Design of a Modular T actile Sensor and Actuat or Based on an Electrorheological Gel
Автор: Richard M. V, Gary Fedder, Pradeep Khosla
Abstract
We present the design of a modular tactile sensor and actuator system for observing human demonstrations of contact tasks. The system consists of three interchangeable parts: an intrinsic tactile sensor for measuring net force/ torque, an extrinsic tactile sensor for measuring contact distributions, and a tactile actuator for displaying tactile distributions. The novel components are the extrinsic sensor and tactile actuator which are “inside-out symmetric” to each other and employ an electrorheological gel for actuation.
1. Introduction
Dozens of tactile sensors have been developed over the past twenty years or so. Seigel [17] and Nichols and Lee [9] provided good early surveys of tactile sensing technologies while Howe’s [5] is more up-to-date. Some of these sensors over the years have gone so far as to become commerciallyavailable or are being produced within corporate R&D labs “for distribution.” Still, none have been successful at wide-spread use or even consistently applied to a particular task. The main reason for this has been the lack of effective, ge-neric, strategies for using the tactile feedback. Several researchers have used tactile feedback for determining object shape [4],[11] but few have achieved robust manipulation [4].
The vast majority of prior designs have relied on rubber and foam. While these have desirable design properties, it has been conjectured that they provide inferior contact “feel.” Shimoga and Goldenberg [14] and Akella, et al [1] have shown hard-surface and foam-surface sensors to have inferior contact properties compared to gels and powders. In particular, impact and conformal properties seem to be worse in Hooke’s Law materials. Active gels, in particular, hold promise for providing not just useful contact properties, but an additional degree of freedom in modulating the grasp. Electrorheological (ER) fluids, which can change viscosity in the presence of an electric field, exhibit such active behavior and can be gelled [19].
Fewer tactile actuators have been developed. Work on actuators (tactors) has focused primarily on virtual reality applications and sensory substitution. Shimoga [15] provides acomprehensive survey of actuators and technologies whilethe work of Kontarinis, et al is more representative of the current state of the art. The primary technology used to-date has been vibrotactile stimulation using piezoelectrics or blunt pins. A few researchers have tried electrotactile stimulation - direct electrical stimulation of the skin. This is an attractive option because of its simplicity of physical implementation. Shimoga et al [16] also investigated the use of commercially available shape memory alloy actuators for providing binary contact information during grasping tasks.
Our motivation for designing “yet another tactile sensor” is rooted in our work in Gesture-Based Programming, a paradigm for programming by human demonstration. In this paradigm, atask expert- not aprogramming expert- programs a complex robot system (Utah/MIT hand on a Puma) by actually demonstrating the task. All the actions the human makes - some deliberative, some fleeting - are considered gestures of one form or another. The system observes the state of the task through vision and observes the human’s gestures through instrumented clothing, such as a Cyber-Glove, Polhemus device, and tactile sensors.
The gestures, which may include events of motion, pose, contact, and sound, are interpreted with respect to a database of known robotic expertise. This expertise base is based on sensorimotor skills [9], the basis of which have been developed off-line, but which are tuned for the task at hand.
Our need for tactile sensors is in two environments. We need substantially identical sensors for both end-of-robot and end-of-human tooling. The reason for this is that we want to observe thetactile gesturesof the human during demonstra-tion and then parametrize robotic expertise agents that make use of the same type of tactile information during execution.
In and of itself, this is not sufficient reason to embark on a tactile sensor design. There is a more basic motivation that springs from the application: the observability problem. Extracting meaning from the tactile gestures the human em-ploys is difficult because much of the information content is unobservable. The human demonstrator can make use of sensory information beyond the capabilities of the instrumented clothing, such as alternative sensing modalities as well as superior resolution and dynamic range. Since tactile sensing technology will not soon approach the capabilities of the human fingertip, we endeavor to reduce the human sensory capacity to that of the robot; in effect, to interject a filter.
What do we gain by doing this? In effect, a shared ontology, or “common view of reality,” while still capitalizing on the respective strengths of the human and robot. Paradigms for programming complex hand/arm systems by human demonstration rely fundamentally on the human for planning, high-level learning, and exception handling. We focus on systems with many degrees-of-freedom (as opposed to simple grippers) because planners for such systems are difficult to construct so there is a “big win” in incorporating human ability. Low-level tuning and repeatable execution are the contributions of the robot. With this in mind, it makes sense to “cripple” the human’s capabilities and force him/her to re-learn basic skills at the robot’s level because that is exactly what the human is good at doing.
With the goal of employing not just a tactile sensor, but a tactile filter as well, it is desirable to have a “symmetric technology” that can be used on both the sensing and actuation ends. A tactile sensor and actuator based on an electrorheological gel addresses all these issues to some degree and provides a novel design approach with many rich directions for analysis and experimentation.
2. Design Concept
The development of this system spans many years and many miles but is far from complete. The original design of our coarsely-foveated ER tactile sensor with grasp actuation capability was completed in Mark Cutkosky’s lab at Stanford [19]. Subsequently, the first prototype intrinsic/extrinsic sensor combination was fabricated followed by a diversion into novel sensor calibration techniques at Carnegie Mellon [18]. Now, we hope to complete the end-to-end human/robot system with this modular ER sensor/actuator.
The modular sensor/actuator system is based on three interchangeable components: an extrinsic sensor array, an intrinsic force/torque sensor, and a conformal tactor array. The tactor array will be for end-of-human use only, either in conjunction with the extrinsic sensor array for gesturing or in conjunction with an external force reflecting device for virtual reality (VR) applications (more on this later). The intrinsic sensor will be for end-of-robot use only and will be used in conjunction with the extrinsic array or a variety of passive tips during manipulation. The extrinsic sensor can be used either on the robot or on the human, both with and without underlying components for sensing.
For sensing human contact gestures, the extrinsic sensor array and the tactor array are similar to a pair of thimbles. The tactor will be somewhat smaller so it can nest inside the extrinsic sensor (Figure 1). Clearance will be provided so an instrumented glove can be captured between the “thimbles” for finger joint sensing.
The design of the two components will be very similar in that the tactor is an “inside-out” version of the sensor. Both use the electrorheological gel developed by Voyles, et al [19] to provide “fleshy” properties. The sensor will use it primarily as a dielectric for capacitive sensing and as a structural material. The tactor will use it primarily for its electrorheological properties.
For sensing robotic contact during manipulation, the extrinsic and intrinsic sensors will be nested to provide both contact force distribution and net force/torque. The intrinsic sensor is based on a cylindrical cantilever beam (Figure 1) similar in concept to that of Bicchi and Dario [3].
Not surprisingly, ER fluids have been proposed and implemented as haptic devices for sensing and actuation in limited ways in the past. Cutkosky has been involved with ER fingers [1][6][19] for a long time, both as sensors and “passive actuators.” Monkman and Sano have both been working on ER display mechanisms recently. Monkman proposes a true tactile display [8], similar in concept to that proposed here, but only simulates its effect in a planar configuration. It is also geared more toward reconstructing the world locally, rather than reconstructing local tactile stimulation from the world. Sano constructed a prototype haptic interface [13] somewhat like a joystick with controllable damping and proposes extending it to all five fingers.
Electrorheological fluids are attractive because they are controlled electrically, which is convenient, they require little power (although voltages are very high), there are no moving parts, and they can be made very compact. In fact, the smaller the dimensions, the higher the field strengths and the stronger the ER effect.
These characteristics make ER fluids attractive to the haptic interface community. Tactile sensing and actuation are probably most limited by packaging issues so any technology that promises to address the packaging issues associated with the resolution, dynamic range and diversity of the sensing and actuation at the human fingertips, even in a primitive way, will get some consideration.
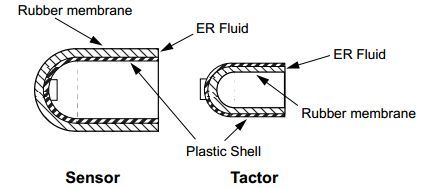
Figure 1: Cross-section of ER sensor and tactor.
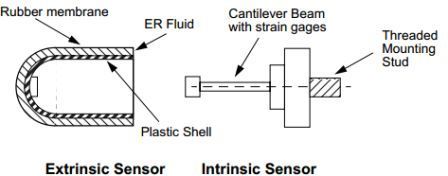
Figure 2: Cross-section of ER sensor and strain gauge sensor.
3. Intrinsic Tactile Sensor Design
The design of the intrinsic tactile sensor is fairly straightforward and has been studied by many. Bicchi and Dario [3] present an optimized design process but space and packaging are the biggest issues in our modular, multicomponent system but we will attempt to optimize performance as best we can.
Our first two intrinsic prototypes used plastic as the structural material but we are investigating various metals for the final implementation. Bonding strain gages to some types of plastic can be extremely difficult.
While the design of the intrinsic sensor has been done many times and will largely consist of engineering trade-offs for this project, we developed a novel calibration procedure during testing of the prototypes that dramatically eases the calibration process. Dubbed “shape from motion calibration” [18], this new technique allows the recovery of the calibration matrix without knowledge of all the applied loads on the sensor. Since applying many precisely-known loads is the primary time-sink, shape from motion is much quicker and actually results in a more accurate calibration because much more data can be gathered cheaply.
4. Extrinsic Tactile Sensor Design
The extrinsic sensor shell will be made of plastic, probably delrin or ABS (as are our current prototypes). The body of the sensor must be insulating to hold the individual capacitive electrodes. In the original cylindrical. prototype, we plated copper onto an acrylic core. We then patterned an array of individual, directwired electrodes to form one half of the sensing and actuation capacitor. The outer rubber membrane was conductive and grounded and formed the other half of all the sensing and actuation capacitors. As in that prototype, there will be no attempt to multiplex the sense elements because that may preclude future use of the actuation potential of the fluid. (In general, although not always, multiplexing the ER excitation voltage reduces the ER effect.)
There are several problems with sensing this way. First of all, it is a displacement sensing technique rather than a pressure or force sensing mechanism. This, of course, is a common approach, but we don’t have a well-behaved medium to accurately relate displacement to force. Instead the fluid (or gel) can change from a Newtonian fluid to a Bingham plas-tic under excitation.
The next problem with using the outer membrane as a sensor element is the unknown rest state. Because the fluid or gel has some freedom to move (the self-healing gel partially solves this problem) and does not return completely to any known or deducible state, it would be necessary to take constant offset measurements to zero the sensor. Gravity load-ing is also a problem. The fluid has a tendency to sag in a gravity field.
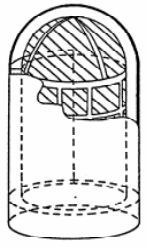
Figure 3: Cutaway view of the original prototype fingertip sensor with plated capacitors.
Our solution to these problems of capacitive sensing is to build micromachined silicon pressure sensors that will be bonded to the plastic core. These miniature pressure sensors are based on the same idea of capacitive displacement sensing, but their size and construction eliminate the above problems. First of all, theydorespond as a Hooke’s Law device, so there is a well-defined displacement/pressure relationship. (Although the complex transmission of the pressures through the gel complicate things significantly.)
They also have a well-defined rest state that they return to in the absence of an applied pressure. Finally, the miniature pressure sensors are designed to work with differential capacitors to improve sensitivity and minimize drift, noise, offset, and other non-signal effects (Figure 4). Of course, we will also bond local processing electronics near, or perhaps integrated with, the pressure sensors for signal conditioning.
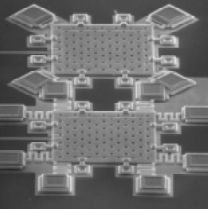
Figure 4: Micromachined differential capacitor pressure sensor (before encapsulation).
As a bonus, the differential configuration allows different capacitor configurations capable of detecting both compressive and shear pressures. In future work this may allow some level of slip detection.
The use of this type of local pressure sensor precludes the use of a Newtonian fluid. If that were the case, all sensors would see essentially the same pressure. This is another advantage of the ER gel. It maintains pressure distributions throughout its volume, however, one of the unsolved challenges is modelling this behavior.
Over the fingertip mandrel (the “bone”) is the ER gel which is held in place by a conductive rubber membrane that also acts as a ground plane. Even though we are using the micromachined sensors for pressure measurement, it may still be necessary to measure the volume of fluid over the sensors to adequately model the fluid behavior or to determine local shape of the object in contact. If this proves necessary, we can plate electrodes between the silicon sensors (or over them with a flexible membrane) to determine outer mem-brane displacement capacitively.
A final note must be made regarding structural integrity of the sensing medium. With rubber and foam-based sensors, there is no question as to where the structural material is. However, with fluids and gels, significant emphasis must be placed on keeping the structure of the sensing medium intact. This includes the pliability of the outer membrane but it can also be greatly enhanced with structural members such as “fingernails.” On the backside of the sensor will be a fluid exclusion dam to help maintain the shape of the outer membrane and to keep the gel reasonably contained in the area of the sensitive sites.
5. Tactile Actuator Design
The tactile actuator (tactor) has already been described as an “inside-out sensor” so we won’t discuss to deeply the phys-ical design issues since they are very similar to the extrinsic sensor. The key difference will be the lack of micromachined pressure sensors. Not only are they unnecessary for the tactor, but their survivability within such strong electric fields would be difficult to guarantee.
It may still be necessary to sense the membrane displacement to estimate fluid volume and electric field strength, but that would be done by the capacitive displacement arrange-ment rather than the localized pressure sensors. We are also trying to incorporate the fixed-separation plate arrangement of Akella, et al [1], but our design is much more space-con-strained. Akella, et al did not use the outer flexible membrane as one electrode. Instead, they interlaced pairs of fixed electrodes perpendicular to the membrane surface. Fluid near the membrane surface was relatively unaffected by the electric fields but upon depressing the membrane, the fluid was forced to pass between the plates, through the high field concentrations. The advantage to this is the plate geometry does not change as the membrane is deformed.
We should pause, briefly, and examine the nature of the “actuation.” An electrorheological fluid only has the ability to change viscosity and even develope yield stress. It has no capacity to actively exert forces on stationary objects. The only way the user can detect a change is by exerting a force on the tactor. For our application, observing a human demonstration, this is not a problem because the user is actually performing a contact task and is exerting forces. Keep in mind we intend to use the sensor/actuator pair as an active filter to control the feedback the human receives.
Even then, some form of sensory substitution must come into play because edges and very rigid surfaces cannot be duplicated with an ER fluid. Instead the user must respond to changes in damping and yield stress.
6. Other Applications
Although our application is in observing human demonstrations, we have considered how our devices might be useful in other domains. The sensors are fairly generic and have general applicability, but the tactor, being a “passive actuator,” is more limited. For example, VR applications do not include physical contact with a real environment, as does human demonstration.
This does not preclude the use of our tactor in VR. Quite to the contrary, our tactor can be used in conjunction with existing net force haptic interfaces such as Salisbury’s Phantom [12] or Hollis’ Magic Wrist [2].
The ER fluid is used in the extrinsic sensor mostly for convenience and symmetry. We can achieve the same dielectric and physical properties without the ER effect. However, maintaining ER capability in the sensor allows another avenue of future work in controlling the properties of the grasp at the contact boundary. Preliminary steps toward this examination have already been taken toward impact control [1] and improved gearing traction for grasping delicate objects [6] but no one has attempted active grasp control, to our knowledge.
7. Acknowledgments
Mr. Voyles was supported in part by a National Defense Science and Engineering Graduate Fellowship, a DOE Integrated Manufacturing Predoctoral Fellowship, and ARPA contract DABT63-95-C-0086.
8. References
Akella, P., R. Siegwart, and M.R. Cutkosky, “Manipulation with Soft Fingers: Contact Force Control,” in Proceedings of the 1991 IEEE International Conference on Robotics and Automation, v.2, pp. 652-657.
Berkelman, P. and R. Hollis, “Interacting with Virtual Environments Using a Magnetic Levitation Haptic Interface,” Proceedings of the 1995 IEEE/RSJ Intelligent Robots and Systems Conference, Pittsburgh, PA, Aug, 1995.
Bicchi, A. and P. Dario, “Intrinsic Tactile Sensing for Artificial Hands,” inProc. of the International Symposium on Robotics Research, R.C. Bolles and B. Roth, editors, MIT Press, Cambridge, MA, 1988, pp. 83-90.
Fearing, R.S., Tactile Sensing, Perception and Shape Interpretation, Ph.D. Thesis, Dept. of Electrical Engineering, Stanford University, Stanford, CA, December, 1987.
Howe, R.D., “Tactile Sensing and Control of Robotic Manipulation,” inJournal of Advanced Robotics, v.8, n.3, 1994, pp. 245-261.
Kenaley, G.L. and M.R. Cutkosky, “Electrorheological Fluid-Based Robotic Fingers with Tactile Sensing,” in Proceedings of the 1989 IEEE International Conference on Robotics and Automation,v. 1, May, 1989, pp. 132-136.
Kontarinis, D.A., J.S. Son, W. Peine, and R.D. Howe, “A Tactile Shape Sensing and Display System for Teleoperated Manipulation,” in Proceedings of the 1995 IEEE International Conference on Robotics and Auto-mation,v. 1, May, 1995, pp. 641-646.
Monkman, G.J., “An Electrorheological Tactile Display,”Presence, v. 1, n. 2, Spring, 1992, pp. 219-228.
Morrow, J.D. and P.K. Khosla, “Sensorimotor Primitives for Robotic Assembly Skills,” in Proceedings of the 1995 IEEE International Conference on Robotics and Automation,v. 2, May, 1995, pp.1894-1899.
Nicholls, H.R. and M.H. Lee, “A Survey of Robot Tactile Sensing Technology,” International Journal of Robotics Research, v. 8, n. 3, June, 1989, pp 3-30.
Salisbury, K., D. Brock and S. Chiu, “Integrated Language, Sensing, and Control for a Robot Hand,” in Robotics Research 3, Faugeras, O.D. and G. Giralt, eds., MIT Press, pp. 389-396, 1986.
Salisbury, K., “Mechanisms for Remote and Virtual Grasping: Hands and the Haptic Interface,” 1993 ISRR, Hidden Valley, PA, Oct. 1993.
Sano, A., “Haptic Interface Device Using Electro-rheological Fluid,” in 1995 ICRA University Laboratory Tour, Nagoya Institute of Technology, May, 1995.
Shimoga, K.B. and A.A. Goldenberg, “Soft Materials for Robotic Fingers,” inProceedings of the 1992 IEEE International Conference on Robotics and Automation, Nice, France, May, 1992.
Shimoga, K.B., “A Survey of Perceptual Feedback Issues in Dextrous Telemanipulation: Part II. Finger Touch Feedback,” inProceedings if IEEE Virtual Reality Annual International Symposium, Seattle, WA, Sept., 1993.
Shimoga, K.B., A.M. Murray, and P.K. Khosla, “A Touch Reflection System for Interaction with Remote and Virtual Environments,” inProceedings of the 1995 IEEE/RSJ International Conference on Intelligent Robots and Systems, Pittsburgh, PA, August, 1995.
Siegel, D.M., Contact Sensors for Dextrous Robotic Hands, Tech. Report AI-TR-900, MIT AI Lab, Cam-bridge, MA, June, 1986.
Voyles, R.M., J.D. Morrow, and P.K. Khosla, “Shape from Motion Approach to Rapid and Precise Force/ Torque Sensor Calibration,” in Proceedings of the ASME Dynamic Systems and Control Division, ASME Winter Annual Meeting, San Francisco, CA, Nov. 1995, pp 67-73.
Voyles, R.M., B.L. Stavnheim, and B. Yap, “Practical Electrorheological Fluid-Based Fingertips for Robotic Applications,”Proceedings of IASTED International Symposium on Robotics and Manufacturing, pp. 280-283, Santa Barbara, CA, Nov. 1989.