1.Actuality of theme
A theme of my master's degree work is enough popular presently, in the period of economic crisis all new innovative technologies in industry are directed on the terms of minimum expense and maximal income. In the conditions of rising in the price of natural gas basic coke replacement technology there is insufflation of powdered coal.
2.Scientific meaningfulness of work
Search of alternative fuel replacement and also process of intensification of the blast-furnace melting, are the glanymi tasks of blast-furnace production. Efficiency of technology of the blast-furnace melting with insufflation in the furnace of the ground up unclose-burning anthracite coals is determined not so much their cost and khimsostavom, how many by the terms of complete gasification of powdered coal within the limits of oxidizing area of stove. Therefore except for subsieve of coals it is necessary to provide their even receipt to all of furmam stove. Replacement of coke a powdered coal in place of dear natural gas, one of main directions of increase efficiency of blast-furnace production determines.
Survey of research and developments
Ukraine:
Presently only on OAO "DMZ" technology is mastered with insufflation in the furnace of powdered coal (100-140 kg) on
1 ton of cast-iron, providing the decline of expense of coke to 400 kg/t cast-iron, increase of the productivity to 2100-2200 t/sutki.
The industrial setting of preparation and insufflation of powdered coal in the high furnaces of the Donetsk metallurgical factory is entered in
exploitation in 1980, and worked practically continuously to 1996. In 2002 on this utsnovke major repairs are executed
with the elements of reconstruction of mcode increasing power. On setting applied and usovershschenstvovana the most progressive of principle chart of arrangement
equipment, counted on individual and managed admission of powdered coal in every furmu of high furnace.
On the basis of new facilities of measuring and systems of automation well-to-do continuous serve of powdered coal in time and on furmam with an unevenness
5%, firesafety equipment.
World:
Presently most distribution was abroad got by a fluidizer preparation and pneumatic serve of powdered coal in a
blast-furnace stove, developed a firm Petrokarb . First the similar setting (without a device for drying of coal) was tested on a high furnace the volume of 465 m3 factory of firm Khanna Furnase Korp. in Buffalo (THE USA), and then the industrial setting is created in Stentone (England).
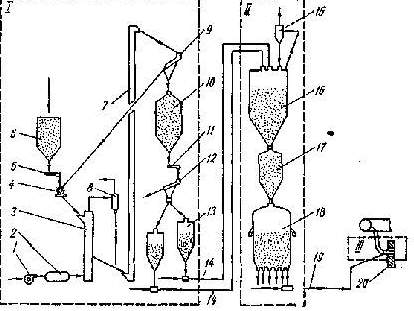
Picture 1. Chart of fluidizer preparation and pneumatic serve of powdered coal in the furnace of high furnace (firm Petrokarb, USA)
On a pic. 1 a fluidizer is rotined preparation and pneumatic serve of powdered coal in the furnace of high furnace. The features of this setting it is been individual serve of braize to furmam of high furnace from a reservoir-feeder 18, pneumatic method of dosage of braize, equal hydraulic resistances of routes, tricking into a braize to furmam. A distributively-dosage separation is equipped devices for weighing of braize in an intermediate reservoir 17, by the regulators of expense of air and braize on every furmu of high furnace. The expense of dust on every furmu is automatically regulated the change of expense of air and overfall of pressure between a reservoir and collector of hot-air of high furnace scope from 2,2 to 7,3 kg/mines.
For the even distributing of braize on furmam pyleprovody exposed to calibration and laboured for the identical expense of coal on every pipeline with a rejection to ±5% . Setting becomes more rational at the use of it for two high furnaces, located alongside. Thus every chamber-feeder works on one blast-furnace stove.
Simplicity of construction of the distributively-dosage setting and high reliability of its work was instrumental in wide distribution of this system abroad. The pneumatic system of firm Petrokarb got wide distribution in the USA and England. In France insufflation of coal is carried out on a chart, to approaching the chart of firm Petrokarb. In the USA and England blew and coal by a largeness to 3 mm and by humidity to 3%, and in France utillized a braize a largeness to 50 mkm.
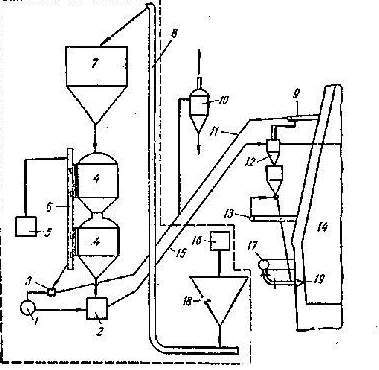
Picture 2. Chart of fluidizer preparation and pneumatic serve of braize in a blast-furnace stove (firm Babkok-vil'koko, USA)
On a pic. 2 a fluidizer is represented preparation and pneumatic serve of braize 6 blast-furnace stove, developed a firm Babkok-vil'koks (THE USA). It differs from the options of firm Petrokarb a compactness and structural implementation of separation of preparation of braize and distributively-dosage separation. Coal measuring less than 38 mm and by humidity 6% delivered in carriages, off-loaded in a lower bunker 18 raw coal from which by an elevator 8 rises in an overhead bunker 7 raw coal. From a bunker through cone pitateli and breech-blocks coal enters reservoirs of the closed system of serve of braize in a blast-furnace stove, preliminary podsushka of fuel is carried out in which. Coal from a lower reservoir 4 given in a crusher 2, where exposed to grinding down and final drying the heated air which is forced in a crusher 2 by a ventilator. The bunker of the prepared dust, perepusknaya chamber and reservoir-feeder of distributively-dosage separation, is transferable cyclones 12 with bunkers, placed near a high furnace. From the bunker of cyclone coal is continuously blown in furmu 19 by air, heated to 100°s, which is given from a collector 13. Setting is equipped a device, allowing evenly to distribute coal on furmam: the expense of fuel on separate furmam differs no more than on ±3%.
The improved setting of the same firm got industrial introduction in Ashlende (THE USA), where: a) a recirkulyacionnyy pipeline and all of transporting agent is removed from a cyclone 12 thrown out in an atmosphere, preliminary passing cleaning in wet skrubbere 10; b) as a transporting agent in place of heated to 100° From air rare gas is utillized (the table of contents of oxygen in him is supported in an amount 2 - 5%); c) the special distributive devices are applied are «distributors» - for the division of pyleugol'nogo stream on eight furm. One from two «distributors» distributes a braize on even, and drugoy- on odd furmy; d) there are devices for the automatic blowing out of pyleprovodov in the case of their corking and stopping of serve of braize coal in furmy at violation of work of injectors.
On setting of factory in Ashlende grinding down of coal is made to 75 mkm and insufflation of him in a hard-baked kind. Podsushka of coal reduces possibility of formation of corks in transport pipelines and allows to blow the greater amount of coal at the unchanging temperature of blowing. The well ground up and hard-baked coal less than wears down pipelines and, providing the receipt of homogeneous ugle-vozdushnoy of mixture, allows to attain by the special divizors the butyleobraznogo type of high exactness of distributing of coal on furmam . In 1972 at the plant in Ashlende an industrial fluidizer was built preparation and insufflation of braize in a blast-furnace stove «Amanda» an useful volume 2240 m3. Setting is counted on the production of 680 t of braize in days and replacement coal 30% coke. Other most foreign fluidizers insufflation of coal on principle little differ from the types described higher.
Conclusion
In the conditions of substantial price increase on natural gas with 2009 his replacement in high furnaces on a powdered coal in an amount to 200 kg on the ton of cast-iron will allow to decrease the expense of coke to 300 - 350 kg/t cast-iron, to promote the productivity and reduce expenses on smelting of cast-iron on 10-15% in spite of increase of capital costs on building of powdered coal separation.
Requirement to quality of charge and blowing:
- iron part must consist of steady-state and sifted from shallow faction (factions - 5,0 mm) gumboil and partly recovered pellet and agglomerate with the maximal relation of Fe/SiO2; that on each 100 kg of powdered coal on the ton of cast-iron the output of slag diminished on 32 kg, it is recommended to utillize metal-lodobavki to 200 kg/t cast-iron;
- a coke must have maximal values of hot durability - CSR (more than 62%), minimum values of reactionary ability - CRI (less than 28%) and fraction composition +(40.80) mm;
- coals must contain to 37% volatile and 12% ash and blown in stove in correlation: to 60% flammable (brands of Gramme), other - high-calorie (easily soiled And, ACE and T);
- a coal ash must have a temperature of melting more than 1400 °Ñ;
- correlation of thicknesses of layers rudy and must not exceed a coke 0,73;
- it is necessary to enrich blowing oxygen to the sizes 23 - 33% from the calculation of 0,5 - 0,8 m3 oxygen/kg of coal for maintenance of theoretical temperature within the limits of 2000 - 2300 °Ñ
Requirement to technology of the blast-furnace melting:
- for the improvement of gas-penetrability of post of charge and coke «totermana» it is recommended to work with the made light center of stove, that single serves of koks fraction +45 mm is loaded in a center, and workings serves, consisting of coke of faction +40 mm, «coke nut» and iron materials, - in peripheral and pro-mezhutochnuyu areas of koloshnika;
- for achievement of maximal degree of oxidization of carbon at furm it is necessary to give oxygen in the torch of burning of powdered coal, and to heat coal blast-furnace gas from additive stimulyatorov of burning;
- working is necessary on maximally possible pressure of gas in a stove;
- for the maintainance of volume of area of circulation at enriching of blowing oxygen it is necessary to rev up blowing diminishing of diameter of furm and increase them hight in stove;
- to develop the technological modes for indemnification of warmth in the furnace of stove at brief stops and subsequent blowing out of high furnaces;
- to equip high furnaces the necessary checking and management an expense and distributing of braize systems on furmam and technological parametrs of the blast-furnace melting.
In future perfection of technology of the use of powdered coal is planned as a decline of degree of grinding down, which makes 0,03 - 0,05 mm, both with the purpose of providing of plenitude of combustion and increases of reliability and automation of work of equipment, and also use of more high-quality coals.