

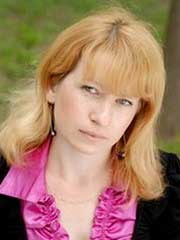
Tatiana Krivchenko
Faculty ecology and Chemical Technology
Speciality "Technology of Refractory Nonmetallic and Silicate Materials"
Fusible Glass
Scientific adviser: prof. Nicholas Belomerya
ABSTRACT
1. Relevance of the topic, objectives, goals
2. The technology of production
Contemporary glass, with its indispensable features and capabilities is one of the most promising materials of the new millennium. It has such features as transparency, hardness, heat resistance, resistance to corrosion by mineral acids and alkalis, as well as the ability to change these properties, it is easy to form the glass ,to choose any color for it. Combining all these features contemporary glass became an indispensable material of modern age.
One of its varieties is fusible glass with melting temperature below 500 °C. The main peculiarity of this type of glass is primarily its low melting temperature, rapid and uniform wetting while soldering of glass items, so as there are no residual stresses after soldering; high mechanical strength of the seam and also it has a consistent coefficient of thermal expansion with solders materials. These properties applied stipulated the field of application of such type of glass.
Fusible glass is a part of silicate paints. The advantages are that it is easily drifted to any painted surface, it dries fast, has no smell, the presence of flame retardant properties, chemical resistance and durability. On this basis, we can obtain a wide range of colors
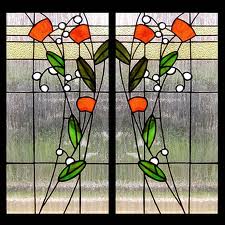
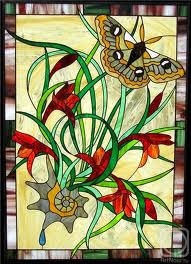
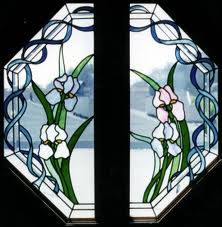
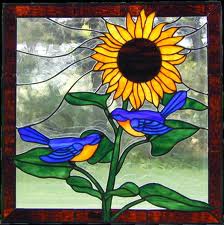
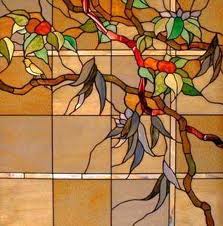
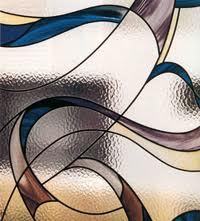
Picture 1.1 – The use of low-melting glass
Besides, silicate paints protect painted surfaces from damage caused by light, rain, snow, wind, temperature difference. Taking into account all these factors a further development and improvement of production technology is necessary for both fusible glass and the paint itself that is impossible to be carried out without proper modernization of equipment, increased requirements for professional skills of workers that is one of the main tasks of the industry nowadays.
Decorating glassware with printing through silk mesh using fusible enamels (the firing temperature 550-600 °C) has become widespread in many countries recently. It is widely recognized that indelible-color enamel label stamped on any product made of glass, contributes to the appearance and gives a bank or a bottle a beautiful look. Meanwhile, the process of cleaning the back of glassware becomes much easier; there is no necessity to soak labels and glue, printing labels and the like[12].
Fusible glass is used for sealing of semiconductor devices with the purpose to protect them against mechanical actions and chemical corrosion, moisture and impurities, making worth its electrical characteristics. In some cases, the use of glass is due to the restrictions imposed on the maximum temperature soldering. Obtaining such glasses makes it possible to use the devices in aggressive environments and at various external actions. All this should help improve the reliability and duration of operation of different devices, which use low-melting glass.
In the ceramic industry fusible glass became widely-used for the decoration of crock by painting a colored glaze, enamels and paints[11]. Application of ceramic paints on the surface of the product allows you to receive long-lasting, highly artistic designs. Unlike organic dyes, ceramic colors are highly resistant to light, durable, bright and juicy colors.
Fusible glass is not interchangeable in those cases when the temperature of sealing or soldering should not exceed 500-600 °C, in order to avoid disruption of the device. But the glass with low softening typically have weak structure, or reduced physical and chemical properties. Therefore, people try to create superior glass by introducing the various components that would stabilize the structure of glass and at the same time would not increase the softening point. Getting of these glasses will let to use the devices in hostile environments and at various external factors. All this should contribute to reliability and longevity of operation of different devices, in which use fusible glass is used.
Actuality:
On this account numerous researches are now conducted on разрабке of new compositions, which would answer modern requirements both from an ecological side and from economic and technological
Novelty of the work :
To get fusible glasses which would possess certain, set properties .
For achievement of this purpose next tasks were put :
1.On literary to choose systems information for the receipt of glasses
2.On the basis of these systems to get base compositions of glasses
3.To conduct practical researches of base compositions
4.To explore possibilities of their practical application.
Raw material is dried, milled and sifted. The raw material materials preliminary prepared, weighed out on the set recipe mix carefully.The process of batch preparation is automated. On the accuracy and thoroughness of the preparation of the initial components and their mixing depends on the quality of welded glass. Tolerances specified contents of the components in the mixture are set separately for each type of glass, and usually they do not exceed ± 0,5-1%. [4,5]. Mixing is carried out in batch mixers: disc, drum mixers. Humidity charge is recommended to maintain at the level of 4-5%. The charge must be uniform, ie the ratio of raw materials at each site, the charge should be treated equally and strictly meet the specified recipe. Clusters and breast of separate components in the mixture causes the formation of defects. The homogeneity of the glass batch is influenced by: grain composition of raw materials, their moisture content, weighing accuracy, quality and duration of mixing, method of transportation and storage [5].

Picture 2.1 –Technological scheme of production
Melting is carried out in rotary poty and skully kilns [12].
The peculiarity of the process of glass melting furnaces is such that the cooking takes place periodically, and has consistently produced the heating stove, batch loading, proper cooking of glass, lighting the mass, melting it and the development of glass. Glassmaking process consists of five stages.
The first stage – silicate. At this stage in the beginning of the Nag Revan in the mixture occur: evaporation, polymorphic transformation, thermal expansion of components. Well as between the mixture components begin chemical reactions.
Second Stage – Glass transition – characterized by the fact that by its end the mass becomes transparent, that is, it lacks not cooked particle charge, but it is riddled with lots of bubbles and striae, that is heterogeneous. Glass transition contributes to the mixing of the melt, which separates the silica film, and decrease the pressure over the melt, because this videlyayutsya gases and mixed melt.
The third stage – lighting – is characterized by the fact that by its completion-vis glass melt is released from the visible gas inclusions, and the fact that an equilibrium state between the glass mass (liquid phase) and the gases that remain in the glass melt itself (gas phase).
The fourth stage – the homogenization. Homogenization takes place simultaneously with the lighting. Heterogeneity of the glass may occur as a result not satisfactory mixing of the components or their bundles during transportation to the place of loading in glassmelting oven[5]. At a critical stage of homogenization is the destruction of the cellular structure of glass and its averaging. To cool the melt was poured from a ready pot (for cooking glass pot furnaces) in cold water to quickly cool it and simultaneously granulating. To this end, the melt must be sufficiently liquid to allow it to pour out a thin stream. During rapid cooling occurs and the refinement of the melt. In addition, for smaller grains, which are easily milled, it is necessary for pouring the melt in the tank with water to conduct an intensive stirring, and add cold water to prevent lumps.
According to the results of literature review on low-melting glass, we can say that the most appropriate systems for data acquisition systems are glasses PbO-SiO2-B2O3; and PbO-SiO2-B2O3-Na2O, which we were chosen to work for the synthesis of glasses of this type. Borosvintsovosilikatnye fusible glass is widely used as a marking enamels on electronic tubes for applying various kinds of drawings and inscriptions on the glass products, electronic converters for soldering glass shell with metal chuck, as well as other various types spayah glass to glass, glass metal, metal to metal.
To get the practical formulations of low-melting glass pre-calculated properties for a series of glass above the above systems with the view to meet the need, given the quantities (temperature coefficient of linear expansion, optical properties, surface tension)[7,8].
Theoretical calculation of properties of glasses was carried out by techniques Appena, Winkelmann and Schott, Dietzel.
To confirm the theoretical data conducted a series of case studies.
To obtain the data of glasses using the following raw materials: SiO2 injected with quartz sand, PbO – lead oxide (Pb+2), B2O3 – was introduced partly brown and boric acid, Na2O – introduced brown (Na2B4O7).
Chromophore materials(СоО) was introduced to painting glass in blue color.
Raw materials are finely ground, weighed according to their mass proportions in the mixture. After thorough mixing of all components of the synthesis of glasses were performed in ceramic crucibles, which were placed in an electric muffle furnace. Melting was carried out at temperatures of 1000-1050 °С. Willingness to glass was determined by stretching the glass yarns and the "cake". To facilitate the further grinding of glass to melt subjected frittovaniyu. Then, the resulting glass is finely ground in a porcelain mortar, until the passage through a sieve 0063. For the practical study of the properties of the glass powder obtained molded tablets. Were defined onset and end melting Tg and Tf, for the studied glasses, they are: for the first composition, glass transition temperature (Tg) 410-430 °C, for the second – 420-450 °С, and the third – 380-400 °С, temperatures that meet expected temperatures
TKLE compositions studied in the range from 75,35 до 91,50 (10-7 1/°С), density of 4415,8 до 5194,5(кг/м³). Refractive index from 1,69 до 1,71.
Thus, we chose a system based on which the results of calculation of the basic properties of glass defined base composition of low-melting glass practical determination confirmed the possibility of obtaining easily. glasses with a melting temperature lying in the temperature range 400-500 °С. In the future, based on these glasses will be more extensively investigated the possibility of their practical use for specific purposes.
- Пащенко А.А. Общая технология силикатов / А.А. Пащенко — Киев: Вища школа. 1983.— 408 с.
- Бутт Ю.М., Дудеров Г.Н. Общая технология силикатов. Учебник для техникумов. Изд. 3-е, перераб. и доп. М.: Стройиздат, 1976. — 600с.
- Сулименко Л.М. Общая технология силикатов / Л.М. Сулименко – М.: ИНФРА-М, 2004.- 336 с.
- Китайгородского И.И. Справочник по производству стекла / И.И. Китайгородского – М.: Государственное изд-во 1963.- 815с.
- Китайгородского И.И. Технология стекла / И.И.Китайгородского – Москва: Государственное изд-во, 1961. – 615 с.
- Волгина Ю.М. Теплотехническое оборудование стекольных заводов / Ю.М. Волгина — М.: Стройиздат 1982. — 276 с.
- Куколев Г.В., Пивень И.Я. Задачник по химии кремния и физической химии силикатов. Учебное пособие для вузов. М.: Высшая школа, 1971. — 240с.
- Матвеев М.А., Матвеев Г.М. Расчеты по химии и технологии стекла. Справочное пособие. М.: Изд-во литературы по строительству, 1972. — 239с.
- Ланцетти А.Г., Нестеренко М. Л. Изготовление художественного стекла – М.: изд-во Высшая школа, 1972. – 278 с.
- Гулоян Ю.А. Декоративная обработка стекла и стеклоизделий / Ю.А. Гулоян: 2-е изд., перераб. и доп. – М.: Высшая школа, 1989. – 223с.
- Визир В.А, Мартынов М. А. Керамические краски – К.: изд-во Техника, 1964. – 256 с.
- Петцольд А. Эмаль / А. Петцольд – М.: Высшая школа, 1958. – 512 с.
- Коцик И., Небрженский И., Фан-дерлик И. Окрашивание стекла – М.: Стройиздат, 1983. – 211с.
- Кутолин С.А., Нейч А.И. Физическая химия цветного стекла — М.: Стройиздат, 1988. — 296с.