АНАЛИЗ СХЕМЫ ОБРАБОТКИ ДАВЛЕНИЕМ С ВРАЩАЮЩИМСЯ ИНСТРУМЕНТОМ В РОТОРНЫХ МАШИНАХ
Чернышев Е.А.
Донецкий национальный технический университет,
г. Донецк, Украина
This brief sketch deals with one special case of a processing method to press wire products’ in rotor machines unless the following is taken into account. To the author’s mind, this is an example of how very good-looking abstract idea is able to be rejected as soon as concretization takes place.
Стаття присвячена аналізу одної схеми обробки на роторних машинах для висадження головок стержневих виробів. Показано її великий недолік. На погляд автора, це є приклад того, як приваблива абстрактна ідея може бути спростована, як тільки має місце конкретизація питання.
При анализе новых схем обработки на роторных машинах, которые позволяют существенно повысить производительность [1], одной из основных задач является выбор рациональной схемы, как с точки зрения ее конструктивной реализации, так и с позиции точности обработки. Ибо многие теоретически возможные абстрактные схемы технологического воздействия [2], которые не только имеют элементарную кинематику, но и реализуются простой конструкцией (а это несомненный плюс), к сожалению, не выдерживают даже первого критического анализа, как только речь идет о качестве обработки.
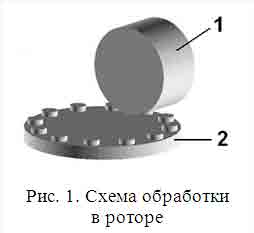
В данной статье рассмотрен такой вариант обработки давлением головок проволочных метизов, схема которого показана на рис. 1. Как видно, обработка давлением осуществляется при вращении инструмента 1 и ротора 2, т.е. имеет кинематику фрикционной передачи, но без проскальзывания, т.к. окружные скорости на начальной окружности ротора и на периферии инструментального диска равны между собой. Эта конструкция имеет то неоспоримое преимущество, что механизма рабочего хода, как такового, нет, ибо обработка осуществляется простым качением за счет вращения инструментального диска. Следует отметить, что данная схема была получена в результате кинематического синтеза на основе комбинирования элементарных движений [3], т.е. с использованием морфологического подхода – мощного метода поиска вариантов решений в инженерных задачах.
Однако определим рабочий угол, т.е. угол поворота ротора, на котором происходит обработка. Обратимся для этого к схеме на рис. 2, на которой обозначены: - радиус инструмента, - радиус начальной окружности ротора, h – высота выступающей проволоки (т.е. величина рабочего хода), - соответственно рабочие углы для инструмента ротора, - угловые скорости инструмента и ротора.
Наглядно видно, что рабочий угол для инструмента определится следующим образом:
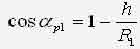
По условию равенства окружных скоростей
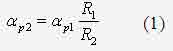
Так как рабочий угол для ротора, очевидно, не может быть равен нулю, то всегда есть скольжение инструмента относительно заготовки, которое на рис. 2 обозначено s. Найти его не составляет труда:

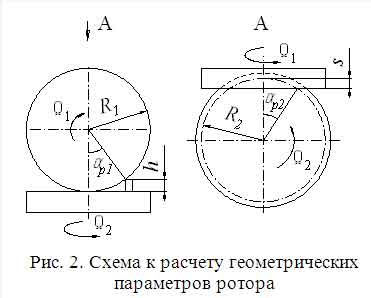
Подставляя (1) в (2) и полагая радиусы равными, легко записать, что , а это означает, что скольжение инструмента равно величине рабочего хода. Если посмотреть на этот факт с точки зрения обработки давлением, то инструмент вместо того, что-бы совершить вертикальное движение сверху вниз, скажем, на 5 мм, осуществит вдобавок движение в сторону на те же 5 мм. Разумеется, инструмент в действительности совершает только вращение, но относительно заготовки какая-либо элементарная площадка поверхности инструмента будет совершать именно вышеописанное движение. Нет нужды говорить о том, к какому результату это приведет.
Конечно, чисто математически мы имеем право записать, что но какова практическая сторона такой записи? Кроме того, радиус инструмента должен быть как можно б?льшим, чтобы угол, под которым начинается обработка, был существенно меньше угла трения, - иначе заготовка будет смята в сторону при качении. Например, для рабочего хода 5 мм этот радиус должен быть не менее 300 мм, и тогда совершенно ясно, что, избегнув смятия качением, заготовка будут смята относительным скольжением, ибо для того, чтобы скольжение не превышало, к примеру, допуск на круглость головки (порядка 0,5 мм) – хотя это тоже недопустимо большая величина, - радиус ротора должен быть 3 метра.
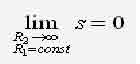
Таким образом, с точки зрения качества обработки данный способ формообразования в роторе имеет внутренне присущие противоречия, обусловленные как раз его кинематикой. Иначе говоря, кинематическая простота является только кажущейся, ибо приведённые рассуждения сделаны не более чем из геометрических соображений. Более того, с точки зрения кинематического синтеза такой способ обработки очень перспективен ввиду очевидных преимуществ конструктивного характера. И тем не менее он отброшен самым поверхностным анализом геометрии.
Как результат можно отметить, что привлекательная сторона абстрактного подхода к решению инженерных задач таит в себе то недопустимое, по мнению автора, упрощение, что методы, пригодные в одних условиях, переносятся в совершенно другие, которые могут не иметь ничего общего с первыми. Поэтому использование абстрактных схем должно сопровождаться критическим анализом конкретных особенностей того или иного решения.
Список литературы:
1. Кошкин Л. Н. Роторные и роторно-конвейерные линии. - М.: Ма-шиностроение, 1986. - 320 с.
2. Михайлов А.Н. Основы синтеза поточно-пространственных технологических систем. - Донецк: ДонНТУ, 2002. - 379 с. 3. Матвиенко А.В., Ищенко А.Л., Коваленко Т.В. Гибкие технологические системы на базе роторных машин// Прогрессивные технологии и системы машиностроения: Межд. сб. науч. тр. - Донецк: ДонГТУ, 2001. Вып. 9. - С. 190 – 195.
|