Advanced controls — fuzzy logic for fluidized bed boiler
Авторы: Dr.Tech. Joronen Tero, Dipl. Ing. Kerschbaum Rupert
Источник: http://herkules.oulu.fi/../isbn9514255194.pdf
Описание: Рассмотрен способ управления котлоагрегатом при помощи Fuzzy логики, ее применение для реализации контроля и оптимизации параметров процесса. Получены результаты, показывающие повышение эффективности сжигания, и уменьшение использования известняка, аммиака и вспомогательных топлив.
Abstract
Fluidized bed combustion is a good technology for burning wet and varying fuels
with low flue gas emissions and high efficiency. A supervisory level control application
constantly controls CFB [Circulating Fluidized Bed] or BFB [Bubbling Fluidized
Bed] combustion to minimize flue gas emissions (NOx [nitrogen oxides], SO2 [sulfur
dioxide], and CO [carbon monoxide]), improve combustion efficiency, and reduce
use of limestone, ammonia and auxiliary fuels. Combustion symmetry is controlled
by means of balancing the fuel feed. Fuzzy logic is used to create controls and optimization
functions in this multivariable and non-linear process. Fuzzy logic should be
the fine-tuning for every BFB and CFB.
Keywords: Fluidized Bed Combustion, Fuzzy Control, Emission Control, Process
Optimization
Introduction
In the Finnish paper and pulp industry the share of fluidized bed technology in burning solid fuel has remarkably increased recently. The first energy solution for FBB was
implemented in 1970's and after that the technology has
been studied and utilized a lot. Finnish research in the field
of combustion technology has been conducted in the form of
a program since 1988, when the Energy Department of the
Ministry of Trade and Industry launched the first phase of
the LIEKKI-program (Hupa and Matinlinna 1998). The research
is continuing as the CODE-program [Modeling Tools
for COmbustion Process DEvelopment]. One part of the
program is to study overall combustion kinetics of solid fuel
in a fluidized bed boiler (Hupa 2000). This information is
used also to design advanced control systems. For decades
the control of fluidized bed boilers has been a great interest
of studies (Pyykkö and Uddfolk 1997, Joronen 2000, Keyes
and Kaya 1984, Criswell 1980, Nyström 1983, Tuovinen and
U. Kortela 1988, Karppanen 2000, Markkula et al 2000,
Kortela et al 1994).
Modern fluidized bed combustion technology has proven
itself to be a way of efficiently disposing of large quantities
of waste water sludge, paper production wastes and other
mill wastes while meeting the latest flue gas emission requirements
(Kokko and Niemelä 2000, U.S. Department of
Energy 2000). Fluidized bed combustion has become a
lower cost alternative to older grate technology. The most
important feature controlling a fluidized bed boiler is bed
control, which means maintaining the proper fluidization and
temperature profiles in the furnace. This demand corrects
air and fuel controls. Traditionally combustion optimization
has been left to an operator. Making corrections to running
models is usually difficult; it is necessary to make adjustments
constantly. The operators do not usually have the
time or sometimes the skills to do this. Solutions to manage
the combustion have been sought from process automation.
While automation manages the combustion, load changes
and variation in fuel quality get paid special attention and
conditions in the furnace are optimized irrespective of load
level or prevailing fuel (Joronen 2000).
Metso Automation has developed an advanced combustion
control application, which runs as an integrated part of metsoDNA
(Metso Automation's Dynamic Network of Applications).
The application utilizes measurements existing in the
standard instrumentation level, including on-line O2 and CO
measurements, together with measurements from the most
significant online emission analyzers. The application provides
set point and parameter outputs to the basic controls.
The application consists of two levels — the coordination
level, which stabilizes the process, and the supervisory
level, which optimizes the process. The supervisory level
control methods are based, among other things, on fuzzy
logic. This advanced combustion control application is made
up of several subsystems, and contains displays for basic
operation, tuning and follow-up (Pyykkö and Uddfolk 1997,
Joronen 2000, Markkula et al 2000)].
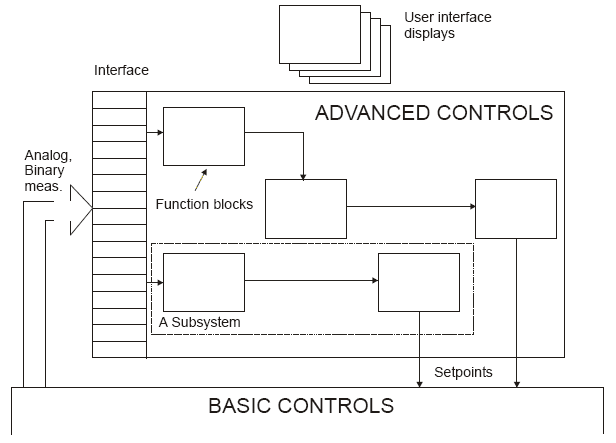
Figure 1 — System diagram, which shows
the application architecture
1. Problems in FBB technology
In the combustion of solid fuels, 90 % of disturbances arise from the fuel. Fuel quality, inconstant flow or symmetrical
feed cause variations. Normally the boiler itself and the air system function as they are designed, but proper handling
of varying solid fuels is still an enigma. As the solid fuel burns quickly in the bed, and neither the amount nor quality
of fuel are constant, there are always oscillations in the combustion. Rapid load changes and imbalance in fuel distribution magnify this effect. These combustion oscillations cause increased emission levels (Joronen 2000).
Emissions are produced as a result of complex chemical reactions. These reactions are a natural part of combustion
and cannot be optimized independently of one another. The principle effects of some operating parameters cannot be
easily decoupled from each other. Combustion management has to take in to consideration all these effects. Fluidized bed combustion, as any combustion process, is multivariable and the cross effects between variables need to be taken in to account (Joronen 2000).
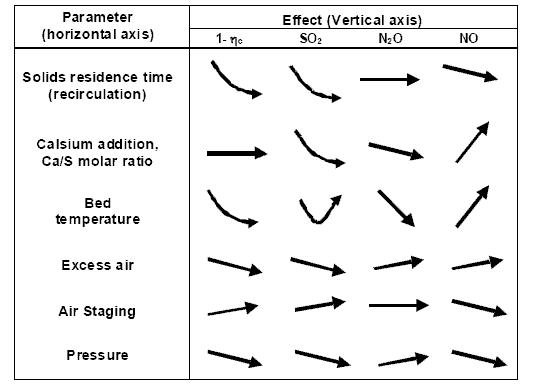
Figure 2 — The phenomenal effects of increases
in operating parameters in CFB
Naturally CO-emissions are low in FBB, so the oxygen level can be quite low. When O2-level decreases, the probability of carbon monoxide concentration in the flue gas increases.If there is not enough air, combustion is incomplete and there will be unburned particles and carbon monoxide (CO) in the flue gas. But even if the total airflow is sufficient, uneven distribution may cause production of CO. For this reason it is important to assure of uniform mixing and turbulence in the whole furnace. Combustion can be incomplete also if the fuel feed increases too rapidly compared to maximum speed of change in airflow (Joronen 2000). Combustion speed of CO and unburned particles can be kept in the acceptable range while the bed temperature is kept high, even when burning low-calorimetric fuel.
Thermal nitrogen oxides (NOx) reaction speed is highly dependent on the combustion temperature. To avoid NOx
generation, the temperature should be as low as possible and kept constant. Especially, there should not be any hot
spots in the furnace as these produce nitrogen oxides. Nitrogen oxides can be reduced back to harmless nitrogen
gas (N2) in low-oxygen combustion conditions. In a BFB, air distribution can easily be staged so that these reductive
conditions are reached. The staging has physical limits; the temperature and air ratio needs to be high enough for combustion in the upper furnace. In a CFB the N2O-emission can be remarkable. The correlations between combustion parameters and NOx- and N2O-emissions are inverse (Amand 1994, Leckner 1998).
In FBB, sulfur capture is easy to realize with limestone injection. Reaction speed and efficiency are highly dependent on the bed temperature. Variations in bed temperature decrease the efficiency of sulfur dioxide capture, increasing
SO2-emissions and consumption of limestone. The reaction uses oxygen, so conditions need to be oxidative. In reductive conditions gypsum, the end product of the sulfur reaction, releases already captured sulfur dioxide. If the oxygen concentration overall or locally decreases, sulfur emission increases. Therefore steady oxidative conditions are vital questions in SO2-control. These conditions need to be taken care of even when load or fuel qualities are transient (Markkula et al 2000).
2. Solutions
The first task in an application delivery project is a careful process study. The study is required because of the different
natures and states of plants. As a result of the study, solutions for the problems are defined. Good fuel and air controls are vital for optimal boiler operation. Any improvement in basic controls results directly in better combustion. The boiler is stabilized and running models are then implemented with coordinating controls. Combustion symmetry, combustion efficiency, CO–level, NOx и SO2 – emissions are controlled and optimized with fuzzy controllers.
Fuel Power and Fuel Caloric Value Compensation
In plants using various fuels the caloric value may vary a lot, and compensation for fuel quality is needed. In the application the boiler load and air controls are changed on a fuel power basis. Fuel power (MW) of the solid fuel is continuously calculated according to the boiler balance. The caloric value is the fuel power divided by fuel flow. The calculated caloric value is a good estimate of the fuel quality.
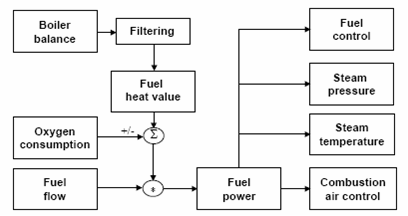
Figure 3 — Picture of total fuel power calculation
and main controls
Total Air Calculation and Air Distribution Model
Calculation of total combustion air is based on fuel power.
This means that the changes in fuel flow caused by a change in caloric value is compensated mathematically. The air/fuel power-ratio is always steadier than air/fuel flow-ratio.
Running models for air distribution; the recipes are implemented.
The filtered airflow is divided to air registers by
recipes. Recipes are tuned for different fuel mixes and operating
situations. The use of basic recipe unifies the operation
and makes optimization possible. Total combustion air
fuzzy control guarantees that the amount of combustion air
is always correct, so that the O2 – controller may operate with
full control range.
Symmetry
Symmetry means homogeneous combustion in the furnace.
Imbalance can be inferred from oxygen levels, flue gas and
steam temperatures. Symmetry fuzzy control balances the
fuel feed.
O2 /CO – Optimization
In FBB the oxygen concentration in the flue gas is controlled
by secondary airflow. Basic set points for airflows are derived
from the model and they vary by boiler load level.
O2/CO – fuzzy optimization corrects the oxygen level so that
the loss due to excess air and carbon monoxide is minimized.
The idea is to minimize the combustion air amount
as near to the limit of complete and incomplete combustion
as possible, considering the emission limits. The efficiency
increases and needed fan power decreases. The change in
excess air has effects also on furnace temperature, nitrogen
emissions, sulfur capture, but the effects are handled with
limitations to O2 – level. .
Bed and Furnace Temperature Controls
Bed temperature fuzzy control is used to keep the temperatures in the bed and in the freeboard within acceptable limits. The fuzzy controller controls ratios between flows of air and recirculated flue gas (if used). The control of temperatures in the bed and in the freeboard is important for efficient burning and sulfur capture with limestone. Safety limitation of the high temperatures in the bed (and cyclone) may also be needed.
NOx – Control
The NOx fuzzy control is based on O2 – level and airflow staging. The control functions together with the O2/CO optimization and the bed temperature control. In some cases NOx emission is controlled primarily with ammonia (SNR), then the aim is to save ammonia with air distribution and O2 – level.
SO2 – Control
The SO2 fuzzy control is based on control of limestone. The reaction conditions are the cross effects taken in to account in other fuzzy controls, so that the use of limestone is minimized. Reaction kinetic and efficiency depend on bed temperature and chemical composition. The fuzzy bed temperature controls the bed temperature; bed chemistry is affected by NOx – control.
3. The Structure of Fuzzy Control
СThe structure of fuzzy controllers used is similar and as simple as possible. Each controller inputs 1 – 5 measurements and has one control output [MISO]. These fuzzy controllers can be divided into three sub-functions: fuzzification, rule base and defuzzification.
In fuzzification the values of selected measurement are
classified to fuzzy sets. In practice this means a calculation of membership values to fuzzy sets. The fuzzy sets are
named illustratively, such as low, normal and high. To make the fuzzy control easy to understand, 3 – 5 triangular membership functions are used, even though the theory does not bound the number or shape of membership functions.
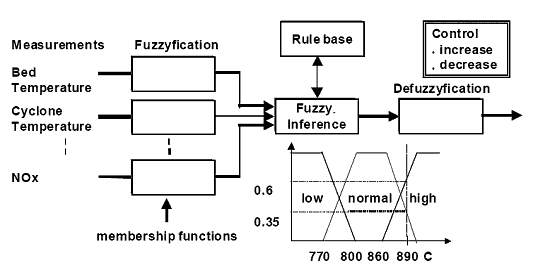
Figure 4 — Рrinciple picture of the fuzzy controlled structure
used in application
The rule-base consists of several if — then rules, which have
been defined through expertise or a fuzzy model. In the
application the reasoning is made by min–operator; the rule's
truth-value is the smallest of the conditions effecting the
rule. Rules have independent weighting value, which can be
understood also as fixed truth-value weighting. The weighting
values are thought as increments of control objects
scaled between –1 to 1. The sign tells if the object of the
control should be either increased or decreased.
In defuzzification the output is proportional to the sum of the
absolute value of the weights. The final increment xp is
simply calculated through all rules 1 to n,
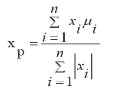
in which xi are the weighting values and μi are the truthvalues
of the rules.
Because of the chosen defuzzification method and construction of the fuzzy reasoning the rule base can be incomplete.
It is noteworthy that the rules, which are not needed, have 0
weight. So two rules, one for a positive increment and the
other for a negative increment realize a functional rule base.
This presumes that the rules are constructed so that the
only exceptional situations that need control are addressed.
If none of the rules is fired the situation is considered to be
OK. The coordinate controls take care of the systematic
relations.
4. Results
The advanced controls of FBB have provided good results.
The applications are in continuous use, the boilers are easier
to operate and emissions have decreased dramatically.
The benefits achieved by better management of combustion
are multi-faceted. The deviations and levels decrease, and
also the process is operated more smoothly. In some cases
steam production capacity can be increased. One clear
result is that the operation styles between shifts are standardized.
The first advanced control application was implemented to
the world's north-most CFB boiler in Rovaniemen Energia's
Suosiola power plant in 1997. The boiler is peat and park
fired and produces electricity and district heat. StoraEnso's
Imatra mills BFB fuzzy combustion management has been
used since 1997. The boiler was at the time of commissioning
the world's biggest FBB, the production capacity is 72
kg/s, 84 bar steam. The boiler utilizes the mill's bark, paper
waste and sludge. The third application was made to
StoraEnso's Anjala papermill's boiler, which was modernized,
from a grate boiler to a FBB in 1995. This boiler utilizesmill's own bark, sludge and some RDF (Refuse-Derived
Fuel).
In the Rovaniemi CFB emission levels were not any problem,
the main focus was in safety limitations of the furnace
temperatures and in increasing the automation level. In
Rovaniemi CFB the oxygen level has decreased by 0.5 %
and the NOx– level because of this. The bed and cyclone
temperatures are under control despite the load level or fuel
caloric value and the combustion is automatically controlled.
In BFB´s Imatra and Anjala decreasing CO and NOx emissions
were the main task. They came up because of varying
fuel and fast load changes. The automation level naturally
increased. In BFBs the amount of time that CO exceeds
emission limits has decreased by approximately 70 % per
annum, and the standard deviation has decreased to one
third. NOx – emission has dropped by 18 – 25 %. At the same
time efficiency has increased by means of decreased O2 concentration in the flue gas and stabilized bed temperature,
which ensures lower UBC [unburned coal]. In BFBs the
combustion is automatically controlled.
At Imatra BFB due to using the advanced control concept,
the time when CO exceeded the emission limit (CO over
250-ppm % of time) has in the long run decreased 67 % and
the standard deviation has dropped 70 %. Just after the
delivery of the control application the drop was about 77 %,
but after a while the level tends to rise. The nitrogen oxides
(NOx) emission has came down 18 % and standard deviation
of NOx– emission limit exceeding has dropped to one
fourth. Just after delivery the drop was about 29 %. O2– level
has decreased 5 % and its standard deviation 20 % and
CO–emissions have been in good control.
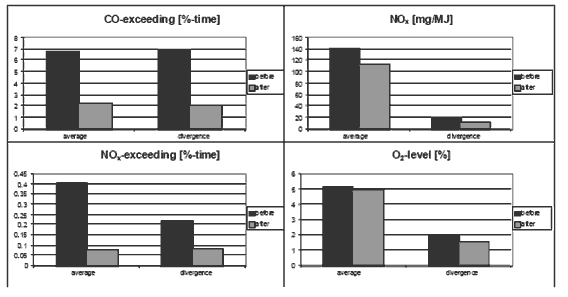
Figure 5 — Results from StoraEnso Imatra mill's BFB
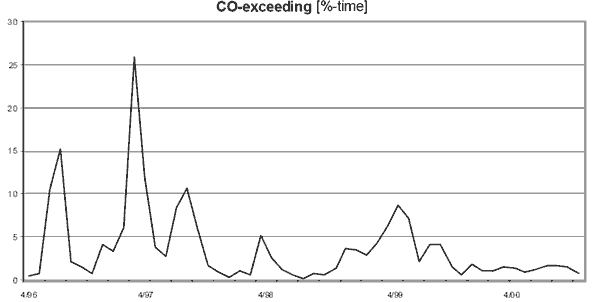
Figure 6 — Trend of the portion of the time CO exceeding
the emission limi
E.ON, UK Ltd. Kemsley could reach impressive results by
the use of upper level fuzzy controls. There a fluidized bed
boiler has to burn sludge and plastic waste. Fuzzy logic
could increase the waste incineration by 15% with equivalent
reduction in gas consumption. That means on one hand
more income and on the other hand additional savings.
(Crowhurst 2005).
Fortum Säteri Power Plant in Finland can report a similar
success story. There the fluidized bed boiler has to burn
peat, coal, sawdust, sludge, industrial waste, animal bonesand gas. (As supporting fuel) This mix is already a very
challenging task for the upper level control, because of high
variations in the fuel heating values. Nevertheless the result
can be highlighted. Fuzzy logic could decrease the supporting
gas consumption by 25%. In parallel the throughput of
waste was increased. The payback time for the fuzzy control
was about a month. (Jalkanen 2005).
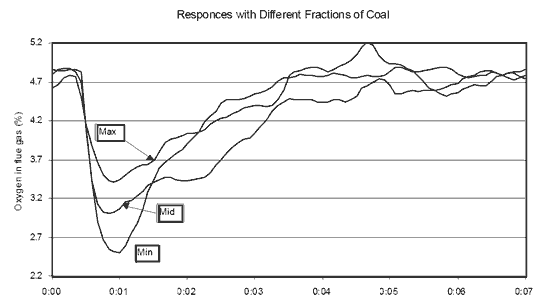
Figure 7 — Three impulse responses with different fractions
of fuel in a CFB
Conclusions
The increase of automation level can offer valuable financial
and environmental impacts in industrial and utility boilers. A
disturbance-free boiler is more reliable and more economical
to use. Combustion is more stable and environmental
emissions are radically reduced. We foresee tight process
control having even greater value as the processes grow
more complex and the environmental demands continue to
tighten up. Basic research is utilized to create new more
sophisticated applications to match future demands.
References
[1] AMAND, L.-E. (1994): Nitrous Oxide Emission from Circulating
Fluidized Bed Combustion. Dr. Thesis, Chalmers
University of Technology, Goteborg, Sweden.
[2] CRISWELL R. L. (1980): Control Strategies for Fluidized
Bed Combustion. InTech, January, pp. 37 – 43.
[3] CROWHURST R. (2005): Kemsley Reference Quote,
E.ON UK., Kemsley Mill, England.
[4] HUPA M. and MATINLINNA J. (1998): LIEKKI 2 Combustion
and Gasification Research Program. Technical
Review 1993 – 1998, vol.1. Rep. L98–3. Turku, Finland
(Internet: http://noon.abo.fi/Ook/Pages/Liekki.shtml).
[5] HUPA M. (2000): Studying the chemistry of combustion
processes. Energy in Finland, Helsinki.
[6] JORONEN, T. (2000): Paastojen vahentaminen
Automation avulla (Reducing emission by means of automation
(in Finnish)), Energia kongressi, Tampere, Finland.
[7] JALKANEN J. (2005): Fortum's Sateri Power Plant,
Metso Automation Customer Magazine Volume 1 2005,
Finland.
[8] KARPPANEN E. (2000): Advanced control of an industrial
Circulating fluidized bed boiler using fuzzy logic. Department
of Process and Environmental Engineering, University
of Oulu, Finland.
[9] KEYES, M. A. and KAYA, A. (1984): Applications of
Systems Engineering to Control Fluidized–Bed Boilers. Fluidized bed combustion and applied technology; The 1st int.
symp., Ed. Schwieger, R. G., pp. III–147–171.
[10] KOKKO, A. and NIEMELA, J. (2000): World's largest
biofuel fired CFB boiler for Alholmen's Kraft. Power-Gen
2000 Europe Conference Proceedings, Helsinki, Finland.
[11] KORTELA, U., IKONEN, E., KOTAJARVI, H. and
HEIKKINEN, P. (1994): Modeling, Simulation and Control of
Fluidized Bed Combustion Process. International Journal of
Power and Energy Systems, Vol. 14, No. 3.
[12] LECKNER, B. (1998): Fluidized Bed Combustion: Mixing
and Pollutant Limitation. Department of Energy Conversion,
Chalmers University of Technology. PII: S0360-
1285(97)00021–C, Goteborg, Sweden.
[13] MARKKULA, E., PYYKKO, J., JORONEN, T. and
NEUBERT, R. (2000): Optimierung und Regelung der Verbrennung
in Mullverbrennungsanlagen mit Hilfe von Fuzzy–Regelungen," (The Optimization and Control in Fluidized
Bed Boilers with help of Fuzzy control), VGB–Konferenz "Thermische Abfallverwertung 2000”, Essen, Germany.
[14] NYSTROM, P. (1983): Leijukerrospoltto ("Fluidized Bed
Combustion" (in Finnish)). Saatotekniikan prosessisovellukset
Seminaariesitelmat 1983, Ed. Kortela, U. and Joensuu,
J., Rep. 50, Helsinki University of Technology, Control Engineering
Laboratory.
[15] PYYKKO, J. and UDDFOLK, J. (1997): Leijukattilan
palamisen hallinta sumean logiikan avulla (Combustion
management of FBB with fuzzy control (in Finnish)),
Automaatiopaivat, Helsinki, Finland.
[16] RAATIKAINEN, T. (2000): Influence of Equipment Operation
and Performance Deterioration on Power Plant
Economy. Lappeenranta University of Technology, Department of Energy Technology.
[17] TUOVINEN, M. and KORTELA, U. (1988): Development
of New Control Strategies for Reduction of Nitrogen
and Sulphur Oxide Emission in Fluidized Bed Combustion,"
Energy Options for the year 2000, Contemporary Concepts
in Technology and Policy, Delaware, USA.
[18] U.S. Department of Energy (2000): Advanced Electric
Power Generation Fluidized–Bed Combustion; JEA Large–
Scales CFB Combustion Demonstration Project, Clean Coal
Technology, Program Update. |