Приводится методика выбора критерия, определяющего порядок и структуру технологической сборки многосекционных шахтных центробежных насосов. Обосновано, что определяющим фактором при сборке насосов с минимальной вибронагрузкой является произведение остаточной массы рабочего колеса на величину вибросмещения.
The technique of a choice of the criterion determining the order and structure of technological assembly of multisection mine centrifugal pumps is resulted. It is proved, that the determining factor at assembly of pumps with the minimal vibrating loading is product of residual weight of the driving wheel on size of vibrating displacement.
Исследование вариантов технологии изготовления рабочих колес многосекционных шахтных насосов проведенное в НИИГМ им. М.М. Федорова привело к разработке модульно-шагового метода [1], реализация которого позволила создать высокоточные, динамически сбалансированные, с небольшим разбросом массы рабочие колеса.
Разработка и внедрение высокоточных рабочих колес потребовало изменения подходов к предсборочной подготовке и собственно технологии сборки многосекционного насоса.
Известно, что для многосекционных насосных агрегатов высокое качество балансировки роторов в сборе может быть обеспечено только при отсутствии последующего демонтажа деталей, в частности колес, для организации окончательной сборки. Вследствие этого, высокое качество балансировки роторов многосекционных насосов, при общей сборке которых, предварительно сбалансированный ротор вновь разбирается, не может быть обеспеченно лишь маркировкой деталей ротора. Для получения высокой степени сбалансированности таких роторов необходимо:
1) обеспечить минимальный остаточный дисбаланс, или минимальное значение вибросмещения для каждого из балансируемых колес;
2) выделить фактор, доминирующий при технологической сборке, позволяющий организовать порядок и структуру сборки как завершающей операции с получением минимально возможной вибронагруженности насосного агрегата;
3) дополнительные параметры величины зазоров по межступенным щелевым уплотнениям, зазоры по валу при посадке колеса, коэффициент снижения вибрации выполняют вспомогательную роль и корректируются по доминирующему фактору;
4) сборку многосекционного насоса нужно осуществлять посредством противофазной установки пары колес.
В дальнейшем, за доминирующий фактор при сборке будут приняты положительные разности так называемой балансной меры. Под балансной мерой будем понимать произведение окончательной массы рабочего колеса на конечную вибрацию, полученную для колеса на стенде для балансировки в динамическом режиме [2].
Предложенный метод сборки многосекционного насоса заключается в следующем: исследование вибропараметров, геометрии масс и кинематической точности рабочих колес при предсборочной подготовке, специальной селекции их по балансной мере и организации собственно сборки. Были исследованы две группы колес: первая группа 22 стальных штампосварных колеса производства завода №1, вторая группа 22 чугунных литых колеса завода №2.
Режущий и мерительный инструмент, применяемый для механической и термической обработки обеих партий колес, идентичен и соответствует единым техническим требованиям операционной технологии, разработанной лабораторией шахтного водоотлива НИИГМ им. М.М. Федорова. Кинематические параметры, отклонения взаимного расположения поверхностей колес коренного и покрывного дисков, ступицы и горловины лежат в пределах, обговоренных техническими требованиями чертежа колеса и приведенных для различных производителей [2].
В таблице приведены результаты взвешивания, параметры балансировки и остаточного вибросмещения стальных штампосварных и чугунных литых рабочих колес.
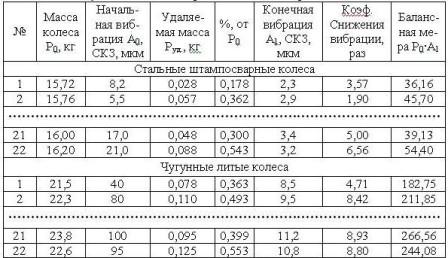
Таблица Результаты балансировки колес центробежных насосов
На рисунке 1 показана гистограмма распределения начальных масс стальных штампосварных колес, которая может быть аппроксимирована двойной экспоненциальной зависимостью (функцией Лапласа) [4].
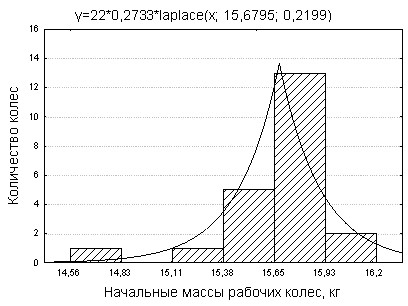
Рис.1 Гистограмма распределения масс стальных штампосварных рабочих колес насосов ЦНС 300 для партии n=22
На рисунке 2 показана гистограмма распределения начальных масс чугунных литых колес при выборке n=22, аппроксимируемая полиномом третьей степени [4].
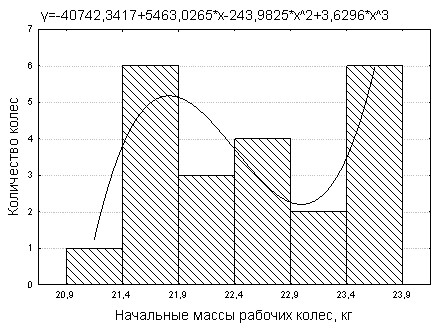
Рис.2 Гистограмма распределения масс чугунных литых рабочих колес насосов ЦНС 300 для партии n=22
Сравнение полученных распределений и их анализ показывает, что фактор массы при разработке технологии сборки не может выступать определяющим сборочным критерием. Это объясняется как различием формы кривых, описывающих плотность распределения, так и большим разбросом параметра массы особенно для чугунных литых колес.
В качестве равнозначного фактора для колес обеих групп было принято произведение остаточного веса рабочего колеса (после снятия дисбалансной массы) на амплитуду вибросмещения балансная мера. Полученная гистограмма плотности распределения балансной меры для штампосварных колес представлена на рисунке 3, для чугунных литых колес на рисунке 4. И в том и в другом случае плотность распределения может быть описана экспоненциальной зависимостью.
В основу предложенного метода противофазной сборки положено:
а) сборка насоса производится парами колес, причем вектора остаточных дисбалансных масс располагаются во взаимно обратном направлении (в противофазе). Ориентация векторов шпоночные пазы. При долблении или строгании шпоночных пазов они формируются по геометрическому центру выборки удаляемой массы, на противоположной стороне коренного диска.
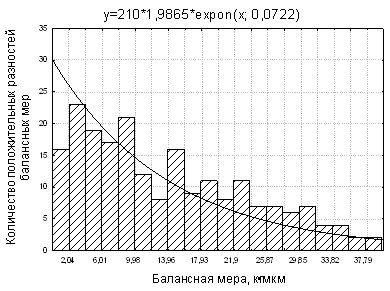
Рис.3 Гистограмма распределения балансных мер стальных штампосварных колес
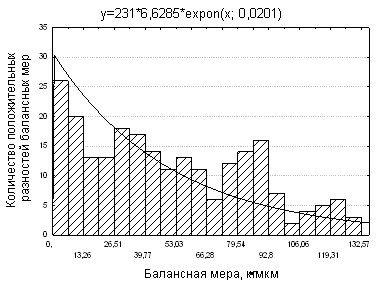
Рис.4 Гистограмма распределения балансных мер чугунных литых колес
б) минимизация балансной меры пары колес осуществляется по положительной разности произведений массы колеса на остаточное вибросмещение, причем каждая пара колес в ряду устанавливается от мидельной части насоса к опорам.
в) порядок устанавливаемых пар осуществляется выборкой из крайнего левого (см. рисунок 3 и рисунок 4) столбца имеющего минимальное значение группы положительных разностей балансных мер, с определением этих разностей для вновь добавленной группы колес со всей оставшейся совокупностью неиспользованных элементов, как в первой группе, так и в последующих.
На рисунке 5 и 6 показаны графики изменения балансных мер взятых из крайнего левого столбца плотностей распределения этих же мер для стальных штампосварных (рисунок 5) и литых чугунных колес (рисунок 6). Для стальных штампосварных колес эта выборка составляет 15 пар колес, для литых (рисунок 6) - 25 пар колес при общей совокупности 231 разности.
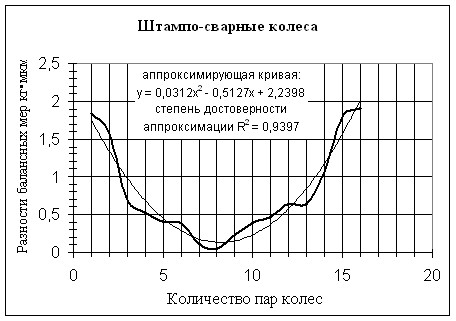
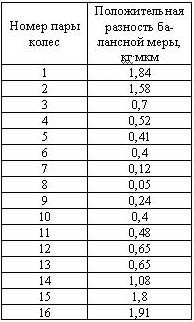
Рис.5 Распределение разностей в пределах минимального отклонения балансной меры для стальных штампосварных колес
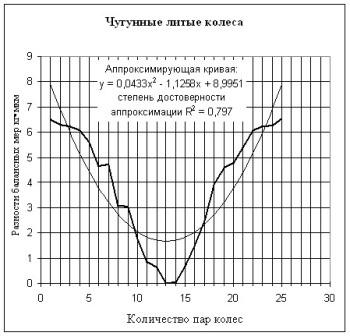
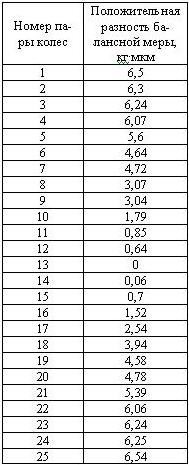
Рис.6 Распределение разностей в пределах минимального отклонения балансной меры для чугунных литых колес
Экспериментальные насосы ЦНС 300Ч600, собранные по предложенной технологии имеют виброскорость 2,2ч2,8 мм/с, что в три раза меньше допустимого по ТУ на насосы этого типа.
Литература
1. Коваль А.Н., Алиев Н.А. Новые технологии производства рабочих колес для шахтных многосекционных насосов // Наукові праці донецького державного технічного університету. Донецьк: ДонДТУ, 2001 Вип. 94 с 77-82.
2. Алиев Н.А. Технологические методы и средства увеличения долговечности шахтных многосекционных насосов в чугунном исполнении. // Збірник наукових праць. Проблеми експлуатації обладнання шахтних стаціонарних установок. Донецьк: НДІГМ ім. М.М. Федорова. 2001 Випуск 94 с. 45-62.
3. Алиев Н.А., Константинов С.С., Лумей М.Ю., Дудченко А.Ю., Исаев А.Е. Особенности технологии изготовления рабочих колес центробежных насосов модульным методом. // Сборник научных трудов, посвященный 45-летию ДГМИ, «Перспективы развития угольной промышленности в XXI веке» (Алчевск, апрель 2002 года/ Ред. кол.: В.Н. Окалелов, А.Ю. Рутковский, С.С. Сиротин и др. Алчевск: ДГМИ, 2002. 207-212 с.
4. Боровиков В. STATISTICA: искусство анализа данных на компьютере. Для профессионалов. СПб.: Питер, 2001. 656 с.
5. Вибрации в технике: Справочник. В 6-ти т./ Ред.. совет: Челомей В.Н. (пред.). М.: Машиностроение, 1981. Т.6. Защита от вибрации и ударов/ Под ред. Фролова К. В. 1981. - 456 с.