Реферат за темою магістерської роботи
Зміст
- Вступ
- 1. Актуальність теми
- 2. Мета і задачі магістерської роботи
- 3. Наукова новизна
- 4. Огляд існуючих рішень і розробок
- Висновки
- Перелік посилань
Вступ
Очисний забій є основним технологічним процесом вугільного підприємства. Від його ритмічної роботи залежить економічні показники шахти.
Виїмка вугілля здійснюється за допомогою комбайнів, стругів і гідромоніторів. Доставка вугілля із забою здійснюється за допомогою скребкового конвеєра. Підтримання вироблення здійснюється за допомогою механізованих кріплень.
Автоматизація гірничого виробництва дозволяє замінити функцію людини з управління, регулювання і контролю технологічного виробництва за допомогою спеціальних пристроїв.
Автоматично діючий пристрій працює більш надійно, виключає помилки персоналу, а головне, при скороченні кількості працівників, які безпосередньо беруть участь у виробництві, забезпечують зростання продуктивності праці, а звільнена робоча сила використовується на іншому робочому місці. Експлуатація забійних машин, комплексів і агрегатів пов’язана зі значними труднощами, зумовленими гірничо-технологічними умовами, пилогазовим режимом шахти, її мікрокліматом і другими факторами.
1. Актуальність теми
В даний час комбайнової виїмкою забезпечується 65–70 відсотків видобутку вугілля. Змінюються в широких межах залягання та фізико-механічні властивості вугілля, потужність пласта, умови кріплення і транспортування, наявність різного роду порушень, особливості технології ведення робіт, особливо в високонавантажених лавах, практично безперервно змінюють режим роботи комбайна. Причому виникає необхідність одночасно виконувати декілька операцій, наприклад керувати швидкістю подачі і розсуненням ріжучих органів. До того ж зона виїмки вугілля є одним з найбільш небезпечних ділянок лави. Тому проблеми автоматизації забійного обладнання приділяється велика увага. Сучасні гірничі машини не обладнані пристроєм для плавної зміни швидкості різання, тому регулювання роботи двигуна здійснюється за допомогою авторегуляторів, підтримуючих задане навантаження двигунів шляхом зміни тільки швидкості подачі [1]. Відомі численні дослідження і розробки з створення датчиків відкритого кордону “порода-вугілля” з використанням перерахованих характеристик.
2. Мета і задачі магістерської роботи
Метою проектування системи автоматизованого управління комбайном по гіпсометрії пласта є підвищення терміну служби електромеханічного обладнання за рахунок створення системи автоматизованого управління комбайном по кордону порода-вугілля.
Для створення даної системи необхідно вирішити ряд завдань, а саме:
3. Наукова новизна
Аналіз літературних джерел з існуючих систем автоматизації процесу видобутку вугілля показав, що основними недоліками даних систем є швидке зношування виконавчого органу і високе навантаження на двигун при різкому переході буріння на більш міцну породу [2].
Вміщують породи розроблюваних вугільних пластів мають середню стійкість. Переважаючими бічними породами вугільних пластів є глинисті сланці. В окремих району басейну у зв’язку зі зміною літологічного складу порід, що складають окремі почту, переважаючими бічними породами є пісковики і піщані сланці, значно рідше вапняки. Механічна міцність гірських порід вкрай нерівномірна і коливається в широких межах [3].
Вугілля Донецького басейну відносяться до гумусовим. Сапроелітовие різниці вугілля зустрічаються тільки у вигляді окремих лінз і вугільних прошарку. Вугілля пластів, що залягають у відкладах середнього і верхнього карбону, мають майже однаковим материнським рослинною речовиною, але мають різні якісні показники, що пояснюється в основному їх різним ступенем вуглефікації, різним ступенем відновлення та окислення в процесі їх формування, а також неоднаковою зольністю і сірчистого. Вміст фосфору у вугіллі досить незначно. Вихід летких речовин коливається в широких межах – від 2 % (антрациту) до 50 % (довгополуменеве вугілля). Теплота згоряння вугілля знаходиться в межах від 7500 до 8750 ккал/кг. Найбільш чисті і малосірчисті вугілля є в західному секторі Великого Донбасу (Південний і Західний Донбас) і відносяться до відкладень нижнього карбону. У Донбасі встановлено закономірне зміна змісту летючих речовин у вугіллі зі зменшенням їх вмісту в напрямку з північного заходу на південний схід і від стратиграфічні вищерозміщених до нижчого рівня. Зольність і вміст сірки у вугіллі коливаються в широких межах. Середній вміст природного золи в більшості вугільних пластів знаходиться в межах 7–20 %. Малозольних вугілля з зольністю до 7–8 % в басейні небагато. В Донбасі переважають вугілля среднесерністие (1,5–3 %). Вугілля Донецького басейну в основному мають легку і середню збагачуваність.
У Донецькому кам’яновугільному басейні поширені всі основні марки кам'яного вугілля: довгополуменеве (Д), газові (Г), жирні (Ж), коксове (К), отощенія спекающиеся (ОС), пісне (Т), полуантраціти (ПА) і антрациту (А), а також перехідні від бурого вугілля до довгополуменеве. Петрографічний склад вугілля досить однорідний [4].
Опірність вугілля різанню в привибійної частини пласта Апр, кН/см, визначається з виразу
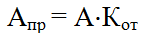
где Кот – коефіцієнт віджиму, що враховує зниження опірності вугілля різанню в зоні віджимання в порівнянні з опірністю різанню неотжатого масиву вугілля;
А – опірність вугілля різанню в неотжатом масиві, кН/см.
Середня опірність вугілля різанню в зоні віджимання Аот, кН/см, визначається з емпіричного виразу

де L – ширина привибійного простору, м;
Р – опірність (жорсткість) кріплення у лаві, МПа.
Швидкість подачі Vп визначається за такою залежністю

де Vп.пр – швидкість подачі комбайна, розрахована за встановленої потужності привода при відомих величинах опірності вугілля різанню Ар та потужності пласта m, м/хв;
Vп.тяг – швидкість подачі комбайна по тяговому зусиллю, м/хв;
kв.п – коефіцієнт збільшення швидкості подачі комбайна в залежність мости від марки вугілля, тому при в’язких вуглях kв.п = 1,002; при крихких вуглях kв.п = 1,15; при дуже крихких вуглях kв.п = 1,303.
До в’язкого вугілля відносяться:
Визначена за формулою швидкість подачі Vп при розробці тонких і вельми тонких пластів перевіряється за швидкістю засувки конвеєра в лаві при управлінні роботою комбайна (Vм).
При 0,8≤m<1,1 м Vк = 1,7–2,3 м/хв.
При 1,1≤m<1,3 м Vк = 2,3–4,5 м/хв.
Для конкретного забою швидкість подачі комбайна слід визначати за фактичною опірності пласта різанню в зоні роботи виконавчого органу Aр.ф.. Також можна використовувати дані про опірності різання пласта в масиві, скориговані за фактичною потужністю і ширині захоплення комбайна (так званий коефіцієнт віджиму kот)
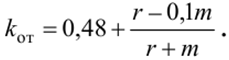
Тоді

Fп – складова сили різання в напрямку подачі комбайна, кН;
Fт – тягове зусилля подачі частини комбайна, кН;
G – вага комбайна, , кН;
α – укут падіння пласта при роботі по простяганню, град. При роботі лавами за падінням або повстання приймається рівним нулю.
Інтерполяція Vп.пр по опірності пласта різанню проводиться по залежності
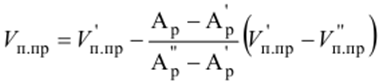
Складова сили різання в напрямку подачі комбайна при конкретному значенні опірності пласта різанню знаходиться шляхом інтерполяції з виразу
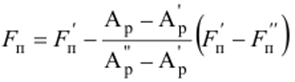
Fп' і Fп" – складові сили різання в напрямку подачі комбайна, відповідні Aр' і Aр", кН [5].
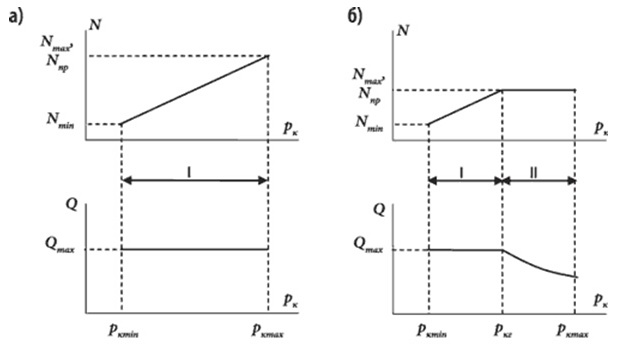
Рисунок 1 – Залежності потужності різання і теоретичної продуктивності комбайна від контактної міцності руйнування породи при відсутності регулювання (а), плавному (б) регулюванні навантаження [6]
Процес видобутку вугілля очисним комбайном представлений на рисунку 2.
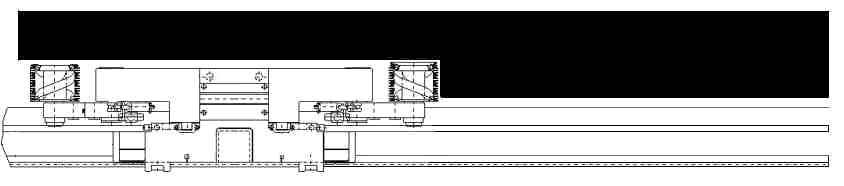
Рисунок
2 – Процес видобутку вугілля очисним
комбайном
(анімація: 9 кадрів, 5 циклів повторення, 115 кілобайт)
На практиці фактично швидкість пересування визначається такими факторами: швидкістю засувки конвеєра, швидкістю повітря, параметрами кріплення [7].
Існуючі системи управління не дозволяють одночасно керувати швидкостями різання і подачі.
Раніше вже були спроби створення подібних систем, робота яких грунтувалася на величинах, отримуваних різними датчиками порода-вугілля. Однак застосування радіоізотопного датчика не безпечно для обслуговуючого персоналу, а тензометричний датчик, який закріплюється безпосередньо на виконавчому органі, має низьку довговічність. З розглянутих пропозицій випливає необхідність створення системи управління, побудованої на наступних принципах:
4. Огляд існуючих рішень і розробок
Замкнутим циклом автоматизації мають автоматичні регулятори навантаження, що працюють за програмою, заздалегідь встановленої людиною. Така система автоматичного регулювання (САР) навантаження двигуна комбайна може мати три варіанти зі зміною: швидкості подачі; різання; подачі і різання. З теорії роботи механізмів відомо, що для підтримки постійного навантаження на двигун і забезпечення максимальної продуктивності машини (комбайна) необхідний вибір оптимальних значень швидкості подачі і швидкості різання в залежності від міцності вугілля. При цих умовах також повинна проводитися автоматичне коректування на зниження струму навантаження в залежності від температурного режиму двигуна, так як двигуни гірських комбайнів працюють на перехідній потужності (годинна – тривала). Такий регулятор САР вимагає створення сучасного тиристорного регульованого приводу для комбайнів, де оптимальні параметри роботи будуть забезпечуватися обчислювальною машиною, виконаної з регулятором. В даний час на основі першого варіанту регулювання Макіївським заводом шахтної автоматики випускається регулятор навантаження УРАН, який забезпечує:
Функціональна схема регулятора УРАН представлена на рисунку 3.
Регулятор має два канали: швидкості і навантаження, які спільно працюють на пристрої виходу, К каналу швидкості відносяться: датчик швидкості ДС, програма швидкості ПС, блок контролю швидкості БКС і блок вихідних пристроїв. До каналу навантаження відносяться: датчик струму ДТ, програма струму ПТ і імпульсний пристрій ІУ. У блоці каналу швидкості проводиться порівняння двох напруг: датчика швидкості і програми швидкості, які пропорційні швидкості подачі UП і установки швидкості програми Uу. У разі різниці між ними виробляється сигнал на включення Електрогідрорасприделітелі ЕДР щодо зменшення або збільшення швидкості подачі.
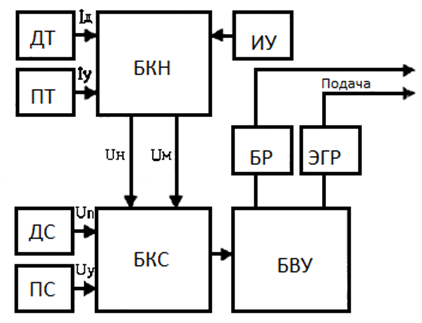
Рисунок 3 – Функциональная схема регулятора УРАН
У блоці каналу навантаження порівнюються напруга пропорційне фактичній току двигуна Iд і напруга програми струмового уставки, пропорційне уставки Iу. При різниці цих значень межах ± 5% Iу регулятор по каналу навантаження не працює (зона нечутливості). При різниці значення в межах 5-25% більше Iу з блоку БКН в блок БКС видається напруга Uн на імпульсне зменшення швидкості подачі до значення встановлення струму Iд в. межах ± 5% Iу. Якщо неузгодженість струму Iд більше 25% струму Iу, то блок БКН видає безперервний сигнал на зменшення швидкості подачі. При недовантаження двигуна комбайна, тобто коли Iу >> Iд, блоком БКН видається напруга Uм на збільшення швидкості подачі до значення встановленого програмою швидкості ПС. У разі застосування в комплексі з комбайном запобіжної лебідки її управління здійснюється блоком реле БР. При пуску комбайна в блоці БКС працює реле часу, який видає сигнал да установку нульової швидкості подачі, а через 2-3 с здійснює процес на нормальне її регулювання. У регулятор УРАН входять пристрої: електронний блок, датчик швидкості, датчик струму, панель індикації, джерело живлення і пульт управління. У комплексі з регулятором УРАН встановлюється апарат контролю роботи електродвигунів КОРД, який забезпечує захист при технологічних перевантаженнях, перекиданні і обриві однієї з фаз.
Апаратура ІПІР-3М це імпульсний пропорційно-інтегральний регулятор навантаження на приводі виїмкових машини. Вона випускається серійно в аналоговому варіанті. Структура цього пристрою представлена на рисунке 4.
Регулятор ІПІР-3М імпульсного типу. Як і апаратура САДУ-2 він містить два контури управління. Один з них є контуром управління по потужності двигуна, інший за швидкістю подачі машини на забій. Як і в попередньому випадку, перший контур має найбільший пріоритет.
Сигнал, який задаэться, і фактичний сигнали за навантаженням двигуна подаються на елемент порівняння критичного і заданого струму навантаження двигуна сигнал з елемента порівняння С1, який формує два вихідних сигналу імпульсного типу. Перший імпульсний сигнал з’являється в тому випадку, якщо струм навантаження двигуна буде перевищувати задане значення. Цей сигнал подається на перший широтно-імпульсний перетворювач ШІМ1, який перетворює сигнал позитивного неузгодженості в широтно-модульований імпульсний сигнал. Ширина імпульсу цього перетворювача пропорційна величині позитивного неузгодженості між заданим і фактичним струмом навантаження. Сигнал з ШІМ1 через логічні елементи І-НЕ і релейний елемент (ключ К1), імпульсно подається на логічний ключ І другого контуру управління. При негативному неузгодженості фактичного і заданого струму навантаження двигуна сигнал з елемента порівняння С1 подається на ШІМ2, що працює за таким же принципом як і ШІМ1. Вихідний сигнал цього модулятора імпульсно включає релейний ключ А4, який через блок логіки управляє виконавчими електромагнітами.
Контур регулювання швидкості подачі містить елемент порівняння С2, призначений для порівняння заданої і фактичної швидкості подачі комбайна. Причому сигнал від задає пристрою надходить через логічний ключ І, на який одночасно подається з ключа К1 імпульсний сигнал позитивного неузгодженості струмового навантаження двигуна. Другим вхідним сигналом елемента порівняння С2 є сигнал з датчика швидкості ДС. Сигнал цього датчика включає одночасно релейний ключ К4, який реєструє напрямок переміщення виїмкових машини.
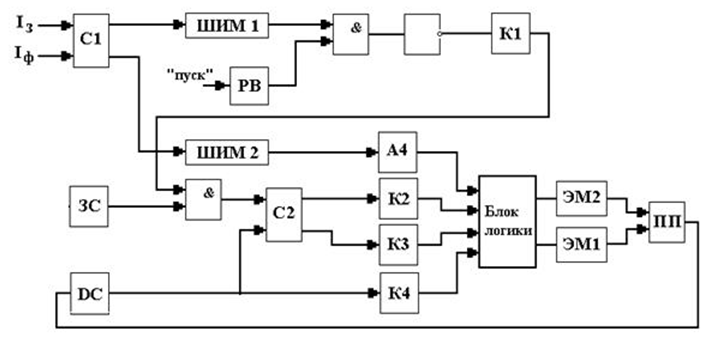
Рисунок 4 – Структурна схема апаратури ІПІР-3М
Принцип управління, закладений в апаратурі ІПІР-3М, може бути реалізований в мікропроцесорному варіанті. Так як контур регулювання навантаженням двигуна є пріоритетним, то на початку цього циклу фактичне навантаження двигуна порівнюється із заданою її величиною, яка зчитується з пам'яті мікроконтролера. Якщо фактичне навантаження не перевищуватиме заданої, то відбувається перехід до оператора перевірки рівності фактичної і заданої швидкостей подачі комбайна. У разі виконання цієї умови відбувається повернення на початок цього циклу (до опитування датчиків), в іншому випадку проводиться перевірка умови нерівності цих швидкостей. При цьому, якщо фактична швидкість подачі комбайна не перевищуватиме задану, то включається режим імпульсного збільшення цієї швидкості, до тих пір поки задана швидкість не зрівняється з фактичною [8].
Робота даних регуляторів заснована на вимірюванні струму в обмотках приводного двигуна і забезпечує номінальне навантаження, змінюючи обертів двигуна. При цьому відбувається швидке зношування виконавчого органу, а також стає неможливим управління комбайном по гіпсометрії пласта. Застосування інших датчиків порода-вугілля не дає бажаного позитивного ефекту, так як вони не охоплюють значну частину діапазону поєднань різноманітних за характеристиками вміщуючих порід і вугілля. Неможливо використання датчиків при значному ушкодженню пластів перехідними дрібно амплітудними порушеннями. Негативний вплив на роботу більшої частини датчиків порода-вугілля надають обводненість і попереднє зволоження вугільних пластів, а також відсутність чіткої межі між вугіллям і породою [9].
Разом з тим проблема визначення та контролю кордону “порода-вугілля” може бути вирішена пристроєм, структурна схема якого приведена на рисунку 5.

Рисунок 5 – Структурна схема пристрою контролю кордону “порода-вугілля”
Пристрій контролю кордону “порода-вугілля” встановлюється на віддалі від робочого виконавчого органу гірничої машини, що підвищує надійність експлуатації і збільшує термін служби чутливого елемента. Включення вимірювального перетворювача за диференціальною трансформаторною схемою дозволяє підвищити точність визначення контрольованого кордону, забезпечує достовірність отримання інформації [10]. Робота пристрою контролю кордону “порода-вугілля” полягає в наступному. Зусилля впливу F масиву вугілля (породи) на поверхню різального органу перетвориться в осьове переміщення L механічного чутливого елемента, що призводить до зміни положення сердечника диференційного трансформаторного перетворювача, на виході якого формується сигнал U, відповідний впливу вугільного або породного масиву. Для приведення вихідного сигналу U в стандартне значення Uст використовується нормуючий перетворювач.
Структурна схема САУ комбайном представленана на рисунку 6.
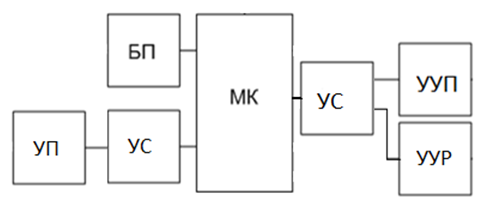
Рисунок 6 – Структурна схема системи автоматизованого управління комбайном
На рисунку 6 прийняті наступні умовні позначення: УП – пристрій перетворення зусилля у зміну напруги; УС – блок узгодження; МК – мікроконтролер; УП – пристрій керування швидкістю подачі; БП – блок живлення; УУР – пристрій керування швидкістю різання.
Ця система управління побудована на новому пристрої, який раніше не застосовувався. Застосування даного пристрою дає можливість системі швидко реагувати на зміну міцності масиву при проходженні кордону порода-вугілля, оперативно змінюючи швидкості різання і подачі.
Висновки
Використання системи автоматизованого управління комбайном по гіпсометрії пласта, створеної на основі пристрою компенсації навантаження, дозволить значно збільшити термін служби як комбайну (відсутність сильних навантажень на двигун), так і самого виконавчого органу за рахунок компенсації різкої зміни зусилля при переході роботи комбайна на породу більш високої міцності.
Примітка. На момент написання даного реферату магістерська робота ще не завершена. Остаточне завершення – грудень 2012 р. Повний текст роботи та матеріали по темі можуть бути отримані у автора або його керівника після зазначеної дати.
Перелік посилань
- Ямщиков В.С. Контроль процессов горного производства: Учебник для вузов. – М.: Недра, 1989, 446 с.
- Горбатов П.А., Петрушкин Г.В., Лысенко Н.М., Павленко С.В., Косарев В.В. Горные машины для подземной добычи угля. / П.А. Горбатов, Г.В. Петрушкин, Н.М. Лысенко, С.В. Павленко, В.В. Косарев – М.: Недра, 1990, 305 с.
- Паффенгольц К.Н. Геологический словарь: в 2-х томах. / К.Н. Паффенгольц – М.: Недра., 1978.
- Горная википедия [Электронный ресурс]. – Режим доступа: http://miningwiki.ru.
- Практикум по курсу «Процессы подземных горных работ» для студентов специальности 7.090301.02 всех форм обучения / под редакцией докт. техн. наук проф. Ярембаша И. Ф., изд. 3-е, дополненное – Донецк: ДонНТУ, 2008, – 118 с.
- Электронная библиотека [Электронный ресурс]. – Режим доступа: http://library.stroit.ru.
- Солод В.И., Гетопанов В.Н., Рачек В.М. Проектирование и конструирование горных машин и комплексов. Учебник для вузов. / В.И. Солод, В.Н. Гетопанов, В.М. Рачек – М., Недра, 1982, 350 с.
- Портал [Электронный ресурс]. – Режим доступа: http://geofut.com.
- Богданов Б.В., Зуев В.С., Гаврилов П.Д., Орлянский В.В. – Системы дистанционного и автоматизированного управления выемочными машинами (патентный обзор) / Б.В. Богданов, В.С. Зуев, П.Д. Гаврилов, В.В. Орлянский – ЦНИЭИуголь, Москва, 1974.
- Шидлович Л.Х. Дифференциальные трансформаторы и их применение. / Л.Х. Шидлович – Энергия, 1966, 96 с.