ЭКСПЕРИМЕНТАЛЬНОЕ ИССЛЕДОВАНИЕ ЗАПИРАЮЩИХ СВОЙСТВ ГАЗОВОЙ СТРУИ
Гичёв Ю.А., Перцевой В.А.
Источник: Металлургическая теплотехника: Сборник научных работ Национальной металлургической академии Украины. – 2006. – 364 с. - С. 68-76
Введение
Данная работа связана с исследованием газодинамической отсечки шлака при выпуске плавки из сталеплавильных конвертеров с целью повышения эффективности отделения шлака. Качественное отделение шлака от стали обеспечивает успешное и экономное выполнение последующих операций, связанных с обработкой стали вне конвертера: дегазация, десульфурация, дефосфация, раскисление, легирование, вакуумирование и проч.
В числе большого разнообразия способов [1] отсечки шлака при выпуске стали из конвертеров выгодно выделяются газодинамические способы отсечки, суть которых заключается в воздействии на поток шлака в момент его появления в сталевыпускном отверстии струями газа, запирающими шлак внутри объема конвертера. По сравнению с другим способами газодинамическая отсечка отличается быстродействием, возможностью дистанционного управления, отсутствием быстроизнашивающихся элементов и компактностью оборудования.
Постановка задачи исследования
Избыточное давление газа в полости сталевыпускного отверстия при газодинамической отсечке должно уравновесить гидростатическое давление шлака и гидроудар, обусловленный резким торможением шлака при отсечке. В соответствии с этим первоочередной задачей экспериментальных исследований являлось определение возможности достижения необходимого для запирания шлака избыточного давления в полости сталевыпускного отверстия.
По физической сути для решения данной технической задачи экспериментальные исследования заключаются в изучении изменения давления турбулентной струи, втекающей в тупиковый канал, т.е. импактной струи. Тупиковый канал в эксперименте имитировал сталевыпускное отверстие, а днище тупикового канала – заторможенный в сталевыпускном отверстии шлак.
Известные результаты экспериментальных исследований по истечению газовой струи в тупиковый канал не удовлетворяют решению данной технической задачи. Например, в наиболее близких по сути к данной задаче работах [2 – 4] исследовалось истечение плоской турбулентной струи в тупики параболической и прямоугольной формы. В опытах варьировались значения абсолютного давления в полости канала и значения противодавления в отводных каналах. На всех типах экспериментальных моделей срез сопла совмещался со срезом тупикового канала. Специфика известных экспериментальных исследований позволяет определить закономерности распределения давления в тупиковом канале только для указанных условий.
В задачу данной работы входили разработка методики экспериментального исследования запирающих свойств турбулентной газовой струи и исследование запирающих свойств газовой струи при различных вариантах натекания струи на тупиковый канал, имитирующий сталевыпускное отверстие.
Методика и результаты исследований
Принципиальная схема экспериментальной установки для исследования запирающих свойств газовой струи представлена на рисунке 1.
Сжатый воздух от компрессора при эксперименте с одним запирающим соплом через форкамеру центрального потока поступает непосредственно к соплу. Кольцевой канал и форкамера кольцевого потока в экспериментальной установке предназначены для возможности размещения нескольких сопел перед моделью.
Модель, имитирующая сталевыпускное отверстие, выполнена в виде тупикового канала и размещена на координатнике, что позволяет изменять угол натекания струи на тупиковый канал. Для наблюдения и фиксации волновой структуры потока установка оборудована также теневым прибором.
Давления в воздухопроводе и в форкамерах фиксировались образцовыми манометрами, расположенными на пульте управления. Другие контролирующие приборы, а также задвижки, позволяющие изменять давление в форкамерах, и привод управления координатником выведены на пульт управления экспериментальной установкой.
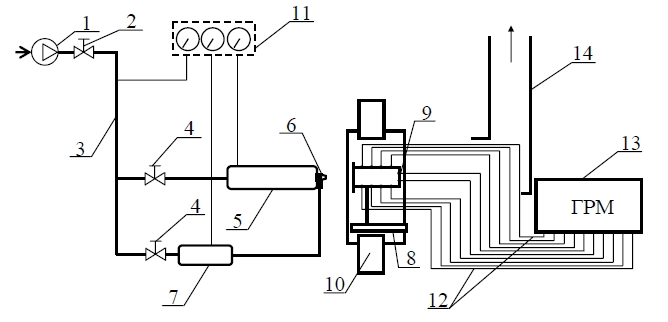
Рисунок 1 – Принципиальная схема экспериментальной установки для исследования запирающих свойств газовой струи:
1 - компрессор;
2 - запорная задвижка;
3 – воздухопровод высокого давления;
4 - регулирующая задвижка;
5 - форкамера центрального потока;
6 - сопло;
7 - форкамера кольцевого потока;
8 - координатник;
9 - модель тупикового канала;
10 - теневой прибор;
11 - щит образцовых манометров;
12 - пакет импульсных линий;
13 - групповой регистрирующий манометр (ГРМ);
14 - воздухоотвод
Суть эксперимента заключалась в измерении давления внутри тупикового канала при натекании на него газовой струи. Для этого модель тупикового канала оборудована дренажными отверстиями, к которым подведены импульсные трубки (линии).
Дренажные отверстия диаметром 0,8 мм выполнены по нормали к оси канала, кромки отверстий выведены над внутренней поверхностью канала (0,3 мм) и обращены к натекающему отоку для возможности измерения полного давления пограничного слоя втекающего в канал потока струи газа.
Пакет импульсных трубок (линий), от дренажных отверстий тупикового канала подведен к групповому регистрирующему манометру, который обеспечивает измерение давления, разрежения и разности давлений одновременно в десяти точках с печатанием показаний в заданные моменты времени.
Конструктивные параметры модели тупикового канала и сопла приняты в соответствии с геометрическим подобием устройству для газодинамической отсечки шлака, а параметры натекающей газовой струи изменялись в диапазоне ожидаемых при эксплуатации устройства значений давления.
В целом эксперимент по натеканию струи на тупиковый канал охватывал следующие значения:
а) диаметр выходного сечения сопла ( d0 ) – 0,016 м, диаметр тупикового канала ( Д ) – 0,04 и 0,06 м, глубина тупикового канала ( Н ) – 0,15 м;
б) относительное расстояние от сопла до оси тупикового канала (h'=h/d0) - 13, 15, 18, 22 и 26, взаимное расположение сопла и тупикового канала соосное (фронтальное натекание струи), т.е. угол ф между осью сопла и осью канала 0o , и наклонное (угол ф – 60o и 45o );
в) абсолютное давление газа перед соплом в форкамере центрального потока ( Рc ) – 0,5, 0,7, 0,9 и 1,1 МПа, число Маха на срезе сопла ( М0 ) – 1,0.
Экспериментальные исследования выполнены в два этапа.
На первом этапе исследовалось давление газа на внутреннюю поверхность тупикового канала при фронтальном натекании струи. Результаты измерений представлены на рисунке 2.
Сравнение давлений газовой струи на внутреннюю поверхность тупикового канала позволяет сделать следующие выводы:
а) При прочих одинаковых условиях давление на поверхность тупикового канала возрастает с увеличением давления перед соплом и с уменьшением расстояния между соплом и тупиковым каналом, что свидетельствует об адекватности результатов измерений;
б) При всех значениях давлений и расстояниях от сопла до тупикового канала давление струи на днище канала заметно выше по сравнению с давлением на боковую поверхность канала, что объясняется следующим.
Во-первых, реакция днища на втекающую в канал импактную струю соответствует полному давлению струи, приближающемуся к давлению ее торможения.
Во-вторых, давление на боковую поверхность канала не отражает в достаточной степени полное давление струи газа в связи с большой скоростью струи, турбулизацией струи вблизи кромок дренажных отверстий и параллельностью направления движения струи боковым стенкам канала.
В-третьих, давление втекающей в тупиковый канал струи на боковую поверхность канала, также как и в центральной части канала уравновешивается встречным, отраженным от днища, потоком газа, что приводит здесь к стабилизации давления.
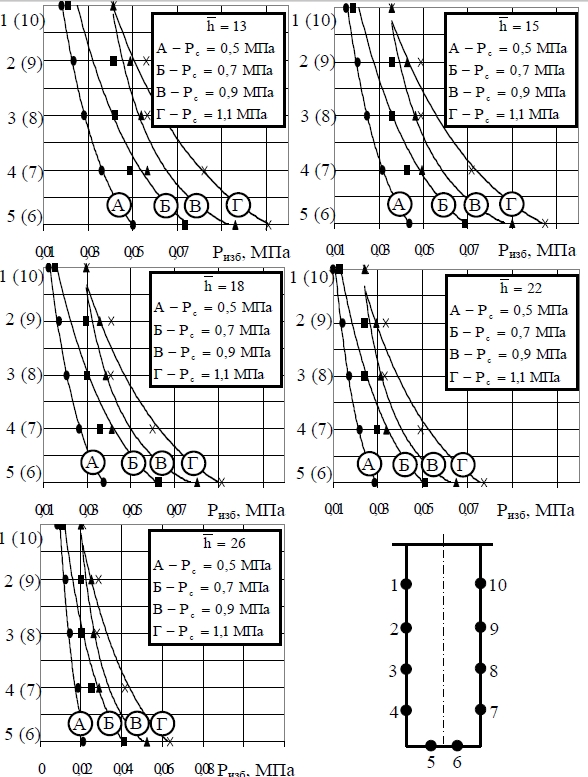
Рисунок 2 – Сравнение давлений газовой струи на внутреннюю поверхность тупикового канала (Ризб) при различных давлениях газа перед соплом (Рc) и различных расстояниях между соплом и тупиковым каналом ( h' ); 1…5 и 6…10 - точки измерения давления
Все это указывает на то, что принятая для отсечки шлака схема движения газа, т.е. непосредственное натекание струи газа на сталевыпускное отверстие, по своей физической сути вполне обеспечивает работоспособность устройства для газодинамической отсечки шлака, а именно, обеспечивает максимальное давление струи на днище канала и стабилизацию давления внутри канала.
Второй этап экспериментальных исследований включал измерения давления газа при боковом натекании струи на тупиковый канал. Результаты измерений представлены на рисунке 3.
Здесь также, как и при фронтальном натекании струи, результаты измерений указывают на их адекватность, т.е. давление на внутреннюю поверхность тупикового канала возрастает с увеличением давления газа перед соплом и уменьшением расстояния между соплом и тупиковым каналом.
В числе особенностей бокового натекания струи можно отметить следующие:
а) Выравнивание давления на внутреннюю поверхность тупикового канала, т.е. резко увеличенное давление на торец канала по сравнению с фронтальным натеканием здесь отсутствует;
б) При боковом натекании на тупиковый канал под углом 45° давление на боковые стенки канала в целом более высокое по сравнению с фронтальным натеканием, а при натекании под углом 30°, т.е. при угле ф между осью сопла и осью тупикового канала 60°, резко снижается.
Обобщение измерений давлений на внутреннюю поверхность тупикового канала выполнено путем усреднения давлений по поверхноcти. Сравнение средних давлений по поверхности при различных углах натекания струи на тупиковый канал представлено на рисунке 4, из которого следует, что изменение угла натекания струи в пределах 45 ? 90° дает диапазон давлений, позволяющий подобрать необходимые режимы эксплуатации устройства для газодинамической отсечки шлака.
При конструировании устройства для газодинамической отсечки шлака можно использовать уравнение регрессионного анализа результатов измерений, которое обобщает всю совокупность измерений избыточного давления
Ризб= - 0,344 + 0,581 * Рc0,1 - 0,028 * h-0,5 + 0,0017 * ф - 0,0032 * Д, МПа.
Вышеприведенное уравнение дает среднеквадратичное отклонение расчетной величины от экспериментальной R2 = 0,949 , что свидетельствует о высокой степени точности аппроксимации совокупности измеренных данных.
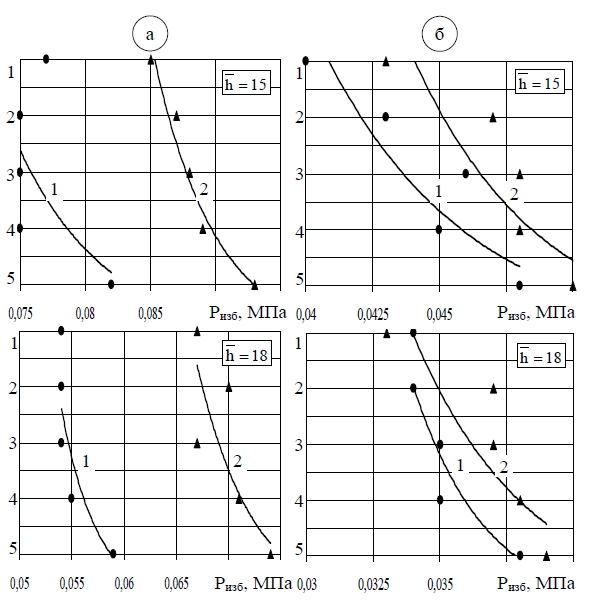
1 – давление перед соплом (Рc) – 0,9 МПа, 2 – 1,1 МПа. 1…5 – точки измерения давления.
Рисунок 3 – Изменение давления газовой струи на внутреннюю поверхность тупикового канала при боковом натекании струи:
(а – угол между осью сопла и осью тупикового канала ф = 45°;
б – ф = 60°)
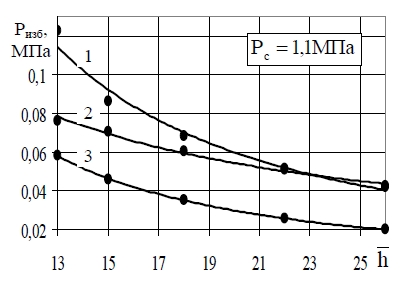
1 – угол натекания 45° ( ф = 45°); 2 – 90° ( ф =0°); 3 – 30° ( ф = 60°)
Рисунок 4 – Сравнение средних избыточных давлений газа внутри тупикового канала при различных углах натекания струи
Выводы
В результате экспериментальных исследований запирающих свойств газовой струи установлено, что принятая для отсечки шлака схема движения газа, т.е. непосредственное натекание струи газа на сталевыпускное отверстие, по своей физической сути вполне обеспечивает работоспособность устройства для газодинамической отсечки шлака, а именно, обеспечивает максимальное давление струи на днище канала и стабилизацию давления внутри канала. Изменение угла натекания струи в пределах 45 ? 90° вполне удовлетворяет условию запирания шлака в сталевыпускном отверстии.
Совокупность экспериментальных данных представлена в виде уравнения регрессии, которое можно использовать для конструирования устройств газодинамической отсечки шлака и разработки режимов их эксплуатации.
Литература
- 1. Гичёв Ю.А. Исследование газодинамической отсечки шлака при выпуске стали из конвертера // Металлургическая и горнорудная промышленность. – 2002. – № 7. – С. 170 – 173.
|