This paper describes research and development into automatic grab ship unloaders, automatic loading machines, and automatic bucket stackers and reclaimers for bulk cargo in the Port of Shanghai, which have been integrated with a multitude of advanced technologies, such as long-range detection, computer networks, automatic control, and intelligent decision-making etc. With the above integration, efficient automatic bulk loading and unloading can be implemented in the port, along with achieving management and control integration of automated operations creatively, and establishing a solid foundation for building fully automatic bulk cargo terminals.
Background
With the development of economic globalisation, the capacity of bulk cargo, especially ore and coal, is growing. In 2007, dry bulk throughput in Chinese ports was 3,565 billion tonnes, an increase of 13.5 per cent in 2006. It is expected that in the next three years, throughput growth of dry bulk cargo will reach 13 per cent. The proportion of dry bulk cargo throughput at the Port of Shanghai is more than 40 per cent and still rising. Presently, both at home and abroad, most bulk cargo is manually handled by handling equipment and operational efficiency and security is entirely dependent on the driver's proficiency. Some terminal areas are also equipped with semi-automatic controlled handling equipment, that is, the main parameters are controlled manually, so that higher efficiency and reliability can be achieved. In order to adapt to today's trends of providing professional, large-scale and high-performance handling equipment, most countries in the world are vigorously studying the applications of information technology and automated and intelligent technology in order to build or upgrade their bulk cargo terminals. Development of new types of bulk cargo handling and distribution equipment, as well as bulk cargo operation management and control systems, will enhance a port's core competitiveness.
This paper introduces bulk grab ship unloaders and automatic and fully automatic bulk loading bucket wheel stacker-reclaimers, jointly developed by Shanghai Port, Shanghai Port Machinery Plant, ABB (China) and Shanghai Jiao Tong University. The study involves a number of key technologies, such as the outline of the longdistance materials detection, computer network, automatic control, intelligent decision making, grab anti-sway, path planning, video surveillance, and remote monitoring equipment, all implemented in order to achieve a high-performance when handling automatically, stacking and remote monitoring bulk cargo.
Facilities
Automatic grab ship unloaders for bulk cargo
Unloaders operate in two existing ways: manual and semiautomatic mode. Efficient manual shipment is entirely dependent on the driver's proficiency, which can easily alter the swinging motion of the grab, thus human factors can result in instability in the efficiency of operations. The semi-automatic mode has two shortcomings: on the one hand, drivers must constantly manually set and update operating parameters, as operations have poor ability to adapt, and there is a big security risk. In particular, due to hold materials, as well as changes in the fluctuation of the tide, the hull is susceptible to floating or tilting, thus using a semi automatic mode to unload ships runs the risk of the grab colliding with the ship. On the other hand, owing to the irregular distribution of bulk materials inside the hold, the driver must still manually set the return point on the top of the hold for the next cycle when starting the automatic circle, in order to achieve optimum unloading and avoid grasping air or grasping a small bucket etc. For the above reasons, both automatic operation and manual adjustment are both difficult to coordinate. On the basis of existing manual and semi automatic functions, automatic grab ship unloaders for bulk cargo (Figure 1) are equipped with hold and materials scanning system (here referred to as a TPS), to automatically detect hold location and distribution, replacing the driver's need to manual setup operations, and br inging into realisation, continuous ship unloading, and improvement in operational efficiency and performance safety. In the unloader's automation programme, the use of a TPS sensor has three main functions: detecting cabin location, materials distribution and return location. The TPS is installed at the front of the cab platform.
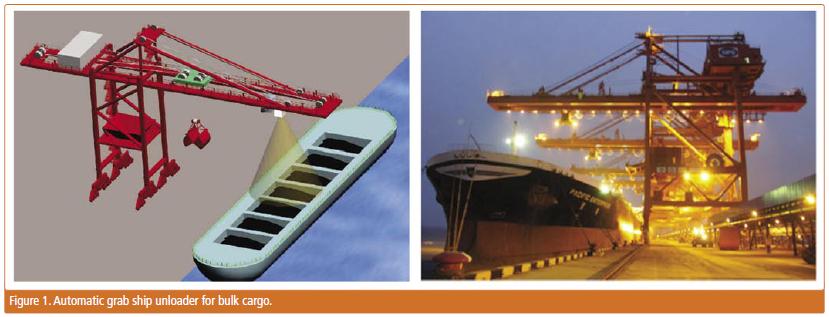
The automatic unloader uses laser ranging detection technology to achieve automatic detection and identification of a number of objectives including ship location, hold location, bilge and hatch and the height of the hold, as well as the types and distribution of materials.
Hold location and the height of the bilge and hatch determine the regional border of shipment operations. Whether the regional operating area is appropriate or not is directly related to the security of shipment process. If the cabin location and the height of bilge and hatch are not correct, grab collision will easily happen. On the other hand, taking security into consideration, the operations area needs to be reduced, but this will also reduce shipment efficiency. Discharging strategy is based on materials distribution in the hold. At the same time, the system needs to determine grab position according to the height of the materials. An incorrect height determination will lead to the phenomenon of a grab being less than full, the air grasping and buried in fighting, which will reduce operating efficiency, operational disruption and even cause accidents. During unloading, ship positioning will change with water and wind, ship height will change with the tidal fluctuations, the materials distribution inside the ship will change with the shipment operations, the movement and the collapse of bulk cargo will lead to changes in materials distribution inside the hold. Shipping location and materials distribution have no fixed rules. The return point of the grab depends on the accuracy of the automatic identification system.
Automatic loading machines for bulk cargo
Shipping operations are currently using manual methods, with the scope of shipping operations and the various shipping sports bodies being controlled by the driver through the console. At present, the main problem in the loading process is that the loading machine's cabin is found at the top of the boom, blocking the driver's sight so that he cannot observe the slip off of the tube and the materials distribution at the bottom of the boom. From this vantage point it is difficult to observe the tilt of the hull and difficult to accurately position the tube slide. Automatic loading machines increase hold detection, traffic detection, materials detection and video surveillance functions, along with providing real-time monitoring shipping operations and control procedures to ensure smooth and uniform loading operations are completed. Automatic loading machines have the function of hold detection, materials flow detection, materials detection and video surveillance functions, which can face different types of ships and material surfaces during continuous operations, planning shipment paths automatically and effectively, as well as reducing the dust, noise and vibration at material transfer points, ensure smooth loading operation. Automatic loading machines use sensors to detect the relative location between the hold and the loading machines (Figure 2), as well as the actual distribution of materials inside the hold. These are necessary conditions for accurate positioning, achieving uniform loading, and increasing the operating efficiency. According to the process of loading and the structural features of loading machines, automatic loading systems use two vertical laser radars as detection equipment to detect, identify and deal with the operations hold and reactor, to load automatically by controlling the movement of wandering extinguishers and large carts.
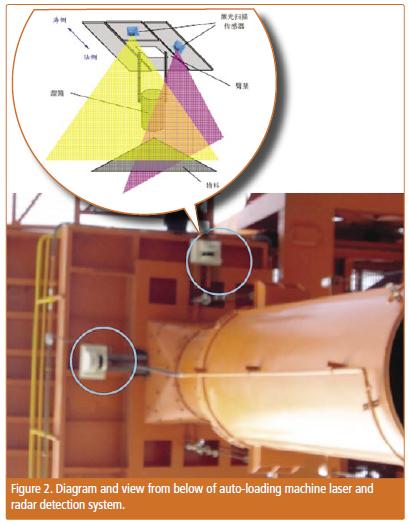