CONTINUOUS TECHNOLOGICAL SYSTEMS AS AN ALTERNATIVE WAY OF NAIL PRODUCTION
Chernyshev E.A., Mikhaylov A.N. (DonNTU, Donetsk, Ukraine)
The article is dedicated to the question of using continuous technological systems for nail production. The features of nail automatics, their limitations and advantages of rotor lines are considered in the article.
Nail production is the important part of machine-building because consumption of nails is the mass process. Therefore, nail production should be arranged well, corresponded with quality requirements and production efficiency.
For many years, nail automatics have been used for this purpose [1-3]. They permit to reach high cycle productivity (13 s-1 for nails in diameter 1.2 mm [2, 3]) and ensure required product quality. It should be noted, that these machines have not almost been changed for long time. Although high productivity for nails of small diameter, it is decreased substantially for nails in diameter 3…6 mm and it equals 3 s-1 [2, 3]. It can be explained with two factors: working regime with intermittent a nail heading and wire feed, and high speeds to obtain required productivity.
For such automatics, one finished product is the result of one kinematics cycle. It is the immanent property of a crank mechanism of a nail heading. The equation for cycle productivity of a nail automatic can be derived [4-6]:
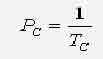
where Рс is the cycle productivity, s-1;
Рс is the time of complete kinematics cycle.
As can be seen, the way to increase cycle productivity consists in decreasing , i.e. increasing of working feeds. It leads to harmful dynamic processes such as vibrations, chatters and sometimes breaking of details. Thus, high speed of working regime is the property of the nail automatics through their structure features.
To our mind, using continuous technological systems (CTS) is an alternative way of nail production. The fundamentals of designing such systems in form of rotor and rotor-conveyer lines was formulated by academician L.N. Koshkin [4] and developed later [5, 6]. In contradis-tinction to processing of the nail automatics, the principle of such systems work consists in processing of workpieces during their transport motion. The cycle productivity of CTS can be defined by the formula [4-6]:

where U is the number of working positions.
This equation shows that the number of workpieces equal the number of working po-sitions is being processed during one kinematics cycle. Consequently, the way to increase consists in increasing U.
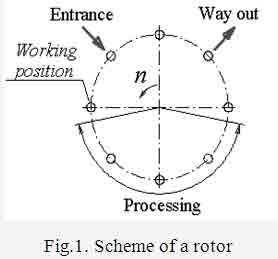
A rotor can be imagined as line of workpieces and tools wrapped in the circle (Fig.1). In work, the rotor is rotated and during certain time a workpiece processing is being implemented. For processing of workpieces with more complex technological process, sequence from some rotors can be applied.
It is important to note, that whole technological process can be automated on rotor line including quality control. Therefore, using CTS (rotor lines) permits to realize complete automa-tion of production. .
Moreover, the principle of rotor work itself permits to avoid an operating mechanism for heading process. It can be reached with simple transport motion of dies and workpieces. Compare two ways to stamp a nail head (Fig.2). In the traditional method (Fig.2a), the heading force is ensured with an operating mechanism, which realizes reciprocating of a die. It cab be obtained with a hydraulic working or mechanical way.
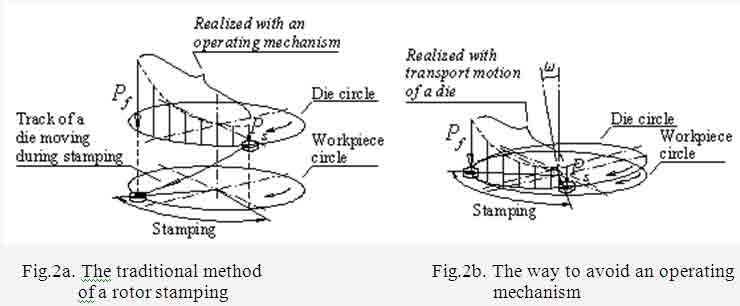
The second way consists in simple transport motion of dies and workpieces as shown in Fig.2b. The die circle is inclined relative to the workpiece circle and the distance be-tween the die and the workpiece is being decreased that gives a chance to realize heading process without special operating mechanism. The negative factor to consider is bending forces arising due to the angle ? (Fig.2b). It creates the limitation of this angle which should be sufficiently small. Numerical modeling of a nail heading with this method is considered in [7]. We can state that at least the numerical solution of the problem shows possibility to apply this method for rea-lizing heading process.
Conclusions. The nail automatics for nail production have immanent properties, which do not allow increasing their productivity. To our mind, continuous technological systems are the more progressive equipment permitting to increase productivity and realize complete automation of production. Also, the rotor principle of work gives the unique chance to realize heading process without special operating mechanism. We think that using continuous technological sys-tems is the step in machine-building development.
References:
1. С.А. Василишин, И.Г. Гураль. Высадка гвоздей с увеличенной головкой// Кузнечно-штамповочное производство. 2001. №8. С. 11 – 13.
2. Г. А. Навроцкий. Холодная объемная штамповка. Справочник. - М.: Машиностроение, 1973. - 628 с.
3. Высокопроизводительное оборудование для производства гвоздей. А.А. Королев, Л.С. Кохан, И.Н. Киреев, А.В. Курилс. – М.: Черметинформация, 1971. – 38 с.
4. Кошкин Л. Н. Роторные и роторно-конвейерные линии. - М.: Машиностроение, 1986. - 320 с.
5. Клусов И. А. Проектирование роторных машин и линий: Учеб. пособие для студентов маш. спец. вузов - М.: Машиностроение, 1990. - 320 с.
6. Михайлов А. Н. Основы синтеза поточно-пространственных технологических систем. - Донецк: ДонНТУ, 2002. - 379 с.
7. Чернышев Е.А., Михайлов А.Н. К вопросу синтеза высокоэффективной технологии формообразования проволочных изделий на роторных машинах// Прогресивні технології і системи машинобудування: Міжнародний зб. наукових праць. – Донецьк: ДонНТУ, РВА ДонНТУ, 2005. – Вип. 29. С. 212 – 219.
|