Ю.Е. Петухов. Некоторые направления развития САПР режущего инструмента
Методологические основы САПР различных объектов и процессов были заложены и в большой степени реализованы в отечественной промышленности в 70—80-е гг. В последнее десятилетие несмотря на общий экономический спад наблюдалась интенсивная компьютеризация как исследований, так и производства, а также резкое расширение возможностей технического и программного обеспечения. Возникшее противоречие обусловило необходимость внедрения различных САПР, в том числе САПР режущего инструмента (РИ)
Опыт разработки САПР РИ и анализ современных программных средств позволили выделить следующие наиболее актуальные и перспективные направления в создании САПР РИ: разработка и развитие баз данных, образующих совместно с системами управления ими банк данных; разработка модулей базы знаний; расширение системного подхода на всех уровнях САПР; использование методов математического моделирования и оптимизации; визуализация проектирования; разработка отраслевых САПР РИ
Для расширения информационной базы САПР, помимо банка данных, систем поиска и документирования, разработаны исследовательские модули (ИМ), которые могут быть использованы как элементы базы знаний. Общие ИМ охватывают следующие объекты: инструментальные материалы (свойства и выбор); базовые элементы, узлы и синтез конструкции РИ; геометрические (угловые) параметры РИ; схемы резания; факторы, характеризующие процесс формообразования РИ и обрабатываемой им детали
Выбор инструментального материала для конкретных условий обработки (вида РИ; типа и состояния оборудования; режима резания; состояния и формы обрабатываемой поверхности; типа производства; экономических критериев и др.)в настоящее время не формализован. В условиях САПР РИ автоматизация выбора инструментального материала достаточно успешно осуществляется на базе метода экспертных оценок; перспективны также методы теории корреляции и стохастическое моделирование.
Специализированные ИМ предназначены для оптимизации отдельных видов РИ на основе аналитических и оптимизационных методов математического моделирования.
Общие и специализированные модули формообразования, входящие в состав ИМ, основываются как на классической теории сопряженныхлиний и поверхностей, так и на более общих численных методах. Разработанные алгоритмы позволяют компьютеру без участия пользователявыводить частные уравнения для расчета режущих кромок, поверхностей и других параметров, отдельных видов РИ. Например, необходимые для многих расчетов преобразования координат, связывающие РИ и обрабатываемую деталь в их относительном движении, может производить специализированный модуль с использованием исходной матрицы преобразований МО следующего вида:
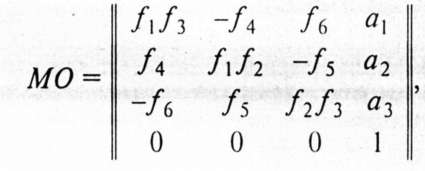
Рисунок 1 – матрица преобразований МО
Разработанный алгоритм позволяет сформировать на базе матрицы МО ряд матриц, описывающих конкретные преобразования координат, произвести над ними требуемые действия, получить координаты поверхности (профиля) детали в системе координат РИ в любой момент формообразования
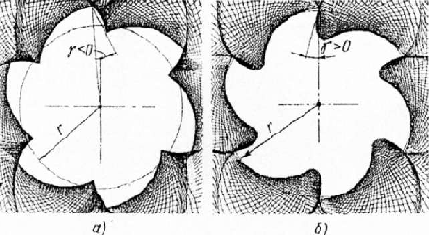
Рисунок 2 – Профиль зубьев концевой фрезы при обработке червячной фрезой: а — у < 0; б — при у > 0
На рис. 2 показаны графические модели формообразования торцевого сечения концевой фрезы при обработке ее канавок червячной фрезой с различной установкой. При первой установке концевая фреза имеет отрицательный передний угол ?, а ее передняя поверхность — выпуклую форму (см. рис. 2, а), при второй установке передний угол положительный, а форма передней поверхности вогнутая (см. рис. 2, б), что облегчает ее последующее шлифование.
Решение задач формообразования на основе системного подхода включает в себя: расчет формы и размеров поверхностей РИ (режущих кромок, профиля, задней поверхности); проверочный расчет, в том числе решение обратной задачи (т.е. определение профиля обрабатываемой w всрхности детали); технологию получения режущих кромок; расчет инструмента второго порядка и его установки при обработке проектируемого РИ; выбор технологии переточки РИ; оптимизацию его профили по выбранным критериям (точности. числу переточек и др.).
Исследования, проведенные на основе сис темного подхода, позволили установить ряд новых зависимостей для РИ с режущими кромками сложной формы (фасонными или в виде пространственных кривых). Например, погрешность \ профиля, возникающую при переточке затыло нанных фрез (она может превысить допуск на профиль), можно многократно уменьшить только благодаря оптимальной установке круга путем изменения смещения с его оси относительно оси фрезы (рис. 3). Положение точек А и В на графике (в точке А дельта = 0, в точке В с = 0) зависит от типафрезы (дисковая, червячная), ее геометрии, размеров и от диаметра шлифовального круга. Для оценки точности фасонных профилей разработана специальная методика, позволяющая определить действительную погрешность как отклонение формы, что особенно важно, если профиль задан или рассчитывается по точкам.
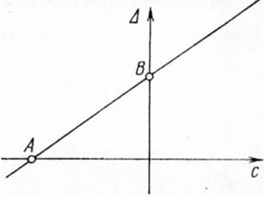
Рисунок 3 – зависимость дельта=f(с) для затылованных фрез
Проведенные для ряда инструментов (фрез, долбяков, резцов и др.) расчеты показали, что системный подход наряду с использованием методов моделирования и оптимизации дает возможность существенно улучшить многие показатели качества РИ (суммарную размерную стойкость, точность и др.), а также снизить стоимость.
Аппарат математического моделирования может использоваться в ИМ и непосредственно в алгоритмах расчета отдельных видов РИ. Помимо известных преимуществ, он полезен тем, что позволяет четко сформулировать основные задачи в виде одной или нескольких целевых функций и ограничения в виде неравенств и уравнений, отражающих внутренние и внешние связи РИ. В достаточно общем случае целевая функция имеет вид К = F (х,) > max (min); Фу (х,) < bj, где К — критерий целевой функции Fзависящей от переменных Xj (ими могут быть число зубьев,геометрические параметры, диаметр и другие размеры РИ), процесса изготовления и эксплуатации РИ; bj — const; функции Фу в виде уравнений, неравенств, таблиц являются ограничениями и отражают требования и условия формообразования, работоспособности, изготовления и эксплуатации РИ.
Если max (min) функции f отсутствует, моделирование носит имитационный характер. Содержание величины К (экономический или технический показатель) зависит прежде всего от вида РИ, обрабатываемой поверхности детали, типа производства и требуемой точности обработки.
В ИМ могут быть включены различные задачи исследования и выбраны различные критерии. Например, при исследовании погрешности дельта затылованных фрез при переточке (см. рис. 3)
К = дельта; х, — размеры и геометрия фрезы, диаметр круга и его смещение с относительно фрезы; ограничениями Фj служат допускаемая ширина зуба и канавки фрезы, значения заднего и переднего углов, пределы изменения с, допускаемые затыловочным станком, и некоторые другие параметры.
Для одного вида РИ как в ИМ, так и в алгоритмах САПР могут быть использованы различные модели с разными критериями К и ограничениями Фj. Например, если червячная фреза, имеющая профиль с протуберанцем (т.е. предназначенная для нарезания колес с выкружкой у основания зуба), используется в единичном производстве, то важным критерием А" является число колес данного модуля (с различными числами зубьев, коэффициентом смещения, припуском под шлифование), которое может быть нарезано одной фрезой. Если та же фреза используется в серийном или массовом производстве, то основной критерий К — это число колес данного модуля с определенным числом зубьев (или суммарное число зубьев всех колес), нарезанных фрезой до (ее полного стачивания.
Таким образом, модели и алгоритм САПР даже для одного вида РИ. И могут и должны быть весьма разнообразны. Тем не менее, для характерных технологических процессов обработки деталей могут быть выбраны определенные критерии и ограничения, т.е. должны использоваться определенные математические модели. Отметим, что применение моделирования для червячных фрез с протуберанцами позволило сократить число их типоразмеров более чем в 2 раза.
Визуализация проектирования путем использования графических моделей и математических зависимостей как на стадии анализа и исследований, так и при получении окончательных результатов и рабочих конструкций облегчает работу конструктора, делает процесс проектирования наглядным, а в ряде случаев дает возможность быстро получать оптимальное решение. Использование, например, в графической системе T-FLEX 3D команд "Функция", "Анимация" и других позволяет быстро и с высокой точностью моделировать обкатку профиля колеса червячной фрезой и получить размеры профиля колеса с выкружкой у ножки зуба. Применение указанного подхода для анализа зависимости переднего угла у фасонного резца, работающего с круговой подачей, имеющего наклонную под углом у переднюю поверхность и переменный угол ф профили, дает полное представление о всех возможных значениях у и позволяет при любом заданном диапазоне изменений у определить допустимые значения ф, при которых у > 0 (рис. 4).
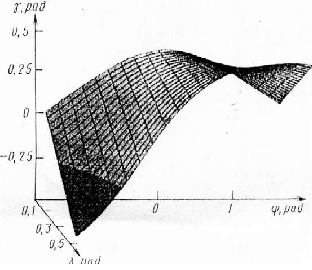
Рис. 4. Зависимость переднею угла а фасонного резца от углов ф и у
Важной особенностью САПР РИ является учет влияния методов контроля. Большая группа РИ (фрезы, долбяки, метчики, специальные резцы и др.) имеют режущие кромки в виде фасонных плоских или пространственных кривых. От точности их формы и размеров непосредственно зависит точность обработки. Поэтому для кон троля таких РИ используют различные приборы, в том числе достаточно сложные и дорогие. Вместе с тем, даже идеально точный прибор еще не гарантирует требуемую точность режущей кромки, так как необходимо, кроме того, правильно выбрать способ и технологию контроля.
Компьютерное моделирование различных РИ с учетом используемых в промышленности измерительных средств позволило разработать подсистему САПР РИ, обеспечивающую контроль сложных режущих кромок. Эта подсистема предусматривает: 1) расчет режущей кромки — проектный или (если имеется рабочий чертеж) проверочный; 2) выбор способа контроля и измерительного прибора; 3) выбор технологии контроля для конкретных приборов, имеющихся у изготовителя и потребителя РИ; 4) разработку технологии получения кромок при изготовлении и переточке РИ с учетом выбранного способа контроля; 5) разработку способа сохранения точности кромок после переточек РИ.
Подсистема контроля охватывает следующие виды РИ: дисковые и пальцевые затылованные и острозаточенные фасонные фрезы; червячные фрезы, обрабатывающие шлицсвые валы, зубчатые цилиндрические и червячные колеса (в том числе зацепляющиеся с конволютным, архимедовым и эвольвентным червяком); долбяки для нарезания внешних и внутренних зубчатых венцов с произвольным профилем; метчики; фасонные резцы.
Использование элементов данной подсистемы в различных отраслях промышленности показало, что она позволяет во многих случаях значительно упростить контроль или повысить точность режущих кромок сложных РИ на величину, составляющую существенную часть (до 30—70% и более) средних значений допуска.
При разработке и эксплуатации САПР всегда были весьма важны различные аспекты ее организационного обеспечения. В настоящее время ввиду ограниченности инвестиций и высоко^ стоимости разработки САПР становятся особенно актуальными объединение финансовых и программных средств, унификация и совместимость последних, т.е. согласованная работа различных предприятий в направлении создания отраслевых САПР (в том числе САПР РИ).