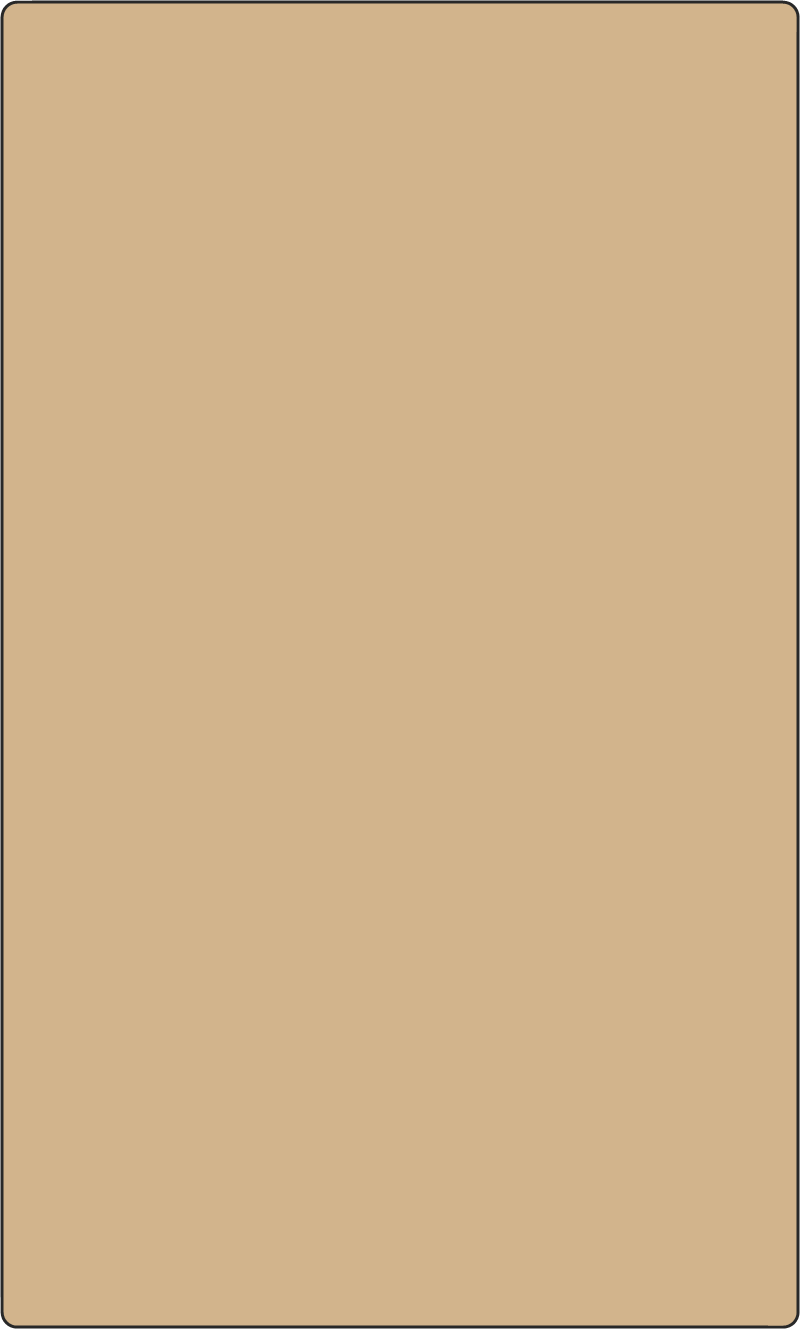
Modern technology often come to the realization of heterogeneous processes occurring between two or more heterogeneous environment in the system "liquid - liquid" and "liquid - solid." This process of mass transfer, dispersion, separation of liquids and slurries, crystallization, prevent scale formation on surfaces of heat exchangers and pipes, the polymerization and depolymerization, etc., and even different chemical and electrochemical reactions.
The technology of hydrodynamic cavitation processing liquids used for the intensification and reducing energy intensity and improving the output quality of processes of homogenization and dispersion.
Cavitation - the formation of a fluid pulsating bubbles (cavities) filled with steam, gas or a mixture thereof.
The process of hydrodynamic cavitation treatment is carried out in a special device - a passive hydrodynamic disperser through directed and controlled conversion of potential and kinetic energy of fluid flow, forcing the pumped hydraulic pump through a reaction chamber dispersant.
As a result, these transformations of energy in special areas of hydrodynamic disperser there and supported the formation of gas or steam cavern, which subsequently closed (collapse) with an increase in local hydrostatic pressure in the fluid. Closure of the cavitation bubbles is accompanied by intensive shock wave processes with the emergence of local zones of high pressures and temperatures.
In point of shock-wave effects are structural and molecular changes in complex molecules, agglomerates and globules, which was originally present in the fluid, the destruction of organic and mineral impurities. Accompanying cavitation processes of heat and mass transfer, and emerging on the downstream fluid jet stream led to intense mixing and dispersion of multi-component immiscible liquids and solids to form a homogeneous and stable over time to a bundle of fine emulsions and suspensions.
Hydrodynamic cavitation processing of fuel oil can be made directly to the fuel-sites with full use of standard equipment circulation systems and pumping oil to the burners.
Switching to a fuel-plant water-fuel emulsions (WFE) to replace conventional fuel oil provides the following benefits:
• Greatly simplified the technology and reduced energy consumption for the preparation of liquid fuels for combustion in boiler furnaces and boilers. This is achieved because of the cycle of fuel excluded operations sedimentation, drainage and cleaning of contaminated oil produced water. Thus, do not need to cost steam and electricity for a long heating fuel in storage tanks that provide settling of water.
• Enhanced environmental safety of boilers and reliability of the equipment. Rationally organized the burning of WFE can reduce the content in the flue gases of oxides of nitrogen NOõ by 20-40%, carbon-black by 70-80%, sulfur oxides by 10 -15 %. compared with the burning of emulsified oil. There is deeper fuel burn, reduced ash deposits on the gas path, increases the reliability of the boiler equipment. Go to the burning of WFE always leads to lower concentrations of nitrogen oxides c(NOõ) in combustion products in a wide range of excess air coefficient a 'in comparison with modes of burning emulsified fuel oil (figure).
|
Figure The influence of humidity burned WFE in the boiler TP-170 on the concentration of nitrogen oxides in exhaust gases:
1- a' = 1,10;
2- a' = 1,15;
3- a' = 1,20 |
The value of reducing Dñ(NOõ) depends on the humidity WFE. With humidity of 10-12% reduction amounts to Dñ(NOõ) = 50-60 ìã/ì3. However, if we move from the initial regime (Wp=5%; a'=1,2) to a regime that combines reduced excess air (a' = 1,10) and work in WFE with humidity around 12%, the total reduction in the concentration of nitrogen oxides amounts to 140 ìã/ì3. An even more abrupt reduction is achieved in regimes with high humidity WFE (Wp = 18-20%), but this is not a basic solution to the technical and environmental reasons. The final decision about acceptable moisture content of water-oil emulsions is determined by environmental and techno-economic optimization.
Abstract
Svetlana Voloshina
Faculty: Physical and Metallurgical |
Speciality: Heat-and-Power Engineering |
|
The scientific adviser: Pjatyshkin G. |
Research and study methods for improving the reliability of the hydrodynamic devices based on thermodynamic analysis of the cavitation process |