
ДонНТУ |
Портал магістрів ДонНТУ
Шальська Олена Євгенівна
Факультет інженерної механіки та машинобудування
Кафедра: Технологія машинобудування
Тема випускної роботи:
"Підвищення продуктивності обробки та якості деталей машин за рахунок вибору раціональних умов використання сучасних матеріалів"
Про автора
Реферат з теми випускної роботи
Актуальність роботи
      Підвищення якості деталей машин завжди було найважливішим завданням машинобудування.
      З точки зору забезпечення якості поверхневого шару, найбільш актуальною є задача обґрунтування остаточного методу обробки відповідальних поверхонь деталей, що визначають експлуатаційні властивості виробу в цілому. Одним з перспективних шляхів вирішення цього завдання є використання обробки матеріалів тонким точінням.
      Об'єктом дослідження є корпусні деталі, зокрема буде розглядатися деталь з чавуну "Блок циліндра", до поверхні отвора якого пред'являються високі вимоги.
      Найбільша ефективність застосування тонкого точіння можлива при правильному, оптимальному виборі режимів різання, схем обробки, геометрії та конструкції інструментів. Для вирішення цих завдань необхідно встановлення зв'язку між експлуатаційними властивостями і параметрами поверхневого шару деталей.
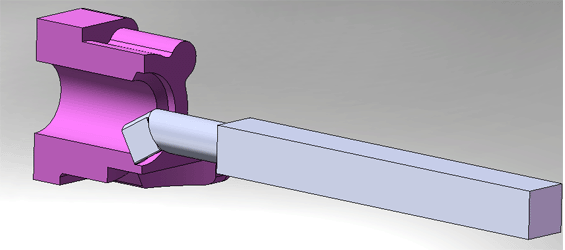
Рис.1 Схема обробки отвору розточуванням
(Анімація розроблена у програмі Gif animator: кількість кадрів - 5, кількість циклів - 10, розмір - 151Кб)
      Розробка рекомендацій по вибору оптимальних режимів різання, розробка математичної моделі для розрахунку параметрів оптимальних умов обробки, необхідних для вирішення задач забезпечення якості обробки деталей з чавуну і визначають актуальність даної магістерської роботи.
Цілі і завдання дослідження
      Мета роботи - підвищити продуктивність і якість обробки деталей машин за рахунок вибору раціональних умов використання сучасних інструментальних матеріалів.
      Основні завдання дослідження:
- Дослідити номенклатуру сучасних інструментальних матеріалів та конструкцію інструментів, оснащених пластинами з ельбору.
- Вивчити особливості процесу обробки різанням інструментами, оснащеними НТМ
- Розробка технологічного процесу обробки деталі типу "корпус"
- Розробка математичної залежності температури різання від режимів різання при обробці інструментами, оснащеним НТМ
- Розробка методики оптимізації режимів різання методом геометричного програмування при тонкому точінні
- Розробка рекомендацій з вибору оптимізації режимів різання
- Обґрунтування доцільності застосування тонкого точіння при обробці чавунів на прикладі деталі типу "корпус" .
Огляд досліджень по темі
     Ефективним способом підвищення якості і точності обробки деталей є вживання інструментів з надтвердих матеріалів, проводячи дослідження по цій темі можна виділити безліч робіт.
      Так наприклад в книзі [10] авторами розглянуті фізико-технічні властивості різновидів кубічного нітриду бору (ельбор-Р, белбор-Р, гексаніт-Р та ін.), синтетичних алмазів і кераміки. Викладені основні відомості за технологією їх виробництва і сферами застосування. Наведені приклади обробки типових деталей інструментами, оснащеними цими матеріалами.
      Зведення про технологічні процеси обробки полікристалічних надтвердих матеріалів (ПСТМ) при виготовленні і відновленні ріжучого інструменту викладені в довіднику [11] Н.В. Новіковим. Так само в цій роботі приведені режими різання при обробці різних важкооброблюваних матеріалів.
      У роботах [6] і [7] А.Г. Сусловим вивчені закономірності формування поверхневого шару оброблюваних деталей і умови раціонального вживання інструментальних матеріалів.
      Але не дивлячись на велику кількість досліджень в цьому напрямі, багато питань залишаються досить актуальними.
Наукова значимість
      Наукова значимість роботи полягає:
у розробці моделі визначення температури різання при тонком точінні деталей в залежності від режимів різання;
розробка математичної моделі оптимізації режимів різання за критерієм мінімальної собівартості з застосуванням методу геометричного програмування;
розробка математичної моделі визначення шорсткості поверхневого шару в залежності від режимів різання.
Підвищення ефективності застосування надтвердих інструментальних матеріалів за рахунок оптимізації режимів різання
      Одним з резервів підвищення ефективності сучасного машинобудівного виробництва є застосування надтвердих інструментальних матеріалів (НТМ) при обробці деталей машин. При використанні інструментів, оснащених НТМ досить актуальні дослідження з визначення оптимальних режимів різання, що забезпечують для заданих умов обробки та вимог до якості оброблених поверхонь мінімальну собівартість.
      Одним з найбільш поширених методів оптимізації в даний час є метод лінійного програмування [1, 2, 3], що дозволяє здійснювати одночасну оптимізацію швидкості різання і подачі з урахуванням діючих при різанні обмежень за критерієм максимальної продуктивності. Обов'язковою умовою використання цього методу є можливість лінеаризації цільової функції й обмежень. Незважаючи на простоту і наочність, цей метод не дозволяє вирішувати задачі оптимізації режимів різання в разі нелінійної цільової функції, якою є собівартість обробки деталей.
      Такого недоліку позбавлений метод геометричного програмування (МГП), який знайшов широке застосування для пошуку оптимальних проектних рішень в різних областях інженерних досліджень, але недостатньо поширений в теорії механообробки [2]. У зв'язку з цим представляє інтерес подальший розвиток МГП стосовно завдань оптимізації режимів різання при використанні інструментів з НТМ.
      Метою даної роботи є визначення оптимальних режимів різання, що забезпечують мінімальну собівартість обробки при заданому рівні якості обробленої поверхні при тонкому точінні з використанням різців, оснащених ельбором - Р.
      Основна вимога МГП полягає в тому, що всі компоненти задачі оптимізації повинні бути виражені кількісно у вигляді узагальнених позитивних поліномів, званих позіномамі, від керованих параметрів. Можливість використання МГП для оптимізації режимів різання обумовлена тим, що цільова функція й обмеження можуть бути представлені у вигляді суми компонентів, кожен з яких виражається степеневою функцією:
(1)
де Ci – позитивна константа; Xj - параметри, які оптимізують; aij - довільні дійсні числа;n – кількість компонентів;m- кількість параметрів.
      При оптимізації режимів різання тонкого точіння в якості критерію оптимізації приймається змінна частина собівартості обробки деталі різальним інструментом за один прохід, що залежить від режимів різання:
(2)
де А - собівартість верстато - хвилини, Аи – вартість одного періоду стійкості інструмента; to- основний час обробки; tc - час зміни інструмента; T - стійкість інструменту.
      Цільова функція, що виражає залежність змінної частини собівартості від режимів різання, з урахуванням відомих співвідношень основного часу обробки та стійкості інструмента з режимами, має вигляд
(3)
де D, L - - діаметр і довжина оброблюваної поверхні; Δ припуск на обробку; V - швидкість різання; S – подача; t – глибина різання; CТ – коефіцієнт і x, y, m – показники, що характеризують ступінь впливу глибини t, подачі S і стійкості T на швидкість різання V, що визначаються в залежності від умов обробки.
      У даній роботі вирішується завдання двопараметричної оптимізації, тобто задача визначення оптимальних значень швидкості різання і подачі при заданій глибині різання в умовах однопрохідної обробки (t = Δ).
      Тоді цільова функція може бути представлена наступним чином:
(4)
      де 
      Для тонкого точіння необхідно враховувати обмеження по гранично допустимої шорсткості обробленої поверхні Ra:
(5)
де k0, k1, k2, k3, k4 – - коефіцієнти і показники, які характеризують міру впливу подачі S, радіусу при вершині r, швидкості V і переднього кута γ на шорсткість обробленої поверхні Ra.
      Це обмеження необхідно представити в наступному вигляді:
(6)
де коефіцієнт 
      Математична модель задачі оптимізації швидкості різання і подачі при тонкому точінні розподілена так:
- пряме завдання МГП - мінімізувати
(7)
при обмеженнях
- двоїста задача МГП - максимізувати
(8)
при обмеженнях
(9)
      Згідно МГП на першому етапі оптимізації швидкості різання і подачі розв'язується система лінійних рівнянь (8), що має єдине рішення:
(10)
      Особливість МГП є можливість уже на першому етапі вирішення оцінити внесок кожної складової цільової функції в загальну собівартість С - (3). Вартість першої складової, пов'язана з машинною обробкою оцінюється вагомістю W01, а складова, пов'язана зі зміною інструменту - W02.
      Далі обчислюється екстремум цільової функції, для чого розраховується максимум двоїстої функції V(W) - (7). На підставі знайденого екстремуму цільової функції складається система лінійних рівнянь для визначення оптимальних режимів різання:
(11)
      У результаті рішення цієї системи визначаються оптимальні подача S0 і швидкість різання V0:
(12)
      Враховуючи, що C02=MC01, встановлюємо:
(13)
де 
      Приклади визначення оптимальних режимів різання, що забезпечують мінімальну собівартість, наведені для токарної обробки загартованої інструментальної сталі Р18 (HRC 62-64) на токарно-гвинторізному верстаті з ЧПК 16К20Ф3. Для цих умов прийнято: собівартість верстато-хвилини А = 0,5коп/мин., Вартість одного періоду стійкості інструменту Аи = 15 коп; час зміни інструменту tc = 1мин.
      Для тонкого точіння використовуються різці, оснащені ельбором Р (передній кут γ = -10, радіус при вершині r = 0,5мм); глибина різання t = 0,5мм; необхідна шорсткість поверхні Ra = 0,63 мкм. Для зазначених умов обробки прийняті наступні коефіцієнти і показники: CТ = 2,8•104, kV = 0,65, kS = -0,52 [4].
      Коефіцієнти і показники, що характеризують ступінь впливу подачі, переднього кута, радіус при вершині і швидкості різання на шорсткість обробленої поверхні: k0 = 0,68; k1 = 0,77; k2 = -0,28; k3 = -0,19; k4 = 0,66 [5]. Розрахункові значення коефіцієнтів С01 = 392,7, СО2 = 4,557; С11 = 16,27. Коефіцієнти вагомості, певні у відповідність з формулою (10), рівні: W01 = 0,28; W02 = 0,72, W11 = 0,85. Оптимальні значення подачі і швидкості різання, розраховані у відповідність з формулами (13) рівні: Sо = 0,084 мм/об, Vо = 54.2 м/мин.
      Наявність аналітичних залежностей для визначення оптимальних режимів різання істотно спрощує розробку рекомендацій з вибору раціональних умов обробки, що особливо актуально для тонкого точіння.
      Для тонкого точіння оптимальна подача Sо збільшується зі збільшенням шорсткості поверхні Ra і радіусу при вершині r; оптимальна швидкість різання Vо збільшується зі збільшеним радіусом при вершині r і зменшується зі збільшенням шорсткості поверхні Ra (рис.1).
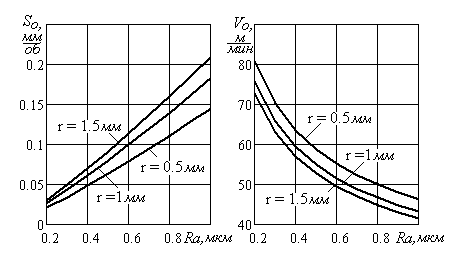
Рис.2. Графіки залежності оптимальних значень подачі S0 і швидкості різання V0 від шорсткості обробленої поверхні Ra для різних радіусів при вершині r при тонкому точінні
      На підставі встановлених аналітичних залежностей для визначення оптимальних режимів різання може бути розрахований коефіцієнт зміни собівартості обробки при відхиленні вибраних режимів різання від їх оптимального значення S = kS0, V=kV0. (K - ступінь відхилення):
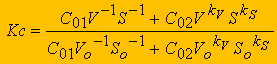
(14)
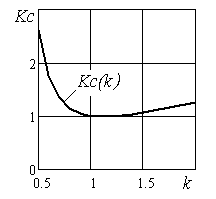
Рис.3. Залежність коефіцієнта зміни собівартості обробки від ступеня відхилення режимів від оптимальних
      З графіка, представленого на рис. 2, випливає, що мінімальна собівартість обробки має місце при k = 1, тобто при оптимальних режимах різання. При відхиленні режимів різання, як в менший, так і в більший бік від оптимальних, собівартість збільшується.
      Таким чином, представлена методика дозволяє для будь-яких умов тонкого точіння виконувати розрахунки оптимальних режимів різання, що забезпечують мінімальну собівартість обробки.
Заплановані практичні результати
      У практичній цінності результатів дослідження слід виділити, що:
- На базі виконаних досліджень підвищена продуктивність на 30 - 40% за рахунок оптимізації режимів різання;
- На підставі розробленої методики встановлені закономірності зміни оптимальних значень подачі і швидкості різання від шорсткості обробленої поверхні і радіусів при вершині;
- Розроблено рекомендації щодо вибору оптимальної конструкції режимів різання;
- Розроблена методика визначення оптимальних режимів різання може бути широко використана для будь-яких видів обробки.
Література
- Старков В.К. Обработка резанием. Управление стабильностью и качеством в автоматизированном производстве. - М.: Машиностроение. 1989. - 296с.
- Оптимизация и управление процессом резания: / О.С. Кроль, Г.Л. Хмеловский. – К.: УМК ВО, 1991. – 140с.
- Ивченко Т.Г., Дубоделова О.С. Исследование возможностей комбинированой лезвийной и отделочно-упрочняющей обработки по повышению качества поверхностного слоя и производительности // Прогрессивные технологии и системы машиностроения: Международный сб. научных трудов. – Донецк: ДонНТУ, 2006. Вып. 31. – С.140-146.
- Лезвийный инструмент из сверхтвердых материалов: [Справочник] / Н.П. Винников, А.И. Грабченко, Э.И. Гриценко и др.; Под. общ. ред. акад. АН УССР Н. В. Новикова. — К.: Техніка, 1988. - 118 с.
- Суслов А.Г., Дальский А.М. Научные основы технологии машиностроения. М.: Машиностроение, 2002. - 84с.
- Суслов А.Г. Качество поверхностного слоя деталей машин. - М.: Машиностроение, 2000. - 320с.
- Качество машин: Справочник. В 2 т. Т.1 / А.Г. Суслов, Э.Д. Браун, Н.А. Виткевич и др. - М.: Машиностроение, 1995.-256с.
- Исследование температуры в зоне резания при точении на токарном станке.(Тольяттинский филиал
Самарского Государственного Педагогического Университета)[Электронный ресурс] - Режим доступа - http://allreferat.org.ua/ref/00030665.txt
- Ивченко Т.Г. Исследование общих закономерностей изменения температуры резания в различных условиях обработки [Электронный ресурс] -Режим доступа - http://www.nbuv.gov.ua/portal/natural/Npdntu/Mim/2009/7.pdf
- Режущие инструменты, оснащенные сверхтвердыми и керамическими материалами, и их применение: Справочник/В.П.Жердь, Г.В. Боровский, Я.А. Музыкант, Г.М. Ипполитов. - М.:Машиностроение, 1987. - 320с.
- Лезвийный инструмент из сверхтвердых материалов: Справочник/Н.П.Винников,А.И.Грабченко,Э.И. Гриценко и др.; Под общ. ред. АН УССР Н.В. Новикова. - К. Техника, 1988. - 118с
Про автора
ДонНТУ > |
Портал магістрів ДонНТУ