спирту за допомогою сірчаної кислоти, відкрите у VIII сторіччі нашої ери. Перше велике промислове використання каталізу здійснено у 1746 році в нітрозному (камерному) способі виробництва сірчаної кислоти.
Причина каталітичної дії різних речовин полягає в зміні механізму реакції в присутності каталізатору, тобто виникненні нового або кількох шляхів реакції, які швидко протікають. Механізм реакції — це сукупність елементарних хімічних стадій, які мають місце в реакційній системі при переході від вихідних речовин до продуктів.
Класифікацію каталітичних процесів можна провести за декількома відмінностями. За фазовим складом компонентів каталітичні реакції зазвичай відносять до гомогенного каталізу (якщо вихідні речовини, продукти реакції і каталізатори знаходяться в єдиній фазі) або до гетерогенного каталізу (реакційна суміш і каталізатор знаходяться в різних фазах).
В гомогенному каталізі навіть дуже маленьких кількостей каталізатору (від 10-13 моль) достатньо для прискорення перетворення великої кількості реагентів в продукти, тому що каталізатор може використовуватися багаторазово. Експериментально встановлено, що швидкість гомогенної хімічної реакції прямо пропорційна концентрації каталізатору. Цей факт підтверджує, що каталізатор дійсно приймає участь в реакції, при цьому він утворює нестійкі проміжні з’єднання, та визначає протікання реакції за іншим, ніж при його відсутності, шляхом.
Каталітичну дію при гетерогенному каталізі пов’язують з наявністю на поверхні твердих тіл активних центрів, природа і число яких часто невідомо[1].
В якості каталізаторів зазвичай використовують тверді речовини і вивчають в основному системи «газ-тверде тіло» і «рідина-тверде тіло». Рідше використовують рідкі каталізатори, які являють собою кислоти (наприклад, H2SO4 або H3PO4), іноді розчини активних речовин в воді або органічні розчинники.
Важливе місце в теорії і практиці гетерогенного каталізу займає «правило Борескова» про приблизну постійність питомої каталітичної активності речовин. Дослідження показали, що питома каталітична активність (для ряду однокомпонентних оксидних і металевих каталізаторів) не залежить від дисперсності активного компоненту і способу приготування при незмінному складі каталізатору.
Правило Борескова, яке виконується, як правило, для стадійного механізму при підвищених температурах, базується на уявленнях про каталізатор і реагуючі речовини як єдиної каталітичної системи, в якій хімічні перетворення перетерплюють не тільки реагенти під впливом каталізатору, але й каталізатор змінює свій склад і властивості в результаті взаємодії з реактивами. В результаті під впливом реакційної суміші встановлюється стаціонарний склад, який визначає питому каталітичну активність, яка не залежить від вихідного стану поверхні каталізатору, тобто від умов його приготування і попередньої обробки[3].
Дослідження гетерогенного каталізу показали, що каталітична реакція протікає на поверхні каталізатору, тому для пояснення сутності питання необхідно передусім розуміння процесу адсорбції. Адсорбція — це процес самовільного змінення концентрації речовини на межі розподілу фаз, який супроводжується зменшенням енергії Гібса. В гетерогенному каталізі адсорбентом є каталізатор, адсорбатом – молекула реагуючої речовини. Розрізняють фізичну адсорбцію і хемосорбцію, хоча між ними немає чіткої межі. З двох процесів адсорбції тільки хемосорбція призводить до помітної зміни енергетичного стану адсорбованої молекули і суттєвому збільшенню її реакційної здатності за рахунок зниження енергії активації, що і пояснює каталітичний ефект. Однак фізична адсорбція може передувати хемосорбції і є стадією каталітичного процесу[1].
Гетерогенно-каталітична реакція являє собою складний процес, який складається з наступних стадій (рис. 1):
- дифузія вихідних речовин з об’єму газової або рідкої фази до зовнішньої та внутрішньої поверхням каталізатору;
- адсорбція реагуючих речовин на поверхні каталізатору;
- хімічна реакція на поверхні каталізатору;
- десорбція продуктів реакції;
- дифузія продуктів реакції від внутрішньої та зовнішньої поверхонь каталізатору в об’єм.
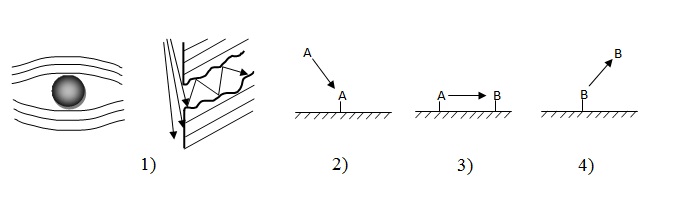
Рисунок 1 — Спрощена схема каталітичного процесу на поверхні твердого каталізатору
Загальна швидкість такого складного процесу визначається швидкістю найбільш повільної стадії, яка часто має назву стадії, яка лімітує.
На зовнішню дифузію впливають розмір та форма часток каталізатору, співвідношення між об’ємом і діаметром реактору і об’ємна швидкість. Від них залежить утворення каналів, по яких протікають реагенти, режими цих потоків, ступінь зворотнього перемішування і часу контактування. Внутрішня дифузія залежить від пористої структури каталізатору. За розміром пори умовно поділяються на три категорії: мікропори діаметром < 15 A, мезопори діаметром від 15 до 150 A і макропори діаметром > 150 A. Діаметр пор обумовлює внутрішню дифузію. Основну частину загальної поверхні багатьох каталізаторів складає внутрішня поверхня, тому саме на ній відбувається більша частина взаємодій і сутичок молекул реагентів[5].
Про подібність механізмів гетерогенного і гомогенного каталізу можна судити по тому, що стадія хемосорбції в першому аналогічна стадії утворення проміжного з’єднання в другому. Відмінність їх полягає в тому, що на поверхні гетерогенного каталізатору, завдяки наявності декількох типів активних центрів, можуть утворитися різні типи активованих комплексів, які призводять до появи різних продуктів реакції.
1.2 Каталізатори в промислових процесах
В промисловості каталізатори являють собою, як правило, багатокомпонентні системи.
Додання до каталізаторів в невеликих кількостях речовин, які називаються промоторами, підвищує його активність за рахунок збільшення поверхні, вибірковості і строку дії.
Промотором (активатором) називають добавку до каталізатору невеликої кількості речовини, яке само по собі може бути каталітично неактивними по відношенню до визначеної реакції, але дуже підвищує активність власне каталізатору. Ефективність дії промоторів залежить від їх кількості. При визначеному співвідношенні активного компоненту і промотору спостерігається максимум активності.
За класифікацією, даною Ч. Сеттерфілдом, промотори поділяють на два основних класи: текстурні, які роблять фізичну дію, і структурні, природа впливу яких хімічна.
Текстурні промотори присутні в каталізаторі, як правило, у вигляді дрібних часточок і мають гальмуючу дію на спікання активної фази. Структурні (хімічні) промотори змінюють хімічний склад каталізатору.
Каталізатори на носіях є широко розповсюдженим типом складних контактних мас. При підборі носіїв слід мати на увазі їх визначені характеристики: необхідні механічні властивості, в тому числі міцність на розчавлювання і стирання, твердість; стабільність в умовах реакції і регенерації (в тому числі термостійкість і корозійна стійкість); пористість, яка визначається середнім розміром пор і розподілом об’єму пор за радіусами.
На даний момент широко використовуються синтетичні носії, які мають порівняно з природними матеріалами ряд переваг. До таких можна віднести: постійність хімічного складу; можливість регулювання пористої структури , що дозволяє її оптимізувати; можливість отримання каталізаторів у вигляді гранул заданих форми, розмірів та інш.
Носій не має спікатися в умовах реакції. Спікання зазвичай починається при температурі, яка складає 0,5 від температури плавлення. Отже, носій повинен мати дуже високу температуру плавлення. У металів помітна рухливість поверхневих часток з’являється при температурах, втричі менших температури плавлення[2].
Промислові каталізатори використовують зазвичай в формі гранул або циліндрів діаметром ~10-3 м, які повинні мати певну механічну міцність, поруватість і високі значення питомої поверхні.
Перехідні метали (особливо VIII групи) здатні каталізувати багато хімічних реакцій гідрування, дегідрування, окиснення важливих промислових процесів, наприклад: окиснення NH3 до NO на Pt в сплаві з Rh, Rd; гідрування CO до CH4 (Ni на Cr2O3, Al2O3); отримання водню конверсією метану з водяним паром і киснем (Ni на носіях)[1].
Широке застосування в реакціях гідрування, дегідрування, ізомеризації знаходять каталізатори кислотно-лужного типу. До твердих кислих каталізаторів відносять:
- нелеткі мінеральні кислоти (H3PO4, H3BO3) на інертних носіях — силікагель, вугілля, кізельгур і т.п.;
- натуральні мінерали (монтморилоніт, каолініт, бентоніт);
- змішані оксиди (Al2O3 — SiO2, Al2O3 — B2O3 і т.п.);
- солі сильних кислот (AlCl3, CuSO4, NiSO4, TiCl4 та ін.).
До твердих лужних каталізаторів відносять: неорганічні луги і аміди (NaOH, KOH, KNH2 і т.п.), нанесені на інертні носії; неорганічні солі та окиси лужного характеру (BaO, CaO, MgO, K2CO3, CaCO3 і т.п.).
До гетерогенних кислотно-лужних каталізаторів слід віднести іонообмінні смоли (іоніти). Іоніти — це зшиті полімери, які мають в своєму складі функціональні іоногенні групи, які можуть генерувати катіони і аніони. Реакції, які каталізуються іонітами, аналогічні реакціям, які прискорюють розчинні кислоти та луги. До недоліків більшості таких іонітів слід віднести їх відносно низьку термічну стабільність, приблизно 150-180 оС.
Особливе місце серед гетерогенних каталізаторів займають цеоліти, які широко використовуються в процесах крекінгу вуглеводнів і гідрокрекінгу і багатьох інших кислотно-лужних процесах. Природні цеоліти – алюмосилікати (~40), які містять в своєму складі оксиди лужних і лужноземельних металів, які відрізняються суворо регулярною структурою пор. Загальна хімічна формула цеолітів Me2/nO - Al2O3 - xSiO2 - yH2O, де Ме – катіон металу; n – його валентність[7].
1.3 Вибір каталізатору
Каталізатор може використовуватися в промисловому процесі, тільки якщо він відповідає визначеним вимогам по відношенню до активності, селективності і строку служби.
Достоїнства промислового каталізатору визначаються прибутком, який може дати його використання. Для оцінки цього необхідно знати: продуктивність, яка очікується, щоб вирахувати капіталовкладення на устаткування; селективність, щоб знайти витрати сировини; тепловий ефект каталітичної реакції, щоб провести розрахунок енергозатрат або прибутку від тепла, що виділяється; строк дії каталізатору, який очікується; вартість[4].
Перш ніж вибрати каталізатор, необхідно уважно розглянути умови, за яких він буде працювати в реакторі. Для цього шляхом термодинамічного розрахунку спочатку треба визначити підходящі інтервали температури, тиску і складу сировини, яка подається до реактору. Необхідно також урахувати конкуруючі побічні реакції і процеси розпаду продуктів. Приймаються в розрахунок також і економічні фактори, в тому числі вартість сировини і реактору, а також раціональне використання енергії. На вибір умов проведення процесу може впливати цінність побічних продуктів, які утворюються, або складність їх відділення. Коли умови здійснення реакції визначені, приступають до підбору каталізатору з речовин, які стійкі при цих умовах. При визначенні стабільності роботи каталізатору задача ускладнюється тим, що в різних зонах реактору умови далеко не однакові. Добрий каталізатор має бути стійким у всіх умовах[3].
При виборі підходящого каталізатору необхідно враховувати небажані побічні реакції, які він може прискорювати. Важливо вивчити хімічні властивості продукту, щоб встановити чи буде він стійкий в умовах реакції при наявності даного каталізатору.
При створенні нового каталізатору чи модифікації того, що мається з метою підвищення строку служби слід враховувати такі обставини: простій при заміні каталізатору; розміри промислового реактору; вартість заміни каталізатору; втрати, пов’язані зі зниженням виробничої потужності і складність приготування високоефективного каталізатору.
Необхідно враховувати, що каталізатор має володіти хімічною спорідненістю хоча б з одним з компонентів реакції. Виключаються хімічно інертні речовини і ті з хімічно активних для даної системи, які утворюють міцні з’єднання з реагентами. Придатність тієї чи іншої речовини в якості каталізатору оцінюється визначеними термодинамічними співвідношеннями. Дослідники максимально активним зразком вважають той, в якого адсорбційний потенціал дорівнює напівсумі енергій реагуючих зв’язків[3].
1.4 Каталітичні процеси в коксохімічній промисловості
Виробництва, в яких одна або декілька основних хімічних реакцій реалізується за участю каталізаторів, називають каталітичними. Але за об’ємом реакційного простору, габаритами і складністю апаратів, кількості обслуговуючого персоналу і загальній вартості експлуатації власне каталітичні процеси і апарати складають у більшості випадків незначну частину такого виробництва.
Типова технологічна схема каталітичного виробництва орієнтовно може бути представлена наступною послідовністю операцій та процесів:
- первинна переробка сировини з отриманням основних реагентів для каталітичного процесу;
- очищення реакційної суміші від домішок, які засмічують (пил) або отруюють (отрути) каталізатори;
- нагнітання газів або транспортування рідких реагентів до реактору;
- підігрів реагентів до температури каталізу;
- каталіз, який зазвичай супроводжується відведенням або підведенням тепла;
- переробка продуктів каталізу в цільові продукти виробництва.
Вміст цих операцій розрізняється в окремих каталітичних виробництвах[3].
В коксохімічній промисловості каталітичні процеси використовують для очищення технологічних газів або для отримання товарних продуктів.
Каталітичні методи очищення газів засновані на взаємодії речовин, які видаляються, з одним з компонентів газу, що очищується, або з речовиною, яка спеціально додається до суміші на твердих каталізаторах, в результаті чого утворюються нові речовини, які легко видаляються з газу методами абсорбції або адсорбції.
відносять процес Такахакс, процес Фумакс-Родакс. Перший метод являє собою абсорбцію сірководню лужним розчином (карбонату натрію або аміаку), який містить в якості каталізатору окиснення натрієву соль 1,4-нафтохінон-2-сульфокислоти. Цей каталізатор дає можливість видаляти з газу 99,8-99,9 % сірководню і отримувати сірку високого ступеню чистоти без домішок токсичних речовин і металів. Другий метод включає промивку коксового газу аміачним розчином, який містить в якості каталізатору пікринову кислоту.
Також для очищення газу від сірчаних з’єднань використовують сухі окисні процеси. Вони засновані на поглинанні сірчаних з’єднань твердими речовинами і наступним окисненням з отриманням елементарної сірки або диоксиду сірки. При звичайних температурах швидкість цих реакцій надто маленька, тому їх проводять в присутності каталізаторів. Прикладом таких процесів є очищення на активованому вугіллі та синтетичних цеолітах[6].
Виробництво коксу супроводжується виділенням токсичних складових коксового газу, в тому числі – аміака. Традиційний шлях його утилізації з отриманням сульфату амонію вичерпав себе через насиченість і переорієнтація ринку добрив. В той же час обмеження на викиди аміаку і введення європейських стандартів на його вміст в коксовому газі (менше 0,03 г/м3) змушують шукати нові шляхи переробки коксохімічного аміаку без утворення неліквідних продуктів.
Рішенням проблеми може стати очищення коксового газу по методу Carl Still, який включає уловлювання аміаку водним розчином і каталітичне розкладення аміачної пари з отриманням азоту та водню, який потім повертається в сирий коксовий газ. Цей спосіб був створений на основі робіт фірми Heinrich Koppers GmdH, які були використані ще наприкінці 1930х рр. (запатентований у 1965 р.), а після того, як скінчився строк дії патенту, почалося його промислове використання[8].
Не менш розповсюдженим компонентом у коксовому газі є окиси азоту, які також підлягають видаленню з газу. Існує безліч каталітичних методів очищення від окисів азоту.
Перший спосіб дозволяє підвищити ступінь очищення газів при підвищенні температури і об’ємної швидкості газового потоку. Газ змішується аміаком у відношенні 1:1 (NO:NH3=1:1) з наступним пропусканням газової суміші через шар металофталоцианінового каталізатору на носії – окисі алюмінію[9].
Цей спосіб дозволяє досягти ступеню очищення газу (99-100) % при температурі (20-150) °С. Також метод дозволяє в цих же умовах підвищити об’ємну швидкість газового потоку від 1,5•103ч-1 до (2,6-5,2)*103 ч-1 при збереженні високого ступеню очищення газу (99-100) %.
Другий спосіб очищення полягає у відновленні газів, що відходять аміаком при підвищеній температурі на модифікованому алюмованадієвому каталізаторі, який відрізняється тим, що з метою підвищення ступеню очищення, використовують каталізатор, модифікований триокисом заліза в кількості (4-5) %мас.
Третій спосіб очищення газової суміші від NO полягає у відновленні NO до азоту моноокисом вуглецю на каталізаторі з вмістом окисів алюмінію, міді, хрому і перехідного металу. Для зниження температури процесу використовують каталізатор, який містить в якості окису перехідного металу окис нікелю при наступному співвідношенні інгредієнтів в молярних долях[10]:
- оксид алюмінію (0,645-0,665)
- оксид нікелю (0,134-1,194)
- оксид хрому (0,032-0,067)
- оксид міді (0,129-0,134)
Четвертий спосіб використовується для зниження вмісту горючих домішок і моноокису вуглецю шляхом відновлення їх горючими газами. Відновлення відбувається на двошаровому каталізаторі, першим шаром якого служить паладований окис алюмінію, в якості другого шару використовують природний матеріал – дуніт. Недоліком способу є підвищений вміст моноокису вуглецю в очищеному газі, яке дорівнює (0,1-0,2) % та дорожнеча процесу. Для його вдешевшення використовуються каталізатори, які не містять благородних металів. В цьому випадку використовують двошарові каталізатори, які містять Al2O3, при цьому використовують каталізатори, які додатково містять NiO, CaO, BaO і TiO2.
2 Використання каталітичних методів в умовах ВАТ «АКХЗ»
На Авдіївському КХЗ каталітичні методи знаходять широке використання. В разі правильного підбору каталізатору можна отримати бажаний результат при мінімальних економічних витратах.
Каталізатори використовуються для отримання фталевого ангідриду методом парофазного окиснення нафталіну. Процес здійснюється на ванадій-калій-сульфатному каталізаторі. Фталевий ангідрид використовується у виробництві алкідних, поліефірних смол, синтетичних лаків і барвників.
Реакція парофазного каталітичного окиснення нафталіну киснем повітря у фталевий ангідрид, яка проходить з виділенням тепла, супроводжується низкою побічних реакцій, на швидкість яких впливають різні фактори практичного ведення технологічного процесу (чистота вихідної речовини, температура реакції окиснення, тиск, швидкість потоку реакційної маси, якість каталізатору та інш.).
Разом з основною реакцією (утворення фталевого ангідриду):
С10Н8 + 4,5О2 = С8Н4О3 + 2СО2 + 2Н2О
мають місце наступні побічні реакції:
а) утворення малеїнового ангідриду:
С10Н8 + 9О2 = С4Н2О3 + 6СО2 + 3Н2О
б) утворення 1,4-нафтохінона:
С10Н8 + 1,5О2 = С10Н6О2 + Н2О
в) повне згорання нафталіну:
С10Н8 + 12О2 = 10СО2 + 4Н2О
Крім того, можливі реакції, які не впливають на вихід, але, в залежності від ступеню забруднення нафталіну, можуть впливати на чистоту готового продукту.
Процес проходить при температурі 370-420 °С. Ступінь перетворення нафталіну при використанні даного методу складає 84 %[11].
Також при абсорбційно-десорбційних методах очищення коксового газу від сірководню отримують сірководневі гази, які містять 40-90 %(об.) сірководню, який не являє собою товарний продукт. На основі цих газів можливо отримати сульфіди амонію, натрію, барію та інші продукти, але більша частина їх перероблюється в сірчану кислоту.
Отримання сірчаної кислоти здійснюється за методом мокрого каталізу. Метод полягає в окиснені сірководню до двоокису сірки і води шляхом спалювання в печах при температурі 1100-1300 °С з наступним окисненням SO2 в SO3 на каталізаторі при 450-600 °С і конденсацією сірчаної кислоти при охолоджені контактних газів до 60-80 °С. Процес відбувається на ванадієвому каталізаторі СВД(К-Д,К)[12].
3 Термокаталітичне очищення викидів при грануляції електродного пеку
Особливе місце як джерело забруднення навколишнього середовища займає пекококсове виробництво, в тому числі і установка для грануляції і розфасовки електродного пеку. Пилогазові викиди при виробництві гранульованого пеку дуже токсичні. При отриманні гранульованого пеку в атмосферу виділяється велика кількість аерозолів і пари поліциклічних ароматичних вуглеводнів (ПАВ), фенолу нафталіну, коксового пилу та інших забруднюючих речовин.
Для очищення викидів, які утворюються при даному виробництві можливо використання термокаталітичного очищення на паладієвому каталізаторі. Змішаний з окисами рідких металів алюмонікель-паладієвий каталізатор призначений для очищення відходящих газів виробництв: пластмас, нафтохімічних, коксохімічних, асфальто-бетона, лінії забарвлення, автомобільного, залізодорожного транспорту та сміттєспалювальних заводів шляхом окиснення пари органічних речовин, окису вуглецю, водню і відновлення окису азоту. Каталізатор використовується в реакторах з поличними касетами і радіального типу з рекуперацією тепла і регенерацією.
Таблиця 1 — Ступінь очищення від деяких речовин при 300-600 °С
Речовини від яких проводиться очищення |
Діапазон концентрацій, мг/м3 |
Ступінь очищення, % |
Фенол, формальдегід, етанол, уайтспірит, толуол, метилетилкетон, циклогексанол, нафталін |
0,5-5000 |
97 |
Поліциклічні вуглеводні |
0,5-5000 |
95-97 |
Бенз(а)пірен |
0,001-0,5 |
97-99 |
Оксид азоту |
1,0-5000 |
70 |
Фуран, діоксини |
0,1-0,5 |
99 |
Аміак |
10,0-5000 |
95 |
Цианістий водень |
0,1-1000 |
95 |
Сірчаний ангідрид, сірководень |
0,1-1000 |
90 |
Оксиди вуглецю |
0,1-3000 |
98 |
Сажа, пил коксу |
0,5-1000 |
90 |
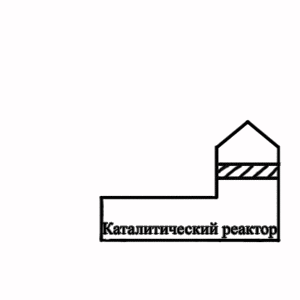
Рисунок 2 — Технологічна схема термокаталітичного знешкодження відходящих газів від ділянки грануляції електордного пеку
Анімація кадрів — 7; циклів повтору — 7; розмір — 30,5 кБ
Література
- Байрамов В.М. Основы химической кинетики и катализа: Учеб. пособие для студ. высш. учеб. заведений/В.М. Байрамов. — М.: Издательский центр «Академия», 2003. — 256с.
- Дж. Андерсон Структура металлических катализаторов/ Перевод с английкого к.х.н. Э.Э. Рачковского, под ред. академика Г.К. Борескова. —М.: «Мир», 1978. — 485с.
- Технология катализаторов/ И.П.Мухленов, Е.И.Добкина, В.И.Дерюжкина, В.Е.Сороко; под ред. проф. И.П.Мухленова. 3-е изд., перераб. — Л.: Химия, 1989 — 272с.
- Катализ в промышленности: в 2х т. Т.1. Пер. с англ./ Под ред. Б. Лига. — М.: Мир, 1986. —324с.
- Катализ в промышленности: в 2х т. Т.2. Пер. с англ./ Под ред. Б. Лига. — М.: Мир, 1986. — 291с.
- Улавливание химических продуктов коксования: учебное пособие для вузов: в 2ч./ А.Ф. Гребенюк, В.И. Коробчанский, Г.А. Власов, С.И. Кауфман. — Донецк: Восточный изд. дом, 2002.
- Попова Н.М. Катализаторы очистки газовых выбросов промышленных производств. — М.:Химия, 1991. — 176с.
- Платонов О.И. Промышленный опыт и перспективы развития технологии каталитического разложения коксохимического аммиака // Журнал «Кокс и химия», 2008. — Вып. 1. — С.22-27.
- Платонов О.И., Егоров В.Н., Лутохин Н.Н., Мельников И.И., Чистяков Н.П., Егоров М.А., Криницын Е.Н., Щукина Р.И. Особенности промышленной технологии каталитического разложения коксохимического аммиака // Журнал «Кокс и химия», 2005. — Вып. 5.—С.37-41.
- А.с. 1324681 СССР, кл. В 01 37/02. Способ очистки отходящих газов от оксида азота/ В.Е. Майзлиш, А.В. Величко, Ф.П. Снегирева, Н.Л. Мочалова, Г.П. Шапошников, Р.П. Смирнов, В.Л. Ивасенко. — №4464169/31-26; Заявлено 20.07.88. Опубл. 07.12.90. Бюл. №45. — 3с.
- Гуревич Д.А. Фталевый ангидрид. — М.: Химия, 1968 —232с.
- Амелин А.Г., Яшке Е.В. Производство серной кислоты: Учебник для проф.-техн. учеб. заведений. — 2-е изд., перераб. и доп. — М.: Высш. школа, 1980 — 245с.
|