Abstract
Сontent
- The purpose
- Objectives
- Relevance of the topic
- Expected scientific novelty
- The functionality of the cutting fluids
- Methods of the cutting fluids
- References
The purpose
To increase processing performance of machine parts by a rational justification of the application of the cutting fluids
Objectives:
- study the possibilities for reducing the temperature with cutting cutting fluids;
- optimization of cutting conditions for turning with cutting fluids using linear programming;
- software development of theoretical calculations of the temperature of cutting and optimum cutting conditions
Relevance of the topic
One method to improve the efficiency of machining is the use of cutting fluids, which is especially important for stainless steel, heat-resistant and high strength steels and alloys with very low machinability.
High temperatures in the processing zone, arising due to the low thermal conductivity of hard materials, determine the need for the study of thermal phenomena in the cutting area and study the effectiveness of cutting fluid to reduce heat and improve performance.
The present method of calculation of heat flows and temperatures in the cutting zone in view of the cutting fluids [1, 2] does not consider the characteristics of hard materials. For these types of materials of interest to the further development of methods for determining the temperature in the cutting area by using different cutting fluids.
In [3] proposed a method for assessing performance processing with different coolants, but the analysis is performed for only one of the material. It is advisable to empower the proposed method for evaluating the effectiveness of different coolants when turning hard materials.
When analyzing the possibilities to increase processing performance, including through the use of COTS is very important the right choice of the cutting. The method of optimization of cutting conditions in turning, taking into account the temperature limitations proposed in [4, 5], can be used for different hard materials. It is interesting to further develop methods for determining heat flows, temperatures and cutting in a wide range of processing conditions of various materials.
Expected scientific novelty consists of:
- in the development of methods for determining the heat transfer coefficient for internal cooling of the cutter;
- to develop a mathematical model for determining heat flow and temperature of cutting taking into account the action of cutting fluids when turning various materials;
- in the development of analytical dependences for calculating the optimum cutting conditions for turning with cutting fluids, ensure maximum productivity.
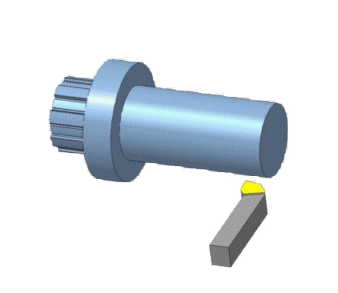
Fig. 1. Тhe process of turning
(animation: 104 kB, 8 frames, 7 cycles of repeating)
The functionality of the cutting fluids
n accordance with modern ideas coolant during the cutting process can produce lubricating, cooling, dispersing and washing steps. Separate the various effects of the coolant can be very difficult, as they may occur simultaneously and separately in different zones of the contact surface of the tool, chip and workpiece, depending on the characteristics of the operation and cutting conditions, the characteristics of processed instrumental material. In most cases, high performance coolant are determined by their lubricating and cooling effect.
Lubricating effect of cutting fluids. Lubricating effect of cutting fluids is manifested mainly in the zone of contact between the tool and chips, as well as a contact tool and the workpiece. It is due to the ability to join in the cutting fluids physical, chemical and physico-chemical interaction with the activated surfaces of the contact zone, and they form a hydrodynamic, physical (adsorption) or chemical lubricating film. Depending on cutting conditions, such films may be formed separately or simultaneously. Physical and chemical lubricants film called boundary. Their thickness varies from several tens to several hundreds of angstroms. Shear strength is higher than that of the hydrodynamic film. In the case of the formation in metal cutting hydrodynamic lubricating films (for example, the processing of copper at low speeds), the friction surfaces are separated by a layer of cutting fluids in a few microns or more. Here, the viscosity of cutting fluids is of predominant importance, and should be optimal. Sometimes, the viscosity can be compensated by sulfur-, chlorine-and phosphorus-containing additives.
Lubricating effect of cutting fluids is manifested in the fact that carbon, oxygen, sulfur, phosphorus and other elements that make up, at high pressures, voltages and temperatures not only reacts with the metal surface to form a boundary lubricant film, but also diffuse into the finest surface layers of rubbing metal surfaces, forming a eutectic alloy with lower coefficients of friction. As a result, facilitated the processes of friction and plastic deformation of the metal.
Many studies have established a positive effect of the cutting fluids lubricant on the processes to prevent sticking and narostoobrazovanie on the cutting edge tools that change the form of chips and chip contact length from the front surface of the tool, resulting in reduced heat generation, cutting forces and machined surface roughness. Lubricating effect of cutting fluids depends on the operation and cutting conditions, the properties of the treated and instrumental materials and is mainly determined by the rate of formation of boundary lubrication and wear of the films, as well as their composition, structure and properties.
The cooling effect of cutting fluids. When cutting the bulk of the mechanical energy is converted into heat. The cooling effect of cutting fluids based on the laws of heat transfer. Heated to high temperature cutting tools, workpiece and chip through the convective heat transfer coolant medium of the heat. In addition, the heat during cutting can be carried out due to heat transfer by radiation, evaporation of medium and chemical reactions occurring during the absorption of thermal energy. Heat sinks associated with radiation, evaporation and chemical reactions are small. Therefore, when assessing the cooling of the cutting fluids restricted to the convective heat transfer, which depends mainly on the thermophysical properties and hydrodynamic conditions of fluid. In the heat most strongly influenced by the viscosity, thermal conductivity, heat capacity, density, and wettability of the cutting fluids and the temperature difference between cooled surface and the liquid flow.
In the process of cutting the highest exposures to high temperature undergoes a tool. Studies show that the use of coolant medium does not prevent the emergence of a high temperature in the tool. However, the effect of cutting fluids greatly reduces the area of ??the heating tool. At the same time supply the emulsion under the pressure of the auxiliary rear surface of the tool is more effective than its free-falling stream of irrigation on the front surface of the tool. For a number of metal cutting operations, the effectiveness of the cooling of the cutting fluids rises when applying liquid in an atomized state, under pressure or through the internal channels of the instrument compared with coolant splash free-falling jet.
However, the cooling effect of cutting fluids may have negative consequences. For example, when milling (intermittent cuts) with carbide tools at high cutting speed, the use of cutting fluids results in significant variations in temperature, cutting part of the mill and reduce its strength. In addition, intensive cooling surface of workpiece usually leads to the emergence of internal stresses in the metal extension that degrades operational properties of the product.
Dispersing action of cutting fluids. By this means the cutting fluids effect their ability to facilitate the deformation of the destruction and fragmentation (dispersion) of the metal, ie, to effect that promotes the formation of new surface. In the presence of surfactant facilitated the nucleation and propagation of microcracks in the metal. Polar molecules are moving along the walls of cracks formed as long as their sizes become larger than the cracks. As a result, in the most confined spaces microcracks have additional disjoining pressure caused by the adsorption layers, which leads to "embrittlement" of the metal and its destruction. The fragility of the metal may increase due to diffusion of atoms and ions in the cutting fluids deformed layers. In this process the metal in the deformation zone quickly reaches the limit of strength and collapses at a lower cost of energy.
Detergent action of cutting fluids. In the process of cutting metal shavings and sludge formed, consisting of fine chips, particles, tool wear and rubbing parts of the machine, scale, dust, mud, thermo-oxidative degradation products of components of coolant and microorganisms. Solid colloidal particles penetrate into the sludge microroughnesses workpiece, machine parts and tools, which are strongly held by electrostatic and mechanical forces. The accumulation of sludge particles leads to a decrease in tool life and quality of the treated surface. Therefore, coolant flush, and must carry a large metal shavings or sawdust, to prevent the formation of carbon deposits and lakoobraznyh on the surfaces of products and tools, heated to high temperatures. Detergent action of cutting fluids is a combination of physical and chemical processes that lead to clean the surfaces of the workpiece, tool and machine parts from the sludge. Flushing and evacuation of large chips or sanding that accumulate in the cutting zone, is one of the important functions of coolant. Flushing action is largely dependent on the amount of coolant supplied to the cutting zone, the flow rate and method of fluid. The effectiveness of flushing of the coolant rises with the introduction of its detergents [6].
Methods of the cutting fluids
In engineering practice, the most common cutting fluids is fed into the cutting zone irrigation in the form of a free-falling jet. In Fig. 2. An example of practical implementation of the scheme coolant on a lathe (rear view).
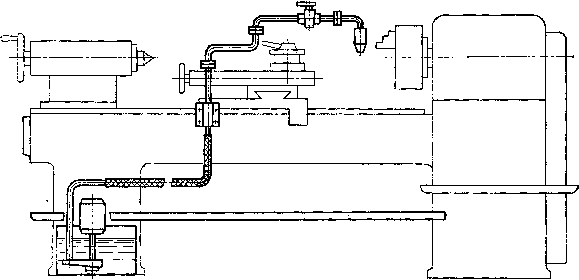
Fig. 2. Coolant system on a lathe
Cutting fluid from the tank in the left cabinet of the machine pump through a flexible hose is fed into the pipeline with a cork nozzle valve and nozzle. From the nozzle tip cutting fluids is fed free-falling stream of the cutting tool and the workpiece.
If you need more intensive cooling of cutting tools applied to internal cooling, which consists in passing a cutting fluids for the internal channels in the body of the instrument. The most commonly used in the internal cooling of the axial-type tools drills, core drills, reamers, broaches, taps and other similar instruments, but can also be used for any other instruments. In Fig. 3 shows the incisors with internal cooling. In the body of a cutter has a cavity whose surface is covered with a porous material (Fig. 3a), moistened with a cooling liquid.
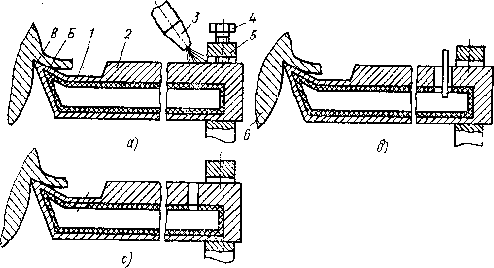
Fig. 3. Cutters with internal cooling
When cutting fluid in cutting tool of the vaporized and condensed in the cold
side of the clamping tool. In porous material 2, it goes back to the cutting part. The incisors may be closed (Fig. 3b) and flow (Fig. 3c) of the cavity.
In 1952 he proposed a coolant in the form of foam, which is formed by the blowing of compressed air and cutting fluids is fed into the processing zone in the same way as the liquid when it is watered. The foam acts in the cutting zone is less efficient than cutting fluids flow, increasing the coefficient of resistance is in the range 1.2 - 1.5. The foam does not spread so freely on the surface of the workpiece and parts of the machine, not sprayed, and therefore pollute less than the workplace. Use this method when processing asymmetrical parts, projecting parts are cast or shoot down a jet of cutting fluids fed irrigation, or in other cases, where the use of more efficient ways of coolant is inconvenient or impossible for some reason.
In the early 50's developed and investigated a way to cool and lubricate the cutting area high-pressure jet of fluid. In this method of coolant is fed into the cutting area from the rear surface of the blade in a thin stream under pressure 20 - 30 atmospheres. The first work to study the effectiveness of this method have shown that it allows you to repeatedly increase the life of the tool compared to machining with coolant irrigation. Further investigation of this method have been devoted to studying the effect of jet velocity, flow rate, temperature and other parameters on the life of the tool. There have been depending on the speed of the jet set, the liquid flow rate and durability of cutting tools on the diameter of the nozzle and the pressure in the supply system. The method of cooling high-pressure coolant jet is especially effective when cutting difficult to cut materials and alloys. Thus, stoykostnye tests showed that the intermittent turning of alloy EI437 resistance of high-speed cutting tools when applying to the cutting area high-pressure jets of coolant increases by more than 6 times as compared to machining with coolant irrigation, and similar results were obtained with intermittent turning of alloy EI766. The method of cooling and lubrication of high-pressure jet of liquid is very effective, you need to studied and developed the method, but it has not yet been widely used in industry because of the very serious inherent weaknesses. One of the reasons hampering the application of the method is a strong sprinkling of the elastic and hazardous liquid jet issuing from a nozzle under high pressure at 50 - 80 m / s. Another reason is the difficulty of ensuring integrity of mobile connections for the supply of fluid lines, pressure 20 - 30 atmospheres. For these reasons, the method is currently used only for treatment of difficult to cut materials and in other cases, where the essential increase tool life by any technical means.
Less effective compared with high-pressure jet cooling method, but it is more convenient, technologically advanced and promising is the way to cool and lubricate the cutting area sprayed liquid. It was first proposed in 1944 as an engineer Novosibirsk G. Pokrovsky. In his article, the author noted that this method is ... certainly deserves much attention
. However, in the difficult war-time method has not been given due attention and only a decade later he was re-explored, developed and taken to the arsenal of means to improve the efficiency of metal cutting.
The essence of the method of cooling and lubricating spray fluid is that the cutting fluids in a special raspylivaetsya raspylivayuschem device with compressed air and fed into the cutting zone in the form of air-liquid mixture. For the formation of air-liquid mixture using special spray installation of various structures.
he most successful and workable was setting type UR-3 (Fig. 4) with double-liquid mixing with air, designed for spraying lubricating fluid, water-based. Compressed air from the factory network, having the valve or plug valve, passes through the filter in a pressure-reducing valve 2 is designed to reduce pressure and maintain it at a constant level during operation.
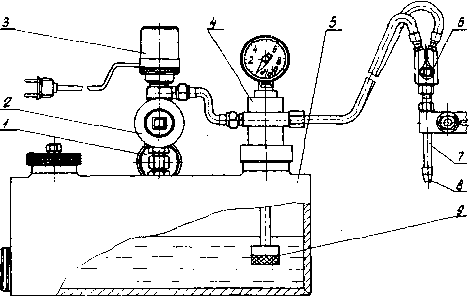
Fig. 4. Installing the UR-3 with a double-fluid mixing with air
Spray are in the cutting zone more effectively than irrigation fluid supplied through supply of oxygen in the cutting zone of compressed air and spray droplets of electrification. The described spray installation is automated. Automation is the use of devices at these facilities, including automatic feed to the cutting area spray during the working stroke of the machine and stops supplying it with the end of the machine [7].
References
- Резников А.Н., Резников Л.А. Тепловые процессы в технологических системах. – М.: Машиностроение, 1990. – 288 с.
- Ивченко Т.Г. Расчет тепловых потоков и температур резания при точении с использованием смазочно-охлаждающих жидкостей. // Надійність інструменту та оптимізація технологічних систем. Збірник наукових праць. – Краматорськ, ДДМА. вип.26, 2010. – c. 90-96.
- Богуславский В.А., Ивченко Т.Г., Зантур Сахби. Повышение производительности обработки труднообрабатываемых материалов с применением смазочно-охлаждающих жидкостей // Наукові праці Донецького національного технічного університету. Серія: Машинобудування і машинознавство. Випуск 7(166). – Донецьк, ДонНТУ, 2010. – c. 9-16.
- Зантур Сахби, Богуславский В.А., Ивченко Т.Г. Оптимизация режимов резания при точении труднообрабатываемых материалов с учетом температурных ограничений // Прогрессивные технологии и системы машиностроения: – Донецк: ДонНТУ, 2010. Вып. 39. – c. 77-84.
- Vadim Bogouslavskiy, Tatiana Ivchenko. Optimisation of cutting regimes at application of technological cutting fluid // ModTech International Conference 25-27th May 2011, Vadul lui Voda: Chisinau, 2011. p. 669-672. (Index to Scientific & Technical Proceedings of Thomson Scientific – Institute for Scientific Information (ISI).
- Смазачно-охлаждающие технологические средства [электронный ресурс]. – Режим доступа: http://www.texnologia.ru/...
- Способы и техника применения технологических сред при резании металлов [электронный ресурс]. – Режим доступа: http://www.info.instrumentmr.ru/...
- Справочник по обработке металлов резанием / Ф.Н. Абрамов, В.В. Коваленко, В.Е. Любимов и др. – К.: Техника, 1983. – 239 с.
Remark! When I wrote this abstract, master's work is not yet completed. The definitive variant will be ready by December, 2012. Full text of work and materials on the subject can be obtained from the author or his adviser after that date.