Технологическое обоснование метода создания высокоточных рабочих колес с минимизацией весового показателя и дебаланса обеспечиваемого специализированной оснасткой, проектирование механических и контрольно-измерительных операций на этапах изготовления модулей, на которые разделено колесо [1].
Экспериментальное внедрение технологии в производство рабочих колес в подпиточные центробежные насосы СНТ 01.510 маслостанции СНТ 40 осуществленное на Новгородском машиностроительном заводе показало нижеследующее:
1. Технологически более сложные стальные сварные колеса, изготовленные по модульному методу, конструктивно-параметрически предсказуемы, нежели чем литые чугунные: весовой разброс у партии рабочих колес из 8 штук не превышал 6ч4 грамм (при диаметре колеса Ш162 мм, диаметре вала Ш28Н9, диаметре ступицы Ш45мм). Причем вес колес в чугунном исполнении, выпускаемых по заводской технологии колеблется в пределах 1.5ч1.9 кг. Разброс составляет от 300 до 400 грамм на колесо даже в пределах одной партии литья. Вес рабочих колес стального сварного исполнения составил 1618ч1500 грамм и при числе оборотов вала насоса nэл=2850 об/мин при серийной сборке (подпиточный центробежный насос СНТ 01.510 двухступенчатый) наблюдается большие вибросмещения и виброскорости.
Для двухмассовой системы, имеющей две симметричные опоры, считаем отсутствующим эксцентриситет масс (перепад по массе равномерно распределен по диску).
Полученные расчетные параметры показывают, что при достаточно близких по весу колес (в данном случае для двухмассовой системы, какой является насос СНТ 01.510) частота колебаний системы лежит в пределах 180ч200 1/сек, при разнице в 0.250ч0.300 кг частота колебаний становиться равной 55ч64 1/сек, то есть практически приближается к вынужденной частоты колебаний, в данном случае для насосов СНТ 01.520 это частота равна "Омега"=(47ч50)1/сек.
Статическая балансировка, оговоренная техническими условиями для рабочих колес центробежных насосов, позволяет установить (ликвидировать) дисбаланс масс относительно геометрической оси вращения детали, причем с погрешностью, зачастую соизмеряемой с погрешностью по перепаду масс между деталями.
Полученные модульной технологией рабочие колеса были установлены в насосы 4х маслостанций ( зав. №573, №574, №575, №576), испытаны на заводском стенде и отправлены на шахты для промышленных испытаний.
На заводском стенде для статической балансировки были проведены испытания рабочих колес, взвешивание и селекция их по массе. Имеющаяся дисбалансная масса во всех случаях не превышает 2ч6 грамм. Съем дисбалансной массы производился по коренному диску на диаметре Ш140 мм при соблюдении технологических условиях допустимого дисбаланса 0.006 мм при рабочем диаметре фрезы Ш16 мм. Полученные и замерянные параметры приведены в таблице 1. Причем замеры твердостей поверхностей дисков (до 56 HRC) повлекут за собой использование для корректировки масс использование твердосплавных фрез.
На заводском стенде СИИ 510 насосы были подвержены динамическим испытаниям: замерам рабочих характеристик и вибропараметров, в том числе вибросмещений и виброскоростей. Результаты измерений и расчетов параметров насосов приведены в таблице №2.
Замеры вибропараметров агрегатов производились виброметром ПИ-19 и пьезоакселерометром ДН-3 входящих в АСИВ (Агрегатированная Система Измерения Вибраций) с нормированной погрешностью измерения среднеквадратичного значения (СКЗ) виброскорости - класс точности 15 и размаха вибросмещения - класс точности 20 по ГОСТ 16826-17.
Согласно полученным рабочим характеристикам и вибропараметрам понятно, что во всех направлениях измерения уровни виброскорости насосов со стальными колесами в 2 и менее раз меньше уровней виброскорости насоса с чугунными колесами, что положительно сказывается на эксплуатационной надежности.
Это объясняется строгой адекватностью объемов, перекачиваемых через каждую межлопаточную зону колеса, так и колес входящих в многосекционную машину.
Также уровень поперечных вибросмещений в многосекционных машинах связан весовым перепадом между колесами. Расчеты и замеры вибропараметров показали, что весовой перепад между колесами должен быть сведен до минимума. Литье, даже высокотехнологичное, не всегда может обеспечить разницу в весе от 2 до 6 грамм между колесами в многосекционной машине.
Технологически это обеспечивается обработкой модулей высокоточных станках с ЧПУ и сборкой их пайкой или сваркой [1].
При применении модульной технологии, при прочих весьма положительных прогрессивных ее сторонах, особенно возможностью изменения рабочих характеристик колеса без переналаживания или остановки производства, она влечет за собой еще и переход от статической балансировки к динимической парной балансировке на специальном стенде.
Сборке как заключительных технологических операций при применении модульной технологии, требует переход на синфазную сборку и отказ селективной сборки. Это связано с переходом от статической балансировки на динамическую колес. Причем после определения вектора остаточной дисбалансной массы одного из колес, к нему в противофазе присоединяется второе колесо с вектором остаточной дисбалансной массы направленным в противоположную сторону. Такая сборка осуществлена на центробежном насосе подпиточного насоса СНТ 01.520, что привело к минимизации вибропаказателей агрегата.
Динамическая балансировка рабочих колес проводится на специально спроектированном и изготовленном стенде рамного типа.
Балансировочный стенд НИИГМ им М. М. Федорова представляет собой неподвижную статику, крепящуюся на фундамент, на котором расположены:
- неподвижная рама;
- приводной электродвигатель;
- подпружиненная подвигаемая рама с установленным на ней узлом крепления рабочих колес насосов;
- ограждения вращающихся частей.
Крутящий момент электродвигателя через клиноременную передачу передается узлу крепления рабочих колес.
Неподвижная рама 1 крепится на фундаменте и является основанием стенда. Эта рама представляет собой сварную конструкцию, выполненную в основном из швеллера №16. К раме приварена плита, на которой смонтирован приводной асинхронный электродвигатель 48. Крутящий момент электродвигателя через клиноременную передачу передается узлу крепления рабочих колес.
К неподвижной раме прикреплена подвижная рама 2 при помощи плоских пружин 14 и 15. Такой тип подвески обеспечивает высокую чувствительность к остаточным дисбалансам и называется - мягкая подвеска.
Со стороны приводного двигателя плоские пружины установлены перпендикулярно оси вращения. Такое расположение позволяет раме иметь расположение, на зависящее от натяжения приводных ремней.
Со стороны узла крепления рабочих колес плоские подвесные пружины установлены параллельно оси вращения рабочего колеса. Эта подвеска обеспечивает высокую чувствительность к колебаниям в горизонтальной плоскости.
В случае значительных дисбалансов рабочих колес могут возникать колебания большой амплитуды. Эти колебания могут привести к выходу из строя индукционных датчиков 52. Для предотвращения этого на подвижной раме со стороны рабочего колеса установлены дополнительные плоские пружины 15, вступающие в работу при зажатии их эксцентриковыми кулачками 10 к неподвижной раме.
Начальные пуски при балансировке желательно проводить при максимальной жесткости пружинной подвески. По мере того, как уменьшается величина вибраций, жесткость пружинной подвески необходимо уменьшать, чем обеспечим увеличение чувствительности стенда.
С противоположной стороны от балансируемого колеса на вал насаживается шкив 6(см. чертеж ДР07.090306-02-470 С.46.1.СБД.02.000) с помощью которого рабочее колесо приводится во вращение приводным электродвигателем. Для уменьшения влияния вибраций электродвигателя на целевые измерения при балансировке рабочего колеса, вал приводится во вращение от электродвигателя посредством тикстропных ремней.
В балансируемое колесо вставляется разжимная цанга 12, и колесо насаживается на вал 3. Далее на колесо устанавливается балансировочный диск 9, специальной шайбой поворачиваются тяги 19, которые попадают в пазы на балансировочном диске. При помощи специального ключа завинчивается упорная гайка13, упирающаяся в шайбу14, которая перемещает тяги 19. Тяги перемещают балансировочный диск 9, который соединен со стаканом 10. Стакан крепится на втулке 11, который упирается в рабочее колесо. Под воздействием тяг колесо перемещается и упираясь в цангу и разжимает ее, тем самым колесо фиксируется на валу. Для соблюдения точности балансировки на втулке отмечен паз, в который должна попадать тяга, также имеющая метку. Кроме того, на цанге имеется метка, которая устанавливается по середине шпоночного паза, напротив отмеченного места на балансировочном диске.
Вращающееся балансируемое рабочее колесо имеет надежное ограждение с целью обеспечения безопасности обслуживающего персонала. Защитное ограждение выполнено передвижным. При установке и снятии рабочего колеса ограждение отодвигается, перед началом балансировки надвигается и фиксируется.
Измерительная аппаратура, применяемая на стенде
Блок-схема измерительной части стенда представлена на рисунке 1
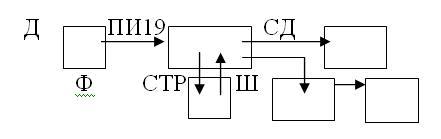
где: Д пьезоакселерометр;
ПИ-19 виброметр;
Ф встроенный фильтр, f=25Гц;
СД стрелочный индикатор;
СТР стробоскоп;
Ш градусная шкала;
Пьезоакселерометр установлен на подвижной раме станка и воспринимает вибрацию от неуравновешенности балансируемого колеса. Сигнал виброускорения подвергается калиброванному усилению, фильтрации в окрестности оборотной частоты (для данного стенда на частоте 25Гц с полосой пропускания фильтра 21...29Гц с целью компенсации неравномерности вращения приводного двигателя), одинарному или двойному интегрированию для получения виброскорости, или вибросмещения, по величине которых судят о дебалансе. Фазовый угол дебаланса определяют стробоскопом, который автоматически включается в момент достижения сигналом максимума и освещает неподвижную градусную шкалу, закрепленную на защитном кожухе приводных шкивов. На данную шкалу проектируется изображение стрелки-указателя, расположенной на вращающемся роторе.
Процедура одноплоскостной балансировки состоит в определении векторов вибрации начального и с пробным грузом.
Методика проведения статической балансировки в динамическом режиме
Методика балансировки рабочих колес:
1. Ознакомится с устройством стенда для балансировки рабочих колес и инструкциями к применяемым измерительным приборам.
2. На подвижной раме по оси стенда установить вибропреобразователь таким образом, чтобы реагировал на горизонтальную составляющую колебаний рамы.
3. Подключить вибропреобразователь к виброизмерительному прибору.
4. С помощью соединительного кабеля соединить блок управления со стендом.
5. Блок управления и используемые вибропреобразовательные приборы должны быть расставлены на столе рядом со стендом в удобном для работы месте.
6. Вилки шнуров питания вибропреобразовательных приборов вставить в розетки.
7. Включить вибропреобразовательные приборы согласно имеющейся инструкции.
8. Движением ручки фиксатора подвижного ограждения рабочего колеса "на себя" освободить ограждение и передвинуть его в сторону от приводного электродвигателя до упора.
9. Вставить цангу 12 в рабочее колесо и насадить на вал 3 до упора.
10. Установить упорную шайбу 11 с балансировочным диском 9 и завести штанги 19 в пазы на шайбе, управляя штангами при помощи шайбы 14.
11. Специальным ключом затянуть гайку 13, чтоб обеспечить плотную посадку рабочего колеса на вал.
12. Установить подвижное ограждение над рабочим колесом и зафиксировать его.
13. Эксцентриковыми зажимами зажать пружины дополнительной жесткости.
14. Кнопкой "Пуск" включить приводной электродвигатель стенда по часовой стрелке со стороны приводного двигателя.
15. После того, как двигатель выйдет на номинальные обороты, при максимальной вибрации, не превышающей 30 мкм, отпустить пружины дополнительной жесткости.
16. Измерить и записать амплитуду А0 и фазу Y0 вектора вибрации.
17. Нажатием кнопки "Стоп" отключить приводной двигатель стенда.
18. После полного останова электродвигателя в произвольном месте установить на винт балансировочного диска пробный груз весом 20 гр.
19. Установить подвижное ограждение над рабочим колесом и произвести пуск двигателя.
20. Произвести повторные замеры амплитуды и фазы вектора вибрации.
21. Затем по правилам векторной алгебры вычисляется местоположение уравновешивающего груза в долях пробного.
22. Поставив найденный груз в "легкое" место колеса определяем остаточный дисбаланс.
23. Отпустить гайку ключом.
24. Поворотом шайбы 15 вывести с зацепления тяги крепления.
25. Снять балансировочный диск, затем балансируемое рабочее колесо.
В диаметрально-противоположном месте, так называемом «тяжелом месте», проводится выборка металла. Масса выбираемого металла равная массе уравновешивающего груза. Затем колесо вновь устанавливается на стенд с целью контроля остаточной вибрации.
Литература
1. Алиев Н.А. Технологическое обоснование методики сборки многосекционных шахтных насосов // Наукові праці Донецького національного технічного університету. Серія: гірнично-електромеханічна. Вып. 51. Донецк, 2002. С. 3-9.
2. Алиев Н.А. Технологические особенности увеличения ресурса динамических насосов. // Международный сборник научных трудов. Прогрессивные технологии и системы машиностроения. Донецк, 2001. Вып. 16 с. 9-18.
3. Алиев Н.А., Эфрос Б.М. Повышение эксплуатационных свойств новых материалов. // Международный сборник научных трудов. Прогрессивные технологии и системы машиностроения. Донецк, 2001. С. 3-9.
4. Алиев Н.А., Бондарь Ю.В., Исаев А.Е. Технология и методика изготовления и сборки многосекционных шахтных насосов горизонтальной и вертикальной компоновки малой вибронагруженности // Международный сборник научных трудов. Прогрессивные технологии и системы машиностроения. Вып. 24. Донецк, 2003. С. 3-12.