Реферат за темою випускної роботи
Зміст
Введення
Актуальність проблеми переробки мідного лому в умовах обмеженості сировинних ринків для промислово розвинених країн останніми роками стає все гострішою. Так, випереджаючі темпи зростання машинобудівного комплексу та привабливість експорту металопрокату на тлі обмеженої сировинної бази рудної сировини, повільного освоєння розвіданих родовищ і практично зупиненої геологорозвідки нових родовищ створює все зростаючий дефіцит мідного сировини для металургійних і ливарних підприємств.
З іншого боку, все інтенсивніше йде процес масового вибуття основних фондів (застарілі верстати, металоконструкції тощо), зважаючи на їх високу зношеність. Тому в даний час дуже високий інтерес металургійних та ливарних виробництв до пошуку сировини на вторинних ринках, а зростаюча вартість енергоносіїв змушує шукати більш ефективні способи їх переробки в товарну продукцію.
Зміст роботи
Металургійні процеси виробництва міді на заводах вторинної кольорової металургії, як правило, включають піро- і гідрометалургійний переділи, конвертації, вогневе рафінування і розливання. Пірометалургічний переділ лому і відходів ведуть в агрегатах різної конструкції: у шахтних, відбивних, електродугах печах, в конвертерах.
Для плавки лому і відходів сплавів міді використовують, як правило, стаціонарні, поворотні і такі, що обертаються відбивні печі.
Для рафінування мідних сплавів використовують обробку розплаву за допомогою різних дутьевих і пристроїв пальників або вводять рафінуючі флюси. Основу домішок, що містяться в мідному ломі, складають свинець, олово, цинк, залізо, нікель, миш'як, сурма і сірка. Невелика кількість вісмуту, теллура, хрому і срібла також може зрідка зустрічаються в розплаві.
Олово, як постійний супутник вторинної міді при окисленні окрім оксиду олова (SNO) утворює діоксид олова (Sno2), який частково розчиняється в міді і не утворює силікатів. В цьому випадку в шлак (рафінуючий флюс) переходять станнати основних металів (зазвичай кальцію). Застосовують також спосіб рафінування вторинної оловосодержащей міді продуванням розплаву сумішшю метан-кисень через верхню склепінну фурму. Показники процесу приведені в таблиці. 1 порівняно з вживаними в промисловості технологіями рафінування в барабанній і стаціонарній відбивній печі і за способом "Контімельт". Аналогічні результати отримані для видалення з міді вісмуту і миш'яку.
Відбивна піч | Спосіб «Контімельт» | Барабанна піч | Продування зверху |
---|---|---|---|
0,216/0,095 | 0,32/0,12 | 0,05/0,003 | 0,155/0,0015 |
0,012/0,005 | 0,127/0,017 | ---- | 0,16/0,0054 |
0,204/0,158 | 0,277/0,169 | 0,005/0,0045 | 0,0115/0,0027 |
На заводі в м. Лимож(Франція) чорнову мідь(98еди) і ме-таллический лом(92еди) переробляють у відбивній печі, з використанням газокисневого дуття. Після стандартного циклу: окислення, знімання шлаку і відновлення отримують аноди, що містять, г/т : 600 срібла, 1100 миш'яку, 2200 свинцю, 500 нікелю, 400 олова, 250 сурм, 100 селена, 100 залоза, 20 вісмуту, 100 цинку, 10 сірки. Відзначається, що при вдуванні газокисневої суміші в розплав окислення і ошлакування олова, заліза і цинку через 15-20мин досягає 90-98. Домішки нікелю, миш'яку, сурми і свинцю окислюються менш ефективно. Використовуючи содовий флюс, вдалося окислювати 80ышьяка і сурми, а також біля 90винца(до 0,05 і 0,07соответственно) лише при перегріванні розплаву до 1127°З . Витрата природного газу в процесі склала 30-50нм3/т вторинної міді.
Швидкість окислення знижується у ряді Fe - Zn - Sn, тобто досягши концентрації домішки, визначуваної коефіцієнтом вза-имного впливу, починається окислення наступного у ряді металу.
Швидкість окислення знижується у ряді Fe - Zn - Sn, тобто досягши концентрації домішки, визначуваної коефіцієнтом вза-имного впливу, починається окислення наступного у ряді металу.
Велика увага на практиці приділяється підбору оптимального складу флюсів. Для видалення олова, свинцю і сурми необхідно обробляти розплав при температурі 1117-1147°З повітрям і флюсом при співвідношенні CaO : Na2O = (1,5-2,5) :1. В результаті за 10мин обробки зміст олова знижується з 800 до 9г/т.
Одним з найбільш поширених процесів переробки низькоякісної вторинної мідьвмісної сировини є шахтна відновна плавка. Велику частину вторинної міді виплавляють в шахтних печах. Переваги шахтної плавки в металургії міді пояснюється деякими перевагами таких печей в порівнянні з відбивними і електричними. До числа основних переваг шахтних печей слід віднести їх високу питому продуктивність, високий коефіцієнт використання тепла, високу десульфурацію і незначну витрату вогнетривів у зв'язку із застосуванням кессонированных стінок.
До основних недоліків шахтної плавки необхідно віднести витрату дорогого і дефіцитного палива(коксу) і необхідність подавати на плавку в основному крупнокусковий матеріал, через що потрібне окусковывать сипкі матеріали перед їх завантаженням в шахтну піч.
Виплавка чорної міді з лому і відходів в шахтних печах - процес безперервний. У верхню частину шахти печі подається і шарами завантажується шихта і кокс, а знизу з горна майже безперервно(за винятком періоду випуску металу і невеликого горна, що йде за цим періодом наповнення) випускається шлак і періодично через 60 - 90 хвилин - розплавлений метал. У зв'язку з цим стовп шихти у міру випуску металу і шлаку опускається вниз, звільняючи місце новим порціям шихти. Таким чином, шихта безперервно рухається по шахті печі зверху вниз, послідовно проходячи через усі зони печі.
Мідь, виплавлена з лому і відходів у відбивних або шахтних печах, містить, як вже вказувалося, значна кількість домішок, основними з яких є цинк, олово, свинець, нікель, сурма і залізо. Усі ці домішки необхідно відокремити від міді.
Першою операцією по відділенню основної маси цих домішок є конвертація чорної міді, що полягає в продуванні через шар розплавленої чорної міді повітря. Операція ця здійснюється в апараті, що носить назву конвертер, звідки і сам процес дістав назву конвертація. Метою конвертації є максимальне видалення цинку, олова, свинцю і частково сурми в газову фазу і переклад нікелю, залоза і частини сурми в шлак з тим, щоб в міді, що залишається в конвертері після продування, містилося цих домішок якомога менше.
Проте практично відокремити мідь від домішок в конвертері вдається лише частково, оскільки:
- цинк, свинець, олово, сурма і нікель неминуче залишаються в невеликих кількостях в конвертерній міді;
- частина міді переходить в шлак разом з частиною нікелю, сурми, цинку, свинцю і олова, з якого доводиться ці метали витягати повторно;
В результаті конвертації чорної міді утворюються три основні продукти:
- конвертерна(чорнова) мідь, в якій концентруються повністю благородні метали, якщо вони містилися в початковій сировині, що завантажується в конвертер;
- конвертерні шлаки, в які переходить майже усе залізо, значна частина нікелю, невелика частина міді, а також частина свинцю, олова, цинку, сурми і інших домішок;
- пил, уловлений з газів конвертера, що відходять, містить основну частину цинку, частину олова, свинцю і сурми і трохи міді.
Для безпосереднього технічного застосування чорнова мідь не придатна, і тому її обов'язково піддають рафінуванню з метою очищення від шкідливих домішок і попутного витягання благородних металів, селену і теллура.
Мета вогневого рафінування на попередній(перед електрохімічною) стадії виробництва зводиться до часткового очищення міді від домішок, що мають підвищену спорідненість до кисню, і підготовки її до подальшого електролітичного рафінування. Методом вогневого рафінування з ро зплавленої міді прагнуть максимально видалити сірку, кисень, залізо, нікель, цинк, свинець, миш'як, сурму і розчинені гази.
Невеликі включення(декілька часток на мільйон часток міді) таких елементів як селен, теллур і вісмут можуть значно погіршити електропровідність і оброблюваність міді властивості, які особливо важливі для промисловості, що виробляє кабельнопроводниковую продукцію, є видатним споживачем рафінованої міді. Електролітичне рафінування вважається основним процесом, який дозволяє отримати мідь, що відповідає найбільш жорстким вимогам електротехніки.
Суть електролітичного рафінування міді полягає в тому, що литі анод(відлитий, як правило, з міді вогневого рафінування) і катоди - тонкі матриці з електролітної міді - по змінно завішують в електролітну ванну, заповнену електролітом, і через цю систему пропускають постійний струм. В процесі електролітичного рафінування вирішуються два основні завдання: глибоке очищення міді від домішок і попутне витягання супутніх цінних компонентів. В результаті електролітичного рафінування передбачається отримати мідь високої чистоти(99,90.99,99u). В цілому анодна мідь є багатокомпонентним сплавом і зазвичай має хімічний склад, приведений в таблицю. 2
Cu | S | Fe | Ni | Pb | As | Bi | Se+Te | Au | Ag |
---|---|---|---|---|---|---|---|---|---|
99.5- | до | до | до | до | до | до | до | до | до |
99,8 | 0,015 | 0,015 | 0,5 | 0,05 | 0,2 | 0,01 | 0,06 | 0,03 | 0,5 |
Для здійснення електролітичного рафінування міді аноди, відлиті після вогневого рафінування, поміщають в електролізні ванни, заповнені сірчанокислим електролітом. Між анодами у ваннах розташовуються тонкі мідні листи - катодні основи.
Електроліт є водним розчином сульфату міді(160...200 г/л) і сірчаної кислоти(135...200 г/л) з домішками і колоїдними добавками, витрата яких складає 50...60 г/т Cu. Частіше за усіх в якості колоїдних добавок використовують столярний клей і тіомочевину. Вони вводяться для поліпшення якості(структури) катодних опадів. Робоча температура електроліту 50...55 0С.
При включенні ванн в мережу постійного струму відбувається електрохімічне розчинення міді на аноді, перенесення катіонів через електроліт і осадження її на катоді. Домішки міді при цьому в основному розподіляються між шламом(твердим осадом на дні ванн) і електролітом.
В результаті електролітичного рафінування отримують: катодну мідь; шлам, що містить благородні метали; селен; теллур і забруднений електроліт, частину якого іноді використовують для отримання мідного і нікелевого купоросу. Крім того, внаслідок неповного електрохімічного розчинення анодів отримують анодні залишки(анодний скрап). Слід зазначити, що чим вище в початковій міді вміст благородних металів, тим нижче буде собівартість електролітної міді.
Між тим усі вищеперелічені технології переробки мідного лому вимагають значних енергетичних і матеріальних витрат. Крім того вони несуть досить важке навантаження на довкілля.
Для зниження енергетичних витрат і зменшення навантаження на довкілля розроблена система технологія, що поєднує виплавку, розливання і плющення мідної продукції.
Операційні цикли процесу Properzi складаються з плавки, рафінування, безперервного литва, твердіння і плющення непрерывнолитой заготівлі з міді для виробництва готової бухти електролітичної мідної катанки.
Нині в промисловості є рафінуючі печі(рис.1) на 25, 40, 80 і 120 тонн / добу. Ці печі мають основну кладку і можливістю нахилу агрегату. Магнезитова цегла і бетон є обов'язковими елементами, що дозволяють витримати хімічну агресивність вдуваних кисню і добавок флюсів, а також отримуваних оксидів, шлаків і газів. Як наслідок цього, піч повинна підтримуватися при високій температурі, оскільки основні вогнетриви швидко руйнуються при циклічному нагріванні і охолодженні.
Нахил печі також є обов'язковим функціональним елементом не лише для контролю рівня під час плавки, але і тому, що повітря і паливо вдувають під рівень рідкого металу в печі на стадії рафінування. Це здійснюється через одну, дві або три фурми, які розташовані вище за рівень рідкого металу під час операцій заправки і плавлення і нижче рівня металу в процесі переробки.
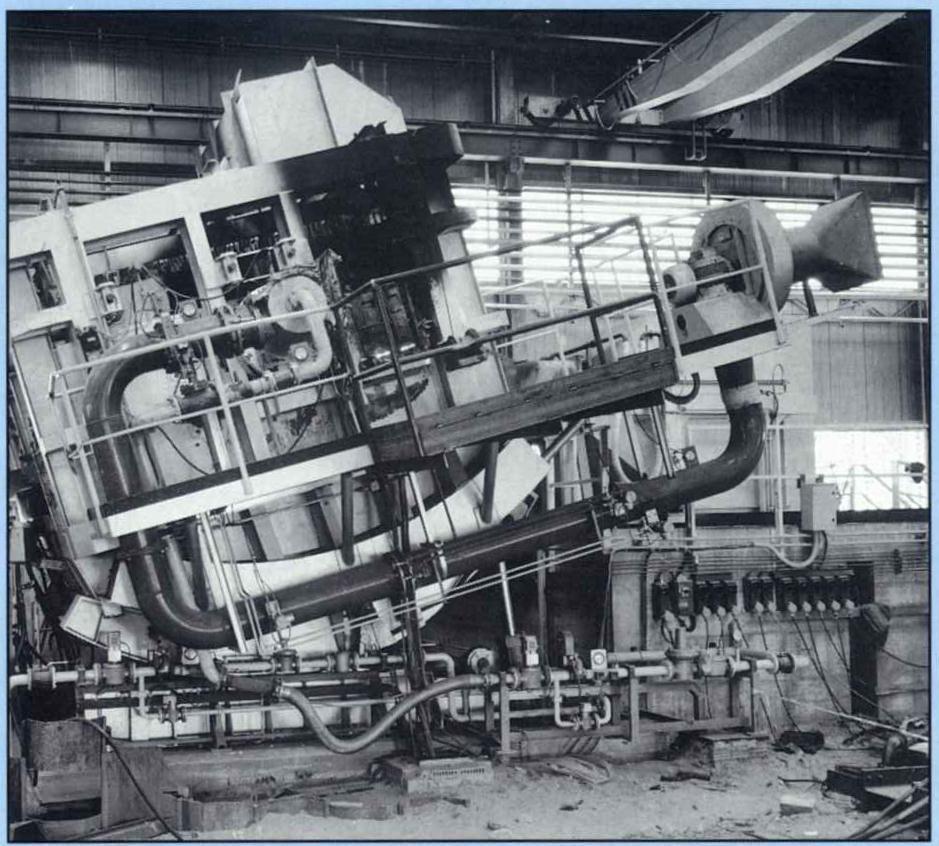
Малюнок 1 - Загальний вигляд похилої рафінуючої печі
Період розплавлення триває зазвичай близько восьми-десяти годин. Змінна потужність пальників(окислювальних і відновних) використовуються для швидкого розплавлення і ретельного окислення металу. Температура в печі підтримується на високому рівні, щоб отримати кращу гомогенізацію розплавленої міді. Як тільки первинний шлак повністю видаляється з печі процес окислення рідкій ванні здійснюється шляхом введення повітря під поверхню рідкої ванни.
Ця операція зазвичай триває близько двох годин, а пекти в цей час має нахил 20 градусів до горизонту. При цьому вміст кисню досягає 10, 000 до 12, 000 ppm. Окислені домішки стають світліше, ніж розплавлена мідь, і плавають на поверхні рідкої ванни, формуючи шар вторинного шлаку. Для інтенсифікації цього процесу в розплав додаються деякі реагенти.
Видалення домішок свинцю, олова і нікелю, які іноді є присутніми у відносно великих кількостях, може викликати деякі утруднення. У таких випадках другий цикл рафінування може бути потрібний для повного видалення домішок. Для цього використовуються спеціальні добавки. Оскільки будь-який розплав має певну кількість домішок, залежних від початкового лому, технологія рафінування повинна коригуватися відповідно до рівня домішок і вимог, що пред'являються до кінцевого продукту.
На завершальній стадії плавки проводяться остаточне рафінування. При цьому з печі видаляються кінцевий шлак і добавки флюсів, що залишилися. Пекти ще раз нахиляється, що дозволяє инжектировать пару і паливо в розплав і значно понизити вміст кисню(до 200-350 ppm). Зміст інших домішок нижче 5 ppm.
Висновки
Використання операційних циклів процесу Properzi знижує енергетичні і матеріальні витрати. Крім того зменшує навантаження на довкілля. Технологічний процес виготовлення мідної катанки поєднує в одному технологічному ланцюжку наступні операції: плавка шихти, відливка безперервної заготівлі, її плющення до розміру катанки, освітлення, охолодження і змотування у бухти. Процес безперервного литва і плющення має значні техніко-економічні переваги перед старим процесом відливання зливків, їх подальшого нагріву, пресування і волочіння.
Примітка
Під час здачі даного реферату магістерська робота ще не була завершена. Остаточне завершення - грудень 2012 року. Повний текст і матеріали по темі можуть бути отримані в автора та його керівника після зазначеної дати.
Література
- Карел С., Zeitlon B. Metall, 1981, Bd, №35,№5, p. 417-421
- Базилевский В.М., Истрин М.А., Барташев И.Л. Вторичные цветные металлы (Справочник). Часть 3. Металлургия меди и свинца. Издательство литературы по чёрной и цветной металлургии. –М.: 1957. – 200 с.
- Купряков Ю.П. Производство тяжёлых цветных металлов из лома и отходов.- Харьков.: Основа.1992. -399 с.
- Худяков И.Ф., Тихонов А.И., Деев В.И., Набойченко С.С. Металлургия меди, никеля и кобальта. Часть 1. Металлургия меди. -М.: Металлургия. 1977. -356с.
- Береговский В.И., Кистяковский Б.Б. Металлургия меди и никеля. –М.: «Металлургия». 1972. -367 с.
- Савенков Ю.Д. Рафинированная медь Украины: / Ю.Д. Савенков, В.И. Дубоделов, В.А. Шпаковский, В.А. Кожанов, Е.В. Штепан _ Донецк: Издательство, 2008._176с.
- Бредихин В.Н. Медь Вторичная: Монография / Бредихин В.Н., Маняк Н.А., Кафтаненко А.Я – Донецк: ДонНТУ, 2006 р.