Особенности
определения технического состояния подшипников качения коренного
вала подъемных машин.
В.А.Яценко В. А. Пристром В.Ф. Рубан
Источник: Проблеми експлуатації обладнання шахтних стаціонарних установок. Збірник наукових праць. - Донецьк: ВАТ "НДІГМ ім. М.М.Федорова, 2007 р. - С. 84-90
1. Постановка проблемы в общем виде и ее
связь с важными практическими задачами.
В
настоящее время подшипники качения и скольжения применяются в шахтных
подъёмных машинах (коренная часть органа навивки, редуктор,
двигатель). Техническая диагностика каждого вида подшипников имеет
свои особенности. Существующие методы предупреждения отказа
подшипниковых узлов основаны на вероятностном прогнозе и связаны с
системой планово предупредительных ремонтов. Требующих разборки и
сборки опор подшипников. Как правило, такой контроль лишь
констатирует факты уже значительных повреждений. Имеет место либо
недоиспользование ресурса подшипника, либо его отказ.
2.Постановка задачи.
Целью данной работы является разработка методов
безразборного контроля подшипников качения шахтных подъемных
установок с использованием в качестве источника информации
вибросигнала.
3. Изложение основного материала исследования с полным обоснованием полученных научных результатов.
Среди существующих методов диагностики, наиболее эффективной является вибродиагностика.
В общем случае, состояние подшипника качения от идеального до полного
разрушения можно разделить на пять стадий. На рис.1. по вертикальной
оси отложены значения амплитуды виброскорости ( мм/с), по
горизонтальной – стадии развития дефектов. Ломаная линия «1»
соответствует уровню фона вибрации, линия «2» –уровню
пиков вибрации. От отметки «0» до «1»считаем,
что общее состояние подшипника «идеальное». На этом
нулевом этапе уровень фона ( линия 1) и уровень пика ( линия 2)
отличаются незначительно друг от друга, а сам фон вибрации значительно меньше
нормируемого.
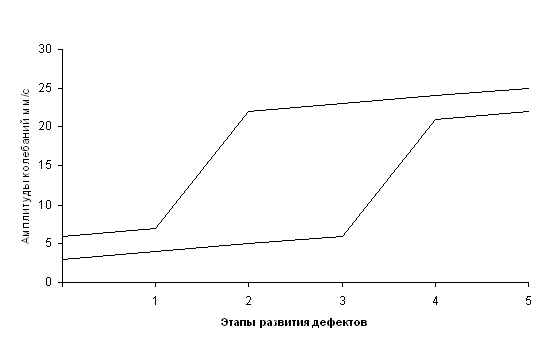
Рис.1. Этапы развития дефектов подшипников качения
Стадия 1. Это стадия возникновения дефекта в процессе
эксплуатации. Начиная с отметки "1" в подшипнике появляется
и начинает развиваться какой-либо дефект, возникают ударные
виброимпульсы, растущие по величине. Энергия импульсов затрачивается
на «углубление» дефекта, в результате чего происходит ещё
большее увеличение энергии импульсов. Уровень фона вибрации по своей
величине при этом остаётся неизменным, т.к. дефект носит локальный
характер и на общем состоянии подшипника пока не сказывается.
Стадия 2. Начиная с точки «2» на рис. 2.2. ударные
импульсы в подшипнике достигают по своей энергии практически
максимального значения. Количественное значение максимума энергии
импульсов определяется типом подшипника и условиями его эксплуатации.
Выделяющаяся в подшипнике энергия импульсов уже столь велика, что её
достаточно для расширения зоны дефекта. На данной стадии остановить
дальнейшее развитие дефекта не возможно, началось его саморазвитие.
Величина пиков вибрации на временном вибросигнале уже практически не
растёт, но и уровень фона тоже меняется мало. Дефект «набирает
силу, готовится к решающему нападению».
Стадия 3. Начинается с точки «3». Зона развития
дефекта столь велика, что подшипник начинает «терять»
своё основное назначение – обеспечивать вращение валов с
минимальным трением. Возрастают затраты энергии на вращение ротора и,
как результат, увеличивается энергия, выделяющаяся в подшипнике,
растёт уровень фона. Это уже стадия саморазрушения подшипника.
Стадия 4. Начинается с точки «4» и является
последней в развитии дефекта, охватившего весь подшипник, вернее всё
то, что от него осталось. Уровень фона вибрации практически сравнялся
с уровнем пиков, иначе говоря вся вибрация состоит из пиков. Работа
подшипников в этой зоне недопустима.
Стадия 5. Это ожидание аварии, чаще всего с большими
последствиями.
Все перечисленные стадии состояния свойственны всем типам подшипников
и видам дефектов. В зависимости от конструктивных и эксплуатационных
параметров имеются некоторые различия в их продолжительности, но при
этом общая картина разрушения одна и та же.
При работе ШПУ в подшипнике, имеющем дефект в спектре вибросигнала,
появляются гармонические составляющие от частоты вращения вала.
В нагруженном подшипнике имеются четыре основные, характерные
частоты: внешней обоймы; внутренней обоймы; сепаратора и тел качения,
которые можно использовать для диагностики ТС. Эти частоты
определяются по известным формулам [ 1].
Частота перекатывания тел качения по внешней обойме ( обозначаемая
ВРFО ):
(1)
где: Nтк- количество тел качения в одном
ряду подшипника;
F1-частота вращения вала;
Dтк-диаметр тела качения;
Dс-средний диаметр сепаратора;
φ- угол контакта тела качения с
обоймой.
Частота перекатывания тел качения по внутренней обойме (ВРF1):
(2)
Частота сепаратора (FTF):
(3)
Частота перекатывания тел качения (BSF):
(4)
Для обнаружения гармоник с вышеуказанными частотами необходимо
выполнить следующие условия:
подшипник должен быть нагружен усилием, близким к номинальному;
подшипник необходимо расположить так, чтобы дефектный участок
проходил через зону нагрузки;
исключить работу механизмов, имеющих вибросигнал с частотой, близкой
к частоте дефектов;
вибродатчик должен быть расположен достаточно близко к нагруженной
зоне подшипника;
частотные параметры датчика должны позволять регистрировать
гармоники с указанными частотами;
регистратор должен иметь разрешающую способность в диапазоне 400-800
линий.
Только при выполнении этих условий можно на ранних стадиях
диагностировать дефекты подшипника. В противном случае высока
вероятность или «пропуска» или «ложного»
определения дефекта.
Определение уровня развития дефекта в большой степени зависит от типа
используемой аппаратуры и места установки вибродатчика.
Для оценки технического состояния и диагностики дефектов
подшипников качения фирмами разработано много методов. Все они
отличаются по своим теоретическим предпосылкам, имеют разную
трудоёмкость, достоверность и конкретное приборное обеспечение.
В самом общем случае оценка технического состояния и поиск дефектов
подшипников качения может производиться :
По общему уровню вибрации.
По СКЗ виброскорости.
По спектру вибросигнала.
По соотношению пик/фон вибросигнала.
По спектру огибающей сигнала.
Диагностика по общему уровню вибрации. Данный способ
диагностики наличия дефектов в подшипниках, в своей основе, входит в
широко распространённую простейшую оценку общего технического
состояния оборудования.
Такая диагностика позволяет определять дефекты только на самой
последней стадии развития, когда они приводят или уже привели к
разрушению подшипников и, следовательно, к повышению общего уровня
вибрации. В принципе это уже предаварийная диагностика дефектов.
Критерии степени развития дефекта в данном методе полностью
ориентированы на соответствующие нормативные уровни вибрации,
принятые для данного механизма. Дефектным считается такой подшипник
качения, вибрации которого превысили общую норму для данного
агрегата. При таком повышении значения уровня вибрации обслуживающему
персоналу необходимо принимать решение о возможности дальнейшей
работы агрегата или о его остановке и замене подшипника.
Несмотря на позднее обнаружение дефектов, такой метод диагностики
состояния подшипников качения достаточно широко используется в
практике и даёт неплохие результаты в тех случаях, когда:
основной задачей проведения диагностического обследования
оборудования является только предотвращение аварий и их
последствий;
останов оборудования и замена подшипника могут быть выполнены в
оставшееся до аварии время без какого-либо ущерба для работы
установки и предприятия, без нарушения общего технологического
процесса;
цикличность проведения ремонтных работ на оборудовании такова, что
оставшийся срок службы подшипника с диагностированным дефектом
превышает оставшееся время работы до его вывода в ремонт по другим
причинам.
Достоинством этого, самого простейшего метода диагностики дефектов,
является так же то, что для его применения не требуется практически
никакого дополнительного обучения обслуживающего персонала, а
стоимость технического оборудования, необходимого для его внедрения,
минимальна.
Если на предприятии до какого либо времени не велись
вибродиагностические работы, то данный метод диагностики обеспечивает
наибольшую эффективность при своём внедрении. Применение всех других
методов диагностики подшипников всегда требует больших начальных
затрат и увеличивает срок окупаемости.
Диагностика по СКЗ виброскорости позволяет выявлять дефекты
подшипников на самых последних стадиях их развития, начиная,
примерно, с середины третьей, когда общий уровень вибрации
значительно вырастет. Требует минимальных технических затрат и нет
необходимости в специальном обучении персонала.
Диагностика по спектру вибросигнала применяется достаточно
часто, т.к. позволяет выявлять, наряду с дефектами подшипников,
дефекты различного оборудования. Он даёт возможность начинать
диагностику подшипников примерно с середины второй стадии развития
дефектов, когда энергия резонансных колебаний вырастет на столько,
что будет заметна в общей картине частотного распределения
вибросигнала. Для реализации данного метода необходим хороший
спектроанализатор и подготовленный персонал.
Диагностика по соотношению пик/фон вибросигнала разрабатывалась
несколькими фирмами и имеет различные модификации:
HFD ( High
Freguency Detection
– метод обнаружения высокочастотного сигнала);
SPM (Shock Pulse
Measurement- метод измерения ударных
импульсов);
SE (Spike
Energy- метод измерения энергии импульса).
Лучшие разновидности данного метода позволяют выявлять дефекты
подшипников качения на достаточно ранних , начиная примерно с конца
первой стадии развития. Приборы, реализующие данный метод
диагностики, достаточно просты и дешёвы.
Диагностика по спектру огибающей сигнала позволяет выявить
дефекты подшипников на самых ранних стадиях, начиная примерно с
первой. Основой является специальный датчик акустической эмиссии и
анализатор спектра, на который подаётся уже отфильтрованный датчиком
сигнал.
Этот метод в настоящее время считается классическим для анализа
вибросигналов с подшипников качения.
Все перечисленные методы различаются типом используемого
оборудования, его стоимостью, эффективностью и квалификацией
обслуживающего персонала. Чем на более ранней стадии и более
достоверно необходимо обнаружить дефекты подшипников, тем большие
затраты.
Самым эффективным методом обнаружения дефектов на ранних стадиях
является метод по спектрам огибающей. Кроме того , он менее
остальных подвержен различным помехам, и, как следствие, имеет
большую достоверность. Этот метод также позволяет проводить полный
анализ состояния оборудования, что делает его универсальным. В этом
случае набор технических средств для диагностики оборудования будет
минимальным по объёму и затратам.
В таблице (1) приведен перечень дефектов, диагностируемых в
подшипниках качения спектральными методами. Все дефекты представлены
в “хронологическом” порядке. Следуя этапам “жизненного
цикла” подшипника. Сначала идут дефекты, связанные с монтажом
подшипников. С ними приходится встречаться уже на этапе ввода
оборудования в эксплуатацию. Далее идут дефекты смазки, а за ними
следуют дефекты, вызванные износом подшипников. Замыкают таблицу
дефекты деталей подшипников типа “скол” и “раковина”.
-
Наименование дефекта подшипника
|
Использ. тип сигнала
|
Основ.част деф.
|
Наличие в сигнале гармоник
|
Порог сильного дефекта
|
Перекос наружного кольца при посадке
|
Спектр + огибающая
|
2 х Fн
|
k=1,2
|
16 %
|
Неоднородный радиальный натяг
|
Спектр + огиб.
|
k x F1
|
k=1,2
|
13 %
|
Проскальзывание в посад. месте
|
Огибаю-щая
|
k x F1
|
k=1,2,3
|
9 %
|
Ослабление крепления подшипника
|
Спектр
|
k x F1
|
k=0.5,1,2,3
|
13 %
|
Задевания в подшипнике и уплотнениях
|
Спектр
|
k x F1
|
k=0.5,1,1.5, 2,2.5,3
|
13 %
|
Проблемы смазки
|
Фон вибра ции
|
-
|
-
|
20
dB
|
Увеличенные зазоры в подшипнике
|
Спектр
|
k x F1
|
k=1,2,3,4,5,6...
|
13 %
|
Износ поверхности наружного кольца
|
Огибаю-щая
|
Fн
|
-
|
16 %
|
Износ поверхности тел качения
|
Огибаю-щая
|
Fc или F1-Fс
|
k=1,2,3
|
15 %
|
Износ поверхности внутреннего кольца
|
Огибаю-щая
|
kxF1
|
k=1,2,..6
|
13 %
|
Дефект группы поверх.трения
|
Огибаю-щая
|
Fн + Fв Fн+F1
|
k=1,2,...
|
16 %
|
Раковины
( сколы ) на наружном кольце
|
Огибаю-щая
|
k x Fн
|
k=1,2,3
|
16 %
|
Раковины
( сколы ) на внутреннем кольце
|
Огибаю-щая
|
k x Fв
|
k=1,2,3
|
15 %
|
Раковины
( сколы ) на телах качения
|
Огибаю-щая
|
k x Fтк
|
k=1,2,3
|
15 %
|
Обкатывание наружного кольца
|
Спектр+ огибающ.
|
F1
|
|
16 %
|
Дефекты изготовления и монтажа подшипников можно отнести к нулевой
стадии, а дефекты смазки и начальные этапы износа соответствуют
первой стадии, когда они только зарождаются.
Сильный износ и зона углубления дефектов подшипников относятся ко
второй стадии, третья -это их деградация, которая диагностируется уже
любым методом.
Для иллюстрации диагностики дефектов подшипников качения приведены
несколько спектров огибающей вибросигнала, свойственных наиболее
характерным дефектам.
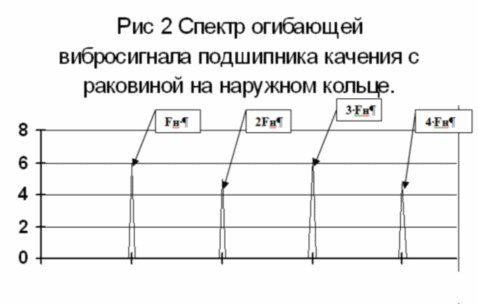
На рис.2. дан спектр огибающей вибросигнала с подшипника качения со
значительной раковиной на наружном кольце. На этом спектре имеется
более десяти гармоник с частотой, кратной частоте наружного кольца
подшипника. Других, значительных, гармоник на данном спектре нет,
поэтому диагностика дефекта не вызывает значительных трудностей.
На следующем спектре огибающей ( рис.3) - дефект типа “раковина”
на внутреннем кольце .Здесь также имеются гармоники частоты
внутреннего кольца, но есть и существенное отличие. Характерные
гармоники имеют боковые полосы, сдвинутые на частоту вращения ротора.
Дефект на внутреннем кольце не находится постоянно в нагруженной зоне
подшипника. В течении одного оборота ротора он то перемещается в
нагруженную зону, то выходит из неё. Таким образом дефект внутреннего
кольца модулируется частотой вращения ротора.
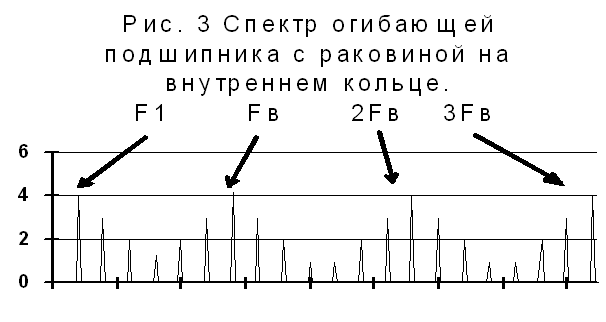
Диагностируемые дефекты принято характеризовать уровнями: слабый,
средний, сильный. Нормированию подлежит порог сильного уровня
дефекта, в долях от которого в дальнейшем рассчитываются пороги
среднего и слабого уровней. Порог среднего уровня дефекта чаще всего
считают равным половине величины порога сильного уровня, а порог
слабого обычно определяют 20 % порога сильного уровня дефекта.
Самым ответственным считается корректное определение уровня порога
сильного дефекта. При этом приходится учитывать три аспекта работы
подшипника и способа проведения замера вибрации:
Чем больше размер подшипника, тем более высоким должен быть уровень
порога сильного дефекта.
Чем выше рабочая частота вращения ротора механизма, тем выше должен
быть уровень порога сильного дефекта.
Измерительный датчик должен располагаться как можно ближе к
контролируемому подшипнику. При удалении датчика часть полезной
информации затухает в конструкции и уровень порога сильного дефекта
необходимо понижать.
Величина порога сильного дефекта во многом зависит от удалённости
элемента с дефектом от вибродатчика. Пороги дефектов внутреннего
кольца подшипника всегда ниже порогов дефектов наружного кольца. Это
объясняется увеличением затухания полезной состовляющей вибросигнала
на более длинном пути передачи, включая дополнительные зазоры в
подшипнике.
При использовании диагностики по спектру огибающей вибросигнала
уровень порога задаётся в % модуляции характерной гармоники
вибросигнала.
При использовании для диагностики дефекта подшипника классических
спектров вибросигналов уровень порога сильного дефекта может быть
задан в долях от нормированного допустимого значения виброскорости на
данном подшипнике или так же в % модуляции. По сравнению с нормой
необходимо использовать не полное , абсолютное значение виброскорости
на данном подшипнике, а только ту её часть , которая наведена
диагностируемым дефектом. Это несколько сложнее, но более точно.
При определении качества смазки за базу для сравнения берётся общий
уровень «фоновой» вибрации исправного подшипника с
хорошей смазкой. При повышении общего уровня «фона»
вибрации в десять раз, качество смазки считается
неудовлетворительным.
Обслуживающий персонал больше интересует вопрос о возможности
дальнейшей практической эксплуатации оборудования с дефектным
подшипником и тех ограничениях, которые накладывает обнаруженный
дефект на возможности использования оборудования. Очень важным для
практики является вопрос о сроках проведения очередного ремонта.
Первоначально состояние подшипника «контролируется» при
помощи достаточно стабильной модели нормального износа, когда в нем
отсутствуют внутренние дефекты. Так продолжается до момента
диагностики в подшипнике какого-либо дефекта. Здесь приходится
отказываться от нормальной модели и переходить к моделям ( ко всем
сразу!) развития дефектов. Очень важной задачей, решаемой при
переходе от нормальной модели развития дефекта к контролю состояния
по модели развития дефекта, является как можно более точное
определение времени зарождения дефекта. Чем точнее оно будет
определено, тем более достоверным будут дальнейшие прогнозы по
величине остаточного ресурса подшипника.
Максимальная скорость развития разных дефектов различна, поэтому
контролировать следует развитие всех возможных дефектов, даже когда
один из них только что зародился, а другой уже достаточно развит.
Никогда нельзя заранее сказать, какой из дефектов раньше всех
разовьётся до недопустимого уровня и послужит причиной смены
подшипника качения при ремонте.
Периодичность проведения диагностических измерений вибрации зависит
от максимальной скорости развития дефекта подшипника в данном
оборудовании. Замеры могут проводиться через интервал времени от
нескольких часов до одного года. При нормальной эксплуатации типового
оборудования и проведении замеров примерно через шесть месяцев
удаётся выявить большую часть дефектов на достаточно ранней стадии и
предупредить аварии.
После выявления первых признаков зарождающегося дефекта интервал
времени между двумя измерениями необходимо сократить. В зависимости
от локализации дефекта интервал времени между замерами сильно
меняется. Он минимален при дефектах тел качения, которые могут
развиваться очень быстро.
Подшипник подлежит замене или ежедневному наблюдению при наличии в
нём двух сильных дефектов.
Процедура контроля состояния многих подшипников на предприятии
становится возможной только при использовании компьютеров, в которых
создаются и работают базы данных по подшипникам и современные
экспертные системы диагностики.
4. Выводы из данного исследования и
перспективы дальнейших поисков в данном направлении.
В данной
статье приведен анализ спектров вибрации различных дефектов
подшипников качения.
В качестве источника информации использовался
вибросигнал.
Диагностика
состояния подшипника качения осуществлялась посредством анализа и
оценки амплитудно-частотных соотношений спектров вибрации
подшипниковых опор, получаемых методом стандартного спектрального
анализа вибросигнала с применением программы «Вибродиагностика».
|