- Introduction
- 1. The aim of this work
- 2. Topicality
- 3. Brown coal as an object of primary processing and agglomeration
- 3.1 Briquetting
- 3.2 Hydrogenation
- 3.3 Pyrolysis and gasification
- 4. Hydrotransportation of coal: state of the problem
- Conclusion
- References
Introduction
According to geological reserves of the main energy raw materials in Ukraine is the coal reserves of about 120 billion tons, including the proven – some 50 billion tons. [1] Coal – the only source of energy, reserves can meet the needs of exploration in the Energy and Industry of Ukraine for a long time – according to different estimates of 300-400 years. In Ukraine, the share of coal in the energy balance is respectively 94.5%, oil – and gas prices 2% – 3.6%. [3]
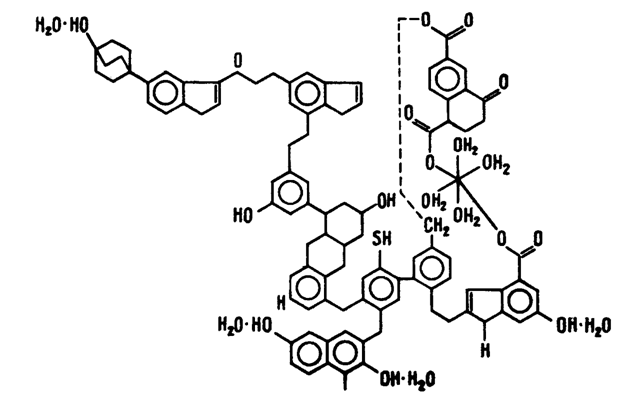
Pic 1. - The chemical structure of brown coal
The Ukrainian economy is developing and increasing the consumption of different energy sources, in the absence of self-developed oil and gas industry has become an alternative to coal. Increase its production is possible only through radical reconstruction and construction of new coal mines, the mines, in turn, requires a long time and large capital investments.
One solution to this problem is to expand the scope of use in large and small brown coal thermal power, which will contribute to a certain degree of stabilization of the fuel and energy balance of the country and creating a reserve of time for the development of the coal industry.
1. The aim of this work
Brown coal is the specific raw materials and has a number of negative features: high humidity and water absorption, high reactive oxygen capacity, underestimate the heat of combustion. These characteristics cause the failure of its long-term storage, transportation over long distances, greater likelihood of spontaneous combustion..
Objective: To examine how the primary processing and refining of brown coal for its subsequent transport, storage and efficient use – liquefaction, gasification, pyrolysis, etc.
2. Topicality
So there is a need to develop such technology primary processing and agglomeration of lignite, which would take into account the specific properties of the original lignite, the conditions of the process of hydraulic transport of coal, and performance requirements of the coal feedstock for further processing of its operations – pyrolysis, combustion, liquefaction, briquetting, dehydration. The solution to this problem may become the technology of coal oil processing agents - aggregation of oil.
Selective aggregation of coal oil combines a set of processes structuring a thin coal polydisperse phase in an aqueous medium using oil reagents. In the process of selective aggregation of coal oil is the mechanism of adhesive interaction oleophilic coal surface with oil, in which it is achieved by selective wetting and building-block in a turbulent flow of water. Hydrophilic particles are not wetted with oil in the structure of the units are not included, which allows you to select them as a breed of suspension.
The processing of brown coal oil selective aggregation eliminates its disintegration and soaking, "conserving" the organic matter in the hydrophobic aggregates that are easily dewatered by mechanical methods, and are good raw material for pyrolysis, briquetting, gasification.
3. Brown coal as an object of primary processing and agglomeration
3.1 Briquetting
Briquetting of coal – the physico-chemical process for mechanically and thermally robust varietal product – briquette having a given geometric shape, size and weight.
The technological process of brown coal briquetting without binder consists of the following operations: preparation of coal particle size and moisture, and compaction. Process parameters to be met by brown coal briquettes: Briquette weight 100-500 g, the mechanical abrasion resistance of 75-80%, compressive and flexural strength, respectively, 70-90 and 10-15 MPa, 3-4% water absorption, heat of combustion 24000-30000 kJ / kg and ash content of 10-25%. [1]
3.2 Hydrogenation
Hydrogenation of brown coal – the process of direct coal into synthetic fuel gas and liquid states of aggregation that occurs at high pressure and relatively high temperature.
This area of coal is studied in different countries. Abroad, the largest commercial application of this technology was in South Africa, where there are four of the plant, with a total annual capacity of about 8-10 million tons of liquid fuel. Works are carried out using a patented technology based on advanced SASOL Fischer-Tropsch method. Given that SASOL has a policy to maintain high fees for the use of technology, this causes the high value of its industrial implementation in other countries.[17]
Requirements for brown coal, which is fed to the liquefaction.
Preparation of brown coal includes the crushing, drying, cooking pasta coal gidrogenizat. Grinding is carried out to a particle size less than 0.1 mm – to increase the reactivity of the surface is realized in the disintegrators. The external surface area is on the increase of 20-30 times the amount of transition time – a factor of 5-10. The coal is then dried. The pores are filled with moisture, which prevents the penetration of the coal substance reagents, it is released in the process in the reaction zone, reducing the partial pressure of H2, as well as increases the amount of wastewater. For drying, use a steam tube dryers, vortex chamber, the tube-dryers in which the coal is dried to a residual moisture content of 1.5%. Coolant are hot flue gases with a minimum of O2 content (0.1-0.2%), coal is subjected to oxidation. Coal is not heated above 150-200 ° C, to avoid reducing the reactivity.
On the basis of large experimental data proved that coal with good gidrovanostyu contains from 65 to 85% with more than 5% H, and has more than 30% volatile (V). The rational for the moisture content of raw coal hydrogenation process – Wrt = 10-15%, ash content Ad = 10-12%, the value of d <0,1 mm, the rate of vitrinite reflectance 0,35-0,95%.
3.3 Pyrolysis and gasification
Pyrolysis
Pyrolysis – decomposition of brown coal when heated without access of air.
Brown coal when heated does not soften, thus there is a release of volatile substances, which are partly decomposed. In the remainder formed a more or less semi-solid, endure strong shrinkage. In semi-coking of brown coal are three temperature zones [3]:
- pre-heating zone to 100 ° C;
- drying zone is 100-125 ° C;
- zone of 225-500 ° C. semicoking
During pyrolysis under the influence of temperature in the coal undergoes substantial changes. The first stage – the evaporation of moisture at temperatures up to 125-160 ° C, and then begins the decomposition of organic matter of brown coal. As of the process removes oxygen, hydrogen and nitrogen, and the solid residue is enriched in carbon. In the initial stages at temperatures up to 200 ° C, oxygen is released mainly in the form of carbon dioxide and water by pyrogenetic removal of functional groups, followed by condensation reactions of radicals that remain.
At a temperature of 200-350 ° C is a smooth decrease in the solid residue, separation of vapors and gases increases by only 6-7%. The zone from 350 to 450 ° C is characterized by increased rate of exit vapor phase and a sharp decrease in the yield of solid residue. In the temperature range 450-550 ° C there are small changes in yield as a solid residue and gas-vapor mixture.
Schematic representation of the pyrolysis of picture 1.3 [6]
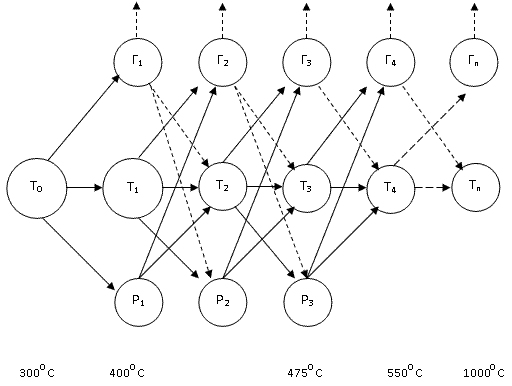
Рис. 1.2 - Block diagram of the pyrolysis
Gasification
The process of transformation of the organic mass of coal into gaseous substance is called gasification. In the process of gasification of carbon is usually converted into carbon monoxide and hydrogen – in the water vapor and, together with sulfur, which is in the coal organic matter – in the hydrogen sulfide, nitrogen – in the oxides of nitrogen. The mineral part of coal depending on the temperature of gasification becomes ash or slag.
Requirements for brown coal, which is fed to the pyrolysis and gasification .
The rational for the moisture content of raw coal pyrolysis – moisture (Wrt) to 15%, ash content (Ad) to 10%, low-sulfur coal should be. For the gasification process - moisture (Wrt) and 65%, ash content (Ad) to 40%.
4. Hydrotransportation of coal: state of the problem
Hydraulic transport of bulk solids was developed in the second half of the twentieth century. At the present time has been extended pipeline transportation of oil, natural gas and petroleum products. With the main hydro-transport system carried the movement of minerals and construction materials, industrial waste and chemical raw materials.
There are two fundamentally different technologies of hydraulic transportation of coal.
The first technology – transportation of the slurry in the mass concentration C = 50%, followed by dehydration at the receiving terminal. Coal is crushed to a particle size 0-1 (3-6) mm and mixed with water (ratio of liquid and solid is 1: 1).
One of the first in the world – the main slurry pipeline mine Black Mesa (Arizona, USA), a length of 439 km and a capacity of 5.8 million tons / year. In 1964, the energy company, Peabody Energy has signed a contract with the Navajo and TAPI to use their water resources to create a slurry and its further transport to the power station in Moheyvi a capacity of 790 MW.
The second technology of hydraulic transportation of coal – in the form of highly concentrated water-coal suspensions. At the receiving terminal of highly concentrated water-coal suspensions used as coal-water slurry fuel (CWF).
The classic method of preparation CWF consists of three main stages (Pic 1.3):
- Crushing of raw coal to a particle size 10 .. 20mm;
- Wet grinding of coal (in the presence of water and plasticizer) to 0.1-0.2 mm;
- Homogenization, storage and transportation.
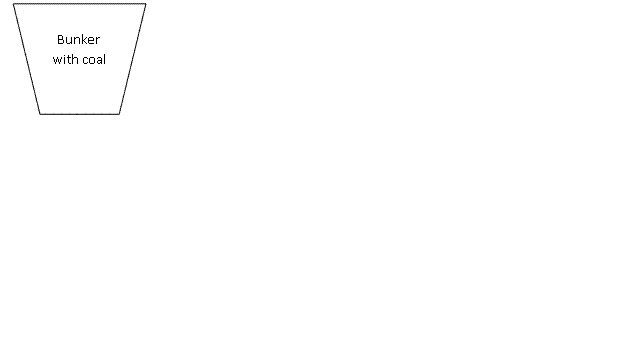
Рис. 1.3 - The classic method of preparation CWF
To use a grinding ball mills or rod drum with a special set of grinding bodies, which provides the desired binary granulometric composition of the coal phase. This step is crucial in the preparation of CWF, as it defines the characteristics further CWF (particle size distribution, viscosity, stability, etc.). In addition, this stage is usually the most expensive.
At the stage of wet milling of the CWF may include various additives necessary to increase the static stability of the CWF, reduced viscosity, and others.
Conclusion
One of the areas of technological progress is the development pipeline. The greatest prospects for the industry and the main hydrotransport oil and bulk materials. Hydrotransport characterized by continuity and uniformity of traffic, increased reliability, the possibility of complete automation, regardless of weather conditions, has an economic advantage over the rail, especially when the mines are located in remote areas, creating less noise, has a much lower transport losses and human impacts on the environment ; short periods of construction.
There are several ways the hydraulic transportation of coal:
- slurry pipeline to further dehydration;
- transport of highly concentrated water-coal suspensions.
The negative properties of brown coal, prevent the use of hydraulic transport, to address this problem the technology of processing coal apolyarnimy agents – aggregation of oil.
Based on the above for the beautification of brown coal in its hydrotransportation, we have chosen the technology of aggregation of coal oil, which fits well with the technology of its further processing and use of: briquetting, liquefaction, gasification, pyrolysis.
References
- Смирнов В. О., Сергєєв П.В., Білецький В.С. Технологія збагачення вугілля. Навчальний посібник. — Донецьк: Східний видавничий дім, — 2011. — 476 с.
- Chun - Zhu Li. Advances in the Science of Victorian Brown Coal – Book, 2004. – 459p.
- Саранчук В.І., Ільяшов М.О., Ошовський В.В., Білецький В.С. Основи хімії і фізики горючих копалин. (Підручник з грифом Мінвузу). – Донецьк: Східний видавничий дім, 2008. – 640 с.
- Світлий Ю.Г., Білецький В.С. Гідравлічний транспорт (монографія). - Донецьк: Східний видавничий дім, Донецьке відділення НТШ, «Редакція гірничої енциклопедії», 2009. - 436 с.
- Мала гірнича енциклопедія. т.1,2 / За ред. В. С. Білецького. — Донецьк: «Донбас», 2004, 2007.
- Липович В.Г., Калабин Г.А., Калечиц И.В Химия и переработка угля - М.: Химия, 1988. – 336 с.
- Чистяков А.Н. Справочник по химии и технологии твердых горючих ископаемых. – СПб.: издат. Компания “Синтез”. – 1996. – 363 с.
- Святец И.Е., Агроскин А.А Бурые угли как технологическое сырье. – М., Недра, 1976. - 223 с.
- Ходаков Г.С, Горлов Е.Г., Головин Г.С. Производство и трубопроводное транспортирование суспензионного водоугольного топлива// Химия твердого топлива. - 2006. - №4. - С. 22—39
- Круть О.А Водовугільне паливо. – Київ: Наук. Думка, 2002. – 172 с.
- Трайнис В.В. Магистральные трубопроводы в США // Уголь. – 1978 - №11, с. 74-77.
- Білецький В.С., Сергєєв П.В., Папушин Ю.Л. Теорія і практика селективної масляної агрегації вугілля. Донецьк: МКП Грань, 1996. - 264 с.
- Гордеев Г.П., Федотова В. М. О критическом влагосодержании бурых углей// Химия твёрдого топлива. – 1989. - №6. – 76-78 с.
- Елишевич А.Т., Оглоблин Н.Д., Белецкий В.С., Папушин Ю.Л. Обогащение ультратонких углей. – Донецк, Донбас, 1986. – 64 с.
- Тамко В.О., Білецький В.С., Шендрик Т., Красілов О.О Вплив механічного подрібнення бурого вугілля Олександрійського родовища на його піроліз// Донецький вісник Наукового товариства ім. Шевченка. Т. 21 – Донецьк: Східний видавничий дім. – 2008. – С. 97-103.
- Калечица И.В Химические вещества из угля. – М.: Химия, 1980. – 616 с.
- Твердов А.А., Жура А.В., Никишичев С.Б Перспективные направления использования углей// Глобус. – 2009. - №2. – С. 16-19.
- Лебедев Н. Н. Химия и технология основного органического и нефтехимического синтеза. – М.: Химия, 1988. – 592 с.
- Крылова А.Ю., Козюков Е.А Состояние процессов получения синтетических жидких топлив на основе синтеза Фишера-Тропша// Химия твёрдого топлива. – 2007. - №6. – С. 16-25.
- Energy & Environmental Research Center (EERC). [Электронный ресурс]. – Режим доступа: http://www.undeerc.org/default.aspx
- Борук С.Д., Вінклер І.А., Макарова К.В. Вплив стану поверхні частинок дисперсної фази на фізико-хімічні характеристики водо-вугільних суспензій на основі бурого вугілля. - Наук. вісник ЧНУ. Вип. 453.: Хімія. – Чернівці, 2009, с. 40-45.
- Касаточкин В.И., Ларина Н.К. Строение и свойства природних углей. – М.: Недра, 1975. – 158 с.
- Кегель К. Брикетирование бурого угля. – М., Углетехиздат, 1957. – 659 с.
- Саранчук В.И. Надмолекулярная организация, структура и свойства угля. – Киев: Наук. Думка, 1988. – 190 с.