Зміст
Вступ. Обгрунтування актуальності
1 Мета та задачі роботи. Наукова новизна
2 Огляд існуючих досліджень і розробок
2.1 Важкооброблювані матеріали, що застосовуються в машинобудуванні
2.2 Теплофізичні особливості процесу різання розглянутих матеріалів
2.3 Роль СОТС при різанні важкооброблюваних матеріалів
2.4 Призначення режимів різання
3 Вибір технічних обмежень і параметрів оптимізації для математичної моделі
Вступ. Обгрунтування актуальності
Незважаючи на більш ніж 80-річний досвід виготовлення деталей з важкооброблюваних матеріалів, машинобудівні заводи відчувають значні труднощі при освоєнні технології обробки різанням заготовок з цих матеріалів. Зниження швидкостей різання приводить до зростання трудомісткості виготовлення виробів.
Спроба інтенсифікувати обробку різанням шляхом введення в зону різання додаткової енергії (різання з попереднім підігрівом зрізаного шару, обробка з введенням в зону різання ультразвукових коливань та ін.), а також замінити обробку різанням електрофізичної, електрохімічної не знайшли значного застосування. Традиційне різання металів є і найближчим часом буде залишатися основним способом виготовлення точних деталей машин, у тому числі з важкооброблюваних матеріалів.
Тому розробка обгрунтованих технологічних рекомендацій з вибору раціональних умов процесу різання і оптимальних конструкцій інструменту для операцій механічної обробки заготовок з широко застосовуються важкооброблюваних сталей і сплавів вельми актуальна. Найбільш досліджена токарна обробка важкооброблюваних металів, процес свердління даних матеріалів ще мало вивчений.
1 Мета та задачі роботи. Наукова новизна
Метою роботи є підвищення продуктивності обробки отворів і стійкості осьового інструменту при обробці важкооброблюваних матеріалів.
Для досягнення поставленої мети необхідно вирішити такі основні завдання:
- Розглянути класифікацію, фізико-хімічні та механічні властивості і область застосування важкооброблюваних матеріалів.
- Вивчити характер протікання теплових явищ при механічній обробці досліджуваних матеріалів.
- Вивчити методи підвищення продуктивності обробки за рахунок обгрунтованого вибору СОТС.
- Розглянути питання оптимізації режимів різання нержавіючих і жароміцних сталей і сплавів.
- Розробити математичну модель розрахунку оптимальних режимів свердління.
- Розробити технологічний процес виготовлення деталі з урахуванням особливостей обробки даного матеріалу.
Передбачувана наукова новизна роботи полягає у визначенні закономірності впливу СОТС на режими різання при свердлінні. Визначення оптимальних режимів різання, для заданих умов обробки при забезпеченні високої ефективності проникнення СОТС в зону різання і ефективного видалення стружки, дозволить підвищити продуктивність обробки, знизити її собівартість, а також підвищити якість оброблених отворів.
2 Огляд існуючих досліджень і розробок
2.1 Важкооброблювані матеріали, що застосовуються в машинобудуванні
У літературі питання про обробку важкооброблюваних матеріалів на сьогоднішній день розглянуто недостатньо широко, особливо це стосується обробки свердлінням. У той же час по обробці лезовий інструментом (зокрема гострінням) існує досить велика кількість всіляких досліджень, які широко застосовуються на практиці. В області обробки важкооброблюваних матеріалів широко відомі роботи Гуревича Я.Л., Подураева В.М., Єгорова І.С. та ін
Так, Гуревич Я.Л. призводить наступний опис властивостей важкооброблюваних матеріалів[1]:
1. Теплостійкі сталі володіють властивістю протистояти деформації і руйнуванню при механічному навантаженні в області температур нижче 550 °С, коли не виникає небезпеки інтенсивного окалиноутворення. p>
2. Корозійностійкі (нержавіючі сталі) мають стійкість проти електрохімічної корозії (атмосферної, грунтової, лужної, кислотної, сольовий, морський та ін.)
3. Жаростійкі (окаліностойкості) сталі та сплави мають стійкість проти хімічного руйнування поверхні в газових середовищах при температурах вище 550 ° С, при роботі в ненавантаженому або слабонавантажених стані.
4. Жароміцних сталей і сплавів мають здатність працювати в навантаженому стані при високих температурах протягом певного часу, маючи при цьому достатньої окаліностойкості.
Крім цього, до важкооброблюваних сталей можна віднести високоміцні загартовані й надміцні сталі, які представляють собою високолеговані і вуглецеві стали мартенситного класу твердістюHRC > 28 [2].
ЦНИИТМАШ розроблена класифікація для важкооброблюваних матеріалів за оброблюваності різанням:
I група.Стали, застосовувані для виготовлення впускних і випускних клапанів двигунів, лопаток і дисків турбін, що працюють при температурах до 500-600 °С. Оброблюваність таких сталей цілком задовільна, мало відрізняється від оброблюваності вуглецевих і малолегованої конструкційних сталей відповідної міцності.
II група.Стали, застосовувані в основному як нержавіючі сталі для виготовлення арматури, турбінних лопаток і дисків, що працюють при температурах до 530-580 °С (1X13, 2X13, 15Х12ВМФ, ЕІ961 та ін), хірургічного інструменту, шарикопідшипників (3X13, 4X13) і інших деталей з високою корозійною стійкістю. Механічна обробка цих сталей виробляється як після відпалу (1X13, 1Х17Н2, 2X13, 15Х12ВМФ та ін), так і після термічної обробки до високої міцності (3X13, 4X13, ЕІ961 та ін.) У отожженном стані ці сталі мають задовільну оброблюваність за швидкістю різання. Застосовувані швидкості різання приблизно в 1,5-2 рази нижче швидкостей різання, що застосовуються при обробці стали 45.
Оброблюваність за чистотою поверхні сталей II групи у відпаленому стані досить низька внаслідок налипання зрізується металу на робочі поверхні інструменту.
III група. Стали цієї групи отримали широке поширення як кислототривкі, нержавіючі і жароміцні матеріали. Вони застосовуються майже у всіх галузях промисловості для виготовлення деталей, працюючих в умовах, що викликають корозію металу або в умовах високих температур. У ряді жароміцних сталей аустенітного класу вони мають найкращу оброблюваність різанням: застосовувані швидкості різання при їх обробці приблизно в два рази нижче швидкостей різання, що застосовуються при обробці стали 45.
IV група. Складнолеговані сталі аустенітного класу, які йдуть на виготовлення дисків і лопаток газових турбін, кільцевих і кріпильних деталей, що працюють при температурах до 650 °С. Оброблюваність їх різанням у три-чотири рази нижче сталі 45.
V група. Жароміцні деформуються сплави на нікелевій і железонікелевих засадах. До них відносяться сплави типу 75-20-2,5 (ЕІ437, ЕІ437А, ЕІ437Б) і складнолеговані сплави ЕІ617, ЕІ445Р та ін
VI група. Ливарні сплави, застосовувані для виготовлення деталей, що працюють в умовах великих навантажень при температурі до 900-1000 °С. Для обробки таких сплавів у більшості випадків застосовують твердосплавний інструмент.
VII група. Сплави на титановій основі (ВТ14, ВТ15, ВТ3-1, ВТ22 та ін.).
До групи VIII віднесені високоміцні сталі (28Х3СНМФА, 30Х2ГСН2ВМ, 35Х5МСФА, 42Х2ГСНМ, Н18К9М5Т)[1].
2.2 Теплофізичні особливості процесу різання розглянутих матеріалів
Аналіз і регулювання теплових явищ при різанні жароміцних і корозійностійких сталей і сплавів надзвичайно важливі. Це обумовлюється двома особливостями:
- Сили різання важкооброблюваних металів значно перевищують сили різання при обробці звичайних конструкційних сталей, це призводить до підвищення величини питомої роботи і кількості тепла на одиницю зрізується обсягу металу;
- Теплопровідність важкооброблюваних матеріалів, як правило, істотно нижче теплопровідності звичайних конструкційних матеріалів. У результаті тепло не встигає відводитися із зони різання, що викликає сильне нагрівання ріжучої частини інструменту. Особливо це актуально для процесів обробки осьовим інструментом, коли останній працює у відносно замкнутому просторі [1].
Виходячи з цих особливостей, робота на рекомендованих для конструкційних сталей режимах різання призводить до швидкого досягнення допустимої температури різання, стійкість свердла різко падає, збільшення сил різання призводить до поломки інструменту. Тому, для важкооброблюваних матеріалів необхідно знижувати швидкості різання від 2 до 20 разів, що призводить до зниження продуктивності обробки. У зв'язку з цим, виникає питання про вишукування таких технологічних методів, які при високій міцності оброблюваних матеріалів забезпечили б досить високу продуктивність і стійкість різального інструмента. Застосування правильно підібраних мастильно-охолоджуючих рідин дозволяє дещо змінити теплові процеси[2].
Малюнок 2.1 являє зміни температури вздовж ріжучої кромки свердла. Максимальний нагрів відзначений на відстані 0,8-0,9 діаметру свердла від його осі. Потім темп зростання температури знижується. Такий розподіл температури вздовж ріжучої кромки є результатом спільного впливу підведення тепла до даного пункту контакту інструменту з деталлю і відведення його в масу деталі. В перерізах, розташованих близько до осі, температура, в міру віддалення точок від леза свердла падає.
![]() |
![]() |
Рис. 2.1 Графік зміни температури вздовж ріжучої кромки свердла. |
Температура на поперечній кромці становить 60-80% від максимального значення. Зі збільшенням подачі S і особливо зі збільшенням швидкості V темп наростання температури на периферійних ділянках виявляється вище, ніж у поперечної крайки, тут позначається вплив тепловідведення у серцевину свердла[3].
Високі температури в зоні обробки, що виникають із-за низької теплопровідності важкооброблюваних матеріалів, визначають необхідність дослідження температурних явищ у зоні різання. Для цих видів матеріалів становить інтерес подальший розвиток методики визначення температур в зоні різання при використанні СОТС та врахування їх впливу на вибір оптимальних режимів різання.
2.3 Роль СОТС при різанні важкооброблюваних матеріалів
Найбільш широко вживаними СОТС є мастильно-охолодні рідини (МОР). Застосування МОР при різанні металів збільшує стійкість різального інструмента, покращує якість обробленої поверхні і знижує силу різання. У даний час застосування технологічних середовищ вважають одним з основних способів поліпшення процесів різання важкооброблюваних матеріалів. Слід зазначити, що ефективність застосування технологічних середовищ визначається їх фізико-хімічним складом і способом подачі в зону різання.
Застосування МОР при обробці важкооброблюваних матеріалів дозволяє значно підвищити їх оброблюваність. Застосовувані в даний час у машинобудуванні змащувально-охолоджуючі рідини, газові середовища і тверді мастила мають ряд характерних впливів на оброблюваний матеріал і обробляє його інструмент, що визначають їх ефективність і область застосування. Серед основних виділяють наступні дії:
1. Охолоджуючу дію. Як вже говорилося, нержавіючі і жароміцні матеріали мають низьку теплопровідність і велика частина тепла, що утворюється в зоні різання, передається інструменту, знижуючи його стійкість. Подводимая в зону різання МОР забирає на себе значну частину утворюється тепла, скорочуючи тим самим відвід тепла в інструмент і підвищуючи його стійкість у кілька разів.
2. Мастильну дію. Ця дія виявляється в тому, що МОР, потрапляючи в зону контакту, утворює на контактних поверхнях адсорбційний мастильний шар. Цей шар призводить до зниження інтенсивності схоплювання тертьових поверхонь (тобто до зниження коефіцієнта тертя), внаслідок їх роз'єднання, обумовленого розклинюючих тиском рідини, і зносу контактуючих поверхонь.
3. Змиваючу дію. Це дія визначається здатністю застосовуваної МОР прискорити процес видалення стружки із зони різання. Ефективність цього впливу визначається видом МОР, величиною його витрат і тиску, а також розмірами і формою стружки.
4. Диспергуючу (руйнівну) дію. Воно проявляється в тому, що застосування при обробці деяких МОР полегшує процес руйнування оброблюваного матеріалу в місці контакту його з ріжучими крайками інструмента, а, отже, сприяє зменшенню роботи і сил різання в порівнянні з обробкою всуху[4].
2.4 Призначення режимів різання
Таблиці режимів різання при свердлінні заготовок з різних важкооброблюваних матеріалів складені по залежностях, встановленим у найбільш доцільних діапазонах швидкостей різання, для свердел з швидкорізальної сталі Р6М5К5 і для свердел з твердих сплавів. Рекомендовані подачі при свердлінні, швидкості різання, осьові сили, крутний момент і ефективні потужності наведені в таблицях [5].
Свердління з вібраціями заготовок з важкооброблюваних сплавів застосовують при обробці отворів діаметром 4-20мм і глибиною 5-20 діаметрів. Для цього розраховані режими різання з вібрацією.
Свердління з внутрішнім підведенням МОР рекомендується застосовувати для обробки отворів глибиною до 15 діаметрів свердла в заготовках з теплостійких сталей (групи I), хромистих корозійностійких сталей (групи II) і хромонікелевих корозійностійких сталей (групи III). При свердлінні із внутрішнім підведенням МОР забезпечується зниження температури різання, надійне відведення стружки, підвищення продуктивності обробки до 2 разів у порівнянні з охолодженням свердел поливом [5].
3 Вибір технічних обмежень і параметрів оптимізації для математичної моделі
Хоча є багато робіт, присвячених питанням застосування СОТС при обробці різанням, питання, пов'язані з використанням їх при обробці важкооброблюваних матеріалів, досліджені недостатньо.
Наявні роботи з оптимізації не охоплюють область обробки спеціальних марок нержавіючих, жароміцних і високоміцних сталей і сплавів. Існуючі рекомендації щодо вибору раціональних параметрів обробки цих матеріалів містять обмежені відомості про вплив функціональних властивостей СОТС на режими різання. Недостатньо інформації і за оцінкою досяжного рівня підвищення продуктивності при застосуванні різних СОТС, що ускладнює обгрунтування їх вибору в різних умовах обробки.
Тому виникає питання створення математичної моделі розрахунку режимів різання важкооброблюваних матеріалів з урахуванням температури різання та впливу СОТС.
Очевидно, що при обробці важкооброблюваних сталей і сплавів одним з перших технічних обмежень для оптимізації і регулювання процесу обробки треба використовувати температуру в зоні різання.
Обмеження 1. Допустима температура різання.
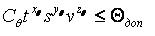
де t глибина різання, мм;
S подача, мм/об;
V швидкість різання, м / хв;
Cλ константа, що враховує умови різання;
xλ, yλ, zλ показники ступеня.
Обмеження 2. Ріжучі можливості інструменту.
Встановлює взаємозв'язок між швидкістю різання, зумовленої прийнятої стійкістю інструмента, глибиною різання, подачею, з одного боку, і швидкістю різання, визначається кінематикою верстата, з іншого боку.
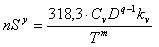
де Cv постійний коефіцієнт, що характеризує нормативні умови обробки;
D діаметр інструменту, мм;
Kv загальний поправочний коефіцієнт на швидкість різання;
T прийнята стійкість інструменту, хв;
m показник відносної стійкості;
q показник ступеня при D.
Обмеження 3,4,5,6. За кінематкою верстата (найменша та найбільша допустимі швидкості і подачі верстата).
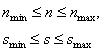
Обмеження 7. Потужність електродвигуна приводу головного руху верстата.
Встановлює взаємозв'язок між ефективною потужністю, що витрачається на процес різання, і потужністю електроприводу головного руху верстата.
Враховують, що крутний момент внаслідок виникають зусиль різання повинен бути менше крутного моменту, що розвивається верстатом по потужності встановленого на ньому електродвигуна, тобто
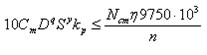
где Сm постійний коефіцієнт, що враховує вплив на зусилля різання оброблюваного матеріалу та інших умов обробки;
Кр загальний поправочний коефіцієнт, що враховує умови обробки;
q, y показники ступенів відповідно при D, S;
Nст потужність електродвигуна головного приводу верстата, кВт;
n коефіцієнт корисної дії передачі від електродвигуна головного приводу до інструменту.
Перетворюючи нерівність, отримуємо
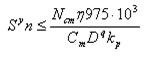
Обмеження 8. Задана продуктивність верстата.
Продуктивність верстата визначається з виразу

де R теоретична продуктивність верстата, шт / год;
Кз коефіцієнт завантаження верстата;
rR число деталей, одночасно оброблюваних на одній позиції.
Тривалість циклу роботи верстата Тц = 1/Q , або

Час циклу визначається за формулою

де То основний технологічний час, хв;
Тв.н допоміжний не перекриваємий час, хв.
Основне технологічне час визначається за формулою

де L довжина робочого ходу інструменту.
Враховуючи, що час циклу роботи верстата повинно бути більше часу циклу, що визначається сумою (Т0 + Тв.н) отримуємо таке нерівність
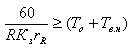
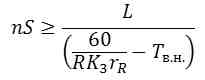
Обмеження 9. Міцність механізму подач верстата.
Зусилля подачі Ро, що діє на інструмент, не повинно перевищувати зусилля подачі верстата Pпод.ст..
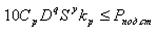
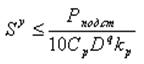
Обмеження 10. Міцність ріжучого інструменту.
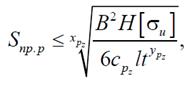
Обмеження 11. Жорсткість ріжучого інструменту.
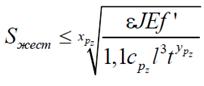
Критерієм оптимальності доцільно прийняти основне технологічне час (або величину, зворотну nS):

nS max
Вибрані технічні обмеження, що відображають з певною точністю фізичний процес різання в сукупності з критерієм оптимальності, дозволяють побудувати математичну модель процесу різання. Однак рішення задачі з оптимізації режимів різання з використанням степеневих залежностей для технічних обмежень представляє певні труднощі.
Одним з перших підходів до параметричної оптимізації технологічних процесів є метод лінійного програмування. В основі цього методу лежить побудова математичної моделі, що включає сукупність технічних обмежень і спрощений вид оцінної функції, приведених до лінійного вигляду логарифмування. Для вирішення цього завдання можуть бути використані методи перебору, симплексний та інші, а також графічний, наочно представляє математичну модель процесу різання[6].
Для використання методу лінійного програмування проводиться лінеаризації оціночної функції і обмежень шляхом логарифмування і приведення до вигляду:
a1iln(n) + a2iln(S) = biТобто отримуємо математичну модель процесу різання, виражену системою лінійних нерівностей, які обмежують область допустимих значень n і S.
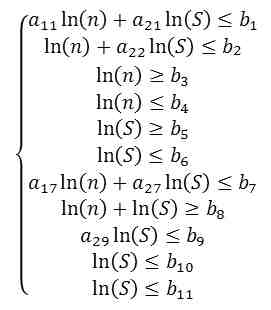
Графічна інтерпретація системи технічних обмежень представлена малюнком 3.1. У цьому випадку кожне технічне обмеження представляється граничної прямої, що визначає полуплоскость, де можливе існування рішень системи нерівностей. Номери прямих відповідають номерам вибраних обмежень. Граничні прямі, перетинаючись, утворюють багатокутник рішень, всередині якого будь-яка точка задовольняє всім без винятку нерівностям.
Рідким штрихуванням позначена область значень n і S, що допускаються кінематикою станка. Частим штрихуванням позначена область значень n і S, що задовольняє всім технічним обмеженням.
Допустима область рішень задачі лінійного програмування є опуклим багатокутником з кінцевим числом вершин. Це означає, що екстремум оціночної функції завжди є глобальним і досягається в одній з вершин такого багатокутника.
Тому знаходження режимів різання, що забезпечують максимальну продуктивність, буде проводиться спрямованим перебором вершин багатокутника і вибором максимального значення оціночної функції (точка nS на малюнку)[7].
![]() |
Рис. 3.1 Графічна інтерпретація системи технічних обмежень. |
Графік наочно ілюструє, що при свердлінні важкооброблюваних матеріалів оптимальні значення режимів різання визначаються температурними обмеженнями (лінія 1) і обмеженнями по заданій продуктивності верстата і міцності механізму подач верстата, заданими лініями 8 і 9.
Встановлено, що при свердлінні розглянутих матеріалів оптимальні значення режимів різання не залежать від обмежень по ріжучим можливостям інструменту (лінія 2), кінематичних обмежень верстата (3,4,5,6), потужності різання (7), міцності і жорсткості різального інструменту (10 , 11).
При використанні СОЖ обмеження по температурі (лінія 1) знімається, і тоді оптимальні значення як подачі, так і швидкості різання зростають, що призводить до підвищення продуктивності обробки.
При застосуванні різних МОР температурні обмеження (1) не враховуються і на перший план виходять обмеження по ріжучим можливостям інструменту (2) і по жорсткості різального інструменту (11), також враховуємо обмеження по заданій потужності верстата (8), за міцністю механізму подач верстата ( 9) і його кінематиці (5). При цьому спрощується вигляд математичної моделі процесу свердління і з'являється можливість розраховувати режими різання і аналітичним методом.
Висновок
У результаті побудови математичної моделі передбачається встановити вплив МОР на температуру різання та оптимальні за продуктивності режими різання при свердлінні виробів з важкооброблюваних матеріалів, а також оцінити можливість підвищення продуктивності їх обробки при використанні різних МОР, використовуючи метод лінійного програмування за критерієм максимальної продуктивності.
Література
1. Обработка резанием жаропрочных сталей, сплавов и тугоплавких металлов. А.М. Даниелян, П.И. Бобрик, Я.Л. Гуревич, И.С. Егоров /Под. ред. Гуревича Я.Л. М. «Машиностроение», 1965. 308с.
2. Подураев В.Н. Резание труднообрабатываемых материалов. М., «Высш. школа», 1974. 587с.
3. Пестрецов С.И. Компьютерное моделирование и оптимизация процессов резания: учеб. пособие / С.И. Пестрецов Тамбов: ТГТУ, 2009 104 с.
4. Латышев В.Н. Повышение эффективности СОЖ. М., «Машиностроение», 1975 88 с.
5. Режимы резания труднообрабатываемых материалов: Справочник / Я.Л. Гуревич, М.В. Горохов, В.И. Захаров и др. 2-е изд., перераб. и доп. М.: «Машиностроение» , 1986 240с.
6. Оптимизация технологических процессов механической обработки / Рыжов Э.В., Аверченков В.И.; Отв. ред. Гавриш А.П.; АН УССР. Ин-т сверхтвердых материалов. Киев: «Наук. думка», 1989. 192 с.
7. Исследование и разработка методики расчета оптимальных параметров режимов резания на токарных станках с ЧПУ. Б. М. Бржозовский, А. Л. Плотников, А. О. Таубе. [Электронный ресурс]. Режим доступа: http://users.kpi.kharkov.ua/cutting/articles/000005/000005.html
8. Макаров А.Д. Оптимизация процессов резания. М., «Машиностроение», 1976 278 с.
9. Лакирев С. Г. Обработка отверстий: Справочник. М.: «Машиностроение», 1984. 208 с.
10. Якобс, Г.Ю. Оптимизация резания. Параметризация способов обработки резанием с использованием технологической оптимизации / Г.Ю. Якобс, Э. Якоб, Д. Кохан. М.: «Машиностроение», 1981. 279 с.
Зауваження! При написанні даного реферату магістерська робота ще не завершена. Остаточне завершення: грудень 2011 р. Повний текст роботи та матеріали по темі можуть бути отримані у автора або його керівника після зазначеної дати.
Вгору