ОБЕСПЕЧЕНИЕ ЭКОЛОГИЧЕСКОЙ БЕЗОПАСТНОСТИ СОРТОПРОКАТНОГО ПРОИЗВОДСТВА ЗА СЧЕТ СНИЖЕНИЯ НЕОРГАНИЗОВАННЫХ ВЫБРОСОВ
В.А. Темнохуд, В.В. Откидач, В.В. Кочура, С.В. МазурДонецкий национальный технический университет
Рассмотрена проблема подавления неорганизованных пылевыделений на прокатных станах. Особенностью предлагаемого способа пылеподавления является совмещение в одном устройстве технологических процессов термического упрочнения и пылеподавления. Приведен алгоритм системы технологического проектирования участка ускоренного охлаждения сортового металла и пылеподавления. Освещены основные результаты проведенных промышленных исследований. Проанализированы составные части эффективности применения разработанных систем.
При прокатке количество пыли, попадаемой в атмосферный воздух, составляет не менее 200 грамм на тонну готового проката, причем до 20% от этого количества составляет мелкодисперсная окалина, наиболее опасная для человека.
При создании технологий нового качественного уровня, обеспечивающих повышение механических свойств проката за счет совмещения в едином технологическом потоке стана операций пластической деформации и термического упрочнения, была также поставлена задача существенного снижения вредных выбросов в атмосферу цеха за счет подавления пылеобразования на выходе из очага деформации компактной струей отработанного охладителя.
Для решения поставленных задач разработана система технологического проектирования участка ускоренного охлаждения в потоке сортового прокатного стана. Входом в систему расчетов служит задание на проектирование, которое включает сортамент охлаждаемого проката по профилям и маркам сталей, геометрические размеры проката, площадь его поперечного сечения, скорость прокатки, температуру металла на входе в охлаждающее устройство и выходе из него, требуемый уровень механических свойств, требуемую степень подавления пылевыделений и ряд ограничений, одно из которых оговаривает схему подачи охладителя на прокат в зоне выхода металла из очага деформации. Выходом являются проектные решения в виде:
- сортамента профилей, охлаждаемых в устройстве;
- конструктивных параметров системы охлаждения;
- технологических параметров работы системы охлаждения;
- компоновки охлаждающего оборудования в потоке стана;
- параметры размещения секции устройства по отношению к выходному сечению очага деформации для обеспечения требуемой степени пылеподавления;
- температурного состояния раската в процессе, как ускоренного охлаждения, так и на стадии выравнивания температур в паузах при транспортировке его по рольгангу;
- экономических показателей эффективности разработанной системы охлаждения.
Процесс принятия решения разделен на ряд подсистем, соответствующих этапам разработки проекта: сортировка сортамента профилей по группам (подсистема "Сортировка сортамента"); определение конструктивных параметров системы охлаждения (подсистема "Оборудование"); расчет технологических параметров работы системы охлаждения (подсистема "Технология"); теплотехнические расчеты по определению температурного состояния раската (подсистема "Температурный режим"); расчеты размещения секции устройства по отношению к выходному сечению очага деформации (подсистема "Пылеподавление"); технико-экономические расчеты и определение показателей эффективности проекта (подсистемы "Экономика" и "Критерии эффективности"). Указанные подсистемы связаны между собой таким образом, что выход из каждой предыдущей системы служит входом для последующей. Степень свободы при выработке проектных решений на каждом этапе регламентирована системой ограничений, а соответствие результатов проектирования требованиям (подсистема "Удовлетворение потребности") достигается благодаря системе обратных связей, которые могут воздействовать на любую из указанных подсистем процесса. Остановимся коротко на характеристике отдельных подсистем. В подсистеме "Сортировка сортамента" (рисунок 1) формируется массив характерных профилеразмеров, обрабатываемых в охлаждающей системе одних геометрических (конструктивных) размеров. При формировании массива исходят из требований обеспечения устойчивости транспортирования охлаждаемого профиля по камере охлаждения и минимизации площади поперечного сечения камеры охлаждения по допустимым значениям расхода и давления охладителя.
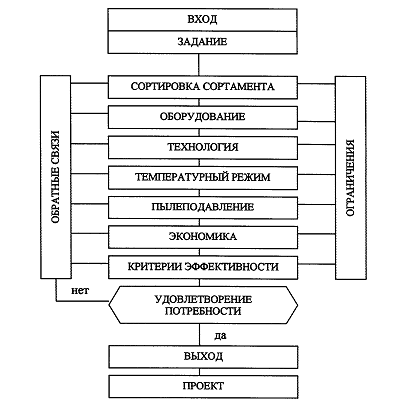
Рисунок 1 – Системная модель алгоритма автоматизированного технологического проектирования систем ускоренного охлаждения и пылеподавления
В подсистеме "Оборудование" формируется задание на проектирование основного охлаждающего оборудования. При этом геометрические размеры профилей массива, полученные в предыдущей подсистеме, выравниваются и округляются по группам соответственно минимальных и максимальных размеров каждого элемента профиля. По полученным данным рассчитывается сечение камеры охлаждения, близкое по форме к сечению охлаждаемого профиля, с учетом допустимой величины искривления раската как в результате пластического деформирования в прокатной клети. При этом расчет длины активной зоны охлаждения производится по явной конечно-разностной схеме с учетом изменения теплофизических свойств металла в процессе охлаждения и необходимой температуры конца ускоренного охлаждения.
В подсистеме "Технология" с учетом геометрических размеров камеры охлаждения и массивов профилеразмеров, полученных на предыдущих этапах расчета, производится определение технологических параметров системы ускоренного охлаждения. Требуемое количество воды, необходимое для охлаждения раската до заданной температуры, определяется из уравнения теплового баланса. При этом нагрев охладителя в камере охлаждения определяется по способности металла отдать необходимое количество тепла с учетом геометрических размеров профиля и максимальной допустимой температуры нагрева охладителя для конкретных производственных условий. Для предотвращения местного парообразования на контакте воды с поверхностью раската обеспечивается необходимая степень турбулизации потока охладителя в камере путем достижения относительной скорости потока 8-12 м/с в зависимости от размеров сечения профиля. При расчете давления охладителя учитываются условия необходимости покрытия гидродинамических потерь в камере охлаждения и проталкивания потока охладителя с необходимой скоростью по длине камеры. При этом площадь поперечного сечения сопла форсунки находится из уравнения неразрывности потока. В зависимости от заданных ограничений расчет технологических параметров работы системы производится как для прямоточной, так и для противоточной схем подачи охладителя. Для обеспечения пылеподавления в очаге деформации расчет технологических параметров работы секции, непосредственно установленной за рабочей клетью прокатного стана, производится только для противоточной схемы подачи охладителя.
В подсистеме "Пылеподавление" производится определение расстояния от оси прокатных валков до секции охлаждения, исходя из условия перекрытия зоны очага деформации потоком отработанного охладителя. При этом учитывают площадь сечения камеры охлаждения и угол раскрытия струи охладителя.
В подсистеме "Температурный режим" производится расчет распределения температур по сечению раската и среднемассовых температур в процессе ускоренного охлаждения и на стадии выравнивания. При расчете коэффициента теплоотдачи на каждом шаге по времени учитывают теплопроводность и кинематическую вязкость воды, абсолютную и относительную скорости движения потока охладителя, геометрические размеры камеры охлаждения и проката, температуру поверхности раската и охладителя, а также длину активной зоны охлаждения проектируемого участка. При этом теплофизические параметры металла и охладителя определяют для охлаждаемой марки стали на каждом расчетном шаге по известным методикам с помощью разработанной подпрограммы.
В подсистеме "Экономика" выполняются расчеты стоимости оборудования участка (установка охлаждения и пылеподавления, насосы, трубопроводы и др.), себестоимости продукции с учетом ускоренного охлаждения, расчетной прибыли и других экономических показателей.
В подсистеме "Критерии эффективности" рассчитывают показатели эффективности предложенного оборудования: тепловая мощность устройства, снижение среднемассовой температуры на 1 метр длины устройства, нагрев охладителя и др. Кроме этого рассчитываются показатели эффективности проекта в целом: прибыль от реализации продукции с повышенным уровнем служебных свойств, рентабельность, срок окупаемости и др. Оценка этих критериев производится путем сравнения с достигнутыми показателями на аналогичных системах.
По описанному алгоритму может быть разработано несколько альтернативных вариантов проектного решения. Путем сравнения их по указанным выше критериям определяется оптимальный вариант.
Предложенная система технологического проектирования была использована при разработке проектов реконструкции с модернизацией участков ускоренного охлаждения на станах 300-1 и 300-3 Магнитогорского металлургического комбината и стана 250-2 комбината "Криворожсталь". Конструкции устройств, выполненные с использованием расчетов по данной модели, внедрены в потоке станов 250, 360 Енакиевского, 400 Донецкого, 330 Краматорского металлургических заводов. Конструкции устройств предусматривали подачу на раскат со стороны выхода из очага деформации струи воды, участвовавшей в теплообмене на всем протяжении активной зоны охлаждающего устройства. При этом окалина, отрывающаяся от поверхности металла при его контакте с валками, смачивается и уносится водой, а не попадает в атмосферу цеха. Степень подавления пылевыделений составила 98-99%. Результаты промышленного освоения подтвердили достоверность расчетов и эффективность принятых технических решений, что позволяет рекомендовать разработанную систему технологического проектирования при расчетах систем ускоренного охлаждения как на реконструируемых, так и вновь вводимых прокатных агрегатах.
Экономическая эффективность разработанных технологических решений определяется в основном повышением качественных показателей сортового проката, однако наряду с этим получен эффект от экономии металла за счет уменьшения вторичного (внепечного) окалинообразования. Также получен и социальный эффект за счет улучшения условий труда обслуживающего персонала при уменьшении тепло- и пылевыделений в атмосферу цеха и неорганизованных выбросов в окружающую среду.