ОПЫТ РАЗРАБОТКИ СИСТЕМ ОТСЕЧКИ ШЛАКА ДЛЯ СТАЛЕПЛАВИЛЬНЫХ АГРЕГАТОВ
Еронько С.П., ЦУПРУН А.Ю., БЕДАРЕВ С.А., Мечик С.В. Донецкий национальный технический университет, НПО «ДОНИКС»
Источник: ОАО «Черметинформация»
Бюлл. «Черная металлургия».- 2007.- № 9.- С. 81 – 87.
Предотвращение попадания большого количества конечного шлака в разливочный ковш во время слива в него стали из плавильного агрегата является важной технической задачей, от успешного решения которой во многом зависит эффективность мероприятий, связанных с рафинированием металла и его доводкой по химическому составу.
Предпочтительным способом активного влияния на объем шлакового расплава, поступающего в ковш во время выпуска металла, считается его отсечка. Достигаемая при этом степень отсечки шлака определяется техническими возможностями используемого механического оборудования, поэтому работы по его совершенствованию имеют достаточно весомую практическую значимость.
Донецким национальным техническим университетом совместно с НПО «ДОНИКС» выполнены работы по созданию и внедрению в производство высокоэффективных устройств для бесшлакового выпуска стали из плавильных печей и кислородных конвертеров [1].
Конструктивное исполнение и принцип действия оборудования для отсечки конечного шлака зависят от типа и геометрических параметров плавильного агрегата, гидродинамических особенностей процесса перелива из него металла в сталеразливочный ковш и наличия свободного места на рабочей площадке со стороны выпускного отверстия.
При эксплуатации электродуговых печей наиболее высокие показатели эффективности отсечки шлака достигаются в случае установки на них затворов, обеспечивающих управляемый донный выпуск стали без поворота корпуса печи. Такая технология выпуска позволяет сократить длительность плавки на 5-7 минут, уменьшить расходы электроэнергии на 6-10%, электродов на 10-13%, огнеупоров на 12-16% и шлакообразующих на 14-16% [2, 3].
Сопоставительный анализ достоинств и недостатков затворов, разработанных известными западноевропейскими фирмами для перекрытия сталевыпускного канала электродуговых печей, показал, что шиберные устройства, монтируемые на корпусе плавильного агрегата, должны отвечать следующим требованиям: надежность работы гидропривода в условиях длительного теплового воздействия; способность конструкции противостоять значительным усилиям, возникающим при перемещении огнеупорной плиты во время открытия канала печи; возможность быстрой замены комплекта огнеупоров без снятия затвора с корпуса плавильного агрегата.
Выполнение указанных требований обеспечивают за счет использования в приводах печных затворов гидроцилиндров двухстороннего действия с принудительным жидкостным охлаждением, применения жестких (коробчатой формы) корпусов затворов из жаропрочной стали и пружинного прижатия подвижного огнеупорного элемента, а также установки дополнительных (управляющих) гидроцилиндров для быстрого отвода скользящего блока от неподвижной обоймы при замене износившихся керамических изделий.
Необходимость разработки отечественной конструкции печного затвора, способного конкурировать с зарубежными аналогами, аргументирована достаточно высокой стоимостью импортных систем, поставляемых в виде полного комплекта, включающего сам затвор, огнеупорные изделия к нему, гидравлическое и электронное оборудование. Безаварийная работа этих затворов гарантируется лишь при использовании высококачественных керамических плит, специального инструмента, а также соответствующем уровне профессиональной подготовки обслуживающего персонала.
Система скользящего печного затвора (рис. 1), разработанная сотрудниками ДонНТУ и НПО «ДОНИКС» [4], имеет несколько принципиальных отличий от зарубежных аналогов, заключающихся в применении взамен поршневого двухплунжерного гидроцилиндра 2, передающего усилие подвижной обойме затвора 5 через рамку 3, установленную в направляющих 1 корпуса печи 4, а также в использовании в затворе балансирных прижимных элементов подвижной обоймы, снабженной роликовыми опорами. Такая схема прижатия огнеупорных плит не только обеспечивает надежную работу затвора даже при наличии клиновидности огнеупорных изделий, а и позволяет уменьшить износ поверхностей трения и нагрузку на привод.
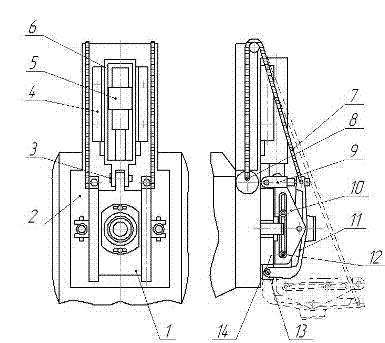
Рисунок 1 – Система скользящего печного затвора
Для обслуживания шибера без снятия его с корпуса печи и исключения необходимости применения специальных вспомогательных гидроцилиндров он снабжен уравновешивающим устройством, включающим контргруз, связанный двумя пластинчатыми цепями с подвижной обоймой. При замене изношенных огнеупорных изделий поворот подвижной обоймы затвора в горизонтальное положение и последующее возвращение ее в исходную позицию осуществляют вручную без приложения значительных усилий.
Опытно-промышленный образец скользящего затвора (фото на рис. 2) прошел опробование на лабораторной дуговой сталеплавильной печи, в ходе которого проверили работу его узлов в условиях длительного воздействия на них интенсивных тепловых нагрузок, а также практически определили продолжительность выполнения операции по замене отработанных огнеупоров, которая составила 18-20 мин. Полученные результаты учтены при выполнении рабочих проектов усовершенствованной системы скользящего затвора для печей различной производительности [5].
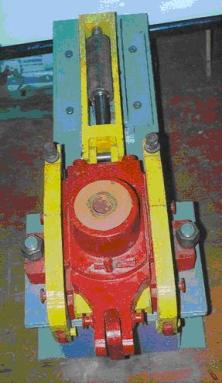
Рисунок 2 – Опытно-промышленный образец скользящего затвора для выпускного канала дуговой печи
Положительный опыт зарубежных компаний, использовавших на протяжении последних десяти лет технические разработки, обеспечивающие бесшлаковый выпуск стали из кислородного конвертера, свидетельствует о том, что отсечка конечного шлака способствует снижению степени рефосфорации, уменьшению угара ферросплавов и раскислителей, а также повышению срока службы футеровки разливочных ковшей. Устраняемые при этом потери, по оценкам специалистов, составляют один доллар США на тонну выплавляемой стали.
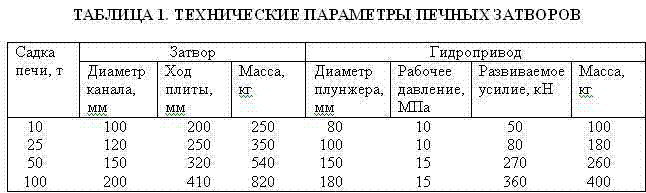
Существенного снижения количества шлакового расплава, попадающего в разливочный ковш во время выпуска стали из кислородного конвертера, удается достичь либо за счет установки на корпус плавильного агрегата скользящего затвора, перекрывающего его выпускной канал в момент появления частиц шлака в струе сливаемого металла, либо за счет применения специальных отсечных элементов поплавкового типа, выполненных из огнеупорного материала и помещаемых в жидкую ванну с помощью механического манипулятора для блокирования входного отверстия летки при подходе к ней шлакового слоя.
Целесообразность использования скользящих затворов для отсечки технологического шлака подтверждена зарубежными компаниями Salzgitter AG, Stopinc AG и RHI Refractories, совместно разработавшими и успешно эксплуатирующими в течение десяти лет систему шиберного затвора на 210-тонном кислородном конвертере. По свидетельству представителей этих компаний, одной из существенных проблем, с которой пришлось столкнуться по ходу освоения технологии бесшлакового выпуска стали, явился дефицит времени при выполнении операций по замене затвора с отработанными огнеупорными плитами в межплавочный период [9].
С целью снижения временных затрат, связанных с подготовкой и установкой шиберной системы на кислородный конвертер, было решено использовать поворотный затвор, у которого, благодаря вращательному движению нижней огнеупорной плиты, минимум в 3 раза увеличивается площадь ее рабочей поверхности, обеспечивающей запирание сталевыпускного канала (фото на рис.3), что позволяет во столько же раз повысить кратность применения керамической части до очередной ее замены.
При разработке данной конструкции, схематично представленной на рис.4, использованы технические решения, прошедшие промышленную проверку в ходе проведенных ранее испытаний опытного образца затвора поворотного типа. В сравнении с известными зарубежными аналогами рассматриваемая механическая система затвора имеет несколько существенных отличительных признаков: обеспечение самоустановки нижней огнеупорной плиты благодаря сферической поверхности подвижной металлической обоймы, защищенность зубьев приводной конической передачи от пыли и брызг жидкой стали из-за ее размещения внутри корпуса затвора, устранение быстрого износа поверхностей трения и уменьшение нагрузки на привод за счет установки вращающейся обоймы на комбинированный подшипник качения.
Электромеханический привод затвора, связанный посредством карданного вала с конической зубчатой передачей и закрепленный в нижней части корпуса конвертера, вынесен из зоны прямого лучистого теплообмена с зеркалом металла в ковше во время выпуска плавки [10].
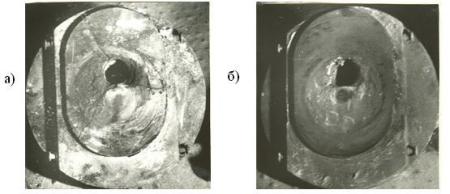
Рисунок 3 – Нижняя огнеупорная плита поворотного затвора:
а) магнезитовая бикерамическая плита;
б) муллито-корундовая плита
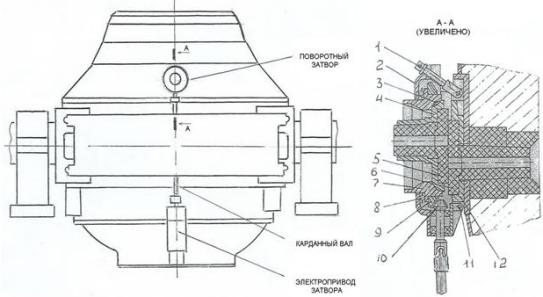
Рисунок 4 – Схема размещения поворотного затвора на корпусе конвертера
Изучение возможности применения манипуляторов с отсечными элементами для реализации бесшлакового выпуска в условиях кислородно-конвертерных цехов металлургических комбинатов Украины и России, построенных более 30 лет назад, показало, что их размещение на рабочих площадках перед конвертерами в большинстве случаев создаст помехи для машин, осуществляющих торкретирование футеровки плавильного агрегата или ее ломку в случае достижения предельного износа [11,12]. Поэтому механическая система манипулятора должна обеспечивать его расположение относительно кислородного конвертера, при котором бы обеспечивалось свободное место для маневрирования вспомогательных машин и механизмов, используемых при обслуживании и ремонте сталеплавильного агрегата.
Результаты тендеров, проведенных на ряде украинских комбинатов с целью поиска потенциальных поставщиков систем бесшлакового выпуска стали из кислородных конвертеров, свидетельствуют о том, что зарубежные образцы манипуляторов не в полной мере отвечают указанному требованию.
В связи с этим сотрудниками ДонНТУ и НПО "ДОНИКС" при разработке конструкций манипуляторов, адаптированных к производственным условиям отечественных металлургических предприятий, использованы методы физического и математического моделирования, а также САПР, позволившие имитировать функционирование проектируемых устройств в различных режимах и определить оптимальные соотношения линейных и угловых параметров их структурных элементов, при которых достигается компактность механической системы в нерабочем положении и нужная траектория движения в пространстве рабочего органа с учетом размеров горловины конвертера и расположения его выпускного канала в момент начала схода шлака в разливочный ковш [13].
У манипулятора, схематично показанного на рис. 5, перемещение отсечного элемента в трехмерном пространстве обеспечивается за счет механизмов вращательного движения. В его состав входит вертикальная колонна 1, установленная в неподвижных опорах, снабженная механизмом поворота 2 и консолью 3, с которой кинематически связана полая штанга 4. Эта штанга имеет возможность поворота в вертикальной и горизонтальной плоскостях, снабжена механизмом уравновешивания и несет на переднем конце отсечной элемент 5, удерживаемый подпружиненным фиксатором. К верхней неподвижной опоре колонны 1 с помощью пальца прикреплен один конец тяги 6, второй конец которой шарнирно связан с кронштейном 7. Благодаря особенностям кинематической схемы, этот кронштейн может поворачиваться на вертикальной оси в горизонтальной плоскости относительно консоли 3 на 90о при ее повороте вместе с колонной на угол 180о, что в конечном счете обеспечивает нужную траекторию движения отсечного элемента и его четкую ориентацию относительно оси сталевыпускного канала сталеплавильного агрегата. Данный манипулятор размещают на рабочей площадке сбоку кислородного конвертера со стороны выпуска стали. При этом манипулятор в исходном (нерабочем) положении не препятствует работе торкретмашин и механизмов для механизированного разрушения отработавшей футеровки. В конструкции манипулятора предусмотрена возможность изменения вылета полой штанги, что облегчает предварительную настройку механизма с целью обеспечения совмещения с продольной осью выпускного канала конвертера направляющего стержня отсечного элемента в момент его сброса в металлический расплав в заключительной стадии процесса выпуска плавки.
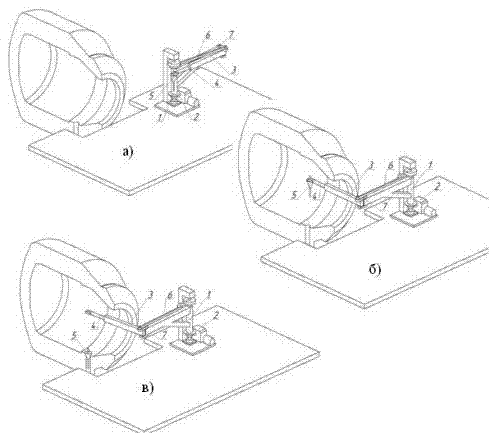
Рисунок 5 – Устройство манипулятора бокового типа и расположение его элементов в исходном (а), промежуточном (б) и конечном (в)
положениях
Фактором, ограничивающим использование данной механической системы, следует считать наличие в конвертерном цехе специального экрана для защиты от теплового излучения в случае его расположения сбоку от конвертера. В таких условиях рекомендуется применять конструкцию манипулятора, схема которого представлена на рис. 6. Главным его отличием от предыдущего является то, что у него нужная траектория перемещения отсечного элемента реализуется за счет последовательного действия механизмов вращательного и поступательного движения.
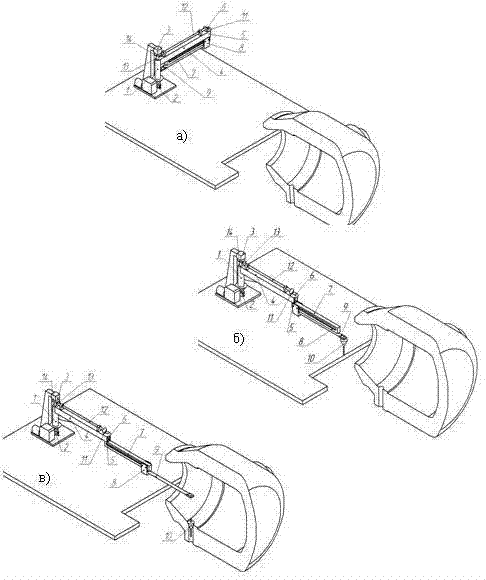
Рисунок 6 – Устройство манипулятора осевого типа и расположение его элементов в исходном (а), промежуточном (б) и конечном (в)
положениях
Этот манипулятор включает вертикальную колонну 1, установленную
с возможностью поворота в нижней 2 и верхней 3 неподвижных подшипниковых опорах и оснащенную консолью 4, на которой
смонтирован подшипниковый узел 5 с вертикальным валом 6. На
нижнем конце этого вала жестко закреплен кронштейн 7, имеющий две
продольные направляющие, в которых размещены ролики каретки 8, имеющей возможность перемещения относительно направляющих и несущей пустотелую штангу 9. На переднем конце штанги с помощью подпружиненного фиксатора закреплен отсечной элемент 10. Механизм поворота кронштейна 7 относительно консоли 4 включает коническую зубчатую пару 11 с передаточным числом равным 1, связывающую вертикальный вал 6 с задним концом горизонтального вала 12, на переднем конце которого жестко закреплено коническое зубчатое
колесо 13, имеющее возможность обкатывания по конической зубчатой шестерне 14. Эта шестерня жестко связана с неподвижной верхней опорой 3 вертикальной колонны 1. Причем отношение чисел зубьев неподвижной конической шестерни 14 и конического зубчатого колеса 13 составляет 2:1. Указанные соотношения конструктивных элементов конических передач позволяют автоматически обеспечить одновременно при повороте колонны с консолью на угол 90о из исходного положения относительный поворот кронштейна на 180о, в результате чего консоль и кронштейн будут сориентированы в линию и займут соосное положение с кислородным конвертером как показано на рис. 6 б. Последующую доставку отсечного элемента в зону расположения сталевыпускного канала конвертера (рис. 6 в) осуществляют перемещением каретки с полой штангой относительно кронштейна с помощью канатного привода (на рисунке условно не показан).
Благодаря отмеченным техническим решениям, защищенных патентом Украины [14], в разработанных конструкциях манипуляторов во время их функционирования составные элементы системы механически взаимосвязаны, что позволило в сравнении с известными аналогами сократить число приводов и исключить сложные электронные схемы контроля и автоматизации. Основные характеристики предложенных манипуляторов приведены в табл.2 [15]. Общие виды манипуляторов показаны на фото (рис.7).
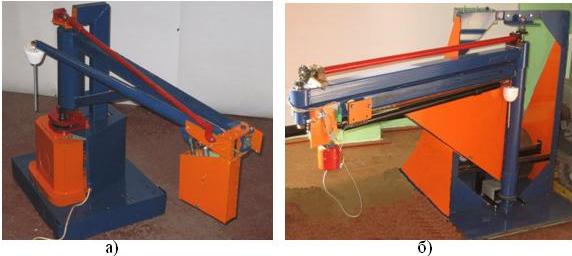
Рисунок 7 – Общие виды манипуляторов для отсечки конвертерного шлака:
а) манипулятор бокового типа МБ-1;
б) манипулятор осевого типа МО-1
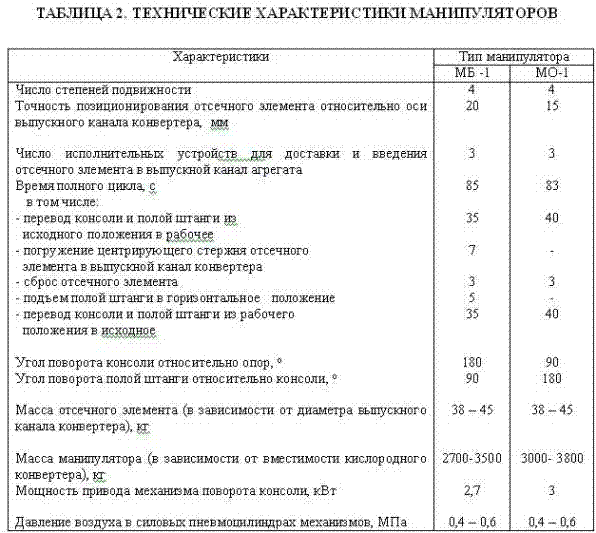
Учитывая то обстоятельство, что на ряде металлургических предприятий стран СНГ в течение определенного промежутка времени в эксплуатации будут находиться мартеновские печи, а выплавляемый в них металл должен проходить внепечную обработку, вопрос отсечки печного шлака для данного процесса производства стали также относится к проблематичным. Бесшлаковый выпуск стали из мартеновских печей обеспечивают чаще всего с помощью желобов, снабженных перегородками, задерживающими шлак, который по отводящему носку направляют в стоящую рядом с разливочным ковшом чашу.
На основании результатов, полученных в ходе проводившихся исследований на физических моделях, установлено, что приемлемая степень полноты отсечки шлака обеспечивается скиммерным желобом со стационарной перегородкой лишь при незначительных колебаниях (в пределах 5-7%) диаметра выпускного канала мартеновской печи от своего номинального значения, а этого в реальных условиях добиться невозможно [16].
В итоге поиска технического решения существующей проблемы
предложена конструкция печного желоба, схема которой показана на рис. 8.
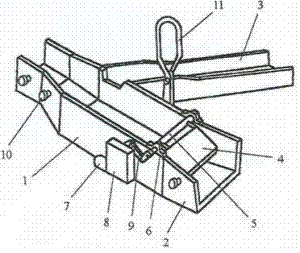
Рисунок 8 – Конструкция печного желоба
Корпус желоба включает приемную 1 и сливную 2 части, а также носок 3 для отвода шлака. Для задержки шлака желоб снабжен заслонкой 4, закрепленной на поперечно расположенном валу 5, установленном в подшипниковых опорах 6. Заслонка выполнена из огнеупорного материала и может поворачиваться с валом на угол 90о. Механизм поворота заслонки, смонтированный на наружной поверхности боковой стенки корпуса желоба, включает электродвигатель 7, редуктор 8 и кривошипно-рычажный механизм 9. Желоб имеет цапфы 10 для его наклона с целью слива остатков металла из приемной части в разливочный ковш, а также серьгу 11, предназначенную для выполнения краном транспортных операций.
В процессе выпуска стали, в момент появления печного шлака на ее поверхности в приемной части желоба заслонку с помощью электромеханического привода поворачивают и устанавливают под оптимальным углом к потоку расплава. Меняя угол положения заслонки в зависимости от массового расхода истекающего из печи металла, добиваются подъема уровня шлака в приемной части желоба до уровня поверхности днища сливного носка, по которому печной шлак отводится в шлаковую чашу.
Эффективность работы предложенного печного желоба в отличие от известных аналогов не зависит от состояния выпускного отверстия сталеплавильной печи. Кроме того, предусмотренный принудительный поворот заслонки в обоих направлениях при надлежащей мощности привода исключает возможность ее зависания даже при наличии металлической настыли на внутренней поверхности канала желоба
В соответствии с расчетной схемой (рис. 9), на основании предложенной методики [17], получили конструктивные параметры желобов мартеновских печей различной производительности, приведенные в табл. 3.
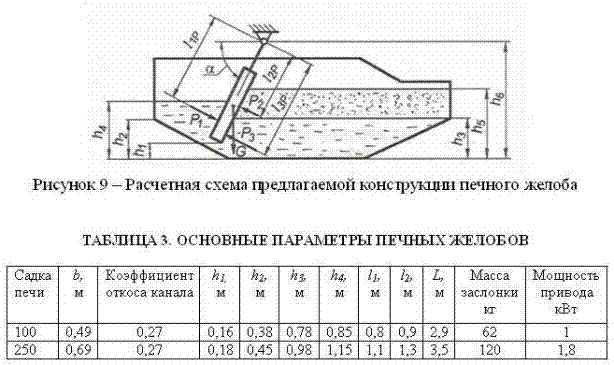
Таким образом, с использованием методов физического и математического моделирования и систем автоматического проектирования разработаны и изготовлены опытно-промышленные образцы новых устройств, позволяющих повысить эффективность технологических операций, связанных с отсечкой конечного шлака во время выпуска стали из плавильных агрегатов в разливочный ковш. Использование предложенных разработок будет способствовать улучшению технико-экономических показателей сталеплавильного производства и снижению зависимости отечественной металлургии от импортных поставок соответствующего оборудования
.
Литература
- Новое оборудование для отсечки шлака при выпуске стали из плавильных агрегатов / С.П. Еронько, А.Н. Смирнов, Д.П. Кукуй и др. // Металл и литье Украины.– 2002.– № 11-12.– С. 35-38.
- Carrier B., Tinnes B. The Metacon-taphole slidegate valve, areliable and economical
equipment for slag-free tapping of electric arc furnaces // Fachberichte Huttenpraxis
Metallweiterverarbeitung.- 1987.-25.- № 10.- S. 931 – 936.
- Short S.H. Sliding valves in new jobs // Iron and International.- 1984.- № 13.-
P. 180 – 181.
- Энкер Б., Пастер А., Швельбергер Й. / Новая стопорная система для шлака кислородно-конвертерного производства стали // Металлургическое производство и технологии металлургических процессов.– 2002.–№5.- С.12-20.
- Бесшлаковый выпуск плавки с помощью затвора выпускного отверстия
ТАР 120 при производстве чистой стали / У. Греф, А. Бергхофер,
Г. Амелер, М. Винкельманн // Сталь.- 2005.- № 7.- С. 51 – 54.
- Патент 75845. Украина. Скользящий затвор для выпускного канала сталеплавильного агрегата / С.П Еронько, А.Н. Смирнов, А.Ю. Цупрун и др. // Бюл. № 5. 2006 р.
- Еронько С.П. Совершенствование системы шиберного затвора для выпускного канала дуговой сталеплавильной печи // Металлургическая и горнорудная промышленность.- 2001.-№ 2.- С. 98-100.
- Вяткин Ю.Я., Шор В.И. Отделение металла от шлака при производстве конвертерной стали // Бюл.ЦНИИЧМ.– 1985.– №22.– С.29-35.1
- Снижение количества шлака в ковше при выпуске плавки из конвертера / Л.М. Учитель, И.Н. Зигало, Е.Н. Пустовой и др. // Сталь.– 1991.– №4.– С.27-28.
- Энкер Б., Пастер А., Швельбергер Й. Новая стопорная система для шлака кислородно-конвертерного производства стали // Металлургическое производство и технологии металлургических процессов.– 2002.– С.12-20.
- Бесшлаковый выпуск плавки с помощью затвора выпускного отверстия ТАР 120
при производстве чистой стали / У. Греф, А. Бергхофер, Г. Амелер, М. Винкельманн // Сталь.-2005.- № 7.- С. 51 – 54.
- Отечественные ковшовые затворы нового поколения / С.П. Еронько,
А.Н. Смирнов, А.Ю. Цупрун и др. // Металлургическая и горнорудная промышленность.- 2005.- № 1.- С.95-100.
- Совершенствования способа отсечки конвертерного шлака с помощью плавающих шаровых стопоров / А.Т. Бондаренко, Ю.И. Черевик, Н.А. Маслов и др. // Металлургическая и горнорудная промышленность.– 1992.– №2.– С.8-9.
- Еронько С. П., Смирнов А.Н., Кукуй Д.П. Разработка эффективных схем отсечки шлака при сливе металла из конвертера // Металлургическая и горнорудная промышленность.- 2003.- №8.- С. 33 – 37.
- Использование математического моделирования и САПР при разработке устройства устройства для отсечки конвертерного шлака / С.П. Еронько,
Е.В. Ошовская, В.В. Киселев и др. // Прогрессивные технологии и системы машиностроения: Сб.научных трудов.- Донецк: ДонГТУ, 2002.- № 23.- С. 52 – 56.
- . Патент 71681. Украина. Устройство для отсечки шлака при випуске стали из ковертера / С.П Еронько, А.Н. Смирнов, А.Ю. Цупрун и др. // Бюл. № 12. 2004 р.
- Новые устройства для реализации технологии бесшлакового выпуска стали из кислородного конвертера / С.П. Еронько, А.Н. Смирнов, С.А. Бедарев и др.// Процессы литья.- 2007.- № 4.- С.
- Оптимизация конструктивных параметров скиммерных печных желобов / С.П. Еронько, В.Я. Седуш, Ю.Г. Полонская и др. // Изв. вузов. Черная металлургия.- 2000.- № 7.- С. 71-73.
- Расчет конструктивных параметров печных желобов для бесшлакового выпуска стали / С.П. Еронько, В.Я. Седуш, Ю.Г. Полонская и др. // Изв. вузов. Черная металлургия.- 2000.- № 9.- С. 67-70.
|