|
Реферат по теме выпускной работы
Содержание
Моделювання процесів перетікання рідкої сталі через сталерозливний канал шиберного затвору проміжного ковша МБЛЗ
Вступ
У практиці безперервного розливання сталі особливе функціональне значення має технологія і обладнання дозування металу, що витікає з проміжного ковша в кристалізатор. При цьому технологи прагнуть забезпечити певну питому витрату сталі (у відповідності зі швидкістю витягування заготовки), максимально компактну поверхню струменя, а також її захист від вторинного окислення.
Найбільшого поширення в сучасних МБЛЗ отримав спосіб дозування за допомогою системи «стопор-моноблок» - «стакан-дозатор», що забезпечує високу стабільність процесу лиття [1,2]. Тим не менш, така схема розливання має певні експлуатаційні недоліки:
- 1. Знос або механічне руйнування головки стопора в процесі лиття;
- 2. Налипання частинок глинозему в області контакту головки стопора з поверхнею стакана-дозатора.
Ці недоліки ускладнюють ефективне дозування сталі і, як наслідок, призводять до збоїв в роботі системи автоматичної підтримки рівня металу в кристалізаторі [3,4]. Також слід мати на увазі, що привід механізму переміщення стопора-моноблока в автоматичному режимі управління виявляється досить інерційним, що, в свою чергу, обмежує досягнення високого ступеня точності роботи цієї системи. Такий ефект найбільшою мірою проявляється при виробництві заготовок малих перетинів з високою швидкістю розливання.
Альтернативним рішенням, яке набуло широкого розповсюдження на ряді металургійних заводів світу, слід вважати використання трьохплитного шиберного затвору (рис.1), встановленого в днище проміжного ковша. Дозування сталі здійснюється за рахунок часткового перекриття розливного каналу при зміні положення середньої плити. При цьому виконані промислові дослідження дозволили обгрунтувати ряд позитивних моментів застосування шиберних затворів для безперервного розливання сортової заготовки [5-7]. Зокрема, використання технології розливання через трьохплитний шиберний затвор забезпечує широкі можливості для реалізації комплексного автоматичного контролю усього процесу розливання. Як правило, він включає в себе автоматичний старт процесу розливання, контроль і підтримку рівня металу в кристалізаторі, автоматичне регулювання швидкості розливання і закінчення процесу розливання, в тому числі і при тимчасовому перекритті шибера (наприклад, при заміні погружного стакану) і т.д. Завдяки цьому досягається функціональна стабільність роботи МБЛЗ, в тому числі її високий ступінь готовності до коректування режимів лиття безпосередньо в ході розливання. Крім того, необхідна висока точність в підтримці рівня металу в кристалізаторі забезпечує також підвищення якості поверхні заготовки, а комплексна автоматизація дає зниження обсягу трудових витрат, припускаючи розливку «без участі людини». При цьому значно зменшується кількість проривів металу і переповнень кристалізатора.
Мета досліджень
Метою цих досліджень було вивчення особливостей руху струменя металу в розливному каналі проміжного ковша та оцінка впливу різних положень середньої плити шибера на стабільність процесу лиття стосовно розливання на сортовій МБЛЗ.
Промислові випробування
Електросталеплавильний комплекс ТОВ «Електросталь» має в своєму складі 50-тонну високопродуктивну ДСП, установку ківш-піч та сортову 3-х струмкову МБЛЗ [8]. Спочатку згідно проекту передбачалася розливання сталі в кристалізатор перетином 125 x 125 мм і 135 x 135 мм відкритої струменем.
Представлена на рис.1 схема розливання через трьохплитний шиберний затвор була реалізована при модернізації сортовий МБЛЗ в ЕСПЦ ТОВ «Електросталь» (м. Курахове). Слід особливо підкреслити, що стосовно умов відливання сортової заготовки в умовах високошвидкісної МБЛЗ подібна модернізація була виконана в Україну вперше.
Первинне випробування системи подачі сталі з промковша через трьохплитний шиберний затвор в умовах сортовий МБЛЗ ТОВ «Електросталь» показало, що він у функціональному плані забезпечує ефективне дозування металу протягом усього циклу розливання. При цьому затягування розливного каналу не спостерігалося. Тим часом при розливанні вуглецевих сталей з підвищеним вмістом кремнію досить часто мало місце поступове (протягом кількох десятків хвилин) затягування отворів розливного стакану, що в подальшому призводило до припинення процесу подачі сталі в кристалізатор. При цьому характерним моментом було те, що ефект затягування спостерігався навіть при досить високих значеннях перегріву металу в промковші над температурою ліквідус (45-50оС і вище).
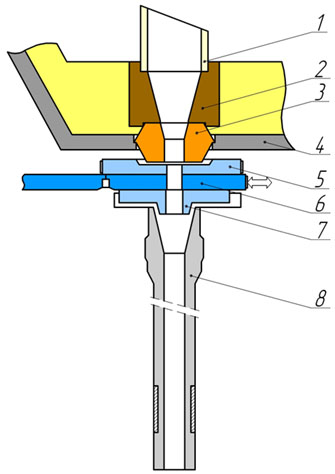
Рисунок 1 - Схема подачі сталі з промковша через трьохплитний шиберний затвор: 1 - стартова труба; 2 - гніздовий блок, 3 - стакан-дозатор, 4 - кожух промковша; 5 - верхня плита шиберного затвора; 6 - середня плита шиберного затвора; 7 - нижня плита шиберного затвора; 8 - погружний стакан
Для визначення можливих причин затягування розливного каналу, в якості базової була взята сталь 55С2, при розливанні якій спостерігалося найбільше число випадків затягування (залишковий вміст алюмінію в сталі становил 0,009-0,015%). Для дослідження було відібрано 10 стаканів-дозаторів із залишками металу, що утворилися після зупинки процесу розливання. Надалі стакани механічно руйнувалися і виконувалась комплексна оцінка стану робочої поверхні розливного каналу.
На першому етапі в ході візуального огляду внутрішньої поверхні гніздових стаканів встановлено, що значних відкладень часток глинозему, які характерні для розливання сталі розкисленої алюмінієм, не спостерігається. У той же час, звертає на себе увагу факт освіти шлакометалліческого граничного шару між вогнетривким матеріалом і рідкої сталлю (рис.2). У більшості випадків товщина шару знаходилася в межах 1,5 - 3,0 мм. По всій видимості, утворення цього шару слід пов'язувати з просоченням сталі у прикордонний шар робочої поверхні стакана-дозатора.
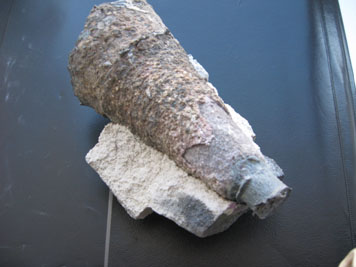
Рисунок 2 - Зовнішній вигляд гніздового стакану із твердою сталлю після його руйнування
На другому етапі досліджень, витягнуті із стакана-дозатора так звані «коріння» застиглої сталі розрізали в поздовжньому напрямку і шліфувалися. Макроструктура стали у відібраних зразках виявлялася методом глибокого травлення в 50% розчині соляної кислоти при температурі +70 oС протягом 50 хв по ГОСТ 10243 - 73.
Встановлено, що всі відібрані темплети можна умовно розділити на дві групи:
- 1. Зразки з щільною макроструктурою без видимих слідів осьової пухкості або усадочною пористості (рис.3);
- 2. Зразки з великою кількістю сторонніх включень, які мають чіткий характер залягання в місцях зменшення прохідного перерізу (ріс.3б).
Для першої групи зразків, затягування розливного каналу слід пов'язувати з тим, що температура розливається металу в гніздовому стакані-дозаторі наближалася до значення температури ліквідус в момент його попадання в розливний канал. Це підтверджується щільною равноосной структурою у всьому перерізі і відсутністю ознак усадочною пористості, характерною для затвердіння замкнутих обсягів. Більш того, характерні області, розташовані по периферії темплети, слід розглядати як ділянки, де відбувалися підвищений відвід тепла через стінки стакану і поступове «наморажування» сталі.
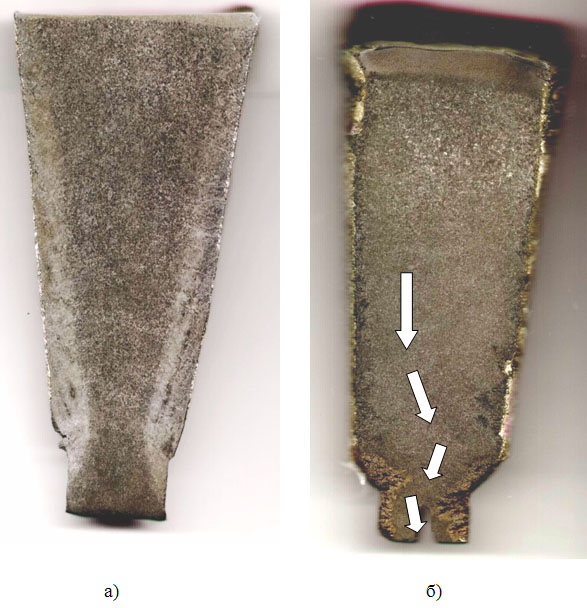
Рисунок 3 - Макроструктура темплетів з різних гніздових стаканів
Для зразків другої групи характерним є те, що їх макроструктура характеризується яскраво вираженими зонами налипання макровключень уздовж бічної поверхні гніздового стакану, які мають вигляд конусних загострень. Даний факт добре узгоджується з результатами роботи [9] і, в свою чергу, свідчить про високу інтенсивності протікання дифузійних процесів. Величина і взаємне розташування конусних загострень обумовлюють зміну напрямку течії металу (показано стрілками), що супроводжується утворенням застійних зон при зменшенні «живого» перетину розливного каналу. Відсутність на темплеті світлотравимих зон дозволяє припустити, що затягування розливного каналу відбувається, в першу чергу, внаслідок його перекриття відкладеннями неметалічних включень в так званих «мертвих» областях, що формуються при зсуві середньої плити шиберного затвора.
Математичне моделювання
В ході виконання третього етапу досліджень основна увага була сконцентрована на вивченні особливостей гідродинамічних явищ, що відбуваються всередині розливного каналу стакана-дозатора і трьохплитного шиберного затвора на математичній моделі. Подібний підхід до дослідження гідродинамічних явищ в розглянутому процесі добре себе зарекомендував у металургійній практиці [10]. Розроблена математична модель була реалізована за допомогою методу кінцевих елементів в прикладному пакеті ANSYS [11,12]. Результатами розрахунків були значення векторів швидкості і сумарної швидкості руху сталі.
Для всієї області обчислень застосували такі граничні умови:
- видкість потоку на вході в стакан-дозатор задається відповідно масовій витраті металу на виході з шиберного затвора; тиск рідини усередині розливного каналу залишається постійним;
- У вертикальній площині симетрії взяли нормальний градієнт всіх змінних, крім швидкості, перпендикулярній поверхні гніздового стакану;
- Швидкість, перпендикулярна поверхні гніздового склянки приймалося рівною нулю.
Розрахунки виконані для 5 положень середньої шиберной плити, при яких відкрита площа поперечного перерізу розливного каналу становила 1,0; 0,90; 0,80; 0,70 і 0,60 від площі перетину отвору середньої плити відповідно. Кількість ітерацій для збіжності рішення в кожному з розглянутих випадків склала 90.
Результуючі зображення характеру перетікання сталі через стакан-дозатор при різних положеннях середньої плити шиберного затвора представлені на рис.4.
Моделювання показало, що в міру зміщення отвору середньої плити щодо отворів у верхній і нижній плитах спостерігається поява і розвиток в рухомому струмені вихорів і областей з меншою швидкістю руху (рис. 4а). Видно, що сприятлива картина закінчення металу з промковша через шиберний затвор в основному зберігається при зменшенні величини відкритої площі поперечного перерізу отвору середньої плити до 0,9 від її номінального значення. При цьому нижче середньої шиберной плити потік рідини заповнює весь вільний обсяг розливного каналу і рухається вниз, що забезпечує рівномірне і симетричне витікання.
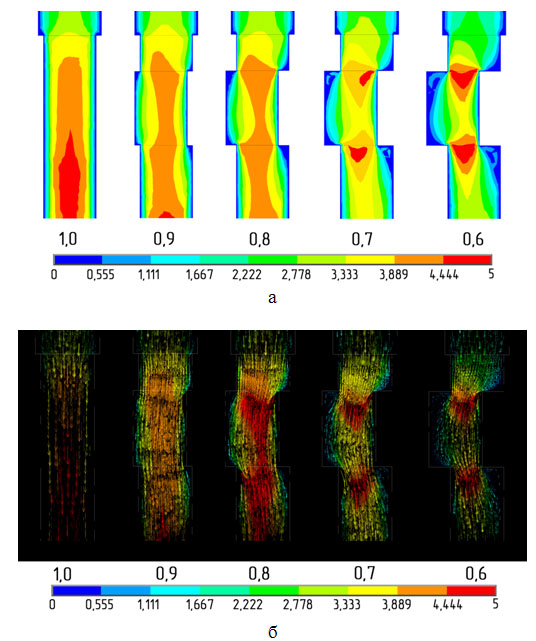
Рисунок 4 - Розподіл полів (а) і векторів (б) швидкостей (м / с) в струмені сталі розливного каналу при різних положеннях середньої шиберной плити
При зменшенні величини відкритої площі поперечного перерізу отвору середньої плити до 0,7 ... 0,8 від її номінального значення гідродинамічна картина руху струменя характеризується меншою стабільністю. Внаслідок того, що середня шиберная плита перекриває значну частину поперечного перерізу розливного каналу, в цій зоні утворюється виступ, що обумовлює появу застійної зони безпосередньо в області отвору середньої плити, а рідинний потік зміщується переважно до протилежної стінки середньої плити.
При цьому у верхній і нижніх плитах формуються яскраво виражені зони зі слабким рухом металу, а в нижній плиті потік стали не завжди може заповнити повністю весь перетин отвору. Можна припустити, що саме такий стан середньої плити є причиною появи відкладень неметалічних включень, добре відомих на ріс.3б.
При ще більшому перекритті розливного каналу (менше 0,7) стабільність перебігу металу в шиберному затвору повністю порушується, оскільки внаслідок виступу середньої плити формуються зони руху металу з малою швидкістю («застійні» зони). У цих зонах відбувається відкладення неметалічних включень, а також намерзання крапель металу на стінки вогнетривів. Тим часом в подальшому навіть при поверненні середньої плити в номінальне становище утворилися тверді нарости будуть перешкоджати нормальному процесу лиття.
Вищевикладені результати добре узгоджуються з виконаними на МБЛЗ промисловими спостереженнями, згідно з якими інтенсивність розвитку процесів затягування отворів шиберного затвору також зростала при збільшенні величини перекриття розливного каналу середньою шиберною плитою. Це слід пов'язувати зі зростанням ролі таких чинників як забрудненість сталі неметалевими включеннями, температурою розливаємої сталі, величиною теплопровідності вогнетривких матеріалів шиберних плит і стакана-дозатора і т.п. Всі ці обставини можуть значно знижувати експлуатаційний ресурс роботи шиберного затвора.
На підставі розглянутих досліджень запропоновано вибір діаметра отвору в плитах шиберного затвора здійснювати з умови, щоб витрата рідкої сталі при розливанні з номінальними режимами забезпечувався при положенні середньої плити, відповідному відкритої площі поперечного перерізу отвору на рівні 0,95-0,90. При цьому перекриття отвору розливного каналу до рівня 0,85-0,80 як штатного режиму лиття допускається у разі виробничої необхідності.
Стосовно до умов розливання на сортовий МБЛЗ ТОВ «Електросталь» рекомендований діаметр внутрішнього отвору шиберних плит становить 25-28 мм в залежності від перерізу заготовки і швидкості її витягування. Збільшення діаметра отвору від початку випробуваного на 10-20%, певною мірою, буде сприяти зниженню швидкості затягування розливного каналу, оскільки відкладення глинозему, що формуються у вигляді різного роду перемичок і наростів, постійно руйнуються і змиваються рухомим потоком металу. Відповідно, ймовірність процесу затягування внутрішньої порожнини розливного каналу в деякій мірі знижується.
В якості додаткового заходу для зниження ефекту затягування розливного каналу на сортовій МБЛЗ також рекомендовано використовувати вогнетривкі вироби з низьким вмістом Al2O3 (на рівні 35-40%), що підвищує теплоізолюючу здатність матеріалу розливного склянки в порівнянні з високоглиноземисті матеріалом.
Висновки
- Використання трьохплитного шиберного затвора для дозування сталі, що випливає з промковша сортової МБЛЗ, в цілому забезпечує високу стабільність і автоматизацію процесу лиття. Висока точність в підтримці рівня металу в кристалізаторі забезпечує також підвищення якості поверхні заготовки, а високий ступінь автоматизації забезпечує зниження обсягу трудових витрат, припускаючи розливку «без участі людини».
- По мірі зміщення отвору середньої плити шиберного затвору щодо отворів у верхній і нижній плитах спостерігається поява і розвиток в рухомому струмені вихорів і областей з меншою швидкістю руху, що перешкоджає підтриманню стабільності процесу лиття. Сприятлива картина перетікання металу з промковша через шиберний затвор в основному зберігається при зменшенні величини відкритої площі поперечного перерізу отвору середньої плити до 0,9 від її номінального значення. При більшому перекритті отвору розливного каналу утворюються так звані «мертві» зони, в яких сповільнюється рух металу і починається утворення відкладень, які змінюють характер течії потоку і призводять до дострокової заміни шиберного затвора.
- Відповідно до умов розливання на сортовій МБЛЗ ТОВ «Електросталь» (перетин заготовки 125 x 125 мм і 135 x 135 мм) рекомендований діаметр внутрішнього отвору шиберних плит становить 25-28 мм в залежності від перерізу заготовки і швидкості її витягування. Ймовірність процесу затягування внутрішньої порожнини розливного каналу зі збільшенням діаметра отвору в деякій мірі знижується.
Перелік посилань
- 1. Смирнов А.Н., Куберский С.В., Штепан Е.В. Непрерывная разливка стали // Алчевск: ДонДТУ, 2010. – 520 с.
- Sahai Y., Emi T. Tundish Technology for Clean Steel Production. – New Jersey: World Scientific, 2008. – 316 p.
- Гаук Ф., Петшке Ю. Износ погружных стаканов и образование отложений глинозема при непрерывной разливке стали// Огнеупоры для МНЛЗ: Труды конференции. – М.: Металлургия, 1986. – С.62-75.
- Flow Dynamics and Inclusion Transport in Continuous Casting of Steel / B.G.Thomas, Q.Yuan, L.Zhang, S.P.Vanka // Proceedings of NSF Conference “Design, Service, and Manufacturing Grantees and Research” , Birmingham, Al, January 6-9, 2003. – University of Alabama: R.G.Reddy, ed., 2003. -P.2328 - 2362.
- Тиннес Б. Опыт эксплуатации шиберных затворов промежуточных ковшей // Огнеупоры МНЛЗ. Труды конференции. – М.: Металлургия, 1988. – С.121-130.
- Pfyl A., Fernandez J., Nieto J. Operation of a 3-plate tundish gate for slab casters with non-stop SN-change at ISPAT Mexicana in Lazaro Cardenas, Mexico // Proceedings 3rd European Conference of Continuous Casting. Madrid-Spain, October 20-23, 1998. – Madrid: 1998. – P.667-667.
- Havenga F., Botes S. Changeover from a 2-plate tundish sliding gate (T70) to a plate tundish sliding gate (33QC-SNS) at the continuous casters V1&V2 of ISCOR’s Vanderbijlperk Works in South Africa // Proceedings 4rd European Continuous Casting Conference. Birmingham, UK, 14-16 October, 2002. – Birmingham: IOM Communication, 2002. – P.112-121
- Развитие металлургического мини-завода ООО «Электросталь» и повышение его производительности / А.Н.Смирнов, А.С.Хобта, А.И.Смирнов и др. // Сталь. 2011. №1. – С.34-37.
- Inclusions and nozzle clogging during steel continuous casting process / Li Shusen, Jin Wei, Zhang Lifeng e.a. // The Iron and Steel Technology Conference and Exposition (AISTech 2008), Pittsburgh, Pa, May 5-8, 2008. - Warrendale (Pa): AIST. 2008. – P.1247-1261.
- Numerical simulation of Al[2]O[3] deposition at a nozzle during continuous casting / Yuan Fangming, Wang Xinghua, Zhang Jiongming, Zhang Lifeng. // Univ. Sci. and Technol. Beijing. 2008. 15. No.3. - P.227-235.
- Каплун А.Б., Морозов Е.М., Олферьева М.А. ANSYS в руках инженера. – М.: Едиториал УРСС, 2003. – 272 с.
- Mazumdar D., Guthrie R.I.L. The Physical and Mathematical Modelling of Continuous Casting Systems // ISIJ International. 1999. Vol.39. No.3. – P.525-548.
|
|