Lyutyy Maikl
    Faculty: "Mechanical"
    Speciality: "Metal-cutting machine-tools and systems"
    Scientific leader:
Malyshko Ivan
Abstract of thesis:
«Countersink Improving productivity through optimization design parameters of an instrument Metal-cutting machines and systems »
Actuality of work
      The main indicators that determine the competitiveness of products, are its high consumer properties and low cost. High quality new products and rapid transition in its issuance provides multioperational machines (ISO) and flexible transfer lines (GAL). However, the high cost of equipment leads to increased production costs, making it not competitive. One effective way of reducing production costs is the concentration of transitions and reducing processing time. Most broad class of surfaces to be processed on flexible automatic lines and machines multioperational are holes, which make up 75% of all machined surfaces. The majority of holes require processing several instruments. Significantly improve the processing performance of these holes can be through the use of combined instruments (CI). Analysis of statistics shows that the CI can be used in the processing step as well as smooth cylindrical holes [1,2]. Csuschestvuyut different points of view on the usefulness of CI. For example, at the Kama Automobile Plant, CI 20% of total axial instruments, while at the factory to them. Likhachev - 80%. GAL produced by the German company Honsberg set at Melitopol Engine Plant, 80% CI staffed [1,2]. Such ambiguity in evaluating the usefulness of CI due to their shortcomings. Currently in the design of CI in most cases uses the same methodology as in the design of one-dimensional axial instruments. This leads to the fact that the shortcomings combined tools is largely inherent in the one-dimensional. Therefore it is necessary to analyze the techniques of design as a one-dimensional and combined axial instruments. Application of CI provides the following benefits: - increased alignment and positioning accuracy of the end surfaces of machined holes - reduced major technological time and auxiliary time associated with the inlet, outlet, replacing the instrument, its adjustment, which increases processing performance - reduces the number of technological equipment , power consumption and the number of workers, reduced production area, increases the reliability of automatic production lines, however, existing designs of CI due to the high concentration of cutting edges on a single instrument a number of disadvantages: - an increase of cut metal makes it difficult to accommodation and transportation for shaving grooves, which leads to package the chips, reduce the quality of surface finish, reduced tool life, and sometimes to malfunction - an increase of cutting forces leads to a break openings, errors in forms of longitudinal and cross sections - packing chips increases the frictional forces, cutting temperature rise, increased Application of tool wear, CI enhances the productivity of technological systems (TS), but this involves a decrease in accuracy. To date, the nomenclature of cutting tools that are used in automatic production, almost coincides with the applied on universal machines. However, they face more stringent requirements on the accuracy of size, shape and quality of grinding, designed in the form of specific standards. One of the challenges of modern production is to increase its productivity, and this in turn leads to an increase in specific volume of the metal, the shooting tool cutting edges per unit time. Using the combined axial tool. This may lead to the fact that bandwidth chip grooves is insufficient, and will limit the growth of productivity. Therefore, already at the stage of the design of tools necessary to take into account the parameters of the processing. In the literature, such studies were conducted for combined drills. However, virtually no studies related with the influence of geometric parameters on the performance of combined countersink cutting process. Therefore, subject master's thesis, devoted to the development of design techniques combined with countersink the productivity of the cutting process, is relevant.
Analysis of existent charts of polishing of spherical surfaces
      It should be noted that the issue of developing new designs, CI subject of many works, both domestic and foreign companies and individual authors [3,4,5,6,7,8,9,10].
AY Shmelev [10] partially codified design axial CI and give analytic expressions for the determination of some structural parameters of step drills.
Existing design techniques axial CI based on a systems approach. The basis for the model calculation the authors provided a form the treated surface [11,12,13]. CI is seen as a synthesis of separate stages, guiding element, a shaft. In the formulation of design synthesis CI first get all the elements included in the projected object, and then carry them dovetailing with each other [11]. Initial data for individual structural parameters are empirical relations, reference data and standards for one-dimensional instruments [13,14],
When designing the CI, and the appointment of cutting conditions, the recommendations and standards developed for one-dimensional instruments. It does not take into account the multiparametric nature of the impacts of working processes in the TS, at CI. Therefore, the design parameters of CI, derived from existing design methodologies do not have the optimum, corresponding multiparametric effects, which leads to the above-mentioned shortcomings in the work of CI.
Interaction design parameters of CI with the working processes in the TS, you can submit the scheme Figure 1.1. On this scheme amply represented multiparameter relationship between CI and workflow.
Given the multiple nature of the construction of CI and the multiparametric nature of their interaction with work processes, obtaining the optimal values of design parameters on emiiriko-statistical models is almost impossible.
The design tool should be considered as part of the TS and its design parameters defined in terms of business processes in the system. Moreover, please note that the interaction of design parameters with workflow is multiparametric nature.
Aims of the Master
      Thus, one cause of the deficiencies of CI, is the imperfection of their design and methodology of the project ¬ mation. Therefore, to eliminate these shortcomings can only be due to the choice of optimal design parameters, and modes.
The purpose of master's work is to develop design techniques combined countersink working on a combined scheme of processing to ensure maximum productivity of the process with sufficient accuracy.
In the master's work must meet the following objectives:
- Review the work of the combined two-stage countersinks processing valve body hydraulic rack in GPS
Analyze the possible schemes for processing;
- Examine the influence of design parameters at the accuracy of the workpiece at maximum capacity;
- With the help of a software package ANSSYS investigate the effect of cutting conditions on the accuracy of processing;
- To develop a method of designing a combined countersinks with the maximum processing performance;
- Check the adequacy of the developed technique to a specific example.
Model countersinks
      At the moment my developed and proposed a two-stage design countersinks. The process of cylindrical surfaces countersink shown in ris.1.2
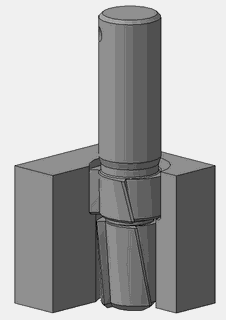
Figure 1.2. - Animated image processing cylindrical surfaces developed countersink (is made on mp_gif_animator 111 KB, 19 Frame, 7 cycle repetition)
Conclusions and prospects for further research
      To improve the effectiveness of automated vehicle can be through the use of CI with
optimal design options. The design parameters of CI are a function of working processes,
occurring in the TS. And between the design parameters and work processes, there are always optimum ratio at which the deficiencies
characteristic of this tool, virtually eliminated. Also, we must remember that the axial tool should be designed not to impersonal
consumer, and for a specific vehicle. Only in this case we can guarantee accuracy and quality of the surfaces. All this can be
subject of further research.
Literature
Малышко И. А. Осевые комбинированные инструменты (рекомендации по проектированию и эксплуатации)/И.А. Малышко.- Донецк: ПКТИ, 1996.-135 с.
Малышко И. А. Проектирование комбинированных осевых инструментов с учетом производительности технологической системы:/ И. А. Малышко, И. В. Киселева. –Донецк: ДонНТУ, 2009-139 с.
Розенберг О.А. Механика взаимодействия инструмента с изделием при деформи-рующем пpoтягивании Розенберг О.Л. -К Наукова думка. 1981.-288 с.
SARTORIUS Общий каталог Printed in Germany 2008 - 572 р.
ISCAR Общий каталог. Printed m Israil 10/2005 - 1166 p.
Инструментальная система фирмы KRUPP WIDIACMPTE каталог.-Германия. 1 1990. - 24 с.
Каталог инструментов фирмы Hertel - Германия, 1983 - 70 с.
Комбинированные инструменты: каталог фирмы HEGENSCHEL DТ CORPORATION (USA). 1988 - 4 с.
Исследования, касающиеся точности обработки сверхтвердыми развертками. Явление нарезки и механизм ее возникновения.// Кэйдзо Сакума, Хироси Киета и Гуан-дзи Лю. 1981 - № 54 - С 723-728.
Максимов М.А. Комбинированные режущие инструменты./ Максимов М А., Киселева Л П., Шмелев А.Я. – Горький: Горьковский государственный университет, 1977, 86 с.
Инструменты для обработки точных отверстий / [Кирсанов С. В., Гречишников В А., Схиртладзе А.Г., Кокарев В.И.]. – М.: Машиностроение, 2003.-330 с. - (Биб-лиотека инструментальщика).
Динник А.Н. Продольный изгиб. Кручение./Динник А.Н. – М.: Изда¬тельство АН УССР, 1955 - 322 с.
Лашнев С.И. Проектирование режущей части инструмента с примене¬нием ЭВМ./ Лашнев С.И., Юликов М.И. – М.: Машиностроение, 1980 - 208 с.
Якобс Г.Ю. Оптимизация резания. [Перевод с немецкого] / Якобс Г.Ю., Якоб Э., Кохан Д – М.: Машиностроение. 1981 - 278 с.
Important note:
During the process of writing, the master’s work hasn’t completed yet. Final completion: December, 20010. The full text of work and materials on the theme could be received from the author or him scientific adviser after the indicated date.
DonNTU |
Master's port |
Biography |
|